Всім привіт!
Давайтека сьогодні поговоримо про такому Холіварние питанні, як притирання клапанів. Процедура на просторах Драйв 2, м'яко кажучи, популярна - я ще не бачив жодного опису капільного ремонту ДВС, в якому не згадувався б цей "ритуал"! Причому поговоримо ми скоріше навіть не про сам притирання, а про ті речі, які викликають його необхідність.
Для початку давайте подивимося, як влаштований вузол клапан-сідло в геометричному плані:
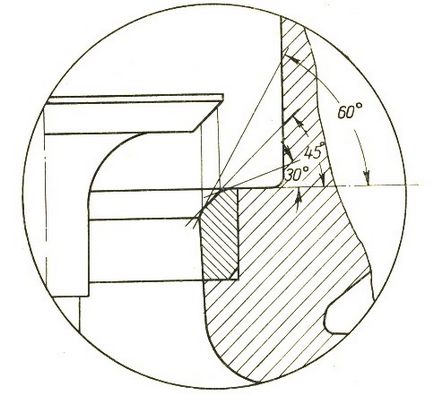
Бачимо купу фасок (причому на сідлі може бути не фаска, а радіус). Про геометрію сідла і вплив її на роботу ДВС багато і виключно дохідливо писав Barik-CZ. я ж хочу звернути увагу на кілька ключових для ресурсу ГБЦ моментів:
1. Клапан підтягується до сідла за допомогою поворотної пружини.
2. Ставлення сили притиску клапана до площі фаски на сідлі дає питомий тиск клапана на сідло.
3. Через фаску на сідлі відбувається охолодження клапана.
Як бачимо, всі ключові для роботи ГБЦ моменти впираються в дві фаски - на тарілці клапана і на сідлі.
Що буде, якщо фаска на сідлі виявиться нерівномірним? Питомий тиск в різних точках сідла буде різним, в зоні з максимальним тиском знос буде істотно швидше, ніж в сусідніх. Як наслідок порушення герметичності, прорив гарячих газів з одночасним різким зростанням температури клапана в зоні прориву газів і практично нульового охолодження в ній же. Як підсумок - прогорание клапана.
Що буде якщо фаска на сідлі занадто широка? Поімеем зниження питомої тиску, як наслідок - меншу надійність ущільнення і ймовірність прориву газів в один прекрасний момент, з усіма наслідками, що випливають.
Очевидно, що клапан закриється герметично тільки за умови, що фаски клапана і сідла будуть абсолютно соосни. Між клапаном та направляючої втулкою є радіальний зазор, зазвичай в районі 0.03-0.04мм.
Разом сумарно у нас є половина від цього зазору - 0.02мм похибки несоосности для сідла клапана й тарілки. Це ми вважаємо, що осі сідла і направляючої втулки паралельні, дуже важливе допущення, запам'ятайте його!
Для нових клапанів, або клапанів перешліфувати на спецоборудовании характерна несоосность фаски і стрижня клапана не більше 0.01мм, приймемо це як аксіому. Виходить, що у нас залишилося не більше, ніж 0.01мм на несоосность сідла клапана щодо осі направляючої втулки.
Тут треба зробити таку ремарку: при заміні направляек несоосность сідла і осі втулки може легко досягати декількох десятих міліметра - це на порядки більше нашого допуску в 0.01мм! З цього робимо висновок, що сідла правити після заміни направляек потрібно обов'язково.
І ось тепер у нас дилема - а як обробляти сідла? Досвідчений читач напевно підкаже - дик спеціальними ручними фрезами ж, ось типу таких:
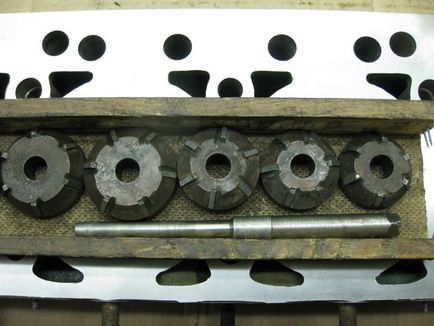
На жаль, але після обробки сідел таким інструментом найкраще місце для відремонтованої ГБЦ - в смітнику ...
