Зубчасті колеса з Цементовані сталей.
Зубчасті колеса широко застосовують в машинах, механізмах і приладах різних галузей машинобудування. Найкраща макрострутура у зубчастих коліс виходить при штампуванні, коли розташування волокон відповідає конфігурації колеса, так як в цьому випадку міцність на вигин підвищується.
При виборі стали для виготовлення зубчастих коліс необхідно враховувати її вартість, оброблюваність, прокаліваемость і деформацію колеса при термічній обробці. Так як основним елементом зубчастого колеса є зуб, що застосовуються стали і методи зміцнення повинні забезпечувати високу контактну і втомну міцність, міцність при вигині, ударі і зносостійкість зуба.
Цементовані зубчасті колеса виготовляють з сталей 20Х, 12ХНЗА, 12Х2Н4А, 20Х2Н4А, 25ХГМ, 20ХН2М, 18ХГТ, 25ХГТ, ЗОХГТ, 20ХГР, 18Х2Н4ВА і ін.
Для підготовки структури до обробки коліс на металорізальних верстатах і для поліпшення механічних властивостей готових зубчастих коліс штамповані заготовки перед обробкою на металорізальних верстатах піддають термічній обробці - відпалу (повного, ізотермічного) або нормалізації, або нормалізації з високим відпуском.
Найкращою для різання (отримання найменш шорсткою поверхні металу) є структура після ізотермічного відпалу по режиму: нагрів до температури в точці Ас3 + 50 ° С, витримка, крапювременное переохолодження до 480-500 ° С і ізотермічна витримка при 580-600 ° С.
Для штампованих заготовок з цементуемих хромомарганцовістих і хромонікелевих сталей застосовують також прискорене охолодження штампованих заготовок від температури кінця кування до 500-600 ° С з подальшим використанням залишкового тепла.
Для газової цементації зубчастих коліс застосовують муфельні і безмуфельні печі. Зазвичай обробку проводять на поточних лініях, в які входять штовхальних піч для газової цементації, механізований гартівний бак, промивна машина, піч для відпустки, камера для охолодження коліс після відпустки. Температура в печі для газової цементації по довжині робочої камери підтримується рівній температурі цементації, а у розвантажувального кінця температура знижується до температури подстуживания.
Для отримання зубчастих коліс з твердістю поверхні зубів HRC ≥ 60 і зменшення биття зубів по початковій окружності застосовують процес нітроцементації в безмуфельних агрегаті. Зубчасті колеса, наприклад зі сталі 25ХГМ, піддають нітроцементації при 870 ° С, подстужівают до 840 ° С, охолоджують в гарячому маслі з температурою 160-180 ° С і відпускають при 160-180 ° С; одержувана твердість поверхні зуба HRC 60-65, серцевини HRC 35-45.
Для зменшення деформації з убчатих коліс застосовують такі способи:
1) ступінчасту загартування; нагріті зубчасті колеса охолоджують у ванні з маслом або розплавленою сіллю з температурою 150-180 ° С і після витримки у ванні до вирівнювання температури по перетину зубчастого колеса до температури ванни охолоджують на повітрі до температури 20 ° С;
2) загартування на спеціальних фіксуючих оправках, які встановлюють в отворі зубчастого колеса;
3) ступінчасту загартування в поєднанні з фіксують оправками; зубчасте колесо поміщають на оправлення після витримки його в гарячому середовищі і потім охолоджують до температури 20 ° С разом з оправкой; 4) загартування в автоматизованих пресах; нагріте зубчасте колесо встановлюють на нижній штамп, затискають верхнім штампом і в такому вигляді занурюють в гартівний бак з маслом.
Зубчасті колеса з поліпшуються сталей.
Зубчасті колеса виготовляють з поліпшуються сталей, наприклад 45, 40Х, 40ХН та ін. А та кож з стали 55ПП зниженою прокаливаемости. Залежно від умов роботи зубчасті колеса піддають різної термічній обробці. нормалізації, поліпшення, загартування і низького відпустки, ціанування (нітроцементації) з наступним загартуванням і відпусткою.
Зубчасті колеса, що працюють при низьких швидкостях і малих тисках, виготовляють зі сталі 45 і піддають нормалізації при 850-870 ° С (твердість НВ 170-217) або поліпшення загартуванні в воді від 820-840 ° С і відпуску при 520-550 ° С (НВ 220- 250).
