Сутність лиття по виплавлюваних моделях полягає в використанні точної нероз'ємною разової моделі, по якій з рідких формувальних сумішей виготовляється нероз'ємна кераміки-чна оболонкові форми; перед заливкою розплаву модель уда-ляется з форми виплавленням, випалюванням, розчиненням або випаровуванням; для видалення залишків моделі і зміцнення форма може бути нагріта до високих температур, що покращує її заповнюваність розплавом.
Основні операції технологічного процесу.
Модель або ланка моделей виготовляють в рознімної прес-формі, робоча порожнину якої має конфігурацію виливка з припусками на усадку та оброблення різанням (рис. 1 а). Модель виготовляють з матеріалів, що мають невисоку температуру плавлення (віск, стеарин, парафін), здатних розчинятися (карбамід) або згор-рать без утворення твердих залишків (полістирол). Готові моделі або ланки моделей збирають в блоки (рис. 1. б) мають моделі елементів ливникової системи з того ж ма-териала, що і модель. Блок моделей складається з ланок, централь-ва частина яких утворює моделі живильників і стояка. Моделі чаші і нижньої частини стояка виготовляють окремо і встанов-ють в блок при його складанні. Блок моделей занурюють в ємність з рідкою формувальної сумішшю - суспензією для обо-лочкових форм, що складається з пилоподібного вогнетривкого ма-ла, наприклад кварцу пилоподібного або електрокорунду, і зв'язок-ного.
В результаті на поверхні моделі утворюється тонкий (менше 1 мм) шар суспензії. Для зміцнення цього шару, збільшення його товщини на нього наносять шари вогнетривкого зернистого матеріалу (дрібний кварцовий пісок, електрокорунд, зернистий шамот). Операції нанесення суспензії і обсипання повторюють до отримання на моделі оболонки необхідної товщини (3-10 шарів).
Кожен шар покриття висушують на повітрі або в парах аміаку 6, що залежить від сполучного. Після сушіння оболонкової форми модель видаляють з неї виплавленням, розчиненням, випалюванням або випаровуванням.
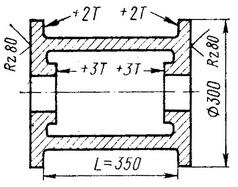
Мал. 1 а. Конфігурація виливки з припусками на усадку та оброблення різанням.
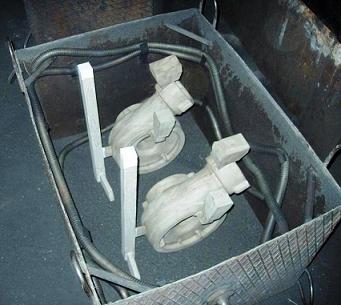
Мал. 1 б. Готові моделі.
Так отримують багатошарову оболонкову форму по виплавленої моделі. Для зміцнення перед заливкою оболоч-ковую форму поміщають в металевий контейнер і засипають вогнетривким матеріалом <5 (кварцевым песком, мелким боем ис-пользованных оболочковых форм). Для удаления остатков моделей из формы и упрочнения связующего контейнера с оболочковой формой помещают в печь 9 для прокаливания. Форму прокаливают при температуре 1223—1273 К. Прокаленную форму извлекают из печи и заливают расплавом.
Після затвердіння і охолодження виливки до за даної температури форму вибивають, виливки очищають від залишків кераміки і відрізають від них літники.
У багатьох випадках оболонки прожарюють в печі до засипки вогнетривким матеріалом, а потім для зміцнення їх засипають попередньо нагрітим вогнетривким матеріалом. Це дозволяє скоротити тривалість прожарювання форми перед за-лівкой.
Мала шорсткість поверхні форми при досить високій вогнетривкості і хімічної інертності матеріалу позво-ляет отримувати отлізкі з поверхнею високої якості.
Після очищення виливків від залишків оболонкової форми Шеро-Ховатія їх поверхні характеризується величиною Rz = 40 мкм, а в окремих випадках досягає Ra-2,5 мкм.
Відсутність операцій роз'єму моделей і форми, використання для виготовлення моделей матеріалів, що дозволяють не розбирати форму при видаленні моделі, висока вогнетривкість матеріалів форми, слід нагріти до високих температур перед заливкою, що послабшають шает заповнюваність, дають можливість отримати виливки складність нейшей конфігурації максимально наближаються до конфігу-рації готової деталі практично з будь-яких сплавів. Коеффіці-ент точності виливків по масі (КТМ) може досягати 0,85-95, що різко скорочує обсяги обробки різанням, відходи металу в стружку.
