Машинобудування висуває дуже високі вимоги до якості виробів, що виготовляються і перш за все до їх міцності, що розуміється в широкому сенсі як опір деформації і руйнування. Ці вимоги обумовлені все зростаючою напруженістю умов роботи деталей машин. При розрахунку деталей на міцність виходили з моделі суцільного твердого тіла, що володіє досконалою структурою, а для виготовлення їх розраховували використовувати прості за складом матеріали (наприклад, вуглецеві і низьколеговані сталі), що відрізняються високою технологічністю. У сучасних же агрегатах значна частина деталей піддається тривалим статичним навантаженням при підвищених температурах або повторним навантаженням (в тому числі і знакозмінних) при нормальних і підвищених температурах або ж працює в умовах впливу на них агресивних середовищ, різких теплових ударів чи радіоактивного випромінювання. Для виготовлення таких деталей потрібні високоміцні, жароміцні, кислототривкі металеві та неметалеві матеріали: стали, сплави, пластичні маси, що володіють підвищеними спеціальними властивостями (межею міцності, довготривалу міцність, межею повзучості, межею витривалості, опором термічної втоми, корозійну стійкість і т.д. ).
Стали і сплави, що задовольняють цим вимогам, як правило, відрізняються складним складом і характеризуються більш низькими технологічними властивостями, що дуже ускладнює виготовлення з них виробів, а в ряді випадків при водить до необхідності створення нових технологічних процесів для додання їм необхідних форми і властивостей.
Вимога поєднувати зазначені вище властивості з малою масою вироби зумовило застосування складових конструкцій, наприклад з металевих і неметалевих матеріалів, з'єднаних склеюванням і пайкою.
Методи розрахунку деталей, що працюють у важких умовах навантаження, на міцність значно складніше, особливо це відноситься до розрахунків деталей авіаційної і ракетної техніки, оскільки в цих випадках конструктор, прагнучи максимально полегшити виріб, виходить з мінімального запасу міцності.
Наприклад, для основних деталей авіаційних двигунів (колінчастий вал, шатун, лопатки і диск турбіни і компресора) мінімальний запас міцності 1,3. 1,5, в той час як в загальному машинобудуванні і будівельній практиці він доходить до 10. 15.
Як відомо, теоретичні значення міцності металу, що розраховуються за величиною енергії, що витрачається на освіту двох нових поверхонь при подоланні міжатомних зв'язків в ідеальній гратах монокристалла, у багато разів вище значень «технічної» міцності, одержуваних при випробуванні реальних зразків того ж металу.
Так, для чистого заліза теоретичне значення міцності> 10000 МПа, а технічне -250 МПа. Ця розбіжність пояснюється наявністю різного роду дефектів-недосконалостей будови кристалічного тіла, вплив яких на властивості цього тіла настільки значно, що сучасну фізику твердого тіла часто визначають як фізику дефектів. До таких дефектів - недосконалостей тонкої структури - відносять перш за все дислокації, тобто особливі зони спотворень атомної решітки, що містяться в реальних кристалах в величезних кількостях (близько 10 8 / см 2).
До дефектів більш грубого порядку відносять субмикроскопические тріщини, за розмірами не перевищують межі дозволу оптичного мікроскопа (: 50,2 мкм). такі
тріщини, відповідно до гіпотези Гриффитса, можуть утворюватися по межах блоків кристала в процесі його росту, а також з'являтися в результаті додатка напружень.
У реальному металі - поликристаллическом тілі - зустрічаються ще більш грубі дефекти, наприклад, мікроскопічні тріщини розмірами> 0,2 мкм. Такі тріщини виникають на поверхні сталевих деталей в процесі їх механічної обробки або експлуатації.
Незважаючи на незначну (близько декількох мікрометрів) глибину, ці тріщини різко знижують міцність деталі (особливо при роботі в умовах складного напруженого стану або впливу поверхнево середовищ), прискорюючи її руйнування. Видалення пошкодженого поверхневого шару механічно (зачисткою тонкою шкіркою, піскоструминної обробкою) або електролітичним розчиненням істотно підвищує міцність деталі.