Зубчасті колеса, що працюють при значних навантаженнях, що вигинають і невеликих швидкостях, виготовляють з легованих середньовуглецевих сталей і піддають поліпшенню - загартуванню в маслі і відпустці при 600-650 ° С (НВ 230- 260).
Зубчасті колеса, що працюють при середніх швидкостях, середніх тисках і невеликих ударних навантаженнях, виготовляють з легованих середньовуглецевих сталей. Режими термічної обробки зубчастих коліс з цих сталей наступні: а) загартування в маслі і відпустка при 180-200 ° С (HRC 50-55); б) ціанування (нитроцементация) при 830-850 ° С, гарт в маслі і відпустка при 180-200 ° С (HRC 55-60); товщина шару повинна бути в межах 0,2-0,3 мм, для чого необхідна витримка 30-50 хв при ціанування і 1-2 ч при нітроцементації.
Великого поширення в заводській практиці отримала поверхневе загартування зубчастих коліс при індукційному нагріванні. Загартування в цьому випадку проводиться двома методами:
1) з наскрізним нагріванням зубів;
2) з нагріванням тільки контактних поверхонь зуба (гарт «ПО зубу») або з одночасним нагріванням контактних поверхонь і западини (гарт «по западині»).
При загартуванню з наскрізним нагріванням зубів зубчастих коліс з сталей, наприклад 45, 40Х, в індукторі нагріваються (до 850 870 ° С), а потім охолоджуються (водяним душем або зануренням зубчастого колеса в масло) відразу всі зуби зубчастого колеса. Зуби прогартовуються наскрізь. На деяку глибину (до 5 мм) гартується також і обід зубчастого колеса. Після гарту здійснюють низький відпустку; твердість поверхні зуба HRC 58-60, а серцевини - HRC 45-55. Цей метод застосовують при загартуванню зубчастих коліс, слабо навантажених і малого модуля (до 4 мм), так як весь зуб має високу твердість і можливі його поломки в процесі експлуатації. Зубчасті колеса з модулем понад 4 мм гартувати цим способом недоцільно.
Методом гарту з наскрізним нагріванням зубів можна зміцнювати і важко навантажених зубчасті колеса (середнього модуля 4-10 мм), виготовлені зі сталі зниженої прокаливаемости. У цьому випадку застосовують об'ємно-поверхневу загартування (при глибинному індукційного нагрівання) - спосіб, розроблений професором К. З. Шепеляковскім і застосовуваний на багатьох заводах. При поверхневому загартуванні з глибинним нагріванням необхідним є застосування інтенсивного охолодження об'єктів, що швидко водою (потоком води або душем). Для виконання такого охолодження застосовують спеціальні гартівні пристрої, одне з яких показано на рис. 1. Вода подається по трубопроводу 1 діаметром 150 мм; проходить по кільцевому пазу 2, який направляє її в зазор між оброблюваних зубчастим колесом 3 і індуктором 4. До включення гартівна вода знаходиться на рівні 5. Така система охолодження дає хороші результати при загартуванню зубчастих коліс модулем 6-10 мм.
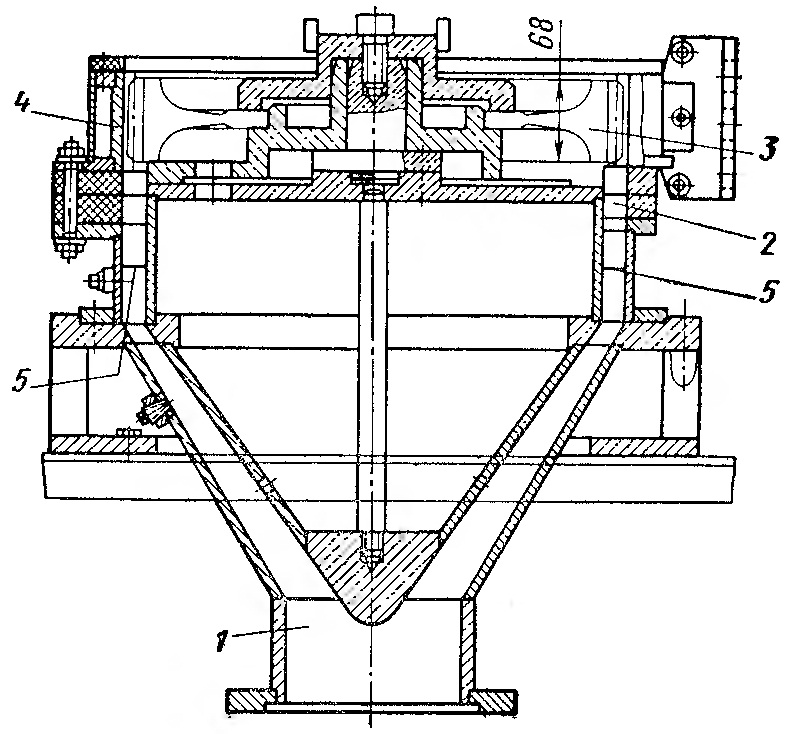
Мал. 1. гартівно пристрій з подачею охолоджувальної рідини паралельно гартує поверхні в зазор між індуктором і зубчастим колесом.
