Розглянуто технологічні прийоми при визначенні дефектів і способи ремонту шпинделів металорізального обладнання. Особлива увага приділяється збереженню початкових виконавчих розмірів, так як їх зміна може зажадати переробки технологічної оснастки, що призведе до економічної недоцільності відновлення.
Шпиндель є однією з найвідповідальніших деталей металообробних верстатів. Від точності і жорсткості шпинделя, а також точності заданого руху багато в чому залежить якість виконуваних на верстаті операцій і виготовлених деталей. В процесі експлуатації верстата поверхні шпинделя в результаті дії ряду факторів зношуються. Відхилення розмірів і відхилення від правильної геометричної форми допускаються в дуже вузькому діапазоні. Це визначає специфіку ремонту шпинделів. Виготовлення нового шпинделя є складним і дорогим процесом. У тих випадках, коли його ремонт тягне за собою також ремонт або виготовлення нових, сполучаються з ним деталей, заміна зношеного шпинделя новим може виявитися більш економічною. Це питання слід вирішувати зіставленням вартостей виконання ремонтних робіт і виготовлення нового шпинделя. У більшості випадків виявляється доцільним виконувати ремонт шпинделів [1].
Шпинделі на кінці мають конічні отвори з різьбленням, посадочні шийки або конуси для базування технологічної оснастки. Якщо при виконанні ремонту змінити розміри виконавчих поверхонь шпинделя, то це зажадає переробки додається до верстата технологічного оснащення, що економічно невигідно. Тому при ремонті шпинделя прагнуть відновити початкові розміри його поверхонь, особливо це відноситься до його виконавчим поверхням.
Для відновлення шпинделя необхідно вибрати найбільш раціональний метод, наприклад: механічну обробку (спосіб ремонтних розмірів), установку компенсаторів зносу, гальванічне покриття і ін. Вибір способу відновлення поверхонь шпинделя визначається величиною їх зносу [2].
Механічною обробкою відновлюють геометричну точність зношеної поверхні: знімають з неї мінімальний шар металу (гострінням, шліфуванням, притиранням) до видалення слідів зносу (без збереження номінальних розмірів), забезпечуючи регламентну точність і параметр шорсткості нового шпинделя [3]. Механічну обробку використовують не тільки як самостійний спосіб ремонту, але і як допоміжну операцію при виконанні наплавлення, металізації, хромування.
До шпинделям пред'являють особливо високі точності вимоги: допустимі відхилення від співвісності і циліндричної посадочних шийок ≤ 0,005 мм; переднє і заднє конічні отвори повинні бути концентричні посадковим шийок, що допускається биття 0,01 ÷ 0,02 мм на 300 мм довжини [4, 5].
Підготовку, наприклад, полого шпинделя до проведення ремонту механічної обробкою виконують наступним чином. Спочатку визначають незношених поверхні з метою їх використання в якості баз для центрування деталі, здійснюваної установкою спеціальних технологічних пробок. Ця операція вимагає точного виконання. Вона багато в чому визначає якість ремонту. Перед установкою пробок контролюють стан отворів на кінцях шпинделя: їх зачищають від подряпин і забоїн, перевіряють на фарбу за допомогою контрольних пробок (відбитки фарби повинні покривати не менше 70% площі поверхні отвору, контактіруемие з поверхнею пробки); при необхідності отвори доводять гострінням, шліфуванням або притиранням. Пробка 3 (рис. 1) має різьбову частину, на неї нагвинчують гайку (на рис. 1 не показана), за допомогою якої випрессовивают пробку, не пошкоджуючи отвори шпинделя [1].
