електролізного ЦЕХ
1. Планування цеху
Електролізний цех являє собою адміністративно і територіально відокремлений підрозділ заводу з повним циклом виробництва - від прийому сировини до видачі товарної продукції. Крім електролізних корпусів, в яких розміщені електролізери, до складу цеху входять наступні відділення: ливарне, капітального ремонту електролізерів, очищення газів і регенерації фторсолей і допоміжних служб.
Електролізери включені в ланцюг послідовно, утворюючи серії. Число електролізерів в серії залежить від напруги джерел постійного струму. Для пре освіти змінного струму в постійний на сучасних заводах застосовуються напівпровідникові випрямлячі з напругою 850 В і коефіцієнтом перетворення 98,5% (робочий елемент в них кремній або германій). Один випрямний агрегат дає струм силою до 63 ка. Число таких агрегатів залежить від необхідної сили струму серії; причому всі вони включаються паралельно. Число працюючих електролізерів в серії визначається також середнім напругою на ванні (за вирахуванням падіння напруги від анодних ефектів) і робочою напругою серії. Остання складається з напруги випрямлячів, зменшеного на падіння напруги всередині перетворювальної підстанції (близько 1% від загальної напруги), резерву напруги на одночасно виникають анодні ефекти (близько 30 В) і резерву напруги для компенсації коливань його у зовнішній мережі (близько 1%).
Таким чином, якщо напруга випрямних агрегатів 850 В, то робоча напруга серії буде 800 В і число працюючих ванн 800 / (Uср - Uа.е), де Uср- середня напруга на кожному електролізері, В; Uа.е - збільшення напруги за рахунок анодних ефектів, В. Число встановлених в серії електролізерів дорівнює числу робочих плюс число резервних, яке може бути підраховано зі співвідношення
де п - число робочих електролізерів; п1 - число резервних електролізерів; тр - тривалість простою електролізера на капітальному ремонті, діб; ТС середній термін служби електролізерів, сут. Зі співвідношення (82) випливає: n 1 = nTр / (Тс -Tр), т. Е. Число резервних електролізерів тим більше, чим більше термін капітального ремонту, і тим менше, чим більше термін служби електролізерів. Наприклад, якщо робоча напруга серії 800 В, то число робочих електролізерів буде близько 190 і резервних 4. Таке число електролізерів повинна бути розміщена в двох електролізних корпусах. Електролізні корпусу входять до складу серії; в цеху може бути кілька електролізних серій. Електролізні корпусу розташовані паралельно один одному і з'єднані між собою транспортним коридором (рис. 58). Для кращої аерації корпусу розташовують вздовж напрямку пануючого протягом року вітру. Між серіями знаходяться ливарне відділі ня, блок допоміжних служб і відділення капітального ремонту електролізерів, а також адміністративні та побутові приміщення.
2. Корпус електролізу
У старих корпусах електролізер БТ розміщені в чотири ряди, що створює труднощі аерації корпусів. Тому електролізери нових конструкцій і великої потужності розташовуються в два ряди. Зазвичай довга вісь електролізера збігається з поздовжньою віссю корпусу (поздовжнє розташування), але електролізери великої потужності типу OA розташовують поперек корпусу в один ряд (поперечне розташування). Довжина корпусів в залежності від числа електролізерів і їх габаритних розмірів досягає 700 м, ширина зазвичай складає 27 м, що визначається стандартними габаритними розмірами мостових кранів.
