Склопакети вже досить довго є оптимальним варіантом заповнення будь-яких типів профілів для скління вікон, балконів, дверей: алюмінієвих, пластикових, дерев'яних. Від якості склопакета безпосередньо залежить якість готових вікон або дверей, тому технологія виготовлення склопакета відіграє значну роль при його виробництві. Будь-яке відхилення від прийнятої технології може спричинити за собою такі наслідки, як повне порушення роботи готової конструкції вікна або скляних дверей.
ХХI століття - століття автоматизації виробництва. Як і багато інших, виробництво склопакетів на сьогоднішній день також є практично повністю автоматизованим. Десятки робітників, які раніше брали участь в процесі виготовлення склопакетів, можуть бути замінені одним-двома робітниками, які подають спеціально підготовлене скло для подальшої роботи автоматів, і вивантажують готові склопакети. Лінія виробництва склопакетів, яка випускає готову продукцію, підрозділяється на кілька відділів, де проходять певні етапи. Підготовлене скло проходить 5 стадій для того, щоб стати склопакетом. Якість обробки скла на кожній стадії є запорукою якості готового склопакета.
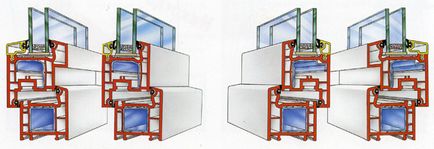
Перша стадія виготовлення склопакета - різка скла.
На цьому етапі цілісний лист підготовленого скла проходить різання. Для цього використовуються спеціальні резочние столи і інструменти, які змінюються в залежності від типорозміру попередньої заготовки для склопакета. Залежно від необхідного результату, підбирається вид інструменту для різання, а також рідина, за допомогою якої вона буде проведена. Якщо раніше ці процеси виконували робочі, то сучасне обладнання для різання є повністю механізованим, система управління процесом закладена в комп'ютер. Завдяки новітнім технологіям виготовлення обладнання для розрізання скла, стає можливим проводити найбільш вигідний розкрій, економлячи при цьому значна кількість матеріалу. Підготовлене для розрізання скло переміщається по столу на повітряній подушці, що дозволяє гарантувати його повну безпеку в процесі виробництва. Після здійснення розрізу скло ламається за допомогою металевих стрижнів, які розташовуються в поверхні столу. Проте, при будь-якому розрізі з подальшим розломом в склі утворюються невидимі оку мікротріщини. Уздовж лінії, яка проведена резочним обладнанням, проводиться розлом і скло розколюється. Рівні краї розлому є неодмінною умовою технології, для чого розлом повинен бути проведений практично одночасно з розрізом підготовленого скла. Така умова є наслідком здатності скла до «самозаліку». Самозалічування скла відбувається таким чином: після утворення мікротріщин, вони склеюються, в результаті чого здійснити рівний розлом скла практично неможливо. Саме для того, щоб запобігти цьому явищу, інструмент вводить на поверхню поперетинали скла спеціальну рідину, яка не дає склу «самозалечіваться». Рідина для різання скла повинна мати незначну в'язкість і хороші зволожуючі властивості.
Разом з розрізанням скла, відбувається ще один процес, який готує скло до наступних етапів. Це різка спейсеров (дистанційні рамки) відповідно до типорозміром даного виду склопакета, а також їх з'єднання за допомогою особливих куточків і вставок. З внутрішньої сторони скла в склопакеті спейсери повинні мати пробиті перфоратором отвори. Простір дистанційної рамки повинно бути наповнене осушувачем повітря, який стоятиме на перешкоді утворенню вологи всередині склопакета. Згідно зі стандартами, поглиначем в цьому випадку виступає молекулярне сито (цеоліт, що має форму гранул) або силікатний гель. Такими осушувачами повинні бути заповнені всі порожні місця спейсеров, при чому розмір гранул поглинача вологи повинен бути більше розміру отворів для дегидрации внутрішнього простору склопакета. Поглинач повинен володіти такими властивостями, які дозволять йому здійснювати вибіркове поглинання газів. Необхідно, щоб поглиналися виключно молекули води, а не молекули інших газів, які є складовими повітря. У якісних склопакетах, саме поглинач вологи перешкоджає утворенню конденсату в камері склопакета. Якщо готовий склопакет допускає освіту вологи на стеклах, це означає порушення технології виготовлення та наявність шлюбу.
Однак при порушенні температурного режиму, в якому повинна здійснюватися експлуатація склопакета, можливе утворення конденсату на склі при досягненні так званої «точки роси». «Точка роси» - це момент, коли поглинач вологи склопакета вже не може впоратися з кількістю вологого повітря усередині склопакета, що відбувається в результаті порушення температурного балансу, і утворюється конденсат. Температура повітря, яка викликає появу конденсату для більшої частини склопакетів - - 45С. Для регіонів, в яких температура часто опускається нижче наведеної позначки, існують спеціальні морозостійкі склопакети, які витримують температури аж до -55С.