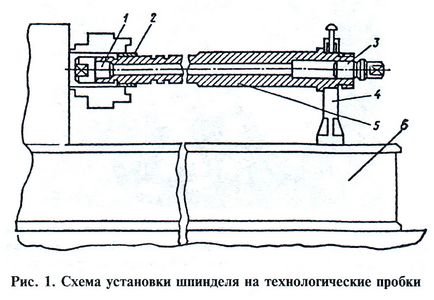
Центрування шпинделя 5 (див. Рис. 1) виконують в такій послідовності: заготовку 2 розрізний цапфи встановлюють і затискають в патроні, розточують в цапфі отвір згідно діаметральному розміром хвостовика шпинделя, що підлягає ремонту; шпиндель одним кінцем встановлюють в цапфу, а передній шийкою в люнет 4; за допомогою сухарів люнета контролюють за індикатором положення шпинделя (допуск биття 0,01 мм); остаточно затискають розрізну цапфу і здійснюють центрування передній технологічної пробки 3 (свердлять і розгортають центровий отвір); знімають шпиндель з верстата 6; растачивают додатково цапфу згідно діаметральному розміром передньої базової поверхні; знову встановлюють шпиндель на верстат і закріплюють в цапфі передній його кінець, а хвостовик розташовують в люнете; додатково вивіряють положення шпинделя за допомогою сухарів люнета; здійснюють центрування другої технологічної пробки 1. Центрові отвори, виконані в технологічних пробках 1, 3, використовують в якості технологічних баз при проведенні ремонтних операцій, зазначених у технологічній маршрутній карті.
Одним із способів відновлення зношених поверхонь шпинделя є застосування тонкостінних компенсаційних кілець і втулок, які встановлюють на епоксидний клей. Ремонтна практика показує, що термін служби таких шпинделів довше, а в деяких випадках і працюють вони краще, ніж нові, якщо компенсаційні кільця і втулки виконані з матеріалів, що володіють більш високими експлуатаційними властивостями, ніж основний матеріал шпинделя [2].
Для установки компенсаційних кілець або втулок зі зношеною поверхні видаляють шар металу (механічною обробкою) з метою посадки деталі-компенсатора з номінальним розміром або збільшеним ремонтним розміром відновлюваної поверхні. Знімається шар металу повинен бути мінімальним: не більше 10 ÷ 15% номінального діаметрального розміру суцільного перетину вала або товщини стінки полого шпинделя.
Для відновлення поверхні шийки шпинделя під підшипник кочення (нерухома посадка) компенсаційне кільце може бути тонкостінних (0,5 ÷ 2 мм), а при відновленні поверхні шийки цієї деталі під підшипник ковзання його товщина повинна бути не менше 2,5 мм. Тонкостінні компенсаційні кільця виготовляють з того ж матеріалу, що і ремонтується шпиндель, або з матеріалу, що відповідає підвищеним вимогам по зносостійкості. Внутрішній діаметральний розмір поверхні виконують за місцем з зазором 0,04 ÷ 0,05 мм, параметр шорсткості Ra 20, а зовнішній - з припуском 3 ÷ 5 мм. Компенсаційне кільце встановлюють на епоксидний клей. Остаточну обробку виконують через 24 годин після затвердіння клею з рясним охолодженням.
Компенсаційні втулки з товщиною стінки 2,5 ÷ 3,5 мм і більше виготовляють з цементованої стали. Діаметральний розмір відновлюваної поверхні (внутрішньої) втулки виконують з припуском 0,2 ÷ 0,3 мм, а діаметральний розмір її поверхні, що сполучається з поверхнею шпинделя, - з припуском 3 ÷ 4 мм. Цю поверхню цементують, потім знімають з неї науглероженного шар металу і гартують втулку до HRCЕ 50 ÷ 68. Внутрішню поверхню шпинделя обробляють, готуючи до установки втулки. Незагартованим зовнішню поверхню останньої обробляють за розміром підготовленій поверхні шпинделя з діаметральним зазором 0,05 мм (шорсткість поверхні Ra 20). Втулку встановлюють в отвір шпинделя на епоксидний клей. Загартовану поверхню втулки шліфують остаточно після затвердіння клею.
Схеми установки компенсаційних кілець і втулок на епоксидний клей при ремонті шпинделів верстатів показані на рис. 2. У шпинделя токарного верстата за допомогою кільця 1 відновлена шийка (рис. 2, а) під підшипник кочення, кільця 2 - опорна загартована поверхня під підшипник ковзання, кільця 3 - конічна поверхня, що служить для установки патрона.
