Змочуваність молібденового покриття серебросо - тримають припоями незначна. Для поліпшення змочуваності на нанесений тим чи іншим способом шар молібденового покриття наносять шар нікелевого покриття. Нікель сприяє гарному розтіканню припоев. Нікелеве покриття товщиною 10-15 мкм на-носять гальванічним шляхом на молібденовий шар, що покриває кераміку, з подальшим вжіганіем. Ні-келевое покриття вжігается в водневих печах при 980 ° С.
Підготовлені керамічні деталі з двошаровим покриттям після відповідної оправ-ки і очищення споюють з металевими частинами аппа - ратури. Для цього використовують тверді припої, головним чином срібло (/ Пл = 961 ° С) або його сплави з більш низькою температурою плавлення. В якості припою застосовують евтектики «мідь - срібло», наприклад, наступного складу: Ag -28,5%, Сі - 71,5% " '. Темпера-тура її плавлення 779 ° С. Металокерамічні спаи для електровакуумної апаратури повинні витримувати-вать температуру не нижче 450 ° с без порушення вакуум - щільності, що відповідає температурі, при якій відкачують прилади. Кераміку з металом споюють в електричних печах в атмосфері водню і азоту при 1030 ± 10 ° с (при пайку сріблом) або 820-830 ° с при пайку сплавом Ag-Сі. Багатоступінчаста технологія споювання закінчується прове ркой якості спайки металу з керамікою.
Нарівні з багатоступеневою технологією разработа-на одноступенева технологія спайки кераміки з ак-тивними металами Ti, Zr, яка отримала назву «термокомпрессіонной сварка». Сутність / цієї техноло-гии полягає в тому, що спай утворюється за одну опе-рацію без попередньої металізації молібденом і покриття 'другим шаром нікелю в результаті взаємодії-дії між твердими фазами. Сварка відбувається під тиском до 20-30 МПа і при одночасному на-нагріванні до 1000 ° С. Однак область застосування Термоком-прессіонной зварювання істотно обмежена. Отримувати вакуумно-щільні спаи можна тільки при повному злагоди-ження коефіцієнтів розширення активного метал-ла і кераміки в усьому діапазоні температур, починаючи від температури затвердіння припою до кімнатної. Зокрема, хороші результати дає спай титану з фор - стерітовой керамікою, коефіцієнт лінійного розширенням-ня яких майже повністю збігається і становить 9-9,5-10
6. В якості припою для спайки кераміки з титаном використовують евтектичних сплав з температу-рій плавлення 779 ° С, чисті нікель і мідь, з котори-ми титан утворює легкоплавкіевтектики, маю-щие температуру плавлення 970-1000 ° С. Титан з кер-Мікою паяють в колпакових вакуумних печах, в яких підтримують вакуум не нижче 1 СПА.
Третій вид металізації технологічно найбільш складний, так як вимоги до розміру нанесеного шару досить жорсткі. Товщина шару близько 1 мкм, а іноді і менше, а ширина шару іноді не перевищує 1 мкм. На-несення таких тонких плівок з точним дотриманням за-
даних розмірів здійснюють шляхом нанесення на по-поверхню виробу у вакуумі атомів 'металу шляхом їх конденсації. Застосовують також методи плазмового і дугового напилення в спеціальних установках предва-редньо обпаленої кераміки. Тонкоплівкова метал-ція вимагає досить високого ступеня чистоти поверх-ності вироби, абсолютної очистки від адсорбованих парів води та інших речовин, підігріву підкладок до 250-400 ° С. Тонкоплівкові покриття наносять без вжи - ганія, а зв'язок кераміки з напиленням металом носить адгезійний характер.
При дифузійному зварюванні з використанням титану в якості активного металу, так само як і при багато-ступінчастою технології, утворюється перехідний шар між титаном і керамікою. Утворення цього щільного і міцного шару обумовлено тим, що титан окислюється до оксиду, який вступає у взаємодію з окси-дами, що знаходяться в кераміці. В результаті возника-ет багатокомпонентна склоподібна фаза> яка і являє собою перехідний шар.
