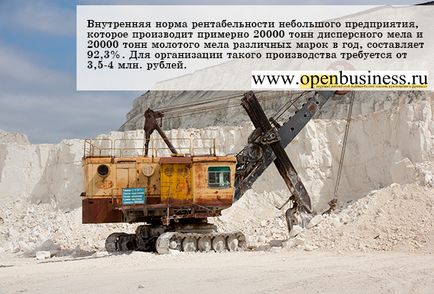
Практично всі види композиційних матеріалів, які застосовуються в різних сферах, мають в своєму складі різні наповнювачі. Останні відрізняються за хімічним складом і за походженням (природні і штучні). У композиційні матеріали вони додаються, в першу чергу, для здешевлення вартості останніх і / або надання їм певних властивостей. Наповнювачі можуть надавати армирующий, бронюють або абразивний ефект, розбавляти або, навпаки, згущувати суміш, стабілізувати і зміцнювати матеріал. Однак, незалежно від походження наповнювачів, вони завжди використовуються у вигляді тонкодисперсних порошків.
Найбільшою популярністю користуються природні і органічні наповнювачі (крейда, вапняк, тальк, барит, каолін, азбести та ін.). А одним з найпоширеніших видів серед них є тонкодисперсний крейда (карбонат кальцію).
Цей наповнювач використовується при виробництві сухих будівельних сумішей, штукатурок, затерли, пластмас, лакофарбовим матеріалів, гуми, паперу, кабелів і т. Д. Основними постачальниками крейди для гумової, кабельної, полімерної, лакофарбової та інших галузей промисловості є підприємства з його виробництва, розташовані в Білгородській і Воронезькій областях.
Попит на крейдяні наповнювачі зростає з кожним роком. Тим часом його виробництво, навпаки, не тільки не зростає, а й навпаки, в деякі періоди знижується, що пов'язано з різними проблемами, загальмовує розвиток галузі. Велике значення має місце розташування постачальників дисперсної крейди, адже чим вони далі, тим більше будуть витрати на транспортування і тим вище буде собівартість продукції. Втім, для покупців із Західної Європи питання з місцем розташування постачальника має не таке велике значення. Європейський ринок збуту перевищує в наші дні 5 млн. Тонн на рік. Найдорожчими є крейдяні порошки, які відрізняються високою дисперсністю і білизною. Не менш дорогі поверхнево-модифіковані (наприклад, гідрофобні) порошки.
Мел проводиться двома основними способами: шляхом подрібнення порід і осадових відкладень (природний або натуральний карбонат кальцію) і хімічним осадженням (хімічно обкладена карбонат кальцію). Тонкодисперсний крейда може мати різну форму частинок, яка залежить від форми його кристала і способу подрібнення. Для подрібнення також використовуються два способи - сухий і мокрий. При мокрому розуміли отримують гладкі і круглі частинки, що при використанні призводить до меншого зносу обладнання. А для отримання тонкосперсного крейди сировину піддається микронизации (з використанням механічного струменевого і ультразвукового подрібнення). У нашій країні, в Білорусії і в Україні найчастіше використовується напівсухий спосіб із застосуванням трехступенчатого циклонного теплообмінника. Вперше він був використаний на польському заводі Chelm і відрізняється від інших методів відсутністю шламоізготовленія крейди.
Мел добувають в кар'єрі за допомогою ковшових екскаваторів у вигляді великих шматків. Сировина на поїздах доставляється в цех сировинної підготовки. Після розвантаження крейда направляється на дві дробарки, де подрібнюється до розмірів близько 50 мм і направляється на зберігання на склад. У міру необхідності подрібнений крейда завантажується в дозуючі бокси, звідки потім подається в сушарку-дробарку разом з коригуючими добавками.
Такий порядок роботи вважається одним з найефективніших, але у нього є і свої недоліки. Шматки крейди, здобуті з кар'єру, повинні бути дуже великими. Мел в невеликих шматках під відкритим небом швидко намокає і стає липким, що ускладнює його складування. З іншого боку, так як технологія передбачає використання крупнокускового крейди, це обмеження не дозволяє використовувати безперервні форми транспортування (конвеєри). А якщо кар'єр розташований поруч з грунтовими водами, то використовувати залізничний або автомобільний транспорт буде проблематично. Це вимагає розширення штату працівників і збільшує собівартість сировини.
У зимові місяці кар'єрні роботи сильно ускладнюються, так як заморожені шматки крейди НЕ висушуються повністю. Вологість крейди залежить від погодних умов і складає від 21 до 28%. При такому методі роботи можливості для контролю вологості сировини сильно обмежені.