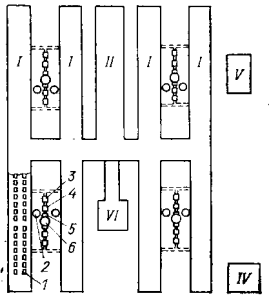
Мал. 58. Приблизний план електролізного цеху: I - електролізний корпус; II- ливарна; III - перетворювальна підстанція; IV - відділення капітального ремонту; V - склад глинозему; VI - адміністративний корпус; 1 - електролізер; 2 - бункер для глинозему; 3 - електрофільтр; 4 - скрубер; 5 - вентилятор; 6 - труба
У сучасних корпусах електролізери ВТ і OA встановлені так, що робочі майданчики збігаються з підлогою другого поверху і розташовані на позначці + 4 м. Такі двоповерхові корпуси дозволяють організувати природну аерацію, при якій холодне зовнішнє повітря надходить через віконні прорізи першого поверху, нагрівається під днищем кожухів електролізерів, проходить через підлогові решітки другого поверху
і спрямовується до ліхтарів на даху корпусу. На відміну від одноповерхових корпусів (для електролізерів БТ) тут немає необхідності в пристрої спеціального припливної вентиляції. Однак через відсутність такої вентиляції неможливо регулювати приток свіжого повітря, а головне, - підтримувати певну його температуру. Одноповерхові корпусу мають висоту (до нижньої основи ферм даху) 13-14 м, двухетажние- 18 м (рис. 59). Аерація разом з припливною вентиляцією забезпечують певну кратність повітрообміну (відношення обсягу подається в годину повітря до обсягу корпусу електролізу); для зимового часу кратність становить 15, для літнього -40.
Стіни корпусу виконані зі збірного залізобетону, мають вікна, в яких замість скла вставлені синтетичні плівки, оскільки скло швидко втрачає світлопроникність під дією фтористих солей. При двухрядном поздовжньому розташуванні електролізерів відстань між торцями сусідніх електролізерів зазвичай прагнуть звести до мінімуму, т. Е. Щоб в проміжку між електролізерами містилися тільки анодні стояки ошиновки. При цьому досягається певна економія капітальних вкладень за рахунок скорочення довжини корпусу і економія на ошиновке та інших комунікаціях. Для проходу обслуговуючого персоналу і проїзду машин, що обробляють ванни, в кожному ряду електролізерів між групами ванн є проходи шириною 1 м і проїзди шириною 3 м. Транспортний коридор, що проходить поперек всіх корпусів і інших виробничих приміщень через їх середину, має ширину близько 12 м і служить для транспортування металу, глинозему та інших матеріалів.
Відстань між рядами електролізерів складає близько 7 м (між кожухами електролізерів), що забезпечує можливість руху машин і механізмів. обслуговуючих електролізери, в двох напрямках. Відстань між стінами корпусу і поздовжніми сторонами електролізерів близько 4 м, що дозволяє обробляти машинами електролізери з цих сторін. У торцях корпусів на позначці другого поверху є майданчики для ремонту обладнання і розміщення матеріалів. Довжина цих майданчиків (відстань від кожухів крайніх ванн до торцевих стінок корпусу) може бути до 35 м.
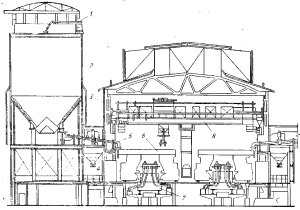
Мал. 59. Поперечний розріз корпусу електролізера.
Для транспортування вантажів, витягів штирів (електролізери ВТ) і операцій по демонтажу та монтажу електролізерів в корпусах є мостові крани. За родом виконуваних операцій розрізняють крани технологічні (перевезення вантажів, витяг штирів і ін.) І монтажні (перевезення анодного і катодного пристрою електролізерів ВТ вантажопідйомністю 150 ÷ 200 т). Для установки монтажних кранів потрібні стіни корпусу посиленої конструкції, а, отже, і великі капітальні витрати. Для електролізерів OA застосовуються інші рішення - катод пристрій при демонтажі і монтажі електролізерів опускається і піднімається за допомогою домкратів і перевозиться спеціальними великовантажними платформами по першому поверху.
Між корпусами близько транспортного коридору встановлені прийомні бункера для глинозему, в які глинозем подається пневмотранспортом зі складу. Уздовж стін корпусу є прибудови для витратних бункерів, в які глинозем надходить з прийомних бункерів.
