На кресленні всі розміри проставляти не треба, останній виявляється сам собою. Але при конструюванні його потрібно знати, а при складанні враховувати. Для цього і розраховують розмірні ланцюги.
Розмірні ланцюги дозволяють розраховувати розміри, які в процесі виготовлення або складанні не виділяються, а виходять самі собою. Такі розміри називають останньою ланкою, тому що вони виходять останніми. Їх позначають великими літерами українського алфавіту з індексом # 8710 ;. Або вихідним ланкою, тому що технолог визначає його заздалегідь. За новим ГОСТу А # 8710; замінений на A # 931; .
Розміри входять до розмірного ланцюг називають состовляющие і позначається великими російського алфавіту А, Б, В з вказівку порядкового номера.
Складові розміри діляться на 2 типу: Збільшують вихідне ланка - це розміри при збільшенні яких вихідна ланка збільшується; зменшує вихідне ланка - це розміри при збільшення яких вихідна ланка зменшується.
Розмірна ланцюг завжди повинна бути замкнута.
Для класифікації розмірів разбіраютс з одним, розміром найближчим до вихідного ланці а решта призначаються методом обходу по контуру.
А # 8710; = - (+) - дивись приклад.
А # 8710; = - - в загальному випадку (1)
де n - число число збільшують розмірів входять до розмірного ланцюг, а m - число зменшують розмірів входять розмірну ланцюг
ESA # 8710; = - (2)
EIA # 8710; = - (3)
TA = +
TA # 8710; = (4)
За відомими значеннями розмірів складових ланок призначити точність на замикаючу ланка.
А1 = 20 +0,2; А # 8710; = - (+) = 60 - (30 + 20) = 10 мм.
А2 = 30 ± 0,15; ESA # 8710; = ES - (EI + EI) = - 01 - (0-0,15) = 0,05 (мм.)
=; EIA # 8710; = -0,4 - (0,2 + 0,15) = - 0,75 мм.
А '# 8710; -. TA # 8710; = ESA # 8710; - EIA # 8710; = 0,8 мм.
По заданому значенню вихідного ланки призначити точність на складові ланки.
1) спосіб рівних допусків (примітивний спосіб).
TAi =; недолік способу - однакові допуски на різні номінальні розміри дають різну точність (квалітет від 1до 14).
2) Спосіб пробних розрахунків. Допуски призначаються з технологічних можливостей апаратури та кваліфікації робітників. А потім коригуються з урахуванням допуску вихідного ланки.
Недолік: суб'єктивність оцінки та прив'язка до конкретного виробництва.
3) Спосіб рівній точності (рівних квалітетів)
Квалитет = const, a = const, T = a # 8729; i (мкм), де i = 0,45 # 8729; + 0,001 # 8729; d, тоді TA # 8710; = # 931; ai # 8729; ii = a # 8729; # 931; ii; і вибираємо квалітет a =.
Приклад побудови розмірних ланцюгів.
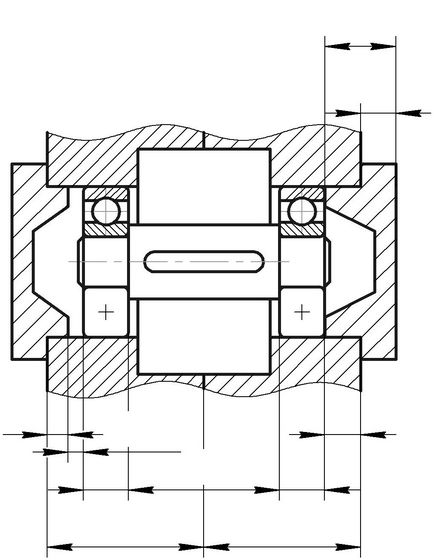
Типи зубчастих коліс.
За призначенням колеса бувають:
Відлікові. головна вимога кінематична точність кута повороту веденого колеса (Вартові механізми, інструменти) - вузькі колеса.
