Шви в конструкціях із зварними з'єднаннями повинні постійно піддаватися контролю. І це не залежить від того, коли з'єднання було зроблено. Для цього використовуються різні методи. один з яких - ультразвукова дефектоскопія (УЗД). Вона по точності проведених досліджень перевершує і рентгеноскопію. і радіо-дефектоскопію. і гамма-дефектоскопію.
Необхідно відзначити, що ця методика не нова. Її використовують з тридцятих років минулого століття, і сьогодні ультразвуковий контроль зварних з'єднань популярний, тому що з його допомогою можна виявити дрібні дефекти всередині зварювального шва. І, як показує практика, саме приховані дефекти є основними серйозними причинами ненадійності свариваемой конструкції.
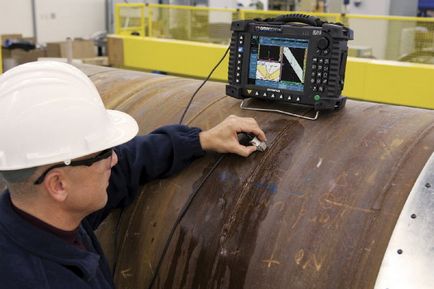
теорія технології
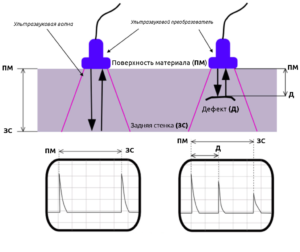
В основі ультразвукових коливання лежать звичайні акустичні хвилі, які мають частоту коливання вище 20 кГц. Людина їх не чує. Проникаючи всередину металу, хвилі потрапляють між його частинками, які знаходяться в рівновазі, тобто, коливаються в одній фазі. Відстань між ними дорівнює довжині ультразвукової хвилі. Цей показник залежить від швидкості проходження через металевий шов і частоти самих коливань. Залежність визначається за формулою:
- L - це довжина хвилі;
- с - швидкість її переміщення;
- f - частота коливань.
Швидкість же залежить від щільності матеріалу. Наприклад, в поздовжньому напрямку ультразвукові хвилі рухаються швидше, ніж в поперечному. Тобто, якщо на шляху хвилі трапляються порожнечі (інше середовище), то змінюється і її швидкість. При цьому, зустрічаючи на своєму шляху різні дефекти. відбувається відображення хвиль від стінок раковин, тріщин і пустот. А відповідно і відхилення від спрямованого потоку. Зміна руху оператор бачить на моніторі УЗК приладу, і за певними характеристиками визначає, який дефект встав на шляху руху акустичних хвиль.
Наприклад, звертається увага на амплітуду відбитої хвилі, тим самим визначається розмір дефекту в зварювальному шві. Або за часом поширення ультразвукової хвилі в металі, що визначає відстань до дефекту.
Види ультразвукового контролю
В даний час в промисловості застосовуються кілька способів ультразвукової дефектоскопії зварних швів. Розглянемо кожен з них.
- Тіньовий метод діагностики. Це методика заснована на використанні і відразу двох перетворювачів, які встановлюються по різні боки досліджуваного об'єкта. Один з них випромінювач, другий - приймач. Місце установки - строго перпендикулярно досліджуваної площині зварного шва. Випромінювач направляє потік ультразвукових хвиль на шов, приймач їх приймає з іншого боку. Якщо в потоці хвиль утворюється глуха зона, то це говорить про те, що на його шляху трапився ділянку з іншим середовищем, тобто, виявляється дефект.
- Відлуння-імпульсний метод. Для цього використовується один УЗК дефектоскоп, який і випромінює хвилі, і приймає їх. При цьому використовується технологія відображення ультразвуку від стінок дефектних ділянок. Якщо хвилі пройшли крізь метал зварювального шва і не позначилися на приймальному пристрої, то дефектів в ньому немає. Якщо сталося відображення, значить, всередині шва присутній якась вада.
- Відлуння-дзеркальний. Даний ультразвуковий контроль зварних швів - це підтип попереднього. У ньому використовується два прилади: випромінювач і приймач. Тільки встановлюються вони по одну сторону від досліджуваного металу. Випромінювач посилає хвилі під кутом, вони потрапляють на дефекти і відображаються. Ці відбиті коливання і приймає приймач. Зазвичай, таким чином, реєструють вертикальні дефекти всередині зварювального шва - тріщини.
- Дзеркально-тіньовий. Цей ультразвуковий метод контролю - симбіоз тіньового і дзеркального. Обидва прилади встановлюються з одного боку від досліджуваного металу. Випромінювач посилає косі хвилі, вони відбиваються від стінки основного металу і приймаються приймачем. Якщо на шляху відбитих хвиль не зустрілися вади зварного шва, то вони проходять без змін. Якщо на приймачі відбилася глуха зона, то, значить, всередині шва є вада.