Режим гарту зубчастих коліс з модулем 6 мм наступний
частота струму 2650 Гц, загальний час нагрівання 90 с, температура нагріву 850 ° С, тривалість охолодження (гартування з самоотпуском при 200-210 ° С, що еквівалентно відпустки в печі при 150-160 ° С) 6,5 с, витрата охолоджуючої води 100 л / с, продуктивність 30 деталей за годину.
В результаті такого гарту виходить шар високої твердості (HRC 59-61) товщиною (біля кореня зуба) 1,9 мм, розташований по контуру зубів і западин (рис. 2), що забезпечує велику зносостійкість, контактну і втомну міцність зубів. Серцевина зуба має твердість HRC 30-35, що забезпечує його високу міцність.
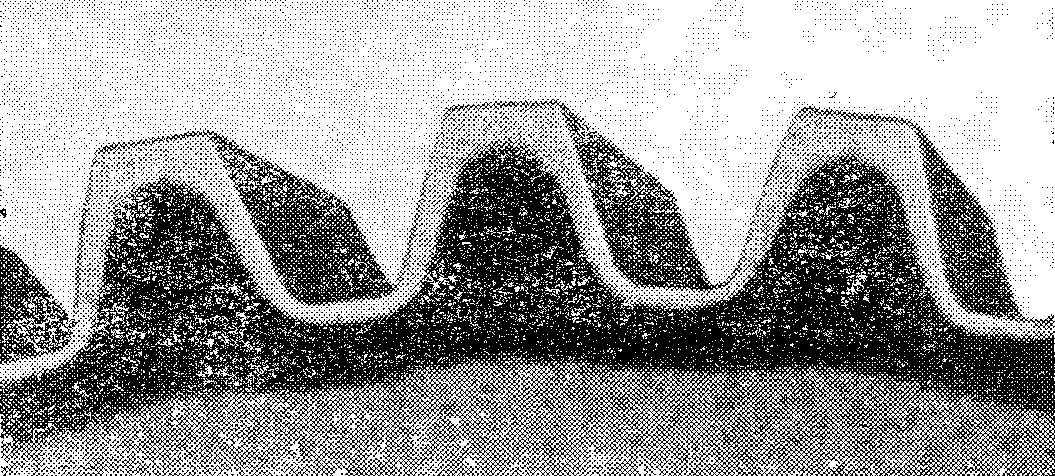
Мал. 2. Макроструктура зубчастого колеса зі сталі зниженої прокліваемості загартованого при глибинному нагріванні
Зубчасті колеса зі сталі зниженої прокаливаемости, зміцнені об'ємно-поверхневого загартуванням (при глибинному індукційного нагрівання), по статичній, динамічній і втомної міцності зубів перевершують такі ж зубчасті колеса з хромомарганцетітанових, хромонікелевих і інших сталей, піддані цементації і загартування.
Великогабаритні зубчасті колеса гартують методом «по зубу» (рис. 3, а) або «по западині» (рис. 3, 6). Недолік методу загартування «по зубу» - зниження втомної міцності зуба. Причина цього недоліку - концентрація напруг на кордоні загартованого шару і поверхні зуба. При загартуванню по западині найбільш навантажене місце зубчастого колеса гартується, вихід напруг, що розтягують на поверхню вершини зуба не є небезпечним, так як це місце зуба не відчуває будь-яких навантажень. Для поверхневого гартування зубчастих коліс застосовують різні індуктори, nозволяющіе проводити загартування методом «по зубу» або «по западині» одночасним або безперервно-послідовним способом.