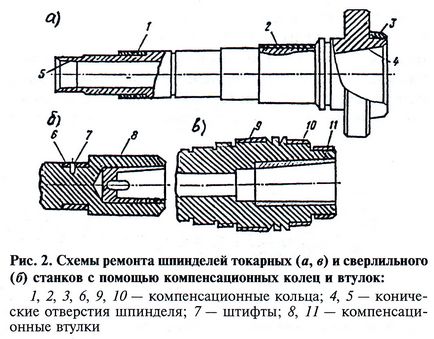
Шейки шпинделя дриля (рис. 2, б) відновлені за допомогою тонкостінного кільця (товщина менше 1 мм) 6 і втулки 8. Кільце 6 виконано з двох півкілець, які зафіксовані двома штифтами 7, поставленими на епоксидний клей. Також за допомогою кільця 9 (рис. 2, в) відновлена конічна поверхню під роликовий підшипник, кільця 10 - поверхня під патрон. Конічний отвір шпинделя відновлено за допомогою втулки 11 з загартованої внутрішньою поверхнею.
При фінішній механічній обробці компенсаційних кілець і втулок можна допускати перегріву, так як може зруйнуватися клейова плівка. Тому операцію слід виконувати з рясним охолодженням.
Шпинделі, що мають знос шийок на сторону 0,005 ÷ 5-0,01 мм, ремонтують притиранням на токарному верстаті. Притирання здійснюють спеціальним інструментом - жімком (рис. 3). Він складається з кільця-хомутика 1, гвинта 2, розрізний втулки-притиру 3 і рукоятки-державки (на малюнку не показана). Втулку-притир виготовляють з чавуну, міді або бронзи, а отвір в ній виконують за розміром відновлюваної шийки шпинделя 4. На оброблювану поверхню накладають тонкий шар суміші, що складається з дрібного наждачного порошку і масла. Після цього одягають жімок і злегка загвинчують гвинт 2. Токарний верстат налаштовують на частоту обертання, при якій швидкість різання знаходиться в межах 10 ÷ 20 м / хв. Вмикають верстат і рівномірно переміщають жімок уздовж оброблюваної поверхні шийки шпинделя. Оновлюють час від часу шар притирочное суміші і підтягують гвинт 2. Усунувши знос, промивають шийку і притир гасом. Потім наносять на шию тонкий шар доводочной пасти з гасом і таким же чином закінчують обробку.
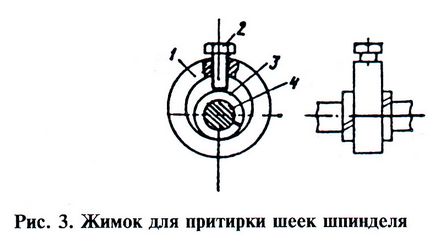
Якщо знос шийок шпинделя перевищує 0,01 мм на сторону, то їх ремонтують тонким шліфуванням з наступною притиранням під ремонтний розмір. Однак такий спосіб ремонту може бути використаний лише тоді, коли є можливість змінити відповідно діаметральні розміри отворів в підшипниках або інших деталях, які сполучаються з шпинделем.
При зносі основних поверхонь шпинделів до 0,05 мм на сторону спочатку виконують їх попереднє шліфування для відновлення точності геометричної форми поверхонь. Потім здійснюють їх хромування - електролітичне нанесення хромового покриття. Цей процес заснований на властивості деяких металів осідати під дією електричного струму з розчинів їх солей (електролітів) на поверхню металевих деталей у вигляді щільного шару. Процес хромування є трудомістким, тривалим і дорогим. Для осадження шару хрому товщиною 0,1 мм витрачається 6 ÷ 15 год. Хромове електролітичне покриття має високу твердість (HRCЕ 65), низьким коефіцієнтом тертя, підвищеною опірністю до зносу. Висока твердість електролітичного хрому обумовлена спотворенням кристалічної решітки, що викликається внутрішньою напругою і впровадженням водню. Недоліком цього способу відновлення є відшаровування покриття. Зі збільшенням товщини його міцність зменшується. Після хромування з поверхні шліфуванням знімають шар до 0,03 мм на сторону. Максимально допустима товщина шару хрому після шліфування для поверхонь ковзання шпинделя не повинна перевищувати 0,12 мм - при тиску ≤ 50 МПа; 0,05 ÷ 0,1 мм - при тиску 50 ÷ 200 МПа; 0,03 мм - при тиску, що перевищує 200 МПа, і динамічному навантаженні з нагріванням.
