Сучасні технології і виробництво
З того часу, як людина дізналася залізо, він почав шукати способи робити його міцніше, надійніше і в той же час надавати йому потрібну форму. Губчасті залізні матеріали у холодному стані били стукалками, щоб надати металу потрібну форму і видалити з нього домішки. Потім, щоб легше було вирішувати цю задачу, здогадалися бити його в нагрітому стані. Цей спосіб назвали гарячої куванням.
Кування - один з найдавніших методів обробки металів. Знаряддями праці коваля в далекому минулому були ковадло, молот і найпростіші інструменти: борідки, зубила, гладилки і т. П. У XVI ст. з'явилися молоти, які приводилися в дію енергією рухомої води (водяний привід). Це дало можливість збільшити масу молота (падаючого бойка) в 10-15 разів - до 400 кг. Сила удару такого молота, природно, значно зросла.
З появою парових машин відкрилися нові можливості для збільшення сили удару молота. Майже одночасно з паровозом народився паровий молот. Маса його бойка (іноді його називають бабою) досягала вже декількох тонн. Але і цього виявилося мало! Все збільшувалися розміри виробів (вали кораблів, стволи гармат) вимагали потужніших молотів.
З'явилися преси, які пригнічували великі, добре нагріті сталеві злитки і цим надавали їм потрібну форму. У той же час (60-70-ті роки минулого століття) з'явилися прокатні стани (див. Ст. "Чорна металургія"). Але ковальська обробка не втратила свого значення. У наш час вона отримала новий розвиток. Куванням не тільки надають металу потрібну форму, а й одночасно покращують його якість: роблять його однорідніше і міцніше.
Мистецтво нагрівати метал
Процес кування заснований на природних пластичних властивостях металів. Однак, коли метал холодний, ці властивості проявляються вкрай слабо. Тому, для того щоб метал став пластичним, його нагрівають до температури понад 1000 ° С. Мистецтво нагрівати метал дуже складне і тонке. Коваль або штампувальник знає, що стали різних марок (або інші сплави) вимагають різних температурних режимів.
Метали - тіла кристалічні. Кожен кристал складається з певного числа симетрично розташованих і утворюють ті чи інші геометричні форми атомів. Кристал заліза - куб. Атоми в ньому розміщуються двояким чином. В одних випадках вони розташовуються в вершинах і центрі куба, утворюючи так звану об'ємно-центровану грати, в інших - ще й посередині кожної грані. Такі грати називається гранецентрированной. У другому випадку атоми розміщені тісніше, ніж в першому. А чим тісніше розташовуються атоми в кристалах, тим міцніше метал.
Залізо може перебувати в різних кристалічних станах. Воно змінюється в міру нагрівання або, навпаки, при охолодженні. Та й розмір самого куба не залишається незмінним: у одних випадках межі куба більше, в інших - менше. Ще в 1868 р російський вчений Д. К. Чернов визначив так звані критичні точки (температури) заліза, при яких відбувається перебудова його кристалів. Згодом виявилося, що такі перебудови характерні не тільки для заліза, але і для інших металів.
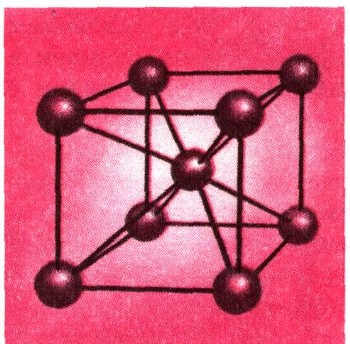
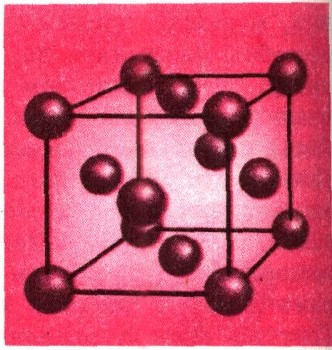
Кування покращує структуру металу. Чим тісніше розташовуються атоми в кристалах, тим міцніше метал.
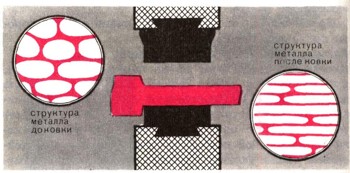
Обробка металів тиском ґрунтується на науці про пластичності. Визначну роль у розвитку цієї науки зіграли вітчизняні вчені Н. С. Курнаков, А. А. Бочвар, Я. І. Френкель, П. П. Давиденков, які своїми працями значно розширили уявлення про пластичному руйнуванні твердих тіл. Радянські вчені розробили фізико-хімічні основи пластичної обробки металів. Все це полегшує головне завдання: за допомогою кування, гарячого і холодного штампування отримувати майже готові вироби заданих розмірів.