Швидкісні колеса. для яких головне плавність входу взуб'ев в зачеплення.
Силові колеса. основні вимоги - хороший контакт зуб, в основному черв'ячні і широкі колеса.
Колеса загального призначення - колеса в яких основний показник невозможновибрать. Всі вимоги однаково неважливі, точність всюди невелика.
Всі колеса обов'язково мають бічний зазор між неробочими поверхнями зуб. Не буває беззазорний зубчастих передач. Бічний зазор необхідний для розміщення мастила, компенсації забруднення і теплового разширения.
Позначення зубчастих коліс на кресленні.
Точость зубчастих коліс задається по 12 ступенями точності:
1 - 5 використовують в годинникових механізмах і інструментах
6 - 9 в машинобудуванні
10 - 12 для сільськогосподарської техніки.
На кресленнях вказують точність по чотирьом нормам
Ст. т. по нормі кінематичної точності
Ст. т. по нормі плавності входу зуба в зачеплення
Ст. т. по нормі контакту зуб
Вид сполучення по боковій поверхні.
Бічний зазор призначають в залежності від типу переду A, B для откритх; С, D для скоростнх; C, D, E, H для закритих; E для тихохідних; H для ручних.
Приклад позначення зубчастих коліс.
9 - 9 - 9 - В або 9 - В; загального призначення.
8 - 8 - 8 - З або 8 - С; конічні колеса.
7 - 9 - 9 - H - відліковий колесо, ручна передача.
8 - 7 - 9 - D - швидкісні вузькі колеса в закритій передачі.
8 - 7 - 7 - C - швидкісна, силова, закрита передача, широкі колеса.
9 - 9 - 7 - E - силова, тохоходная передача, черв'ячні колесо.
Показники норм точності.
Точність реальної зубчастої передачі визначається за показниками. По кожній нормі точності ГОСТ дозволяє до 12 показників. Показники бувають комплексними і приватними. Комплексні показники використовуються в серійному виробництві і фіксують величину не точності. Приватні показники відповідають за причини не точності і їх кількість відповідає кількості причин. Показники по нормам кінематичної точності наведені на малюнках 1, 2, 3, 4, 5, 6 роздаткового матеріалу 8
Графік кінематичної похибки розкладається на гармоніки визначають частоти. Графік виходить на гармонійному синхрофазотрон. Представлені похибки: радіальне биття, овальність, зубцевая частота. Остання на малюнку 7 роздаткового матеріалу 8 є комплексним показником норми плавності входу зуб в зачеплення.
Приватні показники: похибка кроку по лінії зачеплення, похибка кроку по ділильної окружності, похибка форми зуб. Наведено на малюнку 8 і 9 роздаткового матеріалу 8 і 9.
Комплексним показником за нормою контакту є пляма контакту, отримане шляхом зачеплення реального колеса з ідеальним. Малюнок 10 роздаткового матеріалу 9
Приватним показником є допуск на напрямок зуба. Малюнок 11 роздаткового матеріалу 9
Показники за формою бічного зазору.
Дійсний бічний зазор передачі визначається за величиною мертвого ходу або методом свинцевою зволікання (jn)
Вид сполучення по бокових поверхнях позначається великими літерами АBCDEH, він складається з ососновного відхилення, яке позначається так само великими літерами і величини допуску, який позначається малими літерами: a, b, c, d, h (Малюнок 13 роздаткового матеріалу 9).
При збігу осьового відхилення і величини допуску пишеться тільки одна буква - с. При розбіжності дві, Ab
ГОСТ дозволяє призначати нестандартні величини і допуски
наприклад 7 - 8 - 9 - 200У; де мінімальний гарантований бічний зазор jnmin = 200 мкм .; y - величина допуску.
Приватні показники бокового зазору - це найменша додаткове зміщення вихідного контуру зуборізних інструментів. (EHs), яке забезпечує мінімальний гарантований бічний зазор і допуск на зміщення вихідного контуру зуборізних інструментів TH. який забезпечує максимальний бічний зазор.
