Знаючи довжину шляху інструменту l0 і подачу s0 визначимо число обертів шпинделя n0. необхідне для виконання кожного переходу.
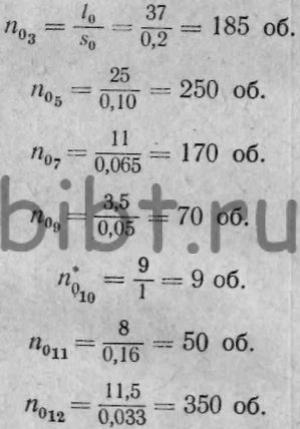
(* Число оборотів шпинделя дорівнює кількості повних ниток нарізати різьблення)
Отримані числа обертів шпинделя n0. необхідні для виконання окремих робочих переходів за пройдене інструментом відстань l0 при виготовленні деталі вказуємо в графі 6 технологічної карти (табл. 56).
1. При підвищених вимогах до чистоти обробки (не нижче v 4) подача не повинна перевищувати 0,05 мм / об при фасонної обробки; при відрізанні - 0,08 мм / об, а при точінні -0,2 мм / об.
2. Подання під час свердління і центрування 0,05-0,3 мм / об, в залежності від діаметру інструменту.
3. Подача при зенкування і розгортання 0,10-0,5 мм / об.
4. Подача при поздовжньому накоченні 0,08-0,4 мм / об.
5. Подання при поперечному накоченні відповідають подачам фасонного різця.
З огляду на, що різні переходи здійснюються при різних оборотах шпинделя n, в результаті чого число оборотів шпинделя непропорційно витрат часу на виконання переходів, для розрахунку настройки верстата користуються наведеними числами оборотів шпинделя nпр. пропорційними витратами часу. Отже, кількість обертів шпинделя необхідно привести до якогось одного числа обертів, т. Е. Ввести коефіцієнт приведення ψ.
За основне число обертів nосн шпинделя в хвилину зазвичай приймають число оборотів найбільш часто зустрічаються переходів, які виконуються на порівняно великих швидкостях різання, т. Е. На максимальних числах оборотів шпинделя.
Відповідно до встановлених переходами найбільше число обертів передбачено для третього переходу, т. Е nосн = n = 1500 об / хв.
Наведене число обертів шпинделя nпр для всіх інших переходів, які виконуються при більш низьких швидкостях різання, визначається множенням дійсно потрібної кількості оборотів шпинделя n0 для даного шляху інструменту на коефіцієнт приведення ψ.
Коефіцієнт приведення ψ дорівнює відношенню основного числа обертів шпинделя за хвилину (nосн) до числа оборотів шпинделя в хвилину (n), при якому виконується даний перехід.
Для третього, п'ятого, дев'ятого і дванадцятого переходів, які виконуються при n = 1500 об / хв. отримаємо
для сьомого переходу
для десятого переходу
для одинадцятого переходу
Користуючись коефіцієнтом приведення ψ. отримаємо наведені числа обертів
Значення коефіцієнтів приведення ψ заносимо в ліву верхню частину технологічної карти, а наведені числа обертів в графу 7, табл. 56.
Користуючись наведеними числами оборотів nпр знайдемо загальну суму всіх чисел оборотів nпр. необхідну для виконання всіх робочих переходів (Поєднані переходи - другий, четвертий, шостий і восьмий - не враховуються.) при виготовленні однієї деталі
Для визначення тривалості допоміжних (неодружених) і робочих ходів, вираженої в сотих частках (променях) циклу, необхідно визначити:
1) орієнтовну тривалість циклу;
2) кількість променів, що припадає на допоміжні ходи;
3) кількість променів, що припадає на робочі ходи;
4) кількість оборотів шпинделя за цикл;
5) кількість оборотів шпинделя, яке припадає на один промінь;
6) кількість променів, яке необхідно для виконання кожного переходу.
Загальну тривалість циклу Тп.ц. орієнтовно можна визначити за формулою
де tn - машинний час, що витрачається на виконання робочих переходів.
де- загальна сума всіх наведених чисел оборотів;
n - число обертів шпинделя за хвилину.
Кількість сотих кулачкового диска (променів), необхідне на холості ходи Кх. визначають залежно від загальної тривалості циклу Тп.ц для даного автомата відповідно до даних паспорта верстата.
