Одним з необхідних умов для забезпечення необхідної точності і довговічності роботи верстата є його правильна установка і кріплення на фундаменті. Тип фундаменту залежить від навантаження, що передається основи верстата, маси верстата і сил інерції, що діють під час роботи верстата. Фундаменти під металорізальні верстати бувають двох типів: перший - фундаменти, які є тільки підставою для верстата, другий - фундаменти, які жорстко пов'язані з верстатом і надають верстату додаткову стійкість і жорсткість. Токарні верстати встановлюють, як правило, на фундаментах другого типу згідно установчого кресленням, який дається в керівництві по експлуатації верстата. У кресленні вказуються необхідні розміри для виготовлення фундаменту, а також розташування верстата в приміщенні з урахуванням вільного простору для виступаючих і рухомих частин верстата. При установці верстата на бетонну основу розмічають гнізда за розмірами, відповідним отворам кріплення станини верстата, а потім гнізда вирубують. Після установки і вивірки верстата за рівнем фундаментні болти заливають цементним розчином. Установку верстата в горизонтальній площині вивіряють за допомогою рівня, встановленого в середній частині супорта паралельно і перпендикулярно осі центрів. У будь-якому положенні каретки супорта на напрямних верстата відхилення рівня не повинно перевищувати 0,04 мм на 1000 мм. Якщо фундаментні болти попередньо залиті в фундаменті, то вивірку виробляють, коли вони не затягнуті. Після установки і вивірки виробляють зовнішній огляд верстата і відчувають його на холостому ходу, під навантаженням, на точність і жорсткість.
Випробування верстата на холостому ходу. Привід головного руху послідовно перевіряють на всіх щаблях частоти обертання. Потім перевіряють взаємодію всіх механізмів верстата; безвідмовність і своєчасність, включення і виключення механізмів від різних керуючих пристроїв; роботу органів управління; справність системи подачі МОР і гідро - і пневмообладнання верстата. У процесі випробування на холостому ходу верстат повинен на всіх режимах працювати стійко, без стукотів і струсів, що викликають вібрації. Переміщення робочих органів верстата механічним або гідравлічним приводом повинно відбуватися плавно, без стрибків і заїдань. При випробуванні верстата на холостому ходу перевіряються також його паспортні дані (частота обертання шпинделя, подача, переміщення кареток супорта і ін.). Фактичні дані повинні відповідати значенням, зазначеним у паспорті.
Випробування верстата під навантаженням дозволяє виявити якість його роботи і проводиться в умовах, близьких до виробничих. Випробування проводять шляхом обробки зразків на таких режимах, при яких навантаження не перевищує номінальної потужності приводу протягом основного часу випробування. У процесі випробування допускається короткочасне перевантаження верстата по потужності, але не більше ніж на 25%. Час випробування верстата під повним навантаженням має бути не менше 0,5 год. При цьому всі механізми і робочі органи верстата повинні працювати справно; система подачі МОР повинна працювати безвідмовно; температура підшипників ковзання і кочення не повинна перевищувати 70-80 градусів С, механізмів подач 50 градусів С, масла в резервуарі 60 С.
Нові верстати в процесі експлуатації, а також після ремонту перевіряють на геометричну точність в ненавантаженому стані, на точність оброблених деталей і на одержувану при цьому шорсткість обробленої поверхні. Вимоги до точності викладені в керівництві з експлуатації верстата. При перевірці на точність верстата перевіряють прямолінійність поздовжнього переміщення супорта в горизонтальній площині; одновисотность осі обертання шпинделя передньої бабки і осі отвору пінолі задньої бабки по відношенню до тих, що направляють станини в вертикальній площині; радіальне биття центрирующей поверхні шпинделя передньої бабки під установку патрона; осьове биття шпинделя передньої бабки і ін.
Прямолінійність поздовжнього переміщення супорта в горизонтальній площині перевіряють за допомогою циліндричної оправки, закріпленої в центрах передньої і задньої бабки, і індикатора, встановленого на супорті, малюнок нижче - а). Зміщенням задньої бабки в поперечному напрямку домагаються, щоб показання індикатора на кінцях оправлення були однакові або відрізнялися не більше ніж на 0,02 мм на 1 м ходу супорта.
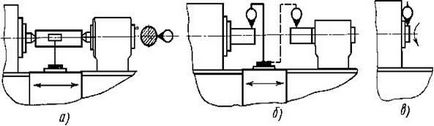
Одновисотность осі обертання шпинделя передньої бабки і осі отвору пінолі задньої бабки по відношенню до тих, що направляють станини в вертикальній площині перевіряють при видаленні задньої бабки від передньої на 1/4 найбільшого відстані між центрами, малюнок вище - б). Перевірку виконують за допомогою циліндричних оправок, вставлених в отвори шпинделя і пінолі задньої бабки, і індикатора, встановленого на супорті. Найбільше показання індикатора на утворює оправлення шпинделя визначають зворотно-поступальним поперечним переміщенням супорта в горизонтальній площині щодо лінії центрів. Не зраджуючи положення індикатора, таким же способом визначають його свідчення на утворює оправлення задньої бабки. Різниця в показаннях індікатоpa не повинна перевищувати 0,06 мм у верстатів для обробки деталей з найбільшим діаметром 400 мм. Допускається тільки перевищення осі отвору пиноли над віссю шпинделя передньої бабки.
