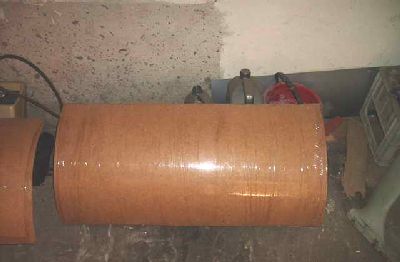
В одному з народних прислів'їв говориться, що зустрічають по одягу, тобто перше враження про людину складається так, як він одягнений. Це правило підходить і для меблів, адже одним із критеріїв, якими людина керується при покупці меблів, є її зовнішній вигляд. А для корпусних меблевих виробів - це фасади.
До виготовлення треба ставитись дуже серйозно, адже ніхто не захоче купувати неякісно виготовлений фасад (навіть якщо по художньому задуму він добрий чи унікальний). Впливає на вигляд фасаду і матеріал, з якого він виготовлений, і його покриття. По виду використовуваного матеріалу фасади можна розділити на:
На сьогодні в меблів, які доступні для широкого загалу населення, використовують фасади з MDF. Вони набагато дешевше фасадів з натурального дерева і забезпечують естетичний вигляд і широку гаму цветов.Последнее залежить від асортименту плівок або фарб.
За своєю конструкцією фасади з MDF можуть бути:
Оскільки, цільні і цільно-гратчасті фасади з MDF прості для виробництва від фасадів рамки-тахлевой конструкції, то розглянемо саме їх.
Що потрібно для виробництва
Як і для будь-якого виробництва, для виготовлення ламінованих фасадів із MDF потрібно мати певний комплекс обладнання, яке б забезпечувало необхідну якість і продуктивність. Для забезпечення технології виробництва МДФ фасадів необхідно наступне обладнання:
а) вакуумний мембранний;
б) вакуумний безмембранних;
в) прес з еластичною подушкою.
Як виглядає технологічний процес
Технологічний процес виробництва цілісних ламінованих фасадів із MDF починається зі складання карт розкрою і самого розкрою плити відповідного формату на форматно-розкрійному верстаті.
Після розкрою заготовки надходять на обробний центр (або фрезерний верстат з ЧПУ) де їх фрезерують. Під час фрезерування на пласті заготовки створюють певний малюнок з певним рельєфом.
Для спрощення програмування верстата з ЧПУ, а також для підвищення його продуктивності заготовки по периметру обробляють на фрезерному верстаті з кареткою. При невеликих обсягах виробництва фрезерування по периметру можна здійснювати за допомогою ручного фрезера.
Після фрезерування на поверхнях утворюється ворс, який негативно позначається на зовнішньому вигляді виробу. Тому заготовки передають на ділянку шліфування.
Наступною операцією в технологічному процесі є операція нанесення клею, яке проводиться методом пневматичного розпилення. Заготівля з нанесеним на неї клеєм подається до місця технологічної витримки, час якої залежить від використовуваного клею і триває 30-60 хв, протягом яких при температурі 18-20 º С клейовий шар висихає. Технологічну витримку потрібно проводити в приміщенні, в яке потрапляє пил і яке обладнане вентиляцією.
Після витримки заготовки подаються на прес (найчастіше - вакуумний), де їх ламіновані. Процес ламінування складається з наступних операцій:
Лицьова матеріалу є великими від розмірів заготовки, тому після ламінування потрібно знімати звіси. Це можна робити прямо біля верстата його ж працівниками, або на окремій ділянці.
Після зняття звисів готові фасади очищають від пилу і інших забруднень і при необхідності упаковують.
Що впливає на якість фасадів
На якість ламінованих фасадів із MDF впливають такі чинники:
Вологість заготовки для вакуумної облицювання повинна становити 8-10%. Вища вологість заготовки призводить до її викривлення. Крім цього, під дією вакууму можливе накопичення вологи на робочому столі верстата і подальше її потрапляння в робочі частини, що може погіршити їх роботу.
Надлишкова вологість також знижує міцність приклеювання плівки до заготовки.