Щоб нагрівати високоякісні стали, будують печі з декількох камер, у кожній з яких підтримують певну температуру. В першу камеру завантажують холодний метал, в ній температура 300-350 ° С. Потім, переходячи з камери в камеру, метал поступово нагрівається до 1050-1250 ° С.
Дуже великі злитки нагрівають у великих однокамерних печах. Під (пол) в цих печах висувною - на ньому злиток в'їжджає в піч і виїжджає після нагрівання. У момент завантаження температуру в печі знижують до 300 ° С, а потім її поступово підвищують.
За допомогою зарядного пристрою печей залежить швидкість і якість нагріву металу. Печі бувають полум'яні і електричні. Раніше полум'яні печі працювали на вугіллі або нафти і в кузнях було димно, чадно. Сучасні кузні працюють переважно на природному газі. Це значно поліпшило умови праці. Ще більш сприятливі умови праці при нагріванні поковок електрикою. Широко застосовуються для цього струми високої частоти (див. Ст. "Обробка струмами високої частоти").
Два способи кування металу
Існує два способи кування - вільна кування і штампування.
Вільну ковку виробляють або ударом на молотах, або тиском на пресах.
При вільному куванні ударом заготовку, яку потрібно викувати, кладуть, що не закріплюючи, на нерухому підставку - ковадло, над якою вниз і вгору ходить молот - бойок. Швидко опускаючи і піднімаючи молот, по попередньо нагрітого металу наносять удари. При цьому метал розплющується (ковалі говорять - тече). Ширина і довжина заготовки збільшується, а товщина зменшується. Після того як заготовку обожмут з одного боку, її повертають на 90 ° і знову кують. Такі операції здійснюються до тих пір, поки метал не прийме потрібної форми, - поковка готова.
Приблизно так само протікає процес вільного кування на пресах, тільки на них заготовку обробляють не вдарив, а пресуванням.
Вільним куванням на молотах і пресах можна обробляти заготовки будь-якої маси - і найменші, і дуже великі, до 200 т, наприклад поковки для турбін наших гігантських електростанцій. Проте у такий спосіб неможливо виготовити деталі точних розмірів і форм. Поковки доводиться потім обробляти на верстатах, перетворюючи багато металу в стружку. Часто буває навіть так: поковки ставлять на верстат за допомогою крана, а деталь вже без праці знімають вручну. Для перетворення поковок в деталі потрібних розмірів і форм потрібен великий парк металорізальних верстатів, величезна кількість інструментів.
Штампування під пресом. Штамп обмежує вільний перебіг металу.
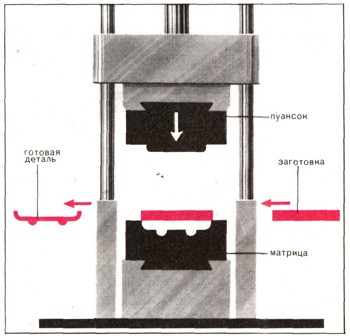
На штампувальних молотах можна обробляти величезні деталі. Тут людині на допомогу приходить механічний "коваль" - маніпулятор.
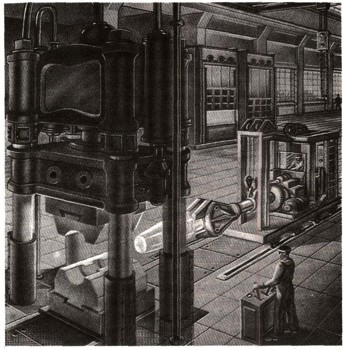
"Критичні точки" Чернова (а і b): а - нижня межа нагрівання стали при загартуванню; b - верхня межа нагрівання стали; друга
критична точка залежить від вмісту вуглецю в сталі; між х і з-температура плавлення сталі різних марок.
Зі сказаного ясно, що метод вільного кування не кращий; до нього вдаються лише тоді, коли треба виготовити одну або невелике число однакових деталей. У масовому виробництві, наприклад на автомобільних, авіаційних, вагонобудівних заводах, деталі не кують, а штампують.
Штампування по суті справи та ж кування, але тут "протягом" металу обмежена формою - штампом.
Штамп складається з двох половин. Нижня половина закріплена на ковадлі нерухомо, а верхня прикріплена до баби молота і переміщається разом з нею вгору і вниз. Метал укладають на нижній штамп. Під ударами молота він заповнює порожнину штампа, приймаючи її форму, так як "протягом" металу обмежена стінками штампа. Заготовки, отримані таким способом, називають штампуваннями .. За формою і розмірами вони значно ближче до виробу, ніж заготовки, отримані вільним куванням. А значить, при подальшій обробці в стружку йде менше-металу.