Радіальне биття центрирующей поверхні шпинделя передньої бабки під патрон перевіряють за допомогою індикатора, малюнок вище - в). При цьому вимірювальний стрижень індикатора встановлюють перпендикулярно утворює центрирующей шийки шпинделя. Радіальне биття шийки обертового шпинделя для патрона з найбільшим діаметром оброблюваної деталі 400 мм не повинно перевищувати 0,01 мм.
Осьове биття шпинделя передньої бабки вимірюють за допомогою оправлення, вставленої в отвір шпинделя, і індикатора, встановленого на верстаті при обертовому шпинделі, малюнок нижче - г). Вимірювальнийстрижень індикатора з плоским наконечником впирається в кульку, який встановлений в центровий отвір оправлення. Осьове биття шпинделя для установки деталей з найбільшим діаметром 400 мм не повинно перевищувати 0,01 мм.
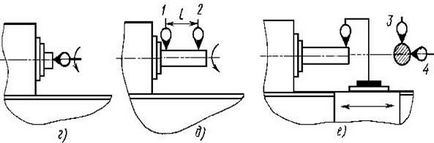
Радіальне биття конічного отвору шпинделя передньої бабки перевіряють за допомогою оправлення довжиною L = 300 мм, вставленої в отвір шпинделя, і індикатором, встановленим в резцедержатель верстата при обертовому шпинделі, малюнок вище - д). Для верстатів з найбільшим діаметром оброблюваної деталі 400 мм радіальне биття оправлення у торця шпинделя (положення 1) не повинно перевищувати 0,01 мм, а на відстані L = 300 мм від торця шпинделя (положення, 02 мм.
Паралельність осі обертання шпинделя передньої бабки повздовжньому переміщенню супорта перевіряють за допомогою оправлення довжиною L = 300 мм, встановленої в отвір шпинделя, і індикатором, встановленим на супорті верстата, малюнок вище - е). Вимірювання виробляють по котра утворює оправлення в вертикальної (положення 3) і горизонтальної (положення 4) площинах. При цьому знімають показання індикатора за двома діаметрально розташованим утворюючим оправлення (при повороті шпинделя на 180 градусів), переміщаючи супорт з індикатором від торця шпинделя на відстань L = 300 мм. Потім визначають середньоарифметичне значення відхилень, виміряних за двома утворюючим (окремо для горизонтальної і для вертикальної площин). Для верстатів з найбільшим діаметром оброблюваної деталі 400 мм допускається непаралельність осі шпинделя напрямку поздовжнього переміщення супорта у вертикальній площині не повинна перевищувати 0,03 мм (причому непаралельність повинна бути спрямована тільки вгору), а в горизонтальній площині - 0,012 мм (непаралельність повинна бути спрямована тільки в сторону супорта).
Точність роботи токарних верстатів перевіряють при обробці зразків. На верстатах з найбільшим діаметром оброблюваної деталі 400 мм точність геометричної форми циліндрової поверхні перевіряють при обробці зразків довжиною 200мм. Попередньо оброблений зразок з трьома пасками, розташованими по кінцях і в середині зразка, встановлюють в патрон або до центрів верстата і обробляють по зовнішній поверхні пасків. Перевіряють сталість діаметра в будь-якому поперечному перерізі, при цьому різниця між вимірюваними максимальним і мінімальним значеннями не повинна перевищувати 0,02 мм. Вимірювання виробляють пассіметром, мікрометром або іншими інструментами.
Площинність торцевої поверхні перевіряють при обробці зразків діаметром d = 200 мм, встановлених в кулачки патрона. Торцева поверхня зразка може мати кільцеві канавки (у периферії, в середині і в центрі) і повинна бути попередньо оброблена. Після проточки торцевої поверхні зразок не знімають з верстата. Результати обробки можуть бути перевірені індикатором, встановленим на супорті так, щоб наконечник індикатора був перпендикулярний вимірюваної поверхні. Вимірювання виробляють шляхом переміщення в поперечному напрямку верхньої частини супорта на довжину, рівну або більше D. Відхилення, яке визначається як половина найбільшою алгебраїчної різниці показань індикатора, не повинно перевищувати 0,016мм. Площинність торцевої поверхні можна також перевірити, торкаючись наконечником індикатора контрольної лінійки, прикладеної до обробленого торця зразка. Лінійку прикладають в різних осьових перетинах перевіряється поверхні і визначають відхилення так само, як описано вище.
Точність нарізати різьблення перевіряють на зразку (діаметр якого приблизно дорівнює діаметру ходового гвинта верстата), закріпленому в центри верстата, при нарізанні трапецеїдальної різьби довжиною не більше 500 мм з кроком, приблизно рівним кроку ходового гвинта верстата. При цьому ходовий гвинт безпосередньо з'єднують зі шпинделем через змінні зубчасті колеса з відключенням механізму коробки подач. Після чистової обробки перевіряють рівномірність різьблення за допомогою відповідних приладів і методів перевірки. За результатами вимірювань визначають накопичену похибка кроку різьблення - різниця між фактичним і заданим відстанню між будь-якими однойменними (не сусідньої) профілями витка різьби в осьовому перерізі по лінії, паралельній осі гвинта. Величина накопиченої похибки кроку різьблення не повинна перевищувати 0,04 мм на довжині 300 мм.