Процес ламінування пов'язаний з використанням високої температури - 110-140 º С, що призводить до випаровування вологи з заготовки. Волога випаровується, накопичується під плівкою, утворюючи пухирі різного розміру. При охолодженні заготовки з плівкою маленькі бульбашки розгладжуються самостійно, але плівка в цьому місці приклеєна вже неякісно. Пухирі, не розійшлися, можна проколювати і доклеювати по використанню фена, але це знижує якість і забирає багато часу.
Устаткування для фрезерування та особливості процесу
Зараз на нашому ринку представлений широкий асортимент обладнання для фрезерування частин заготовки, починаючи від простого, закінчуючи складним багатоопераційним обробляють центром. Вибирати є з чого, але щоб зробити правильний вибір, потрібно добре подумати і проаналізувати багато факторів.
Основним критерієм при виборі обробного центру повинна бути його продуктивність, яка залежить від таких факторів:
Лише після визначення необхідної продуктивності можна придбати певну модель обробного центру. Але не варто купувати центр з найбільшою продуктивністю, тому що велика продуктивність, тим вище його вартість. Обробний центр і вакуумний прес повинні бути підібрані так, щоб жоден з них не простоював і не був перевантаженим.
Процес фрезерування починається з розміщення заготовки на робочому столі. Щоб заготовка НЕ зміщалася, її потрібно надійно закріпити. Робиться це механічно (за допомогою гвинтових затискачів) або за допомогою вакуумних «присосок». Верстати з механічними затискачами дешевше, ніж верстати з вакуумними «присосками», але при кріпленні ними неможливо здійснити фрезерування по периметру.
У простих верстатах робочого інструмента замінюють вручну, що забирає багато часу. У більш складних заміну інструменту здійснює сам центр, вибираючи потрібний інструмент з відповідного магазіна.Но такі центри є більш складними в програмуванні.
Проблемою є те, що на фрезеровані поверхні утворюється ворс. Після нанесення клею внаслідок змочування ворс піднімається і орієнтується перпендикулярно до поверхні. Висихання клею закріплює ворс в такому положенні, тому на поверхні утворюються нерівності, помітні неозброєним оком.
Для зняття ворсу заготовку потрібно шліфувати, але ручна шліфовка порушує геометрії профілю, стає помітним після ламінування. На жаль, більшість виробників не приділяють цій проблемі належної уваги.
Більше десяти років тому в Німеччині був розроблений досить ефективний спосіб видалення ворсу з фрезерованому поверхні MDF. Його назвали Termoreibglaetten або вигладжування шляхом нагрівання тертям.
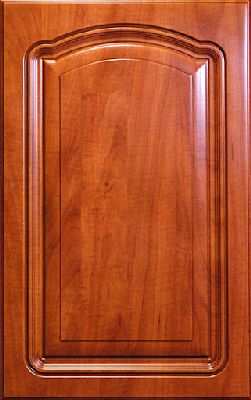
Цей спосіб полягає в тому, що при тому ж закріпленні заготовки вже сформований профіль обробляють гладким інструментом, який обертається. Цей інструмент повинен точно відповідати профілю фрези. В результаті тертя відбувається розплавлення лігніну, що міститься в волокнах деревини. Інструмент притискає ворс, який лігнін приклеює до фрезерованому поверхності.Недостаток цього методу - використання спеціального інструменту, профіль якого повинен точно повторювати профіль фрези.
Клей і його нанесення
Для вакуумної ламінування використовують одно- та двокомпонентні ПУ-дисперсії. Як затверджувач в двокомпонентних клеях використовують модифікований поліізоціанат, який додають в кількості 5% до ПУ-дисперсії. Клеї на основі ПУ-дисперсій активізують нагріванням. На сьогодні найбільше використовують такі марки клеїв: "Йовапур 150.00», «Йовапур 150.30», «Йовапур 150.50», «Супратерм 436», «Дорус ФД 144/1 ЛЗ», «Хенкель FD 144/6» і «Хенкель FD 150 / 6.