І ось чому: такий інструмент центрується по направляючої втулці за допомогою так званого пілотного стрижня, або просто пілота. При діаметрі стрижня клапана в 10-11мм жорсткість пілота ще хоч якось достатня для коректного центрування інструменту, але при діаметрах стрижня клапана 7 і менш міліметрів жорсткості пілота абсолютно недостатньо. В результаті пілот банально гнеться, що не дозволяє говорити про точне центрування інструмента. Реальна похибка співвісності осей сідла клапана і втулки, яку можна отримати за допомогою такого пристосування - 0.08-0.1мм, в 10 разів більше допустимої! Додаємо до цього вкрай низьку чистоту обробки поверхні - знову ж через низьку жорсткості інструмент "дробить".
Природно, після контрольного складання ніякої герметичності не буде. Варіант залишиться один - притирати по-старому, компенсуючи несоосность від обробки і дефекти рельєфу. Та ось невдача, при цьому ми автоматично отримуємо фаску сідла різної ширини, разом з усім комплексом проблем описаних вище.
Крім того, при притирання частки абразиву впроваджуються в матеріал сідла, яким часто опиняються пористі чавун або порошкові матеріали на основі бронзи. Отримуємо абразивний сідло, термін служби якого дуже невеликий, зі зрозумілих причин. Навіть якщо сідло тверде і не схильне до впровадження абразиву - немає ніяких гарантій, що залишки притирочное пасти не сповзуть під час "ритуалу" по стрижні клапана на напрямні втулки. Зрозуміло, що користі від абразиву там теж не багато ... Відмити абразив хоча і можна, але дуже і дуже складно, та й гарантій на повне видалення дати фізично неможливо.
І якби ж то тільки Неспіввісність сідла і втулки та абразивом справа кінчилася, але ж ні! Вигин пілота укупі з "ручним приводом" інструменту дає нам додаткову непаралельність осей втулки і сідла. А це означає, що стрижень клапана буде при кожному закриванні згинатися, щоб тарілка села на місце. Як наслідок різко зросте темп накопичення втомних напружень в тілі клапана і рано чи пізно (скоріше рано) голова у нього відвалиться і радісно розмолоти весь циліндр. Крім цього незапланована радіальне навантаження на м'яку направляючу втулку зіпсує її дуже швидко. Напевно ж багато хто чув страшилки як після капіталки клапана пообривало або направляйкі померли на мізерному пробігу? Ось це воно і було :)
Так яким же чином обробляються сідла правильно?
Варіантів не багато, цілий один - сідла прирізають на спеціальних верстатах, особливо цікаві можуть погуглити по марці Serdi. Суть процесу в тому, що ГБЦ закріплюється на жорсткому столі верстата, потім шпиндель з ріжучим інструментом центрується по пілоту. Принциповий момент в цьому місці такий, що пілот використовується для центрування ДО початку обробки і не бере участі в центруванні інструменту безпосередньо в процесі різання. Відповідно мала жорсткість пілотного стержня не впливає на похибку обробки.
Реальна точність при серійному виконанні робіт на такому обладнанні - 0.01-0.015мм, саме те що необхідно для гарантовано герметичного закривання клапана без будь-якої додатково мехобработки.
Ексклюзивністю така робота ніякий не володіє, багато контор в Росії надають подібні послуги. Будь-який зацікавився даною тематикою людина без зусиль знайде все явки і паролі за допомогою пошуку, причому практично в будь-якому регіоні країни :)
До речі про герметичність, якщо вже вся метушня у нас заради неї утворилася - а як перевіряти то результат праць?
Популярна методика - солярка або гас в камеру згоряння і чекати поки витече (або не витече). Начебто логічно і очевидно все, але нестиковочка є - ДВС збираємо, або насос для перекачування соляри?
Коректно перевіряти герметичність клапанів повітрям, загальноприйнята назва процесу - вакуум тест. До впускного або випускного каналу ГБЦ (смотря какие клапана перевіряються) через найпростіший адаптер підключається вакуумний насос з вакуумметром. Для герметичного клапана нормою вважається здатність тримати розрядження в 0.6-0.7Атм. І ніякої солярки! Цікаво, що до складу будь-якого спецверстатів для прірезанія сідел входить вакуум-тестер для контролю результатів роботи.
Друзі, любите своїх залізних коней, освоюйте сучасні (якщо такими можна назвати технологією 20 річної давності) способи ремонту. Пора вилазити з початку 20го століття, минули часи коли замурзані мотористи терли клапана червоною цеглою в поле :)