Демонтаж, розбирання та дефектация
Залежно від виробничих можливостей підприємства і конструктивних особливостей двигуна ремонт його може здійснюватися на судні або в цеху. Як правило, при капітальному ремонті двигун демонтують (знімають з суднового фундаменту) і доставляють в цех для ремонту. Великогабаритні дизелі великої маси з фундаменту не знімають, а демонтують окремими вузлами.
Ремонт двигуна в цеху скорочує терміни ремонту, однак подальші роботи на судні по монтажу і центрування двигуна можуть бути вельми трудомісткими, тому необхідність демонтажу в кожному окремому випадку повинна бути обґрунтована.
При капітальному ремонті двигуна в цеху основними етапами є: розбирання; дефектация (виявлення зносів і пошкоджень); відновлення деталей; виготовлення нових деталей замість забракованих; вузлова зборка; загальне складання двигуна; випробування в цеху; монтаж на судновому фундаменті; випробування на судні.
Демонтажні роботи починають з від'єднання від двигуна всіх трубопроводів, попередньо видаливши з них і з двигуна воду, масло і паливо; потім знімають з двигуна контрольно-вимірювальні прилади, арматуру; всі отвори закривають заглушками. Одночасно ведуть роботи з розбирання майданчиків, приводів до арматури та інших частин, що з'єднують двигун з конструкціями корпусу судна. Потім роз'єднують фланці колінчастого і приводного валів, від'єднують двигун від суднового фундаменту, вивантажують і транспортують в цех, де встановлюють в горизонтальному положенні на спеціальний фундамент або металеві балки.
Розбирання двигуна - один з найважливіших технологічних процесів ремонту, багато в чому визначає його тривалість і вартість. Недбала розбирання нерідко призводить до пошкодження, а іноді і до втрати деталей.
Процес розбирання двигуна на судні і в цеху по суті однаковий, проте розбирання в цеху зручніше і значно продуктивніше, так як виконується в більш сприятливих умовах. Послідовність розбирання двигуна залежить від його конструкції; в кожному окремому випадку розбирання повинна проводитися відповідно до інструкції заводу-виготовлювача.
Належна увага при розбиранні дизелів необхідно приділяти таврування і маркування деталей та місць їх установки відповідно до інструкції, щоб при подальшій збірці встановити деталі правильно. На спеціалізованих підприємствах, які ремонтують швидкохідні дизелі одного типу, деталі при розбиранні не маркується.
Послідовність розбирання двигунів, що мають в якості основної деталі остова фундаментну раму, приблизно така: спочатку знімають контрольно-вимірювальні прилади, потім електрообладнання, трубопроводи, тяги паливних насосів і регулятора частоти обертання, видаляють стійки з клапанними важелями, штовхачі і штанги клапанів, навісні агрегати, кожух шестерень, розподільний вал, кришки циліндрів, виробляють роз'єм нижніх головок шатунів і, повертаючи колінчастий вал, послідовно піднімають поршні з шатунами, витягуючи їх з ц іліндров. Потім випрессовивают втулки циліндрів, відокремлюють циліндри (блок циліндрів), знімають маховик, розкривають Рамов підшипники, піднімають колінчастий вал і укладають його на козли. До випрессовкі втулок циліндрів зарубашечного простір очищають від накипу і піддають гідравлічному випробуванню, причому випрессовкі втулок зручніше проводити після демонтажу блоку циліндрів або окремих циліндрів. Якщо розбиранні піддають кілька однакових двигунів, то їх деталі, як правило, не знеособлюють. Ремонт швидкохідних двигунів, як уже вказувалося, виробляють на спеціалізованих підприємствах, де впроваджено технологічний досвід заводів масового або великосерійного виробництва даних двигунів. Висока точність механічної обробки, стандартизація і взаємозамінність багатьох деталей дозволяють вести ремонт по потокової схемою з знеособлення значної кількості-деталей; уникають знеособлення лише спільно оброблених деталей. На ряді підприємств розбирання двигунів передує їх зовнішня мийка в спеціальних мийних машинах.