Є і ще перевага: відштампувати деталь можна набагато швидше, ніж отковать. За час, в яке звичайний молот откует одну або дві деталі, молот зі штампом зробить десятки, а то і сотні деталей.
Наскільки штампування вигідніше інших способів, можна судити з такого прикладу. Сорок з гаком років тому, коли в Москві тільки починали робити автомобілі, колінчаті вали вирізали із сталевої штаби. При цьому в стружку йшло близько 2/3 металу. Потім вали стали кувати. З поковок, отриманих вільним куванням, доводилося знімати тільки 1/2 металу. Тепер колінчаті вали штампують. Втрати зменшилися до 1/3. ще великі.
В останні роки машинобудівники стали застосовувати нові високоміцні і дуже дорогі матеріали. Тому перед технологами ковальського виробництва постало завдання - домогтися ще більш точних штамповок, щоб і за формою, і за розмірами Ені максимально наближалися до виробів. Це завдання тепер вирішена, і на ряді заводів виробляють великогабаритні точні штампування.
Чому ж зовсім не відмовитися від вільного кування? Тому що виготовити штамп складно і дорого: його роблять з дуже міцної сталі і дуже точно. До штампуванні вдаються в тих випадках, коли потрібно виготовити досить велика кількість однакових деталей. Тільки тоді витрати на виготовлення штампів виправдовуються.
Вільну ковку виробляють пароповітряними, пневматичними молотами.
Найпростіший паровий молот складається з масивної станини, у верхній частині якої знаходиться робочий циліндр, а в ньому 'поршень ,, пересувається вгору і вниз (як у велосипедному насосі). На кінці поршня - шток, до якого прикріплена важка сталева баба - молот. У циліндр, в простір під поршнем, під високим тиском подають пару -поршень разом зі штоком і бабою піднімається, Сильно стиснутий під поршнем пар утримує важкий молот у верхньому положенні.
Нагріту заготовку кладуть на ковадло, укріплену на чавунному або сталевому підставі.
Все готово. Можна почати ковку. Пара з-під поршня випускають і нагнітають його в простір над поршнем: баба падає і завдає удар по заготівлі. Так, по черзі впускаючи і випускаючи пару, піднімають і опускають бабу. Вона вдаряє по заготівлі, обжимає її. Заготівля поступово змінює форму, метал "розтікається".
Але ось кування закінчена. Деталь охоплюють ланцюгами, кран піднімає і забирає її. Негайно підвозять наступну заготовку.
Схема роботи пневматичного молота для кування металу.
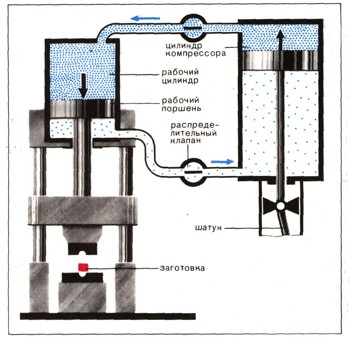
Важкі парові молоти поступово витісняються гідравлічними пресами. Потужності їх безперервно ростуть. Ще недавно максимальне зусилля пресів не перевищувало 100 МН. А зараз на радянських заводах діють кувальні преси із зусиллям в 300-400 МН і більше. Фундаменти, на які вони спираються, йдуть глибоко в землю -на десятки метрів. Щоб привести такі преси в дію, потрібні електродвигуни величезної потужності.
Штампувальні молоти мало чим відрізняються від молотів для вільного кування. Коли штампувальник натискає педаль, баба автоматично піднімається. Частина металу при штампуванні випливає в проміжок між двома половинками штампа, і утворюється задирок, який потім видаляють на обрізному штампі.
Штампи бувають одноруч'евие і многоручьевим (струмки - це поглиблення в нижній, нерухомої частини штампа, від форми яких залежить конфігурація деталі).
При роботі на одноручьевом штампі заготовку, попередньо підготовлену вільним куванням, доводиться перекладати з преса на прес, зі штампа на штамп, поки вона не прийме потрібної форми.
А на многоручьевого штампі всього за кілька ударів молота, перекидаючи заготовку зі струмка в струмок, можна виготовити складну деталь.
Схема процесу формування металу вибухом: над формою зміцнюється лист металу, яа точно розрахованій відстані над заготівлею підвішується вибухову речовину. Вибух відбувається в воді: вона рівномірніше розподіляє вибухову хвилю.
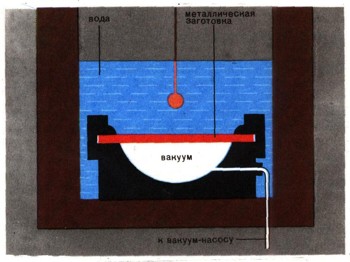
вибухова хвиля вдавлює метал в форму.
