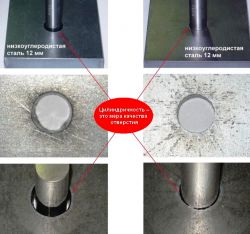
На сучасному металообробному заводі або підприємстві, які використовують у виробництві заготівельну технологію плазмового різання, виникає необхідність обробки отворів під болтове з'єднання. Зараз в технологічному процесі використовується наступний ланцюжок операцій:
На верстаті плазмового різання з числовим програмним управлінням обробляється контур деталі, поглиблення і отвори діаметром більш ніж від півтора до двох товщини оброблюваного металевого листа. Плазмою або маркером позначаються центру отворів під болтове з'єднання. Діаметром отворів можна порівняти з товщиною листа. Потім, в одному з двох режимах, або в автоматичному - дорогим і повільним, з портальних сверлением пневматичної сверлильной головкою. Або в другому режимі, менш точному і більш времязатратном - ручну дрилем на магнітах, корончата свердлами свердлити отвори потрібного діаметру.
Виробники оборядованія для плазмового різання металу і джерел плазми, давно були спантеличені даною проблемою. Свердління отворів в металі порівнянних розмірів, діаметрами з товщиною листа металу, є одним з основних недоліків нової сучасної і перспективної технології плазмового різання.
Для вирішення даної проблеми в рамках великих виробництв, недостатньо використання тільки новітніх і сучасних плазмових джерел, що створюють плазмову високотемпературну дугу з поверхнею розрізається листа.
В якості демонстрації високих точностних якостей нових плазмових джерел, демонструються зразки створені в лабораторних умовах. На сучасному верстаті плазмового різання і в умовах реального виробництва, можна отримати отвір в аркуші металу, нітрохи не поступається за якістю обробки гідроабразивного або лазерного різання металу.
Але як бути в умовах російського заводу? На реальному виробництві часто кваліфікації, досвіду і професіоналізму оператора явно недостатньо? Не можна виключати й інші фактори, які впливають на якість плазмового різання, якість металу, різкі перебої і скачки напруги, якості технічних газів і витратних матеріалів.
Необхідні глибші знання можливостей плазмового обладнання для різання металу. Використання технологічних можливостей джерела струму спільно з апгрейдом управляющейпрограмми в CAM модулі і можливостями системи числового програмного керування.
Компанія Hypertherm, є світовим лідерів з виробництва плазмових джерел для портальних верстатів плазмового різання металу. На виробництві Hypertherm була створена і запатентована новітня технологія плазмового різання металу - TRUE HOLE. TRUE HOLE створена для вирішення проблеми різання отворів під болтове з'єднання в листовому металопрокат.
Які проблеми в обробці отворів необхідно було вирішити:
- Необхідно вибрати між перегином або задиром всередині вирізуваного плазмою отвори в металі під болтове з'єднання (див. Рис. 1);
- Звуження нижнього діаметра отвору по відношенню до верхнього (На рис. 2 червона лінія - бажана форма, синя - реальна форма).
Які параметри різання необхідно виправити для отримання отвори бажаної форми:
1. Використовувати в якості як плазмообразующего так і та захисного газу кисню. Чистота технічного кисню 99,5%. Властивості газу - сухий, знежирений при тиску 793 кПа і витратою газу 4250 літрів на годину. Використання кисню викликано кращими властивостями горіння, що перевищують властивості горіння повітря.
2. Так як під час різання лінійних ділянок контурнойго розкрою, використовується повітря, як плазмообразующий газ, то вартість різання металу не така висока, як при використанні при постійній різання металу кисню. Необхідно автоматичне перемикання пологів газів на різних ділянках різання металу. На кисень в початковий момент різання отвору. Цього можна домогтися за умови внесення необхідної програмної вставки в G-код керуючої програми верстата плазмового різання металу.
3. Необхідно знизити подачу захисного газу під час різання якісних отвори під болтові з'єднання.
4. Для отримання найякіснішої форми отвори необхідно врізатися в лист металу строго в центр майбутнього отвору (див. Рис. 3). При цьому необхідно відключити компенсації руху дуги на величину радіуса вирізується в металі дуги.
5. Це можна отримати, також вплинув відповідне додавання в G-код керуючої програми на верстаті з ЧПУ в CAM модулі.
7. На кінцевій ділянці траєкторії плазмового різання металу, необхідно зменшення швидкості різання. Необхідна сила струму 20% від робочого значення. Вимкнення руху верстата через накопиченої інерційності руху головки.
8. Для цього необхідно додаткове втручання в G-код керуючої програми.
Виконання всіх перерахованих умов, дозволить отримувати дійсно якісні отвори по співвідношенню диметра і товщина розрізається плазмою листа металу 1: 1. (Рис. 4)
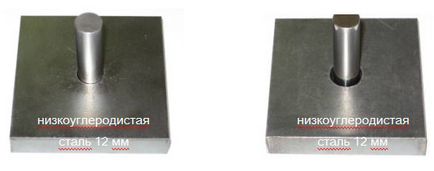
Дана технологія має наступні обмеження:
1. Тільки чорна сталь
2. Товщина від 3 до 25 мм
Нижче наведена таблиця товщини і робочих струмів, на яких можливе використання технології TRUE HOLE:
4. Існує ще одне обмеження для використання даної технології TRUE HOLE на необладнаних верстатах плазмового різання. Можливості порталу, на якому встановлений плазматрон обмежені - необхідно щоб портал підтримував певне прискорення в 40 мГ.
У зв'язку з перерахованими обставинами, виникають питання впровадження технології TRUE HOLE на сучасне підприємство. Можливі два варіанти:
- Перший - новий купується верстат плазмового різання повинен бути обладнаний цією технологією TRUE HOLE.
- І другий - глибока модифікація існуючого на проізводствеоборудованія.
Модернізація існуючого на виробництві верстата для плазмового розкрою листового матеріалу:
Для модернізації існуючого на виробництві обладнання, необхідно виконати деякі умови:
Спочатку апгрейдити плазмовий джерело до Hypertherm HPR 260 XD. Якщо на виробництві встановлено джерело струму відмінний від Hypertherm, то необхідна закупівля необхідного джерела плазми. В іншому випадку, якщо встановлено джерела струму попереднього покаления - Hypertherm HPR 130 або HPR 260, то необхідна заміна таких елементів:
1. Набір для модернізації - 228 524 - 1шт
- Новий пульт управління з прошивкою для джерела плазми
- Програмно апаратні засоби для ручної (або) автоматичного газового консолі і інструмент для їх заміни.
- Фітинги для з'єднання нової головки до кабелю.
2. Нова голівка плазматрона HPR260XD - 228521 - 1 шт
3. Кабель пальника 20 м - 228 547 - 1 шт.
4. Омічний кабель 45 м - 123 991 - 1 шт.
Для реалізації технології True Hole недостатньо мати в своєму арсеналі джерело струму Hypertherm HPR260XD.
Необхідна інтеграція в систему наступних опцій:
1. Автоматична газова консоль 078533 - 1шт.
2. ЧПУ EDGE PRO від компанії Hypertherm
3. CAM модуль TurboNest виробництво компанії MTC
4. Система контролю висоти плазмового різака Hypertherm.
У разі купівлі нового верстата плазмового різання металу, необхідно, щоб всі вищевказані пункти були включені в систему виробником обладнання.
Варто відзначити якісного виробника - американську компанію Retro Systems. Ця компанія використовує технологію True Hole від Hypertherm на своєму обладнанні на високому рівні якості.