3. Вентиляція, газоотсоса регенерація фтористих солей
При електролізі алюмінію виділяється значна кількість шкідливих в вигляді газів і пилу. Залежно від типу і потужності електролізера на 1 т алюмінію виділяється: 8-12 кг фтористого водню, 9-12 кг твердих фторидів в вигляді пилу (в перерахунку на фтор), 11-12 кг сірчистого ангідриду. Для електролізерів БТ і ВТ, крім того, з поверхні анода виділяється значна кількість шкідливих в вигляді летючих речовин. У повітрі робочої зони, крім пилу фтористих солей, витає досить багато пилу глинозему розміром близько 1 мкм, яка також представляє собою небезпеку для здоров'я працюючих. І, нарешті, від електролізерів в цех надходить значна кількість тепла. Теплонапруженість (кількість тепла, що надходить на 1 м 3 робочої зони на годину) для електролізерів середньої потужності становить 400 кДж / (м 3 · год), для електролізерів великої потужності 800 кДж / (м 3 · год).
Для видалення шкідливих речовин на електролізерах всіх типів є місцеві відсмоктувачі та укриття. Так, на електролізерах БТ име ється шторних укриття, що закриває весь електролізер. Системою газоотсоса через штори просасивается зовнішнє повітря і разом з ним видаляються шкідливості, що виділяються як з кірки електроліту, так і з поверхні анода. Норми відсмоктування залежать від потужності електролізера: зазвичай 1200-1500 м 3 / ч на кожні 10 кА. Для повітрообміну в корпусу, обладнані цими електролізерами, надходить свіже повітря за допомогою системи припливної вентиляції. У зимовий час повітря проходить через калорифери і далі надходить в канали припливної вентиляції, розташовані між рядами ванн. Ефективність шторного укриття (т. Е. Частка шкідливих речовин, що видаляються системою, від загальної кількості шкідливих) становить 85-90% і визначається часом роботи ванн з відкритими шторами.
На електролізерах ВТ шкідливості надходять в Дзвонове укриття і далі в пальники, в яких відбувається дожигание СО. Обсяг відсмоктується газу приблизно на порядок менше, ніж на електролізерах зі шторним укриттям, а концентрація шкідливих речовин в ньому відповідно вище, що полегшує завдання повного очищення газів. Разом з тим, при обробках ванн все шкідливості надходять в простір корпусу. Крім того, і в проміжках між обробками гази проходять між нещільно в секціях газозбірного дзвони або в тріщинах. Тому ефективність церковного газоотсоса невелика - 60-70%. Інша кількість шкідливих виноситься аерацією через ліхтарі на даху корпусу в навколишній повітряний простір. У цьому один з головних недоліків електролізерів ОТ.
На електролізерах OA проблема видалення шкідливих вирішується пристроєм укриттів стулчастого типу. При заміні анода відкривають тільки одну стулку над ним, при обробці ванни - половину укриття з однієї поздовжньої сторони. Ефективність стулчастого укриття 90-95%. При тривалій роботі ефективність знижується за рахунок збільшення нещільності між стулками, викликаного викривленням їх через нерівномірне нагрівання.
Гази з корпусу електролізу надходять в систему газоочистки. Зазвичай застосовується двоступенева система «мокрою» очищення (рис. 60): для видалення пилу і смолистих речовин гази проходять через електрофільтр, потім надходять в скрубер або пінний апарат, де проходять другу сходинку очищення - поглинання фтористого водню содовим розчином. Далі гази направляються в трубу, через яку і викидаються в атмосферу. Щоб розвіяти їх на великі відстані і тим еамим зменшити концентрацію шкідливих труба має висоту 120 м.
У двоступеневих установках знепилювання здійснюють в електрофільтрах різного типу з напругою до 90 кВ постійного струму. У мокрих електрофільтрах осад пилу на осади-них електродах видаляється змиванням, в сухих - струшуванням. В тому і в іншому випадку пил спрямовується в силосні башти, звідти - в бункера електролізного цеху. Другий ступінь очищення здійснюється в скрубберах різного типу або в пінних апаратах, зрошуваних 3-5% -ним розчином соди. Найбільш надійні з апаратів пінного типу, апарати зі стабілізацією пінного шару, в яких ступінь поглинання фтористого водню досягає 95-98%.