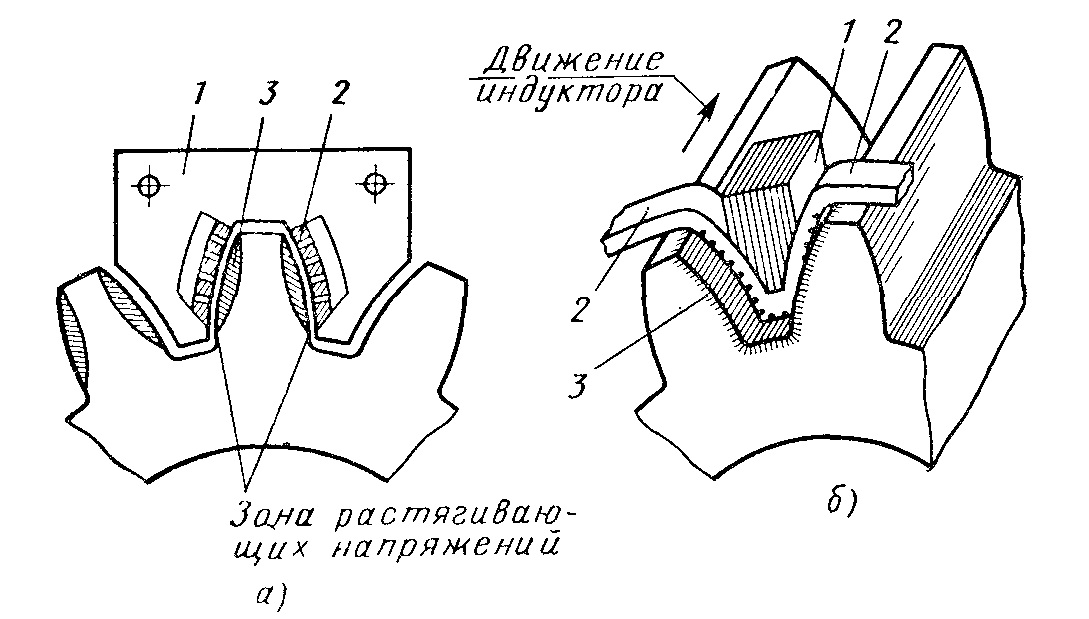
Мал. 3. Схема позубной гарту зубчастих коліс:
а - "по зубу"; б - "по западині"; 1 - магнітопровід; 2 - індукуючий дріт; 3 - нагрітий шар.
Поверхневе загартування зубчастих коліс здійснюється на спеціальних верстатах і установках.
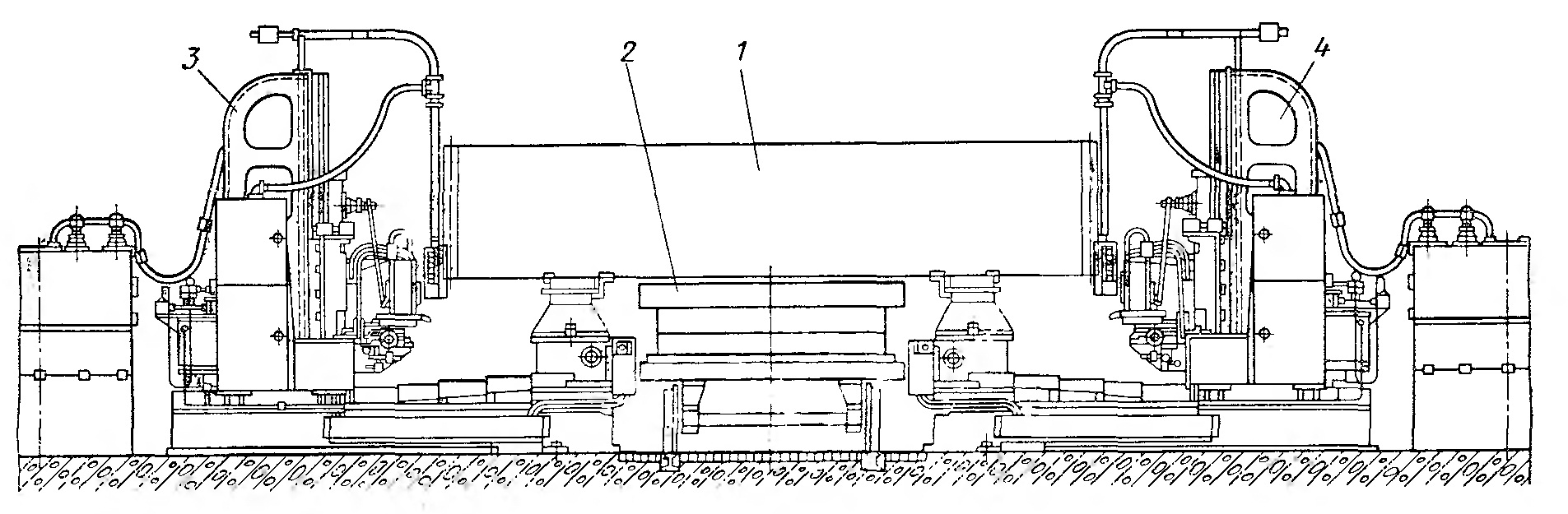
Мал. 4. Установка для високочастотної гарту великогабаритних зубчастих коліс
При загартуванню «по западині» одночасним способом індуктор 1 (рис. 5) вводять між зубів з зазором між індуктором і нагрівається поверхнею 2-2,5 мм. При цьому нагріваються западина і обидві сусідні поверхні по всій довжині зуба. Спрейера 2 подстуживания безперервно охолоджують зовнішні поверхні нагріваються зубів щоб уникнути відпустки раніше загартованих поверхонь. Після закінчення нагрівання, що триває кілька секунд, індуктор 1 виводять з западини, і після паузи (для вирівнювання температури) з гартівних спрейера 3 нагріта поверхня охолоджується водою протягом часу, що забезпечує загартування з самоотпуском. Після закінчення гарту зубчасте колесо 4 повертають на один зуб, індуктор вводять в чергову западину між зубами і процес повторюють.
