Сварка (наплавка) кольорових металів зі сталлю представляє певні труднощі. Наприклад, при зварюванні латуні зі сталлю газовим зварюванням відбуваються вигоряння і випаровування цинку в металі шва і погіршення його якості (пористість і зниження міцності). Крім того, пари цинку насичують навколишній простір, що шкідливо для здоров'я людини.
Технологічний процес зварювання латуні зі сталлю вугільної дугою запропонований новаторами заводу «Електроапарат» Н. М. Цибульським, В. І. Кузьмичовим і І. О. Чечісом. Цей процес забезпечує високу якість зварного з'єднання і зменшення виділення шкідливих парів цинку при зварюванні латуні зі сталлю.
Особливості запропонованої технології полягають і наступному:
1. Зварювання проводиться графітовим електродом діаметром до 10 мм. Електрод рекомендується заточувати на конус.
2. В якості присадочного металу застосовується легкоплавка бездимна латунь марки ЯК-62-05.
3. присадні дріт покривається флюсом, що складається з 25-30% бури і 70-75% борної кислоти. Перед нанесенням флюсу гарячим способом присадний дріт нагрівається газовим пальником до вишневого кольору, посипається сумішшю бури і борної кислоти, а потім підігрівається ще раз. При холодному способі присадний матеріал спочатку занурюється в рідке скло, після чого посипається сумішшю і просушується на повітрі.
4. Сварка ведеться постійним струмом прямої полярності при довжині дуги, що дорівнює в середньому 2-5 мм. Величина зварювального струму встановлюється для катета шва 5 мм в 270-300 А, а для шва 4 мм - 250-275 А.
5. При зварюванні виріб розташовують під кутом 5 10, електрод нахиляють на кут 75-90 ° до осі шва, а присадні дріт на кут 30 ° у протилежну сторону. Зварювання проводиться справа наліво.
6. Накладення шва здійснюється при рівномірному коливальному русі електрода - з відповідними рухами присадочного матеріалу.
При зварюванні латуні робоче місце повинно бути обладнане добре діючої місцевої вентиляцією. Найбільш зручно проводити зварювання на столі з гратами, оснащеному системою витяжки газу вниз, що забезпечує кращу видимість формованого шва.
На Електродотримачі рекомендується встановлювати козирок для захисту руки від тепла дуги.
Сварка графітовим електродом значно покращує якість і зовнішній вигляд зварювальних швів, а також підвищує продуктивність праці.
Річна економічна ефективність від впровадження становить 10 тис. Рублів.
Спосіб наплавлення оловянистой бронзи на сталь. При наплавленні мідних сплавів безпосередньо на сталь відбувається проникнення кольорового металу в сталь. Для виключення цього явища існує ряд способів: наплавка проміжного шару на сталь, створення полів стискають напруг в поверхневому шарі сталі та ін. Однак такі способи знижують в 2-3 рази міцність від утоми наплавлених виробів.
З метою виключення зазначеного недоліку групою новаторів запропоновано новий спосіб наплавлення оловянистой бронзи на сталь (авт. Свід. № 548391), який полягає в наступному. На поверхню стали попередньо наплавляют шар кременистої бронзи або латуні. Ці сплави утворюють дифузійну прошарок в зоні наплавлення, яка при подальшій наплавленні оловянистой бронзи перешкоджає її проникненню в сталь. Щоб прошарок в процесі наплавлення оловянистой бронзи НЕ розплавляється, товщина її повинна бути не менше 2-3 мм.
Спосіб зварювання сталеалюмінієвих трубних перехідників встик. В енергетиці та інших областях техніки знаходять застосування трубопроводи зі сталі та алюмінію. З'єднання труб з різнорідних металів проводиться аргоно-дугового зварювання неплавким (вольфрамовим) електродом.
Новатори Ленінградського кораблебудівного інституту Г. А. Бєльчук і Б. А. Кох розробили спосіб зварювання сталеалюмінієвих трубних перехідників встик (авт. Свід. № 484944) на заміну раніше застосовувався способу зварювання внахлестку.
Особливостями запропонованого способу є:
а) несиметрична оброблення крайок з кутом скоса сталевої деталі в 1,5-2 рази більше алюмінієвої;
б) багатопрохідний двостороння наплавка з попереднім підігрівом. Товщина алюмінієвої заготовки вибирається в 2 рази більше сталевий.
Труби, спочатку піддається попередній обробці: сталеву трубу очищають і алітіруют на довжині 100-150 мм, а алюмінієву - знежирюють, цькують і пасивують. Потім проводять оброблення крайок сталевої труби 3 під кутом 70 °, а алюмінієвої 1 - під кутом 40 °, як показано на рис. 24.
Перед зварюванням труби збирають з зазором 1,5-2 мм і підігрівають до 100-120 ° С.