У двигунів крейцкопфний типу спочатку від'єднують шток поршня від поперечки крейцкопфа і тільки після цього, піднявши поршень разом зі штоком, виймають з циліндра. Потім тимчасово закріплюють крейцкопф на паралелі, розбирають головні з'єднання і Мотильова підшипник шатуна (кривошип колінчастого вала знаходиться в ВМТ). Повільно обертаючи колінчастий вал, виводять шатун з станини і виймають його, знімають крейцкопф і паралелі.
Під час розбирання будь-якого двигуна рекомендується дотримуватися таких загальних правил:
- деталі та труби систем і прилади укладати на заздалегідь підготовлені місця;
- розбирання виробляти тільки спеціально призначеними для цієї мети інструментами і пристосуваннями;
- при розбиранні не застосовувати надмірних зусиль, а якщо вузол не піддається розбиранню, з'ясувати причини;
- все відкриті порожнини закривати спеціальними кришками (використання в якості заглушок клоччя і ганчір'я забороняється);
- кінці трубок глушити дерев'яними пробками або спеціальними заглушками;
- якщо деталь кріпиться декількома гайками, то спочатку послідовно послабити їх, а вже потім відкручувати; гайки після розбирання навертати назад на болти або шпильки, а якщо цього зробити не можна, то гайки з кожного вузла збирати на окрему дріт з биркою.
Наступний етап - подетальная розбирання, т. Е. Розбирання вузлів на окремі деталі.
Іноді при ремонті двигуна в цеху з метою зменшення маси двигуна і запобігання можливих пошкоджень його вузлів і деталей під час вивантаження з судна і транспортуванні в цех виробляють демонтаж окремих вузлів на судні і відправляють їх у цех. Полегшений двигун від'єднують від суднового фундаменту і також направляють в цех.
Розглянемо технологію розбирання деяких найбільш відповідальних вузлів двигуна. Випрессовкі втулок циліндрів виробляють для їх заміни, а іноді для очищення водяного простору. Втулки випрессовивают за допомогою пристосування, показаного на рис. 104. Знизу до торця втулки підводиться диск 8, що має по колу чотири отвори, в які заводять стрижні 7. Зверху на шпильки циліндра встановлюють чотири підставки 6 і два гідравлічних домкрата 5. На головки плунжеров домкратів поміщають жорсткі прокладки 4, які впираються в скобу 3 , насаджені на стрижень 7 і закріплену гайками. На дві інші підставки 6 встановлюють скобу 2, з'єднану з двома іншими стрижнями 7; під цю скобу заводять клини 1. Під час активного пристосування, в за-сорочкового простір впускають пар низького тиску для підігріву циліндра і полегшення випрессовкі втулки, злегка підбивають клини і вводять в дію домкрати, за допомогою яких і випрессовивают втулку.
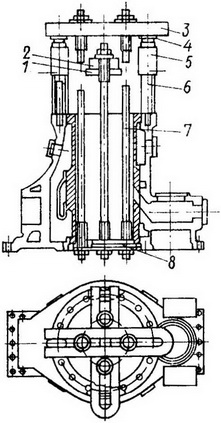
Мал. 104. Пристосування для гідравлічної випрессовкі втулок.
Послідовність розбирання поршнів залежить від їх конструкції. Розбирання більшості поршнів двигунів крейцкопфний типу зводиться до від'єднання штока поршня від його головки і зняття поршневих кілець з поршня. Від'єднання поршня тронкового двигуна проводиться шляхом випрессовкі поршневого пальця за допомогою спеціального пристосування, що дозволяє уникнути ударів по пальцю. На рис. 105 показано найпростіше пристосування для випрессовкі пальця 1 поршня 2. Через пустотіла палець поршня пропущений болт 4, під головку якого підкладена шайба 5. Другим кінцем болт проходить через отвір П-подібної скоби 3, що спирається на поверхню поршня. Навертивая гайку на болт 4, випрессовивают палець і від'єднують шатун від поршня. якщо
палець плаваючий, а поршень силуміновий, то знімають заглушки, що фіксують палець, нагрівають поршень в маслі до 250 ° С (523 К) і виймають палець з поршня. Поршневі кільця знімають за допомогою нескладних пристосувань, що оберігають їх від поломки.
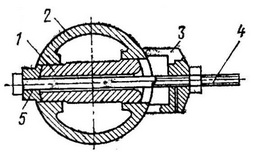
Мал. 105. Пристосування для випрессовкі поршневих пальців.