При зносі більше 0,05 мм на сторону здійснюють нарощування поверхонь металом одним з відомих способів, наприклад вибродуговой наплавленням, потім проводять механічну обробку [6].
При шліфуванні шийок шпинделя їм надають у напрямку до заднього кінця шпинделя кону- доцільність до 0,01 мм, щоб при шабруванні підшипників шар фарби, нанесений на шиї, повністю використовувався для зафарбовування поверхні підшипників. Конічні отвори на кінцях шпинделів при відновленні зазвичай шліфують, потім по конусному калібру підрізають торці. Торець фланця на кінці шпинделя після відновлення конусної посадочної шийки також підрізають.
При відновленні конічного отвору шпинделя механічну обробку його поверхні можна здійснювати за допомогою спеціальних пристосувань, не знімаючи шпинделя з верстата. Це забезпечує точне центрування осі конічного отвору шпинделя з віссю його обертання.
Для контролю точності відновленого конічного отвору шпинделя використовують стандартний конусний калібр, контрольна ризику на якому не повинна входити в отвір. Між рискою і торцем шпинделя має бути відстань 1 ÷ 2 мм. Биття осі цього отвору перевіряють індикатором по контрольної оправці, вставленої в отвір.
На рис. 4 для прикладу показаний ремонтний креслення шпинделя токарного верстата, а в таблиці - технологічний процес його ремонту з урахуванням даних, визначених під час перевірки. Знос поверхні 1 [М48] х 1,5 - 0,4 мм на сторону. Поверхня 2 - Ø49,96 мм [Ø50кб]; поверхню 3 - Ø59,95 мм [Ø60 кб]; на поверхні 4 - [М64] х 6 - різьблення зам'яли на 0,25 мм на сторону. Поверхня 5 - Ø74,97 мм [Ø75кб]; поверхню 6 - Ø69,87 мм [Ø70 кб]; на поверхні 7 - [М68] х 2 - різьблення зам'яли на 0,3 мм на сторону; на поверхні 8 - Надир і забоїни до 0,75 мм. Поверхні 10 і 11 - 6,07 мм - [6js6], Биття поверхні 2 [Ø50кб] становить 0,035 мм, поверхні 6 [Ø70кб] - 0,055 мм, буртика поверхні 6 - 0,05 мм. У квадратних дужках дані номінальні розміри шпинделя (до зносу) [4].
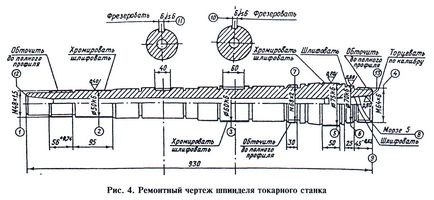
Для ремонту шпинделя (див. Рис. 4) використовують токарно-гвинторізний, вертикально-фрезерний, круглошліфувальний верстати, верстак з слюсарними лещатами і гальванічну ванну, а також відповідну технологічну оснастку, до складу якої входить: четирехкулачковиі і повідковий патрони, нерухомий люнет, верстатні гвинтові трикулачні лещата, пристосування для внутрішнього шліфування, оправлення установки шпинделя, гайкові ключі, токарні центри, мідні підкладки, хомутик, прохідний відігнутий, розточний і різьбовій різці, кінцева фрез , Шліфувальний круг ПП х 400 х 40 х 127 - Е5 - К, пробка шпонкова 6,5js6, штангенциркуль, мікрометр важільний, індикатор, конусний калібр (Морзе 5).
При ремонті шпинделів різьблення зазвичай прорізають до повного профілю, нестандартні гайки до них виготовляють заново.
Для запобігання деформацій шпинделів їх слід поміщати вертикально в спеціальні стелажі.
Технологічна послідовність ремонту шпинделя