Наплавлення металу виконують таким чином. Внутрішній шов 4 утворюють в послідовності а, b, с, а зовнішній шов 2 - d, е, f, g, h. Після зварювання посилення зварного шва видаляють шляхом проточки з двох сторін.
Розроблений спосіб зварювання забезпечує підвищення якості з'єднання сталеалюмінієвих труб.
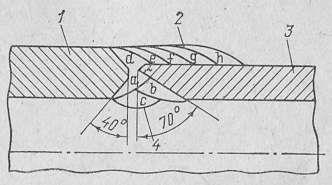
Мал. 24. Схема зварювання сталеалюмінієвих трубних перехідників встик.
Спосіб відновлення ножів прес-ножиць наплавленням. У виробничому об'єднанні «Кіровський завод» впроваджено спосіб відновлення ножів прес-ножиць наплавленням, що дозволяє замінити трудомістку операцію проточки ножів і продовжити їх термін служби.
Перед наплавленням зношені ділянки розправляються фрезеруванням. Зварювання виробляють електродами марок УОНІ 13/4 ХЮВ5МФС і ЕН-60М з попереднім підігрівом ножів в печі до температури 350- 400 ° С.
Режим наплавлення електродами діаметром 5 мм наступний:
Після наплавлення ножі піддають механічній обробці. Досвід експлуатації відновлених ножів показав, що стійкість їх не нижче стійкості нових.
Річний економічний ефект від впровадження наплавлення склав близько 20 тис. Рублів.
Автоматичне зварювання під флюсом із застосуванням порошкоподібного присадочного матеріалу. У центральній зварювальної лабораторії тресту «Союзпромбуммонтаж» розроблені рекомендації по виробництву автоматичної зварки під флюсом із застосуванням порошкоподібного матеріалу для стикових з'єднань листових металоконструкцій товщиною до 30 мм. В результаті досліджень і впровадження даного способу зварювання виявлені великі переваги його перед звичайною зварюванням під флюсом, які полягають у наступному:
1) відпадає операція оброблення крайок зварюваних листів незалежно від товщини металу;
2) зварювальне з'єднання виконується двостороннім зварюванням за два проходи;
3) відпадає необхідність у флюсовій подушці, яка замінюється тимчасової сталевий підкладкою;
4) зменшується витрата зварювального дроту в середньому на 60%;
5) підвищується в 2-2,5 рази продуктивність підготовчих і складально-зварювальних робіт;
6) знижується в 2 рази і більше собівартість виконання 1 пог. м шва;
7) підвищується якість зварювання (відсутні прижоги, поліпшується формування шва, підвищуються механічні властивості зварного з'єднання).
Рекомендації включають вимоги до зварювальних матеріалів, флюсу і присадним матеріалами, а також до підготовки листів під зварювання.
Зварювальний дріт надходить на зварювання в очищеному від бруду, масла і фарби вигляді, а флюси (АН-348А або АН-26) повинні бути прожарити при температурі 200-250 ° С протягом 1 -1,5 год.
Порошкоподібний присадний матеріал (ППМ) виготовляється. з електродного дроту марок Св-08А, Св-08Г2С, Св-08ГА і ін. діаметром 1-2 мм.
При виготовленні порошку з присадочного матеріалу необхідно, щоб довжина 'кожної крупинки не перевищувала діаметра дроту, за винятком дроту діаметром 2 мм, де ця довжина повинна бути не більше 1 мм. У табл. 2 дані рекомендації з вибору марки ППМ для різних марок металу зварюваних листів.
Що підлягають зварюванню листи після очищення кромок від бруду, іржі і масла збираються з необхідним зазорів в стику, а на кінцях з'єднань прикріплюються вхідні і вихідні пластини, рівні товщині зварюваних листів. З боку, протилежного основного шву, рекомендується встановлювати прихватки довжиною 40-50 мм.
Щоб уникнути висипання порошку або крупки в зазор між крайками під зварюваний стик підкрадається металевий лист або смуга. ППМ засипається в зазор між крайками в необхідному обсязі. Наприклад, ППМ з дроту діаметром 1,0-1,5 мм засипається в зазор урівень. Сварка з використанням ППМ проводиться в два проходи. При виконанні другого проходу з боку, протилежного першому, необхідно виробляти розчищення кореня шва Електрошліфовальная машиною з колами товщиною 3 мм.
Для зварювання може бути застосоване стандартне обладнання: автомати ТС-17МУ, ТС-35, АДС-1000-2. Як джерела живлення можна використовувати зварювальні перетворювачі ПСМ-1000-1, ПСМ-1000-4 і випрямлячі УКСМ-1000. Зварювання проводиться на токах зворотної полярності.
Описані рекомендації можуть бути також з великим ефектом застосовані при зварюванні в нижньому положенні з односторонньою або двосторонньою -разделкой стиків, кутових швів балок і колон великого перерізу способом «у човник».
Порошкоподібний присадний матеріал (ППМ) для різних марок металу зварюваних листів і електродного дроту