Одно-і двокомпонентні клеї добре наносити на MDF методом пневматичного розпилення. Перед нанесенням клею з заготівлі необхідно видалити пил. Наносять клею в два етапи: на першому етапі на фрезеровані поверхні заготовки і торці, а потім підсушується. На другому етапі клей рівномірно наносять на всю поверхню. Витрата клею на плоскі поверхні приблизно 50 г / м2, а на фрезеровані поверхні і торці - 100. 110 г / м2.
Після нанесення клей повинен висохнути. При температурі 18-20 ˚ С і в залежності від марки клею тривалість висихання - 30-60 хв. ЇЇ зменшують пропускаючи заготовки з нанесеним клеєм через сушильну камеру. Важливо, щоб температура в камері не перевищувала температури активації клею.
Плівка для ламінування
Для ламінування фасадів з MDF у вакуумних пресах використовують полімерні плівки - дуже еластичний матеріал з широким асортиментом декоративних, технологічних і експлуатаційних властивостей.
Серед полімерних плівок, використовуваних для ламінування, можна виділити наступні три основні групи:
Для забезпечення якості готового фасаду поверхню плівки покривають стійким до механічних пошкоджень лаком (акриловим або лаком УФ-сушіння. Хороша світлостійкість і можливість чищення гарантують отримання високих експлуатаційних показників.
ПЕТ плівки є альтернативою плівкам з ПВХ. Вони майже нічим не поступаються плівкам ПВХ в універсальності і простоті використання, але ПЕТ плівки дають кращий результат при виготовленні фасадів з високоглянцевого покриття. ПП плівки використовуються для виготовлення деталей з простим профілем.
Обладнання для ламінування
Ламінування фасадів з MDF можна здійснювати на декількох видах обладнання (рис. 1).
Мал. 1. Обладнання для ламінування фасадів з MDF
Процес ламінування з допомогою еластичної подушки можна здійснювати в одно- або багатоповерховому пресі для гарячого пресування. У проміжок між плитами преса встановлюють еластичну подушку, на яку вкладають заготовку з плівкою (плівкою до безпеки). Після цього відбувається процес ламінування. Недоліком еластичною подушки є те, що вона не здатна повторювати малих радіусів заокруглень.
Як мембранний, так і без мембранний прес дозволяє ламінувати заготовки зі складним профілем - саме в цьому і полягає їхня перевага над еластичною подушкою. У мембранному пресі для забезпечення герметичності і притиснення плівки до заготовки використовують еластичну мембрану. Це дозволяє одночасно ламінувати декілька заготовок плівками різного кольору.
У без мембранном вакуумному пресі полімерна плівка є одночасно облицювальний матеріал і мембраною. Перевагою такого преса є те, що не потрібно витрачати додаткові кошти на придбання мембрани.
Як відбувається процес ламінування
Ламінування досить відповідальний процес і при порушенні технології брак неминучий. Щоб звести кількість браку до мінімуму потрібно дотримуватися певних вимог.
Щоб якісно заклеїти торці заготовку потрібно встановлювати на підкладку. Товщина підкладки залежить від еластичності плівки і становить 10-18 мм. Розміри підкладки повинні бути менше розмірів заготовки на 2-4 мм. При більшій різниці розмірів плівка розірветься. Підкладка може бути масивної або гратчастої конструкції, але слід враховувати те, що при відстані між сусідніми опорами більше 250-300 мм заготовка може ламатися.
Слід враховувати і те, що відстань між сусідніми заготовками, а також між заготівлею і краєм стола не повинна бути менше ніж 80-100 мм.
Перед тим, як покласти заготовку на стіл вакуумного преса, її потрібно очистити від сторонніх елементів. Після установки заготовок на столі відбувається затягування плівки і закриття притискної рамки або мембрани. Заготовки зі столом заїжджають в термокамеру де відбувається нагрівання до потрібної температури. При досягненні потрібного значення температури включають вакуум і проходить процес обгортання заготовки плівкою. В такому стані заготовки витримують в камері протягом 2-2,5 хв. Після цього стіл виїжджає з камери і заготовки протягом 2-3 хв. дозріває при включеному вакуумі.
Після обробки заготовки знімають зі столу вакуумного верстата і обрізають залишки плівки (зняття звисів).