Зазвичай холості ходи Кх мають наступну орієнтовну тривалість:
де - 1 сек. - час для подачі і затиску матеріалу;
t2 = 0,667 сек. - тривалість першого перемикання револьверної головки на 1/6 обороту;
для кожного наступного перемикання револьверної головки приймаємо t2 = 1,5 -2 сек. т. е.
t3 = 0,25 сек. - час перемикання напрямку обертання шпинделя;
сек. - час на відведення відріз ного різця;
t5 - час на зачистку інструментом поверхонь деталі в кінці обробки (З урахуванням часу на зачистку приймається рівним 0,5 сотих кулачкового диска (променів)).
Кількість сотих холостих ходів приймаємо в залежності від їх тривалості, яке вказується в паспорті верстата. Ці дані заносимо в графу 9 технологічної карти (табл. 56). Загальна кількість сотих холостих ходів становить Kx = 17,5 променя. Для побудови кривих холоcтих ходів слід користуватися спеціальним шаблоном, який викреслюється в масштабі 1. 1 і додається до паспорту верстата (фіг. 138).
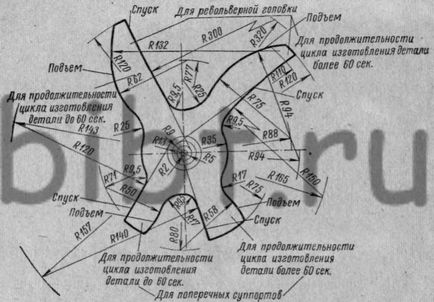
Фіг. 138. Шаблон для побудови кривих холостих ходів.
Кількість сотих кулачкового диска (променів) для окремих робочих ходів (переходів) Kр.х визначається за формулою променя,
де Kр.о - загальна кількість сотих диска для всіх робочих переходів;
nпр - наведене число обертів шпинделя для виконання даного переходу;
- загальна сума всіх наведених чисел оборотів.
Кількість сотих кулачкового диска Kp буде
де Kx - кількість променів для здійснення холостих ходів.
Для автомата +1136 Kx = 17,5 променя. Для відповідних переходів отримаємо
Отримані значення кількості променів кулачка Kp для окремих робочих ходів заносимо в графу 8 технологічної карти (табл. 56). Кількість сотих робітників і неодружених послідовно розташованих переходів в наростаючому порядку заносимо туди ж в графи 10 і 11.
При визначенні радіусів на кулачках для кожного переходу необхідно враховувати відстань від торця шпинделя до револьверної головки. Найменша відстань для кожного переходу, рівне 75 мм, показує, що в третьому переході в кінці обточування ролик найбільш віддалений від центру кулачкового диска револьверної головки (R = 120 мм - найбільший радіус кулачкового диска).
Початком підйому кривої для зазначеного переходу, з урахуванням довжини шляху l0 при обтачивании деталі по Ø 24 мм, буде
де - шлях інструменту при робочому ході (табл. 56, графа 4).
П'ятий перехід - обточування деталі по> Ø 20 мм буде закінчено в частині кулачка з радіусом R5.
де L5-відстань від торця шпинделя до револьверної головки на п'ятому переході;
L3 - відстань від торця шпинделя до револьверної головки на третьому переході.
Початком підйому кривої для зазначеного переходу з урахуванням довжини шляху інструменту буде
У наступних переходах, в залежності від величини зміни відстані між торцем шпинделя і револьверної головкою, кінцеві радіуси матимуть інші значення.
На сьомому переході
На десятому переході
Радіус кулачка для закінчення нарізування різьблення береться зазвичай менше на 10-15% довжини різьблення, щоб плашка не притискаючись з великим зусиллям до державки і револьверна головка рухалася б з деяким відставанням. З цієї причини застосовуються так звані висувні державки. Тому в технологічній карті (табл. 56) в графі 13 радіус на 1 мм менше т. Е. R10 = 99 мм.
На одинадцятому переході
Радіус кулачка при останньому перемиканні головки (одинадцятий перехід) вибирається конструктивно, т. Е. В даному випадку R = 70 мм.
Радіуси перемикань револьверної головки зазвичай зменшують на 1-1,5 мм.
Відповідно до даних, отриманими при розрахунку сотих (променів) і радіусів кулачкового диска, виробляємо побудова профілю і креслення кулачка револьверної головки (фіг. 139).
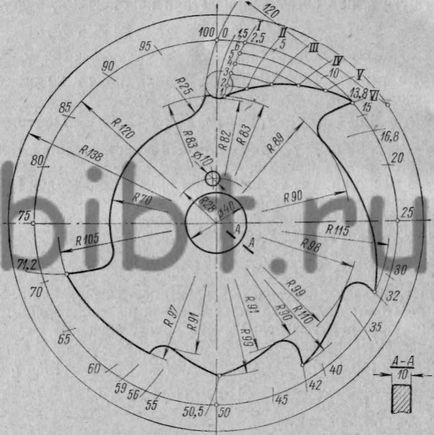
Фіг. 139. Побудова профілю кулачка револьверної головки.