Найбільш грубими є мікроскопічні, видимі в ряді випадків неозброєним оком дефекти, що представляють собою різного роду порушення цілісності або однорідності металу. Ці дефекти можуть стати причиною особливо сильного зниження міцності деталі і її руйнування. Зі збільшенням розмірів деталі ймовірність наявності дефектів зростає, тому реальне зниження міцності на великогабаритних деталях виявляється більш помітно (масштабний фактор).
Найбільш детально вплив дефектів на працездатність конструкцій вивчено для виробів, виконаних зварюванням. У більшості випадків ступінь впливу того чи іншого дефекту на працездатність конструкцій встановлюють експериментально: випробуваннями зразків з дефектами.
При здачі конструкції в експлуатацію насамперед оцінюють допустимість наявності зовнішніх дефектів. Значення їх допустимості, як правило, вказані в технічних умовах на виготовлення конструкції і залежать від умов її експлуатації.
Встановлено, що опуклість шва не знижує статичної міцності, однак дуже впливає на вібраційну міцність. Чим більше опуклість шва і, отже, менше кут переходу від основного металу до наплавленого, тим сильніше воно знижує межа витривалості. Таким чином, надмірна опуклість шва може звести до нуля всі переваги, отримані від оптимізації технологічного процесу щодо поліпшення якості зварних з'єднань, що працюють при вібраційних (див. Захист від вібрації), динамічних і повторно-статичних навантаженнях.
Значним (за впливом на працездатність) зовнішнім дефектом є підріз. Він неприпустимий в конструкціях, що працюють на витривалість. Невеликої довжини підрізи, що ослабляють перетин шва не більше ніж на 5%, в конструкціях, що працюють під дією статичних навантажень, можна вважати дозволеним.
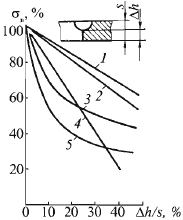
Мал. 1. Вплив відносної глибини Δh / s непровару кореня шва на статичну міцність стикових з'єднань (без опуклості): 1 - Ст3; 2 - сталь 12X 18H9T; 3 - сталь 25ХГФА; 4 - сплав Дl6T; 5 - сталь 30ХГСНА.
Напливи, різко змінюючи обриси швів, утворюють концентратори напружень і, тим самим, знижують витривалість конструкції.
Напливи, які мають велику протяжність, слід вважати неприпустимими дефектами, так як вони викликають концентрацію напруг і нерідко супроводжуються непроварами. Невеликі місцеві напливи, викликані випадковими відхиленнями зварювальних режимів від заданих, вирішуються.
Кратери, як і пропали, у всіх випадках є неприпустимими дефектами і підлягають виправленню.
Для остаточної оцінки якості зварного з'єднання контролер повинен знати значення допустимості зовнішніх і внутрішніх дефектів, які вказані в НД. Результати численних досліджень показують, що для пластичних матеріалів при статичному навантаженні (рис. 1, криві 1, 2, 4) вплив величини непровару на зменшення їх міцності прямо пропорційно відносної глибині непровару. Для малопластичних і високоміцних матеріалів при статичному (див. Рис. 1, криві 3, 5), а також при динамічної або вібраційної навантаженні (рис. 2) пропорційність між втратою працездатності та величиною дефекту порушується.
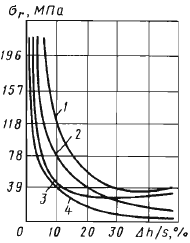
Мал. 2. Вплив відносної величини Δh / s дефектів на міцність від утоми стикових з'єднань з низьковуглецевих сталей (без опуклості): 1 - підрізів; 2 - пор; 3 - непровари; 4 - шлаків.
Встановлено, що пори і шлакові включення при їх відносної сумарної площі в перерізі шва до 5. 10% практично мало впливають на статичну міцність з'єднання (рис. 3). Якщо шви мають значну опуклість, то пори і шлакові включення сумарною площею (розміром) 10. 15% від перетину шва слабо позначаються на статичної міцності. Для ряду конструкцій (закладні деталі, стики арматури) в залежності від місця розташування таких дефектів їх допустима величина може складати 10. 25% від перетину шва.