Точність отлівск відповідає 8-11-му квалітетами СТ РЕВ 145, а припуски на обробку різанням для виливків розміром до 50 мм складають близько 1,4 мм, а розміром до 500 мм - близько 3,5 мм. Тому лиття по виплавлюваних моделях відноситься до прогресивних матеріалу-і трудосберега-ющим технологічних процесів обробки металів.
Короткі історичні відомості. Прообразом сучасного процесу лиття по виплавлюваних моделях є лиття по воскових моделях, відоме в глиб-кой давнини. Уже в стародавньому Елам і Вавилон близько 4 тис. Років тому вико-вали воскові моделі для виготовлення литих прикрас, предметів побуту. Стародавні греки і скіфи близько 2,5 тис. Років тому відмінно володіли цим способом.
В епоху Відродження великі художники, скульптори використовували воскові моделі для відливання художніх виробів - скульптур, прикрасі. Елементи воскових моделей використовувалися і стародавніми українськими майстрами при литті дзвонів, гармат, церковної та речей домашнього вжитку. Воскові моделі широко при-змінювалися і в ювелірному виробництві.
Надалі розвиток цього процесу показало економічну доцільність-ність його використання в машинобудуванні і приладобудуванні. Таким способом одержують точні виливки з різних сплавів товщиною від 0,8 мм і більше, з хорошою, чистою поверхнею малої шорсткості, з невеликими припусками на обробку.
Процес отримання виливків добре механізований й автоматизо-ваний. На базі цього процесу створені автоматизовані ливарні цехи з виробництва точних виливків.
Однак лиття по виплавлюваних моделях - процес м н о г о о п е р а ц і о н н и й.
Маніпулятормие операції при виготовленні і збірці моделей, нанесенні суспензії на модель і інші досить складні і трудомісткі, що ускладнює автоматизацію процесу.
Процес складається з ряду тривалих операцій, що визначають продуктивність: пошарове формування та сушка шарів оболонкової форми на моделі, прожарювання форми.
Внаслідок великої кількості операцій, технологічних факто-рів, що впливають на розміри порожнини форми і відповідно виливки, знижується її точність.
Якість виливків, одержуваних таким способом, істотно залежить від стабільності якості вихідних матеріалів для виготов-лення моделей, суспензії, форми, а також від стабільності режимів технологічного процесу. Це ускладнює автоматиза-цію управління технологічним процесом.
Зазначені вище особливості технологічного процесу виготов-лення виливків в керамічних оболонкових формах визначають т р і в а ж і е й ш и ї і р о б л е м и його розвитку: скорочення числа операцій технологічного процесу і їх тривалості, спрощення маннпуляторних операцій з метою їх автоматизації; реалізація резервів підвищення точності виливків, якими володіє даний процес; створення систем автоматизованого управління технологічним процесом.
Особливості формування і якість виливків.
Особливості формування виливків в оболонкової формі обумовлені тим, що, як правило, перед заливкою форму нагрівають до порівняно високих температур. Ці особливості полягають в наступному.
Невеликі теплопровідність, теплоємність і щільність матеріалів оболонкової форми і підвищена температура форми знижують швидкість відводу теплоти від розплаву, що спосіб-ствует поліпшення заповнюване ™ форми. Завдяки цьому мож-ли отримання складних виливків зі сталі з товщиною стінки 0,8-2 мм, зі значною площею поверхні. Поліпшенню заповнюваності форми сприяє також і мала шерохова тости її стінок.
Невисока інтенсивність охолодження розплаву в нагрітій оболонкової формі призводить до зниження швидкості затвердіння виливків, укрупнення кристалічної будови, можливості по-явища в центральній частині масивних вузлів і товстих (6-8 мм) стінок усадочнихдефектів - раковин і рихлоти. Тонкі ж стінки (1,5-3 мм) тверднуть досить швидко, і осьова пористість в них не утворюється. Для зменшення усадочнихдефектів необхідно створювати умови для спрямованого затвердіння і харчування виливків. Для поліпшення кристалічної-ського будови виливків використовують термічну обробку.
Підвищена температура форми при заливці сприяє розвитку на поверхнеет-і -Контакт виливок - форма фізико-хімічних процесів, які можуть призвести до зміни струк тури поверхневого шару виливка, порушення нормальної роботи на її поверхні.
Наприклад, на виливок з вуглецевих сталей характерним дефектом є окислений і зневуглецьована поверхност-ний шар глибиною до 0,5 мм. Причина окислення і обезуглеро-вання виливків полягає у взаємодії в основному кисню повітря з металом виливки при її затвердінні і охолодженні.
