Термічна обробка стали
1. Вивчити теоретичні основи термічної обробки сталі
2. Вивчити СТО та її застосування на практиці.
Термічна обробка стали
1. Теоретичні основи ТО.
Термічною обробкою називається сукупність операцій нагрівання, витримки та охолодження твердих металевих сплавів, з метою отримання заданих властивостей за рахунок зміни внутрішньої будови і структури.
ТО термічна обробка.
Так як основними факторами будь-якого виду ТО є температура і час, то режим ТО зазвичай представляється графіком в координатах t - # 63; ,
де t - температура;
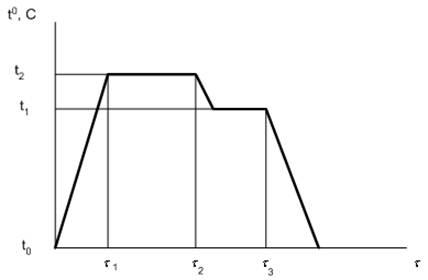
Кут нахилу характеризує швидкість нагріву або охолодження. Постійна швидкість нагріву або охолодження зображується на графіку прямою лінією з певним кутом нахилу. В результаті ТО в сплавах відбуваються структурні зміни. Після ТО металеві сплави можуть перебувати в стані рівноваги (стабільному) і нерівноважному (метастабільних) стані.
Б. Види ТО стали
СТО - власне-термічна обробка (передбачає тільки температурний вплив на метал).
ТМО - термомеханічна обробка стали (передбачає зміну структури металу за рахунок як термічного, так і деформаційного впливу).
ХТО - хіміко-термічна обробка стали (в результаті взаємодії з навколишнім середовищем при нагріванні змінюється склад поверхневого шару металу і відбувається його насичення різними хімічними елементами).
Включає: отжиг, нормалізацію, загартування, відпустка і старіння.
Складається в нагріванні до певної температури з подальшою витримкою і повільним охолодженням в печі для отримання рівноважної, менш жорсткої структури, вільної від залишкових напружень.
Відпал I роду: не пов'язаний з фазовими перетвореннями в твердому стані. Залежно від призначення розрізняють наступні види відпалу I роду: дифузний, рекрісталлізаціонний і отжиг для зняття внутрішніх напружень.
Дифузійний відпал, або гомогенізація, є різновидом відпалу, що застосовується з метою усунення в легованої сталі (як і в інших сплавах) дендритних ліквації.
При дифузійному відпалі з метою інтенсифікації дифузійних процесів сталь нагрівається до 1000--1100 ° С і піддається тривалій витримці (18--24 ч). Для усунення крупнозернистості після гомогенізації проводиться звичайний отжиг, або нормалізація.
Відпал рекристалізації. Цей вид відпалу проводиться з метою усунення наклепу холодного деформованого металу. Нагадаємо, що наклепаного метал дуже твердий і крихкий, його кристалічна решітка внаслідок високої щільності дислокацій і наявності великої кількості інших дефектів (вакансій, переміщених в міжвузля атомів), а також з-за спотворень і великих внутрішніх напружень знаходиться в нерівноважному стані, володіючи великим запасом надлишкової вільної енергії. У сильно наклепаного металі через злиття дислокацій в місцях їх скупчення спостерігаються небезпечні дефекти - зародки тріщин.
Отже, в ряді випадків наклеп доводиться усувати. Для цього потрібно нагрів, стимулюючий дифузійні процеси. Наклеп можна усунути, застосовуючи вже розглянутий звичайний отжиг. Однак відпал рекристалізації через значно більш низької температури і набагато меншої тривалості його проведення при практично однакових результатах потребує менше часу.
Температура нагріву при цьому виді відпалу вибирається на 150--250 ° С вище температури рекристалізації (Гр) оброблюваного сплаву. Це найменша температура, необхідна для протікання в наклепаного металі процесів, які повертають йому вихідні (до деформації) значення характеристик механічних та інших властивостей.
Відпал рекристалізації вуглецевої сталі виробляється при температурі нагріву в межах 600-700 ° С.
Самостійна робота: отжиг для зняття внутрішніх напружень.