- Дельта-метод. В основі цього способу контролю зварних з'єднань ультразвуком лежить переизлучение дефектом спрямованих акустичних коливань всередину зварного з'єднання. По суті, відбиті хвилі діляться на дзеркальні, трансформовані в поздовжньому напрямку і перєїзлучать. Приймач може вловити не всі хвилі, в основному відображені і рухомі прямо на нього. Від кількості отриманих хвиль буде залежати величина дефекту і його форма. Не найкраща перевірка, тому що вона пов'язана з тонким налаштуванням обладнання, складність розшифровки отриманих результатів, особливо, коли перевіряється зварювальний шов шириною більше 15 мм. При проведенні ультразвукового контролю якості металу цим способом висуваються жорсткі вимоги до чистоти зварювального шва.
Ось такі методи ультразвукового контролю сьогодні використовуються для визначення якості зварних з'єднань. Необхідно відзначити, що найчастіше фахівці використовують луна-імпульсний і тіньовий метод. Решта рідше. Обидва варіант в основному використовуються в ультразвуковому контролі тру.
Як проводиться ультразвукова дефектоскопія
- Проводиться зачистка зварного шва та прилеглих до нього ділянок на ширину 50-70 мм з кожного боку.
- Щоб вийшли більш точні результати на з'єднувальний шов наноситься мастильна засіб. Наприклад, це може бути солідол, гліцерин або будь-який інший технічний масло.
- Проводиться настройка приладу по ГОСТ.
- Випромінювач встановлюється з одного боку і включається.
- З протилежного боку шукачем (приймачем) виробляються зиґзаґоподібні переміщення уздовж зварного стику. При цьому прилад трохи повертають туди-сюди навколо своєї осі на 10-15 °.
- Як тільки на моніторі з'явиться сигнал з максимальною амплітудою, то це ймовірність, що в металі шва виявлено дефект. Але необхідно упевниться, що відображає сигнал не став причиною нерівності шва.
- Якщо не підтвердилося, то записуються координати вади.
- Згідно ГОСТ випробування проводиться за два або три проходи.
- Всі результати записуються в спеціальний журнал.
Увага! Контроль якості зварних кутових з'єднань (таврових) проводиться тільки луна-імпульсним способом, тіньовий метод тут не підійде.
Параметри оцінки результатів
Чутливість приладу - основний фактор якості проведених робіт. Як з його допомогою можна розпізнати параметри дефекту.
По-перше, визначається кількість вад. Навіть при найближчих один до одного відстанях луна-метод може визначити: один дефект в зварювальному шві або два (декілька). Їх оцінка проводиться за наступними критеріями:
- амплітуда акустичної хвилі;
- її протяжність (умовна);
- розміри дефекту і його форма.
Протяжність хвилі і ширину вади можна визначити шляхом переміщення випромінювача уздовж зварювального з'єднання. Висоту тріщини або раковини можна дізнатися, виходячи з різниці часових інтервалів між відбитою хвилею і випромінювань раніше. Форма ж дефекту визначається спеціальною методикою. В основі її лежить форма відбитого сигналу, що з'являється на моніторі.
Метод ультразвукової дефектоскопії складний, тому якість отриманих результатів залежить від кваліфікації оператора і відповідності отриманих показників, які регламентує ГОСТ.
Переваги і недоліки ультразвукового контролю труб
До переваг методу для контролю зварних швів можна віднести наступні критерії.
- Обстеження проходить швидко.
- Діагностичний результат високий.
- Метод контролю зварних швів за допомогою ультразвуку - найдешевший варіант.
- Він же і найбезпечніший для людини.
- Пристрій для контролю якості шва - портативний прилад, тому мобільність технології забезпечується.
- Ультразвукова діагностика проводиться без пошкодження досліджуваної деталі.
- Немає необхідності зупиняти обладнання або об'єкт для того, щоб провести контроль зварювання.
- Можна перевіряти стики нержавіючих металів, чорних і кольорових.
Недоліки теж є.
- Контроль зварних з'єднань трубопроводів або інших конструкцій не дає точності за формою знайденого дефекту. Вся справа в тому, що в тріщинах або раковинах зварного шва можуть бути присутніми повітря (газ) або шлак. У двох матеріалів щільність різна, а значить, і різна відбивна здатність.
- Складно визначити дефекти в деталях зі складною конфігурацією. Відправлені хвилі можуть відбитися на іншій ділянці шва, а не на досліджуваному, за рахунок кривизни. А це видасть некоректну інформацію.
- Складно провести ультразвуковий контроль труб, якщо метал, з якого вони виготовлені, має грубозернисту структуру. Усередині матеріалу відбуватиметься розсіювання спрямованого потоку і загасання відбитих хвиль.
- Важливо відповідально підійти до очищення зварного шва. Його хвилястість або забруднення, іржа або окалини, краплі розбризканого металу або повітряні сідла і пори на поверхні створять перешкоду до отримання правильних показників, відповідних ГОСТ.
Проконтрольований шов - це гарантія, що зварена конструкція знаходиться під наглядом. Дослідження підтверджують його якісно стан. Тобто, воно низьке або достатня, щоб об'єкт був прийнятий в експлуатацію або продовжував експлуатуватися. Тому існують певні нормативи, які застосовуються для тимчасового періоду проведення перевірок. Їх необхідно строго дотримуватися.
Поділися з друзями