Формування скла - основна і найважливіша після скловаріння технологічна стадія виробництва виробів зі скла. Сукупність цих двох безпосередньо пов'язаних процесів визначає тип скляного виробництва, його технічний рівень і економічну ефективність. Формування скла зводиться до перетворення в'язкого розплаву (скломаси) в тверде виріб заданої конфігурації в результаті застосування певного силового впливу до об'єкта формування і його поступового охолодження і затвердіння. Таким чином, в процесі формування скло в результаті його охолодження переходить зі стану в'язкої рідини через пластичне в тверде крихке стан, т. Е. Процес формування пов'язаний зі зміною в'язкості в широкому інтервалі температур. Відповідно до цього інтервалу температур в'язкість скла в процесі формування змінюється від 102 до 1012 Па-с, причому саме на завершальному етапі формування відбувається найбільш значне збільшення в'язкості.
Температурний хід в'язкості, т. Е. Зміна в'язкості з температурою для різних за складом стекол, істотно впливає на їх плинність, здатність до деформування і твердненню, отже, на весь процес їх формування. Розрізняють два різновиди стекол - «короткі» і «довгі». Для «коротких» стекол характерно різке зростання в'язкості при охолодженні, т. Е. Для них характерний більш короткий температурний інтервал, отже, вони швидше втрачають деформаційних здатність (рухливість, плинність, пластичний стан) і швидше тверднуть. «Довгі» скла відрізняються поступовим і помірним зростанням в'язкості при охолодженні. Отже, зберігають здатність до деформації і твердненню більш широкому інтервалі температур, т. Е. Більш повільно. Отже, зміна в'язкості скла з температурою пределяет вибір того чи іншого способу формування. Загальний хід процесу формування можна умовно розділити на дві стадії: формоутворення і фіксація форми. Під час першої стадії пластичної стекломассе надають необхідну Лорм вироби. На стадії фіксації форми форма вироби закріплюється в результаті твердіння скломаси, характер якої зумовлений видом вироби і способом його охолодження.
Існує велика кількість способів формування скла, які розрізняють за характером впливу на стекломассу, виду вироблених зі скла виробів і принципу взаємодії скломаси з форми органами і пристроями. Найбільш поширені способи формування: видування, пресування, пресовидування, відцентрове формування, витягування, прокатка, формування на підкладці металу, моллірування, виливок, пресування. У виробництві сортового посуду і високохудожніх виробів в основному використовують видування, пресування, пресовидування і відцентрове формування.
Видування - найпоширеніший спосіб циклічного формування порожнистих штучних виробів - здійснюється під впливом равнодействующих розтягуючих зусиль, створюваних у внутрішній порожнині виробу, що формується стисненим повітрям (тиском 0,2 ... 0,3 МПа). Виробляють вироби як вручну (ручне видування), так і механізованим способом.
Незважаючи на те, що ручне видування малопродуктивні і вимагає великих фізичних зусиль, цей спосіб незамінний при виробництві високохудожніх виробів складної конфігурації з кришталю. Основний інструмент при ручному видуваніі- склодувна трубка.
Процес видування складається з наступних операцій:
1) попередньо нагріту до температури прилипання склодувну трубку опускають в скломасу і набирають її на трубку;
2) набрану на кінець трубки стекломассу закочують на металевій плиті або в інших пристроях (катальні-ках або делок) і з неї видувають баночку (при наявності металевої баночки або складальної головки ця операція відсутня);
3) на підготовлену баночку повторно набирають скломасу в кількості, необхідній для вироблення вироби; доручену набір роздмухують в «пульку», яка по конфігурації наближається до готового виробу;
4) видувають виріб заданої конфігурації і розмірів в формах.
Форми для ручного видування виготовляють преимуществен але з металу, іноді з дерева, вогнетривких матеріалів і т. Д.