Нормалізація. Особливостями режиму цього виду термообробки є температура нагріву і охолодження на спокійному повітрі. Ці особливості обумовлені специфічними цілями нормалізації. Стосовно до доевтектоїдних стали, особливо низьковуглецевих (0,05--0,25% С), нормалізація за більш короткий час і при більшій простоті режиму охолодження дозволяє отримати ті ж результати, що і при відпалі, т. Е. Вельми ефективне подрібнення зерна у литих і кованих заготовок.
Так як охолодження на повітрі забезпечує більш високу ступінь переохолодження аустеніту, ніж при відпалі, то продукти його розпаду виявляються більш дисперсними. Внаслідок цього нормалізацією можна отримати більш сприятливу дрібнозернисту структуру стали, що володіє підвищеними характеристиками міцності властивостями.
У ряді випадків, коли від матеріалу виробу не потрібно підвищених характеристик міцності властивостей, нормалізація замінює загартування. Особливо це стосується деталей з низьковуглецевої сталі, для яких застосування гарту виключається через дуже високою критичної швидкості гарту.
При нормалізації заевтектоідних сталей через прискорений виділення з аустеніту надлишкового (вторинного) цементиту небажана цементітная сітка навколо перлитових зерен не утворюється. У зв'язку з цим однією з цілей нормалізації є руйнування згаданої сітки у заевтектоідних сталей.
Критична швидкість загартування має дуже важливе значення. Від неї залежить таке технологічне властивість стали, як прокаліваемость, т. Е. Здатність гартуватися на певну глибину.
Таким чином, введенням в сталь вуглецю і легуючих елементів можна підвищити прокаліваемость.
Оскільки зміна швидкості охолодження від поверхні в глиб деталі залежить від температури і роду охолоджуючої середовища, то при оцінці прокаливаемости слід враховувати і ці чинники.
Однією з цілей легування конструкційних сталей є зменшення критичної швидкості гарту і отримання наскрізної прокаливаемости виготовлених з них деталей при загартуванню не тільки у воді, але і в більш структурно-фазового складу. Інтенсивність і результат цих перетворень залежать від температури відпустки.
До першої групи входять ріжучий і вимірювальний інструменти, а також штампи для холодного штампування. Від їх матеріалу потрібні висока твердість (понад 58 HRC) і хоча б невеликий запас в'язкості.
Другу групу складають пружини, ресори та інші вироби, від матеріалу яких потрібне поєднання високої межі пружності з задовільною в'язкістю.
Третя група виробів включає більшість деталей машин, що випробовують статичні і особливо динамічні або циклічні навантаження. При тривалій експлуатації виробів від їх матеріалу потрібне поєднання задовільних міцнісних властивостей з максимальними показниками в'язкості.
Способи загартування стилі. Вибір способу охолодження нагрітої під загартування сталевої деталі залежить від її форми і розмірів і хімічного складу сталі.
Найбільш простий спосіб загартування - це загартування в одному охолоджувачі, при якому нагріта деталь занурюється в охолоджуючу рідину і залишається там до повного охолодження. Недоліком цього способу є виникнення значних внутрішніх напружень. Для вуглецевих сталей перетином більше 5 мм закалочной середовищем є вода, для деталей менших розмірів і легованих сталей - масло.
Для зменшення внутрішньої напруги застосовується гарт в двох середовищах, при якій деталь спочатку охолоджують у воді до 300--400 ° С, а потім для остаточного охолодження переносить в масло. Недоліком цього способу є складність регулювання витримки деталей в нерпою охолоджуючої рідини.
Отже, в залежності від температури нагріву існує три види відпустки: низькотемпературний (низький), середньотемпературна (середній) і високотемпературний (високий).
Самостійна робота: відпускна крихкість I, II роду і способи її усунення.
Відпал: нагрів до певної температури з подальшою витримкою і повільним охолодженням в печі.
Нормалізація: нагрів до аустенітного стану.
Загартування: нагрів вище температур фазових перетворень, витримці і охолодженні з високою швидкістю.
Відпустка: нагрів нижче критичної точки і наступним охолодженням.
Поліпшення: гарт з високим відпусткою (покращує загальний комплекс механічних властивостей, найбільш ефективна ТО для конструкційних сталей).