При визначенні радіусів кулачків поперечних супортів слід враховувати, що найбільший радіус кулачка Rn = 75 мм відповідає положенню, коли ріжучакромка інструменту знаходиться на осі деталі, т. Е. Доходить до центру деталі, а ролик важеля прилягає до найбільшого діаметру кулачка.
На дев'ятому переході - обробка фасонного профілю і канавки Ø 14 мм - ріжучакромка інструменту, встановленого на передньому супорті, не доходить до центру деталі на величину r = 7 мм. Отже, найбільший радіус кулачка переднього супорта буде
Мінімальний радіус кулачка складе
де- шлях інструменту при робочому ході для дев'ятого переходу.
На дванадцятому переході - відрізка деталі - найбільший радіус кулачка вертикального супорта буде а мінімальний радіус кулачка
Радіуси на кулачках для кожного переходу вказують в графах 12 і 13 технологічної карти (табл. 56).
Різець, встановлений на передньому поперечному супорті, виробляє обточування деталі починаючи від променя 71,2 до 75,5 (фіг. 140, а). Крива кулачка, побудова якої починається у променя 75,5, знижується від найбільшого радіуса R = 68 мм до мінімального радіуса R = 64,5 мм. Точки на променях 75,5 і 71,2, отримані відповідно до радіусами R, з'єднують кривої, побудованої по Архімедова спіралі.
Різець, встановлений на вертикальному супорті, виробляє обточування деталі починаючи від променя 75,5 до променя 97,0 (фіг. 140, б). Крива кулачка починається у променя 97,0 від найбільшого радіуса R = 75 мм до мінімального радіуса R = 63,5 мм.
Для полегшення роботи з викреслювання на кулачках кривих холостих ходів, т. Е. Кривих підведення і відведення робочого вузла, слід користуватися спеціальним шаблоном (фіг. 138). Підведення і відведення револьверної головки або іншого робочого вузла повинні виконуватися в мінімальний час, а отже криві холостих ходів кулачка повинні мати крутий підйом і крутий спуск.
Час виготовлення однієї деталі або тривалість циклу (одного обороту розподільного вала) визначається за формулою
де nшп.осн - основне число обертів шпинделя за хвилину;
nц - число обертів шпинделя, необхідне для виготовлення однієї деталі (за 1 цикл)
Отримане час обробки Т уточнюють відповідно до таблиці тривалості одного обороту розподільного вала з урахуванням застосовуваних змінних зубчастих коліс, що додається до паспорта верстата.
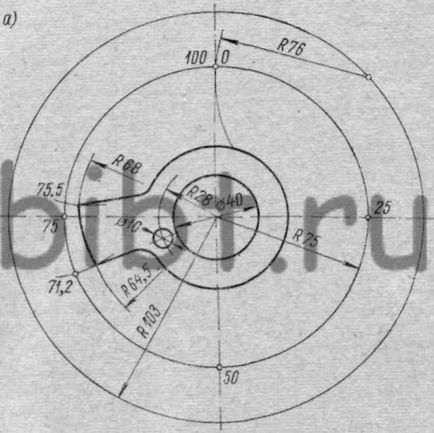
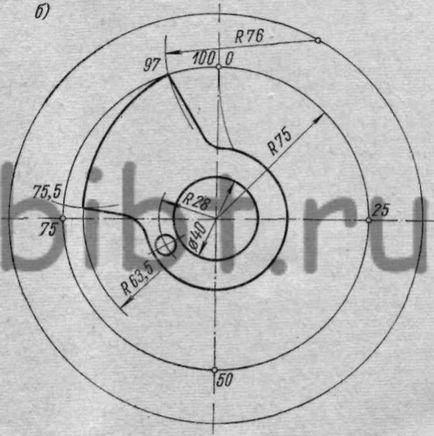
Фіг. 140. Побудова профілю кулачка поперечного супорта. а - переднього; б - заднього.
Відповідно до таблиці змінних зубчастих коліс розподільного вала верстата 1136, має тривалість одного обороту розподільного вала, т. Е. Час на обробку однієї деталі складе 65 сек.
Продуктивність Q автомата виражається кількістю деталей, виготовлених в одиницю часу
де Т - час обробки однієї деталі в сек.
Дійсну штучну продуктивність Qд з урахуванням втрат можна визначити за формулою
де η = 0,8 - 0,95 - коефіцієнт використання верстата.