Розбирання шатуна тронкового типу зводиться до випрессовке втулки головного підшипника з попередніми висвердлюванням стопорів, а також видалення вкладишів Мотильова підшипника.
Розбираючи колінчастий вал, спресовують шестерню приводу розподільного вала і маховик, знімають заглушки, що забезпечують герметичність масляних порожнин шийок вала; при необхідності знімають противаги.
При розбиранні розподільного вала спресовують передавальний шестерню, а в разі потреби і кулачкові шайби. Якщо вал складається з декількох частин, їх роз'єднують.
Перед дефектації розібрані деталі двигуна чистять і миють для видалення нагару, корозії, жирового шару і накипу. Очищення роблять хімічним, механічним і ультразвуковим способами.
Дефектация деталей - відповідальний етап технологічного процесу ремонту ДВС. Завданням дефектації є перевірка цілісності деталей (виявлення зовнішніх і внутрішніх тріщин, уламків і т. П.) І визначення ступеня зносу, деформації, порушень взаємного розташування поверхонь і їх чистоти.
Від того, як організована дефектация, залежать якість і вартість ремонту. При недостатньо уважному контролі може знизитися його якість, а надмірно жорсткий контроль може викликати перевитрата запасних деталей. Дефектация дозволяє розділити всі деталі на три групи. До 1-ої групи відносять деталі, що мають допустимий знос, а також пройшли необхідні види перевірки; до 2-ї групи - деталі, які мають граничний знос і зміну геометричної форми поверхні, але відновлення яких можливо; до 3-й групі відносять деталі, що мають ознаки остаточного браку і непридатні до відновлення.
При дефектації деталей виробляють зовнішній огляд, перевірку на спеціальних приладах для виявлення невидимих оком дефектів, перевірку герметичності, вимірювання розмірів і перевірку для виявлення відхилень від первісної геометричної форми.
Зовнішній огляд передує всім іншим перевіркам і проводиться за допомогою лупи. Він дозволяє виявити тріщини, раковини і інші дефекти, а також зміни поверхневого шару металу (наприклад, перегрів - за наявністю кольорів мінливості). До застосування лупи виробляють візуальну перевірку, а місця, недоступні огляду, перевіряють обстукуванням для виявлення тріщин. Для виявлення в деталях вад, невидимих простим оком, на підприємствах застосовують магнітну дефектоскопію, просвічування рентгенівськими променями, гамма-дефектоскопію, ультразвукової та люмінесцентний контроль.
При дефектації деталей ДВС (виключаючи деталі паливної апаратури) необхідні наступні контрольно-вимірювальні інструменти, прилади та пристрої: мікрометричні скоби з межами вимірювань 0-75 мм, 25-50 мм і більше в залежності від розмірів поршневих пальців, шийок колінчастого вала і поршнів; індикаторний Нутрометри зі вставками різної довжини; мікрометричний Нутрометри; індикатор лінійний зі штативом; щупи; штангенциркулі; рівень слюсарний з ціною поділок 0,05-0,20 мм на 1 м довжини; резьбомери; перевірочна лінійка сталева; пристосування для вимірювання розбіжності щік кривошипа; вантажі і тонка сталевий дріт для схилів; металеві рулетки і метр.
На спеціалізованих підприємствах поряд зі звичайним інструментом широко застосовують бракувальні калібри і спеціальні вимірювальні прилади. Контроль за допомогою калібрів високопроізводітелен. Калібри бувають необхідні при перевірці розмірів важкодоступних поверхонь. Для визначення розмірів деталей прецизійних пар паливної апаратури впроваджується пневматичний метод вимірювань. Пневматичні прилади відрізняються високою продуктивністю і більшою точністю, ніж індикаторні.
Вимірюючи деталі, користуються певною методикою, яка враховує конструктивні особливості та умови роботи кожної деталі. Діаметр циліндричних поверхонь тертя перевіряють в декількох поясах, визначаючи відхилення від циліндричної форми по довжині (конусність, бочкообразность, корсетні). Діаметр перевіряють в декількох взаємно-перпендикулярних площинах, визначаючи відхилення від циліндричної форми з поперечним перерізом (овальність). Записавши дані вимірювань в карту вимірів і обробивши їх, роблять висновок про те, до якої групи за ступенем дефектності слід віднести дану деталь двигуна.