§ 10. Механічна обробка
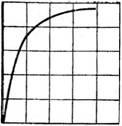
2 Л 6 в 10 Мікротвердість HV ID Г Па
Мал. 26. Кореляція між мікротвердістю і твердістю по Моосу
Мал. 27. Стадії механічної обробки кераміки
Механічна обробка кераміки - це Трудоем-кий і складний процес, мета якого - отримання через робів з високим ступенем точності. У деяких випад - "ях виробу необхідна механічна обробка, напри-мер перед металізацією тонким шаром. Деякі виро-лія, такі як корундові підкладки для інтег-ральних тонкоплівкових схем, 'мікроплати до етажерочних мо-дулею, деякі керамічні конденсатори, подшип-ники ковзання і багато деталей вакуумних приладів, вимагають додаткової механічної обробки, так як звичайними технологічними методами виготовити з -Делі високої точності не представляється можливим. У деяких випадках виникає необхідність додання виробу профільної форми з прецезіонного дотримані-ням усіх радіусів заокруглення, а також зі свердлінням отворів. В окремих випадках відхилення від заданно-го розміру не повинно перевищувати часток мікрометра. Сос-тояніе поверхні виробу оцінюється по її точності і чистоті. Встановлено 11 класів точності (ГОСТ 10336-80), які характеризують відповідність заданий-ним розмірам виробів, причому меншого по порядку класу відповідає більш точна обробка. Стан поверхні (шорсткість) оцінюється по ГОСТ 2789-73. Встановлено 14 класів чистоти поверхні. Стан поверхні визначається по еепрофілограм - ме, на якій відображаються нерівності, виступи, впадаючи-ни (пори), тріщини.
Механічна обробка кераміки може вироб-диться різними способами: різанням, шліфуванням, ультразвукової обробкою. Найбільш поширений-ний вид обробки - шліфування: плоске, кругле. торцеве, внутрішнє і т. д. Для шліфування кераміки можна використовувати різні абразивні матеріали, такі як природний і штучний корунд, карбід кремнію, карбід бору. Однак в даний час переважно використовують (як більш ефективний) штучний алмаз, в деяких випадках - кубічний нітрид бору (боразон, ельбор). Механічна обработ-ка, особливо шліфування, залежить від властивостей кераміки, таких як твердість, крихкість, міцність, пористість, стан поверхні, термостійкість, і від властивостей аб-разівного матеріалу і інструменту. Вона також залежить від швидкості знімання кераміки, притискає зусилля, ох-лажденія виробу, що шліфується і інших умов обра-лення.
Найважливіша властивість кераміки, що визначає її по-датлівость механічній обробці, - твердість. Суще ствует кілька методів оцінки твердості. Найбільш прийняті методи - це мінералогічна шкала Мооса і 'Мікротвердість. Керамічні матеріали мають тверд-дость по Моосу 6-9,5. Кореляція між твердістю по Моосу і мікротвердістю дана на рис. 26. Кераміку, твердість якої по Моосу менше (8 мікротвердість 150 МПа), з точки зору механічної обробки вус -ловно відносять до м'якої, а більше 8 (мікротвердість більше 150 МПа) -до твердої.
Важлива властивість кераміки - її крихкість, яку прийнято визначати як відношення опору зрушенню оСдв до опору на розрив Страз за формулою
X = ° СДВ / ° разів • де X - критерій крихкості.
Кераміка. у якій х> 1 [2], вважається крихкою. При шліфуванні крихкість, як ми побачимо далі, є корисною властивістю, і зі збільшенням крихкості умови шліфування поліпшуються. Механічна міцність ке-Рамик, як властивість до певної міри відображає щільність, мікро - і макроструктури, розподіл фаз, ступінь кристалізації, розподіл пір, суттєво-но впливає на процес шліфування. Пористість кераміки погіршує стан її поверхні і знижує клас чи-простоти. Термічна стійкість кераміки повинна бути така, щоб при її розігріві в процесі шліфування вона не руйнувалася.
Механічну обробку кераміки шляхом шліфув-ня виконують в три стадії: чорнова, чистова і до-горілчана (рис. 27). Ці стадії відрізняються кількістю сошлифовать кераміки і станом її поверхні (табл. 9). На першій стадії сошліфовивать до 80% підлягає видаленню матеріалу, причому обробка ведеться на підвищених швидкостях грубозернистим інструментом, в результаті чого на поверхні осту-ються глибокі ризики і відколи. Припуск в розмірі деталі може становити 0,3-0,5 мм, буває одне - і двусторон-ним і залежить від розмірів деталі. На другій стадії шліфування обсяг обшліфувати матеріалу зменшується, шорсткість поверхні також зменшується, так як друга стадія обробки ведеться абразивним інструментом з більш дрібним зерном. Нарешті, третя стадія - доведення до номінального розміру - зазвичай проводиться шліфувальними алмазними порошками (пастами) потрібної зернистості. Стадію доведення отож-дествляют з поліруванням, при якій досягається клас точності 1-3.
У процесі шліфування руйнується і ізнашіва-
Таблиця 9. Стадії алмазного шліфування кераміки