Таким чином, товщина зуба, що впливає на бічній зазор між зуб залежить від робочого смещающего інструменту.
Робочі допуски на зубчасті колеса.
ГОСТ вимагає, що б все табличні допуски для всіх показників за всіма нормами точності були витримані на робочої осі зачеплення, тобто враховували точність складання, точність посадкового валу під колесо і точність нарізування зуба. В результаті робочий допуск на нарізування зуба може бути зменшений в порівнянні з табличним вдвічі.
Робочі допуски по нормі бічного зазору.
Якщо базою для базою для установки інструменту при нарізування зуба обраний зовнішній діаметр заготовки, то база повинна бути в 4 рази точніше витримується розміру і допуск на зміщення інструменту слід даліть на три частини. Допуск на радіус заготовки дорівнює ¼TH тоді
Tdзаготовкі = 0,5 # 8729; TH
Так само слід контролювати форму заготовки.
Tрадіальное биття = 0,25 # 8729; TH;
Таким чином на нарізування зуба залишилося 50% від ТН (рисунок 15 роздаткового матеріалу 9)
У серійному виробництві можна зробити пристосування і установку фрези вести щодо пристосування. Тоді базою буде вісь отвору в заготівлі, а допуск ТН можна цілком віддати на нарізування зуба.
Робочі допуски за кінематичною нормі точності.
Допуск на радіальне биття зубчастого вінця Fr завжди доводиться ділити на 2 частини, тому що радіальне биття вінця залежить від форми і розташування посадкового валу. Контроль необхідно здійснювати щодо робочої осі зачеплення. Робоча вісь - це вісь, що проходить через центри посадочних поверхонь під підшипники.
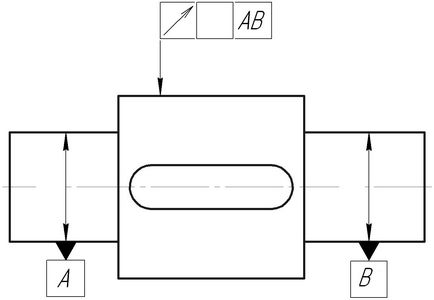
Робочі допуски по нормі контакту зубів.
Якщо колесо широке, відношення довжини маточини до діаметру отвору більше 0,8, то його установка на вал не залежить від торцевих поверхонь, і весь допуск по нормі контуру зуб цілком віддається на нарізування зуб.
Якщо колесо вузьке, відношення довжини маточини до діаметру отвору менше 0,8, то при складанні слід призначити точність на установчі торці вала і колеса. В цьому випадку допуск на напрямок слід розділити на 3 частини:
0,25FB - на контроль торцевого биття, вала. 0,25FB - на торцеве биття зубчастого колеса з урахуванням діаметра установочного торця і ширини вінця. 0,5FB - безпосередньо на нарізування зуба (рисунок 15 роздаткового матеріалу 9)
Допуски по нормі плавності.
Ці допуски не залежить від монтажу і збірки. Допуск на крок зуба і допуск на форму зуба цілком віддається на нарізування зуба.
Креслення зубчастого колеса.
На кресленні зовнішній діаметрзаготовкі виконаний по 14 квалітету, а контроль радіального биття призначають із розрахунку 0,1 модуля так як припускаємо серійне виробництво і весь допуск на зміщення вихідного контуру цілком оідадім на нарізування зуба. Значення всіх допуском по всім нормам наведено в стандартній таблиці в правому куті креслення. На лівому торці колеса для забезпечення норми контакту призначений контроль торцевого биття з розрахунку 0,25FB · dзагатовкі / B, де dзагатовкі = 166 мм; ширина вінця B = 20 мм.