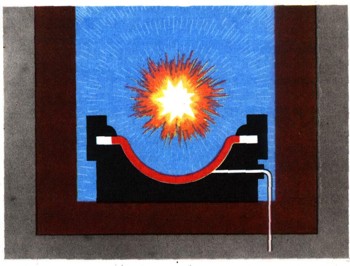
Різновид штампувальних молотів - горизонтально-кувальні машини. Їх застосовують для гарячого штампування деталей з прутків: кілець, втулок і т. Д.
У цих машин штампи зазвичай многоручьевим. Вони складаються з матриці і пуансона. Матриці тут - 2 металевих півкола, а пуансон -міцний сталевий стрижень. Зближуючись, матриці (рухаються вони по горизонталі, звідси і назва машини) затискають пруток і таким чином надають металу потрібну форму. У той же час укріплений на спеціальному повзунові пуансон (теж рухається по горизонталі) заходить в цю утворену матрицею порожнину, пробиває заготовку (пруток) і відрізає її.
Цим методом виготовляють, наприклад, кільця для підшипників.
Сучасна кузня мало схожа на кузні старих заводів. Пар, вода, стиснене повітря і електрику звільнили людину від важкої роботи. Людина безпосередньо більше не братиме участі у формуванні поковки або штампування. Сучасний коваль - механік при ковальської машині або навіть при автоматичній лінії з ковальських машин. Такі лінії, наприклад, успішно діють на автомобільних заводах. На них роблять колінчаті вали двигунів і інші складні деталі.
Щоб виготовити такі машини, потрібні величезні поковки. Їх доводиться робити на потужних молотах вільним куванням. Ось підйомний кран за допомогою гігантської "вилки" витягує з печі злиток і переносить його на ковадло молота.
Ніде не видно ковалів. Раптом лунає звук сирени. Широкими рейкової колії, прокладеної поперек прольоту, до молота під'їжджає металева будка на чотирьох кутках. Це так званий маніпулятор - механічний "коваль". З передньої стінки у нього видається масивний сталевий хобот. Він захоплює край зливка, затискає його, кладе на ковадло - молот починає свою роботу. Ось кування готова, хобот знову захоплює її і акуратно знімає з молота. Хто ж керує цією роботою сталевого "коваля"? Машиніст з кабіни маніпулятора. Перед ним табло з кнопками, важелі, з їх допомогою він пускає в хід механізми молота, переміщує злиток. Маніпулятор звільнив від важкої роботи 7 осіб.
Пошуки нових, більш досконалих способів додання металу необхідної форми привели до думки використовувати для цієї мети енергію направленого вибуху, виробленого в воді. Штампування вибухом має велике майбутнє, так як їй піддаються навіть
найтвердіші метали. На малюнку видно, як відбувається цей прогресивний технологічний процес. Над формою зміцнюється лист металу. Між ним і формою створюють вакуум. На точно розрахованій відстані над аркушем металу підвішується вибухову речовину. Потім все занурюється в воду (вода рівномірніше розподіляє вибухову хвилю, ніж повітря). Відбувається вибух, і вибухова хвиля з дивовижною точністю вдавлює метал в форму.
Пресування і холодна висадка
Штампування буває і холодної. В цьому випадку вона називається пресуванням. При пресуванні з листа металу або пластмаси вирубують (вирізують) деталь, а потім надають їй в спеціальних штампах або за допомогою згинальних верстатів потрібну форму. Так роблять різні деталі - від маленьких шай-бочок до кузовів автомобілів і корпусів літаків. Тільки преси, звичайно, для цих деталей використовують різні: для шайбочек - трохи вище звичайної тумбочки, а для панелей автомобільного кузова - з двоповерховий будинок.
Поряд з пресуванням деталей з листа в машинобудуванні все ширше застосовується метод холодного висадження - деталі отримують на механічних пресах без нагріву металевих заготовок. При цьому методі ширина однієї частини заготовки збільшується за рахунок її висоти, і навпаки. Так з різних металів і сплавів, а також з пластмас роблять прості шайби, болти і т. Д.
Метод холодного висадження завдяки своїй економічності все більш витісняє на машинобудівних заводах механічну обробку деталей на металорізальних верстатах. Справа в тому, що при холодній висадці деталей не утворюється стружки, тому цей спосіб прозвали ще безвідходним. Наприклад, раніше, щоб виготовити болт, треба було зробити 5-6 операцій на різних верстатах: фрезерному, токарному, різьбонарізні. І кожен раз з верстата звисала металева стружка. А тепер натиск преса - і вилітає зовсім готовий болт.
Компанія steeland.com.ua виробляють недорого ковані елементи на вибір.