Зі збільшенням вмісту в середовищі, що оточує виливок, газів-окислювачів O2, СО2 і парів Н2О, при високих температу-рах виливки і форми процеси обезуглероживания інтенсіфіці-ються. Тому невелика швидкість охолодження виливки в на-Гретою оболонкової формі сприяє збільшенню глибини обезуглероженного шару виливка. Збільшення вмісту вугле- роду в стали підвищує інтенсивність зневуглецювання по-поверхневого шару виливка.
Для зменшення глибини обезугле-Рожен шару використовують спеціальні технологічні прийоми. засновані на запобігання або зменшення контакту кисло-роду повітря з твердіє відливанням; на створенні навколо виливки відновної газового середовища і на швидкому охолодженні, т. е. скорочення часу реакції.
На відливання з легованих сталей наслідком фізико-хімічної взаємодії матеріалів форми і виливки при високих температурах є точкові дефекти (піттінг). призводять до зниження корозійної стійкості, жаростой-кістки і жароміцних виливків і їх шлюбу.
Попереджувати появу цього дефекту можливо створенням відновної газового середовища в формі, заливанням форм в ва-вакуумі, нейтральною або захисному середовищі; зменшенням або устра-ням взаємодії оксидів виливки і форми; заміною її вогнетривкого матеріалу, наприклад кремнезему, високоінертнимі основними (магнезитові, хромомагнезитові).
Прагнення отримати виливки з чистою, гладкою поверх-ністю викликає необхідність використання вогнетривких мате-ріалів з малими розмірами зерна основної фракції (С005). Це знижує газопроникність оболонкової форми до неяк-ких одиниць, створює небезпеку утворення повітряних мішків у формі при її заповненні, призводить до зниження заповнюваності форми і утворення дефектів виливки через незаповнення форми.
Ефективність виробництва і сферу застосування.
На основі виробничого досвіду можна вказати наступні переваги способу лиття в оболонкові форми по виплавлюваних моделях:
- можливість виготовлення практично з будь-яких сплавів виливків складної конфігурації, тонкостінних, з малою шорсткістю поверхні, високим коефіцієнтом точності по масі, мінімальними припущеннями на обробку різанням;
- різким скор-щением відходів металу в стружку;
- можливість створення складних конструкції, що поєднують кілька деталей в один вузол, що спрощує технологію виготовлення машин і приладів;
- можливість економічно вигідного здійснення процесу в одиничному (дослідному), серійному і масовому виробництвах, що важливо при створенні нових машин і приладів;
- зменшення витрат формувальних матеріалів для виготовлення 1 т виливків, зниження матеріаломісткості виробництва;
- поліпшення умов праці і зменшення шкідливого впливу ливарного процесу па навколишнє середовище.
Поряд з перевагами спосіб має і сліду не-достатками:
1) процес виготовлення форми багатоопераційний, трудомісткий і тривалий;
2) велика кількість технологічних факторів, що впливають на якість форми і виливки, і соответствен-но складність управління якістю;
3) велика номенклатура матеріалів, що використовуються для отримання форми (матеріали для моделей, суспензії, обсипання блоків, опорні матеріали);
4) складність маніпуляторних операцій виготовлення моделей і форм, автоматизації цих операцій;
5) підвищена витрата металу па літники і тому невисокий технологічний вихід придатного (ТВГ).
Зазначені переваги і недоліки визначають ефек-ву область використання лиття в оболонкові форми по виплавлюваних моделях:
- виготовлення відливок, максимально наближаються по конфігурації до готової деталі з метою зниження трудомісткості обробки важкооброблюваних металів і сплавів різанням, заміни трудомістких операції зварювання або папки для підвищення жорсткості, герметичності, надійності конструкцій деталі, вузла, обробки тиском трудіодеформіруемих сплавів;
- виготовлення тонкостінних великогабаритних виливків по-щення точності з цілі зниження маси конструкції при по-підвищенні її міцності, герметичності та інших експлуатаційних властивостей;
- виготовлення відливок підвищеної точності зі сплавів з особливими властивостями і структурою.
Виробництво виливків по виплавлюваних моделях знаходить ши-рокое застосування в різних галузях машинобудування і в при-боростроеніі.
Використання лиття в оболонкові форми для отримання заготовок деталей машин замість виготовлення їх з кованих заготовок або прокату дозволяє в середньому зменшити відхід металу в стружку на 34-90%, знизити трудомісткість обробки різанням на 25-85%, собівартість виготовлення деталей на 20-80% .
Однак, слід враховувати, що економічна ефективність істотно залежить від вибору номенклатури відливок, виготовлені-ваних цим способом. Тільки при правильному виборі номенклатури деталей можна досягти високої економічної ефективності виробництва.