Такі дефекти, як тріщини, оксидні плівки, несплавлення, неприпустимі.
З урахуванням всіх перерахованих конструктивно-експлуатаційних чинників для альтернативної оцінки небезпеки впливу зварювальних дефектів їх доцільно розділити на дві групи: об'ємні і площинні. Об'ємні дефекти не роблять істотного впливу на працездатність з'єднань. Ці дефекти (пори, шлаки, флок) можна нормувати за розмірами або площі ослаблення ними перетину вироби. Площинні тріщиноподібні дефекти (тріщини, оксидні плівки, несплавлення, гуркіт) по НТД, як правило, вважаються неприпустимими.
При виявленні неприпустимих зовнішніх або внутрішніх дефектів їх обов'язково видаляють. Видалення зовнішніх дефектів слід про водити вишліфовкой із забезпеченням плавних переходів в місцях виборок. Місця вибірок годі й заварювати в разі, якщо збереглася мінімально допустима товщина стінки деталі в місці максимальної глибини вибірки. Дефекти з кореня шва видаляють по всій довжині врівень з основним металом. Якщо в процесі механічної обробки (вишліфовкі) не вдалося повністю виправити зовнішні дефекти, то їх як недопустимі внутрішні дефекти необхідно повністю видалити.
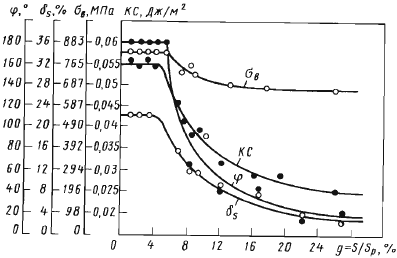
Мал. 3. Вплив відносної площі дефектів (пор) на механічні властивості стикових з'єднань з легованої сталі (σв = 850 МПа після гарту і відпустки).
Заглиблення зовнішні і внутрішні дефекти (дефектні ділянки) в з'єднаннях з алюмінію, титану та їх сплавів слід видаляти тільки механічним способом: вишліфовкой абразивним інструментом або різанням, а також вирубкою з подальшою зашліфовкі.
У ряді випадків в конструкціях із сталі допускається видаляти дефектні ділянки повітряно-дугового або плазмової струганням обробкою поверхні вибірки абразивними інструментами. При цьому поверхні виробів з вуглецевих і кремніймарганцевистих сталей повинні бути зачищені (зашліфовані) до повного видалення слідів різання.
Виправлення дефектів з заваркою вибірок в зварних з'єднаннях, які підлягають обов'язковій термічній обробці і виконаних з легованих і хромистих сталей. потрібно проводити після високого (450. 650 o С) відпустки зварного з'єднання (проміжного, арешту чи), за винятком окремих випадків, обумовлених технологічними інструкціями.
При видаленні дефектних місць доцільно дотримуватися певних умов. Довжина видаляється ділянки повинна бути дорівнює довжині дефектного місця плюс 10. 20 мм з кожного боку, а ширина оброблення вибірки повинна бути такою, щоб ширина шва після заварки не перевищувала подвійної ширини до заварки. Форма і розміри підготовлених під заварку вибірок повинні забезпечувати можливість надійного проварена в будь-якому місці. Поверхня кожної вибірки повинна мати плавні обриси без різких виступів, гострих заглиблень і задирок. При заварці дефектного ділянки необхідно перекрити прилеглі ділянки основного металу.
Після заварки ділянку треба зачистити до повного видалення раковин і пухкості в кратері, виконати на ньому плавні переходи до основного металу.
У зварних швах з наскрізними тріщинами перед заваркою потрібно засвердлити їх кінці, щоб запобігти поширенню тріщин. Дефектний ділянку в цьому випадку проварюють на повну глибину.
Заварку дефектного ділянки проводять одним із способів зварювання плавленням (ручного дугового, дугового інертними газами і т.д.).