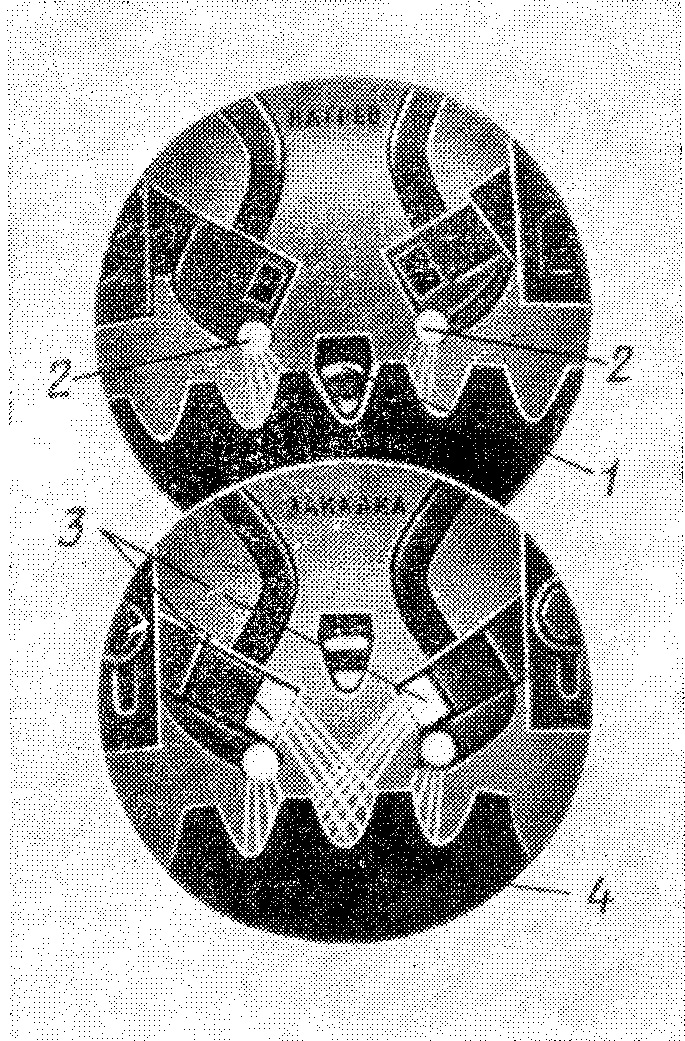
Мал. 5. Схема гарту зубчастого колеса по западині
Іноді при загартуванню крупномодульних зубчастих коліс на деяких зубах на стороні, протилежної попередньої гарту, через виникнення теплових і структурних напруг з'являються тріщини. Щоб уникнути появи тріщин, доцільно застосовувати спосіб гарту «по западині через зуб», що полягає в наступному. Спочатку проводять першу індукційну загартування «по западині через зуб» (рис. 6).
Мал. 6. Схема гарту зубчастого колеса по западині через зуб
Після першої гарту зубчасте колесо піддають відпустці при 180-200 ° С. Після відпустки гартують необроблені боку зубів, а потім знову проводять низький відпустку. При такому способі тріщини на поверхні зубів не виникають.