Тип склопакета відіграє вирішальну роль і при обсязі заповнення дистанційної рамки або спейсера. Як правило, супутня документація по технології вказує більш точні цифри, але як мінімум це 50% від загального обсягу спейсера. Виготовляється дистанційна рамка з металевого профілю або стрічки: алюмінієвого, сталевого. При виготовленні сталевого профілю для дистанційних рамок, відбувається додаткова обробка профілю або стрічки антикорозійним покриттям. Проте, виготовлення спейсеров з інших матеріалів також можливо, за тієї умови, що загальні вимоги і стандарти будуть дотримані.
Для того щоб підвищити теплоізоляційні характеристики склопакета, найчастіше використовуються спейсери з тепловим розривом. Технологія установки дистанційних рамок TPS є однією з останніх розробок і дозволяє значно підвищити рівень теплоізоляції склопакета. При цьому спейсери виготовляються не з металевого профілю, а з бутилкаучуку. Стрічка з цього матеріалу істотно знижує проникнення холодного повітря. Недоліками бутилкаучуку є його зовнішній вигляд і необхідність контролю вологопоглинання. Склопакет, дистанційні рамки якого виготовлені за технологією TPS, має деякі затримки в поглинанні вологи проникаючої в склопакет, проте при довгому часу використання віконної конструкції, це грає не таку значну роль.
Друга стадія виготовлення склопакета - мийка скла.
На цьому етапі проводиться миття розрізаного і підготовленого скла за допомогою спеціальних щіточок, розташованих усередині мийної машини. Для миття скла використовують демінералізовану воду. Для того щоб мийка не принесла поверхні скла ніяких пошкоджень, необхідно використовувати щетинки строго певної жорсткості. Багато характеристики майбутнього склопакета залежать від правильного твори стадії мийки підготовленого скла. Раніше мийка проводилася вручну, що значно погіршувало його якість. При проведенні миття скла не рекомендується застосування миючих засобів. Одним з головних умов якісного склопакета є щільне старанність герметика до поверхні скла, а мийка вручну порушує герметичність покриття і відповідно позбавляє склопакет його високих характеристик.
Третя стадія виготовлення склопакета - нанесення герметика.
Після миття скла, на спейсерние заготовки наноситься первинний шар герметика. Дистанційні рамки з'єднуються один з одним за допомогою куточків з металу або пластику, і на їх поперечні сторони наноситься шаром в декілька міліметрів (мінімум 3 мм) спеціальне покриття з герметика. У вигляді герметиків на сьогоднішній день використовуються бутилен. Існують певні стандарти, при порушенні яких відбувається передчасний вихід склопакета з ладу або невідповідність його характеристик заявленим. Герметичний шар повинен бути строго рівномірний, не мати порожніх проміжків і ширину не менше 3 мм. Якщо виробництво склопакетів має обмежені розміри, допускається ручне нанесення герметика (як і в разі ремонту склопакета, який може бути викликаний порушеннями в технології при його виробництві).
Четверта стадія виготовлення склопакета - первинна збірка.
Після того, як на спейсери нанесено герметичне бутилове покриття, проводиться попередня збірка склопакета, яка включає в себе прикріплення підготовлених і очищених стекол з дистанційними рамками, на які нанесено герметичний шар. Колір бутилового покриття на цій стадії повинен бути ідеально чорним. Якщо ж на покритті виявляються білі сліди, то це означає, що покриття чіпали руками (при ручному покритті бутиловой стрічкою, роботи повинні бути проведені в спеціально призначених для цих цілей рукавичках) або скло не було достатньо вимито. Технологія передбачає так зване «м'яке» покриття поверхні скла, яке є нестійким до впливів зовнішнього середовища. Поверхня скла з «м'яким» покриттям є тією стороною, яка знаходиться всередині камери склопакета. Необхідно, щоб ще на стадії різання скла поверхню, на яку буде нанесено бутилове покриття, була ідеально очищена від «м'якого» покриття для щільного старанності бутила до скла, що забезпечить повну герметизацію, а також не зашкодить поверхні скла. При цьому із зовнішнього боку склопакета очищена поверхня повинна бути невидима, щоб зовнішній вигляд склопакета не погіршувався.
Після того, як проведена попередня збірка, склопакет відправляється під прес, який стискає його для остаточної фіксації. Під пресом склопакет повинен знаходиться деякий час для того, щоб бутилове покриття проникло в верхній шар поверхні скла для забезпечення надійної герметизації.
Як правило, для того, щоб склопакет не зруйнувався в процесі складання і монтажу, перед первинною стадією збірки, виробляють шліфування країв скла.
П'ята стадія виготовлення склопакета - завершальна.
Після обробки склопакета пресом, проводиться покриття бокових частин склопакета другим шаром герметика, який призначений для точного збереження первинної геометрії склопакета під час його подальшої експлуатації. Для цього використовуються поліуретанові, силіконові або тіоколової герметики. При цьому, температура у виробничому приміщенні, де виготовляються склопакети, повинна бути не нижче + 16С і не вище + 25С; вологість повітря не вище 50%.
Завдяки якісному виготовленню склопакетів, без порушення технології і стандартів, ми отримуємо дійсно відмінний продукт, який доповнює і покращує характеристики віконного профілю. При установці високоякісних склопакетів, Ваші пластикові вікна будуть відмінно захищати приміщення від холоду і шуму, а також служити чудовою прикрасою будинку. Адже скла - це відображення зовнішнього світу, і якими будуть вони, таким Ви будете бачити світ, який Вас оточує.