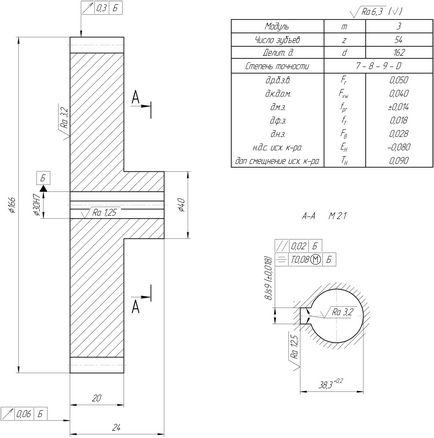
Загальні допуски по ГОСТ 30893.2 - mK
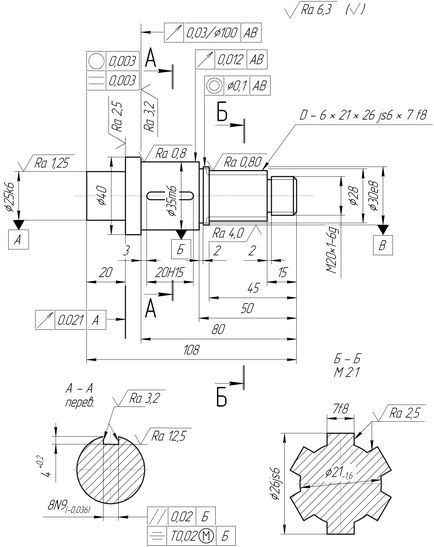
Незазначені граничні відхилення розмірів: H14, h14, ±
Це інструмент для контролю придатності деталі без шкали, за принципом «так - ні». Калібр - це спеціальне вимірювальне засіб, неуневерсальное. Калібри бувають нормальні і граничні. Нормальні представляють собою копію приєднується деталі. Виготовлення за нормальними калібрами полягає в підгонці деталей під калібр. Недоліком способу є суб'єктивність оцінки і те, що калібри використовуються тільки для посадок з зазором. Переваги методу в тому, що можна взяти калібр в поле для підгонки часто ламаються деталей. Граничні калібри виготовляються за граничними розмірами деталі і мають дві сторони: прохідну і непрохідну. Калібри для контролю отвори називаються пробка. Калібри для контролю валів - скоба.
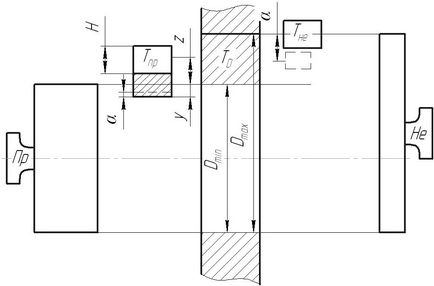
Калібри використовуються для контролю деталі в масовому і серійному виробництві. Їх ізготавлівиают для розмірів ряду Ra 5, для квалитетов з 5 - 18, для полів допусків з основного відбору переважно в системі отвору. Калібри дорогі, вироби їх роблять з зносостійких матеріалів. Прохідна сторона зазвичай буває з покриттям. Калібри виготовляють по 4 квалитету. Для збільшення довговічності калібрів поле допуску прохідній частині калібру зміщують в сторону допуску деталі на величину z і встановлюють кордон зносу y. Для розмірів більше 180 мм. допуск непрохідний боку і кордон зносу зміщується в бік допуску деталі на величину # 945; для компенсації перекосу. Нові калібри видаються робочим. Частково зношені начальникам цеху. Зношені - замовнику. Для зменшення ваги, калібри пробка роблять з усіченого профілю.
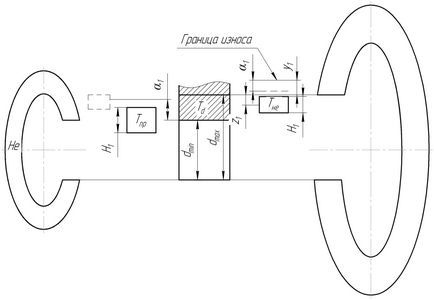
Скоби виконують двухстронній або односторонніми комбінованими.