Відмітна особливість більшості виробів, видуває мих на трубці, полягає в тому, що їх верхня частина (горло), будучи до кінця формування з'єднана з трубкою і, перебуваючи під час всього процесу поза формою, не набуває необхідної конфігурації і в місці зчленування трубки з виробом в його верхній частині утворюється ковпачок або віночок. Таким чином, отримане після відділення від трубки виріб по суті є ще напівфабрикатом і його край потрібно додатково обробляти (обрізанням, шліфуванням, поліруванням або отопку).
Ручним видуванням вироби виробляють бригадним методом. Зазвичай одна бригада, що складається з 5 ... 6 осіб, виготовляє 850 ... 1000 виробів на ніжці (або 200 ... 300 ваз для квітів). Впровадження в ручне виробництво засобів малої механізації (наприклад, одночасне видування пійла вироби і формування фігурної ніжки, використання ланцюгових конвеєрів) значно підвищує продуктивність праці.
При механізованому способі різноманітний асортимент виробів видувають стисненим повітрям на різних стеклофор-мующіх агрегатах. Склоформ агрегати різняться принципом харчування їх стекломассой: крапельним (напівавтомати ВВ-2, автомати АБ-6, АВ-6, ВВ-7, IS-6, S-10) і вакуумним (автомати ВВ-6; ВС-24).
У стеклоформующих машинах вироби видуваються в положенні або дном вгору, або дном вниз. Як правило, в машинах з крапельним харчуванням видування в чорновій формі проводиться дном вгору, потім заготівля перевертається і видування в чистовий формі закінчується дном вниз. На машинах з вакуумним харчуванням вироби видуваються і в чорнових, і в чистових формах дном вниз.
Розглянемо послідовність формування на прикладі видування склянок. Після вдавлення плунжера I відбувається попереднє вільне видування II, поворот і витягування III. Остання стадія IV - видування в формі при одночасному обертанні трубки.
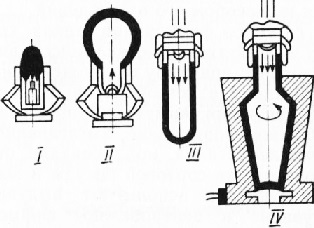
Мал. 1. Послідовність механізованого видування склянок на автоматах з вакуумним харчуванням: 1 - набір порції скломаси після вдавлення плунжера, 11 - попереднє вільне видування, III - поворот і витягування пульки, IV - видування вироби у формі при одночасному обертанні трубки
Пресування - найстаріший спосіб циклічного формування штучних виробів.
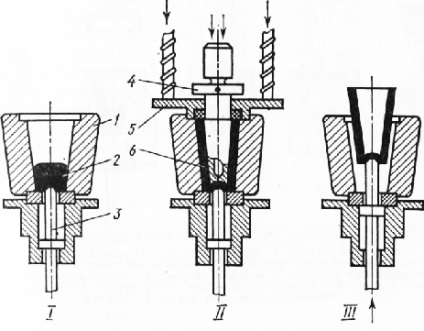
Мал. 2. Послідовність операцій прямого пресування скломаси: I - подача краплі скломаси в чистову форму (прес-форму), II - пресування вироби пуансоном формові кільцем, III - виштовхування готового виробу з прес-форми; 1 - під чистове прес-форма, 2 -порція скломаси, 3 - піддон-виштовхувач, 4 - пуансон, 5 - формове кільце, 6 - готовий виріб
Пресування буває пряме і непряме (литьевое). Як правило, прямим пресуванням виробляють вироби з розвиненою внутрішньою порожниною. У цьому випадку використовують ручні (ПСП -2), напівавтоматичні та автоматичні (АПП -12, АРП -10) преси.