Розглянемо більш докладно один з найпопулярніших способів отримання тонкодисперсної крейди. Він включає в себе грубе дроблення вихідної сировини, магнітне сепарування, мокре размучіваніе, тонке подрібнення в струменевих дезинтеграторах, збір суспензії з введенням диспергатора, збагачення в гидроциклонах з проміжним збором суспензії, вторинне тонке подрібнення в струменевих дезинтеграторах, збір суспензії, контрольний відсів, распилітельную сушку , при якій в якості диспергатора використовується триполіфосфат натрію або суміш триполифосфата натрію з вуглекислим натрієм, який вводиться на стадії мокрого размучіванія з п оследующім видаленням часток з розміром більше п'яти міліметра домішок на віброгуркоті і віброситі. Після вторинного подрібнення і збору суспензії здійснюється відмивання суспензії водою.
Цей спосіб, як видно вже з одного перерахування етапів, є складним і включає в себе велику кількість різних операцій. Найгірше, що готовий продукт, отриманий таким чином, має не таку високу якість і чистоту.
Багато виробників розробляють власні способи отримання тонкодисперсної крейди, які дозволяють поліпшити чистоту і якість продукції, а також вирішити проблему з утилізацією відходів при виробництві. Наприклад, мокре размучіваніе, збір суспензії, тонке подрібнення і сушка, грубе дроблення вихідної сировини - все це проводиться під впливом статичної навантаження з подальшим грохоченням в кілька стадій. При цьому виділяють крупно, середньо і мелкокусковие фракції, а що залишилися відходи размучівают і перемішують за допомогою вібромешалкі в три стадії в спеціальних ємностях.
Цей спосіб теж досить складний, тому що припускає чергування процесів вібраційного впливу, відстою і зливу суспензії і т. Д. Відстій суспензії відправляється на прес-фільтрацію, його кристалічна частина змішується з речовиною, в якості якого використовується пил з електрофільтрів цементного виробництва, і направляється потім на гранулювання.
При виборі місця розташування заводу необхідно враховувати близькість і доступність таких ресурсів, як електроенергія, газ, залізничний транспорт, розташування постачальників вихідної сировини і його якісні характеристики.
На свою номінальну потужність таке підприємство зможе вийти вже через 4-6 місяців після початку роботи. Для роботи на заводі знадобиться близько 30-35 чоловік в штаті, включаючи директора, головного бухгалтера, головного інженера, маркетолога / начальника відділу збуту, майстрів, контролера ВТК, завідувача складом, лаборантів, слюсарів, операторів обладнання, сторожів, водіїв, слюсарів-наладчиків .
Для виробництва крейди потрібне спеціальне технологічне обладнання. Мінімальний набір включає в себе сушильний барабан продуктивністю близько 10 тонн на годину, ролико-маятникову млин такий де продуктивності, систему пневмотранспорту і пилеосажденія. Все це обійдеться в 1,5-2 млн. Рублів. Для розміщення цього обладнання, організації складів і побутових приміщень знадобиться площа в 1000 кв. метрів. Для підприємства з більшою проектною потужністю (близько 100 тисяч тонн продукції на рік) буде потрібно, відповідно, і більший капітал.
Завод з переробки крейди підрозділяється на кілька ділянок. Точна їхня найменування та розподіл залежить від використовуваного методу переробки. Наприклад, при сухому способі подрібнення крейди ці ділянки будуть такими: ділянку сушки крейди, установки для подрібнення і сепарування крейди, вторинне сепарування крейди, ділянку гідрофобізації (обробка поверхні) крейди, силосний і пакувальний ділянки, ділянка подрібнення негашеного вапна, управління цеху. На ділянці сушіння крейди сировину дробиться до фракції менше 20 мм, просівається і просушується до вологості менше 8% (сушка здійснюється на іншій дільниці), після чого воно за допомогою пневмотранспорту подається на ділянку сушки крейди.
Мел сушать на сушарці з киплячим шаром, доводячи його до вологості менше 0,3%. Пил з фільтра може або знову надходити в сушарку, або ж передаватися на установку вторинного сепарування. Установки для подрібнення і сепарування крейди включають в себе вихревую млин і турбосепаратор з декількома колесами. На ділянці сепарації дисперсність крейди доходить до 8 мкм.
На ділянці вторинного сепарування крейда вже не подрібнюється, а піддається процедурі сепарації. На ділянці гідрофобізації сировину обробляється стеаринової кислотою. При цьому сам крейда подається в накопичувальний силос, а обробка здійснюється за допомогою вихровий млини і шляхом додаткового нагрівання. Порошок стеаринової кислоти змішується з наповнювачем, і при випаровуванні поверхню крейди піддається рівномірної обробці. Силоси використовуються для упаковки продукції в клапанні мішки і біг-беги.
Ця схема розподілу ділянок на виробництві дрібнодисперсного крейди може змінюватися, в залежності від асортименту продукції, що виробляється і використовуваної технології.