При поглинанні содовим розчином відбувається реакція HF + NaСО3 = NaF + NaHC03. Содовий розчин циркулює в системі поглинання до тих пір, поки концентрація NaF не досягне
15 ÷ 20 г / л Потім розчин надходить у відділення регенерації криолита Тут він піддається освітленню для відділення зважених часток глинозему і вуглецю, які йдуть у відвал, і надходить в реактор на варіння криолита. В реактори подають також приготований розчин алюмінату натрію і при температурі 75 С йде реакція
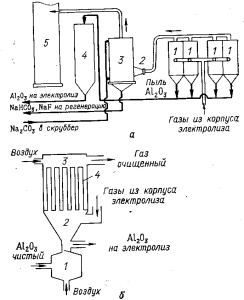
Мал. 60. Схеми газоочистки: а - «мокра»; 1 - електрофільтр; 2 - вентилятор; 3 - скрубер; 4 - силосна вежа для глинозему; 5 труба; 6-суха: 7 - камера змішування; 2 - бункер; 3 - рукавний фільтр; 4 - рукав
Кристали криолита відокремлюють від маточного розчину згущенням, кріоліт фільтрують, промивають, висушують і направляють на електроліз. Матковий розчин надходить на приготування оборотного содового розчину, для чого в нього вводять свіжу соду і на-
правляться в систему газоочистки. Отриманий, так званий регенераційні кріоліт має К.О. = 4 і забруднений домішками оксидів заліза, кремнію, сульфатами і ін. Його використовують в основному на пуску ванн. Розглянута схема «мокрою» очищення газів характеризується складністю і значною кількістю відходів.
Від цих недоліків вільна «суха» очищення, розроблена в останні роки. Гази електролізного виробництва пропускають через рукавні фільтри, на внутрішню поверхню яких нанесено шар Аl2 О3. При проходженні газу глинозем поглинає з нього фтористий водень з утворенням, як передбачається, з'єднання Al2 О3 HF. Сорбційна здатність глинозему залежить від його питомої поверхні і від змісту γ-фракції; для звичайного металургійного глинозему питома поверхня повинна бути не менше 40 м 2 / г (Буркат та ін.). Залежно від сорбційних-ної здатності на установки газоуловлювання подається від 40 до 100% всього глинозему, що йде на електроліз.
Чистий глинозем надходить в камеру 1 (рис. 60, б), в якій він змішується з повітрям і подається для осадження на поверхню фільтрів. Коли шар глинозему на фільтрах досягає товщини близько 1 мм, камера 1 відключається, і на фільтри починає надходити забруднене газ електролізного виробництва. Очищений газ димосмоками викидається через трубу в атмосферу. Після закінчення певного часу, коли сорбція стає малоефективною, подачу забрудненого газу припиняють і зовні рукавів подають стиснене повітря для отдувки глинозему, який з рукавів падає в бункер і передається в ємності для подальшого транспортування на електроліз. Цикл очищення повторюється.
Рукава мають розміри: діаметр 0,3 м, висоту 10 м; вони об'єднані в секції по 200 шт. в кожній. Для очищення газів великого заводу необхідно мати до десяти таких секцій. Фільтруючими тканинами служать матеріали, здатні протистояти агресивному впливу газів при 150 ° С: поліестер, лавсан та ін.
Зазначена система очищення придатна для електролізерів OA. Для електролізерів БТ і ВТ, гази яких містять значну кількість вуглецевих возгонов, забивають фільтри, розроблена інша система: «реактор - рукавний фільтр». У цій системі поглинання HF, пилу і возгонов відбувається головним чином в реакторах, в яких гази енергійно перемішуються з глиноземом. Потім суміш надходить на фільтрацію.