Розглянемо послідовність операції прямого пресування (рис. 2). У чистову прес-форму подається порція скломаси у вигляді краплі. На неї опускається пуансон, що охолоджується зсередини водою і таким чином формується виріб, зовнішній контур якого обмежується стінками прес-форми, а внутрішній - пуансоном. Щоб стекломасса НЕ видавліва-
лась з прес-форми, на неї зверху накладають і притискають механізмом преса формове кільце. Після невеликої ви тримки (щоб виріб відразу не деформувалося) пуансон з формовим кільцем піднімають у вихідне положення, а виріб після охолодження і затвердіння видаляють з прес-форму за допомогою піддону-поршня 3. Пресування ведуть в нероз'ємних або розкривних формах при виготовленні складних асиметричних виробів .
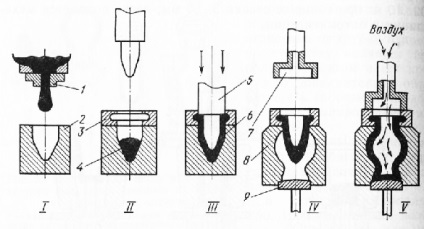
Мал. 3. Послідовність формування виробу методом пресовидування: I - подача порції скломаси в чорнову форму, II - підведення пуансона до чорнової формі, III - пресування горла вироби, IV - перенесення заготовки з чорновою в чистову форму, V -видуваніе вироби в чистовий формі; 1 - живильник, 2 - чорнова форма, 3 - формове кільце, 4 - порція скломаси, 5 - пуансон, 6 - кулька, 7 - дутьевая трубка, 8- чистове форма, 9 - піддон
Недолік цього способу в обмеженості застосування, наприклад цим способом можна формувати вироби з тонкими стінками (менше 2 мм), що розширюються донизу, з виступами або заглибленнями складної конфігурації на стінках. Крім того, поверхня виробів, одержуваних цим способом, невисокої якості (з кованими, тонкої матовістю) через різке охолодження скломаси і твердіння в контакті з поверхнею прес-форми в ході формування.
Пресів и дуван і е - спосіб формування виробів з в'язкої скломаси, в якому поєднується пресування пуансоном і видування. Цим способом виробляють, як правило, ши-рокогорлие вироби.
Розглянемо послідовність формування виробу способом пресовидування.
Існують склоформ машини (Гартфорд-28), в яких кулька в процесі формування залишається нерухомою, а переміщаються чорнова (відводиться в сторону) і чистове (піднімається до кульці знизу) форми.
Недолік цього способу формування в складності процесу і технології, однак цей спосіб забезпечувала-кість точне регулювання товщини і чітке відтворення геометричних розмірів формованих виробів.
Цент робежно е формування засноване на використанні відцентрової сили бистровращающейся форми. Цим способом формують порожні циліндричні або конічні вироби різного призначення з стекол, які важко піддаються формуванню (тугоплавких, «коротких», що кристалізуються).
Послідовність операцій при формуванні наступна. У форму подається точно відважені порція скломаси, і форма починає швидко обертатися. Створюється відцентрова сила, під впливом якої стекломасса рівномірно розподіляється по внутрішніх стінках форми, точно відтворюючи се конфігурацію. Чим більше частота обертання, тим більше Відцентрова сила і тим вище скло піднімається в формі. Тривалість формування 10 ... 15 с.
Вироби, відформовані цим способом, мають гладку блискучу поверхню навіть при складній конфігурації. При відцентрові формуванні в порівнянні з іншими способами скорочується витрата скломаси за рахунок того, що не утворюється формувальний ковпачок. Крім того, цей спосіб легко піддається механізації, завдяки чому скорочується кількість Ручної праці і знижується собівартість вироби.
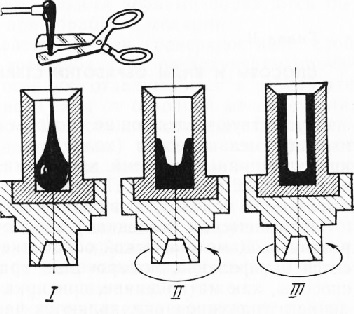
Мал. 4. Послідовність формування виробу відцентровим способом: I - ручний набір скломаси в форму для формування, II - початок підйому скломаси в формі в момент включення обертання форми, III - остаточне формування виробу