Спосіб лиття в оболонкові форми заснований на отриманні разових полуформ і стрижнів у вигляді оболонок товщиною 6 ... 10 мм.
Їх виготовляють шляхом затвердіння на металевій оснащенні шару суміші, в якій сполучна речовина при нагріванні спочатку розплавляється, а потім твердне (необоротно), надаючи оболонці високу міцність. Технологія лиття в оболонкові форми включає ряд операцій, виконання яких при литті даними способом має яскраво виражені особливості.
До них відносяться. приготування спеціальної піщано-смоляних сумішей; формування на модельної оснащенні тонкостінних оболонкових форм і стрижнів; збірка форм і їх підготовка до заливання.
Для приготування оболонкових форм випускають спеціальне сполучна, що представляє собою суміші фенолформальдегидной смоли з каталізатором затвердіння смоли, що вводиться в кількості 7 ... 8%.
Попереднє формування оболонки найбільш часто виробляють, використовуючи поворотний бункер 1, в який засипають піщано-смоляних суміш 2 (рис. 19, а). На верхню частину бункера, забезпечену кільцевим каналом 3 для подачі охолоджуючої води, встановлюють моделями вниз і закріплюють нагріту до 200 ... 240 o С металеву модельну плиту 4. На ній закріплена за допомогою чотирьох напрямних колонок 5 плита 6 штовхачів 7. Штовхачі, рівномірно розподілені по всій плиті, виходять на робочу поверхню, як моделі, так і модельної плити. Їх фіксують спеціальними хвостовиками в гніздах плити 6 і закріплюють в ній притискної плитою 8. Модельна плита з виштовхує пристроєм поміщена в корпус 9. Для фіксації плити штовхачів в початковому положенні на напрямних колонах 5 встановлені пружини 10.

Мал. 19. Технологія лиття в оболонкові форми
Для попереднього формування оболонки бункер 1, забезпечений цапфами 11 і поворотним механізмом, повертають на 180 о і формувальний матеріал падає на гарячу модельну плиту (рис.19, б), ущільнюючи під дією гравітаційних сил. У прилеглому до плити шарі суміші смола плавиться (при температурі 95-115 o С), змочуючи зерна піску, а потім починає полимеризоваться, загустевая і отверждаясь в міру прогріву до більш високої температури. За 30 ... 40 з витримки смола встигає оплавитися в шарі товщиною близько 10 мм.
Шар залишається на модельної плиті після повороту бункера в початкове положення (ріс19, в) і скидання на дно бункера не прореагував, що зберегла свої початкові властивості і придатною для подальшого використання частини суміші.
Тепер модельну плиту зі сформованої оболонкової напівформи знімають з бункера (рис.19, г) і подають в піч 12 (рис.19, д), де при температурі 300-400 o С за 90 ... 120 с закінчується полімеризація, і смола набуває високу технологічну міцність. Потім готову оболонкову полуформу знімають з модельної плити (рис.19, е) і з'єднують з іншого полуформой (наприклад, склеюванням) на спеціальному пневмопрессом (рис.19, ж). Для виключення прориву розплаву, форми з вертикальним роз'ємом зазвичай заформовують (рис.19, з) в опорний наповнювач (пісок, дріб і т.п.). Форми невеликої висоти з горизонтальним роз'ємом в більшості випадків не заформовують і заливають на піддонах з піщаної постіллю. В оболонкові форми отримують виливки практично з будь-яких промислових сплавів масою до 200 ... 300 кг.
Переваги лиття в оболонкові форми в порівнянні з литтям в піщано-глинисті разові форми полягають в наступному:
- зменшення параметрів шорсткості поверхні і істотне поліпшення зовнішнього товарного вигляду виливків;
- можливість отримання виливків з тонким і складним рельєфом, а також товстостінних виливків з литими каналами малих перетинів;
- зменшення трудомісткості ряду операцій технологічного процесу (приготування суміші, виготовлення форми, очищення виливків і ін.);
- скорочення в 8 ... 10 разів і більше обсягу переробки і транспортування формувальних матеріалів;
- зменшення металоємності формувального обладнання.
Крім того, для лиття в оболонкові форми характерна менша жорсткість з оболонки, що слід розглядати як гідність методу в порівнянні методами лиття в кокіль.
Основні недоліки методу лиття в оболонкові форми:
- відносно висока вартість смоляного зв'язуючого;
- складність модельної і стрижневою оснастки;
- підвищене виділення шкідливих хімічних речовин в ході термічного розкладання смоляного зв'язуючого;
- недостатня міцність оболонок при отриманні важких виливків;
- схильність до появи деяких специфічних видів дефектів, які супроводжують низьку газопроникність ливарної форми.
Лиття по виплавлюваних моделях.
Сутність лиття по виплавлюваних моделях зводиться до виготовлення виливків заливанням розплавленого металу в разову тонкостенную нероз'ємному ливарну форму, виготовлену з жидкоподвижного вогнетривкої суспензії за моделями разового використання (разові виплавлювані моделі виготовляють з легко плавких компонентів - парафін, жирні кислоти та ін.) З подальшим затвердінням залитого металу, охолодженням виливки у формі і витяг її з форми (рис. 20).
Рис.20. Послідовність операцій процесу лиття по виплавлюваних моделях: 1 - виготовлення моделей в прес-формі; 2 - збір моделей в модельний блок на металевий стояк; 3 - нанесення на модельний блок вогнетривкої суспензії; 4 - обсипання шару суспензії зернистим матеріалом в киплячому шарі
Відмінними рисами лиття по виплавлюваних моделях є низька теплопровідність і висока початкова температура форми, що значно знижує швидкість відводу теплоти від залитого металу і сприяє поліпшенню наповнюваності порожнини форми, але одночасно приводить до укрупнення кристалічної будови і до появи усадочних раковин і пористості в стінках товщиною 6 ... 8 мм.
Керамічна суспензія дозволяє точно відтворити контури моделі, а освіту нероз'ємному ливарної форми з малою шорсткістю поверхні сприяє отриманню виливків з високою точністю геометричних розмірів і теж з малою шорсткістю поверхні, що значно знижує обсяг механічної обробки виливків. Припуск на механічну обробку становить 0,2 ... 0,7 мм.
Заливка розплавленого металу в гарячі форми дозволяє отримувати складні по конфігурації виливки з товщиною стінки 1 ... 3 мм і масою від декількох грамів до декількох десятків кілограмів з жароміцних важкооброблюваних сплавів (турбінні лопатки), корозійно-стійких сталей (колеса для насосів), вуглецевих сталей в масовому виробництві (в авто- і приладобудуванні, інших галузях машинобудування) рис. 21; Мал. 22.
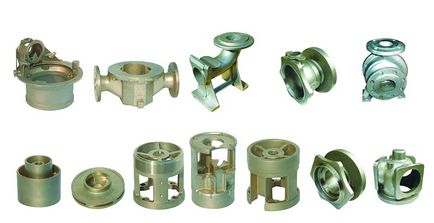
Мал. 21. Виливки, отримані методом лиття по виплавлюваних моделях
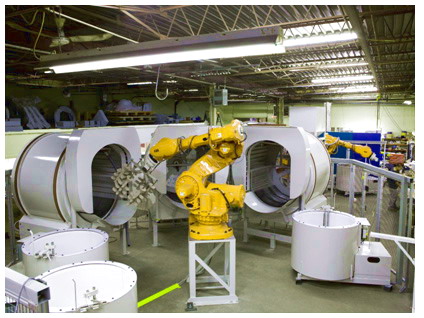
Мал. 22. Лиття по виплавлюваних моделях
Лиття в кокіль. Сутність кокильного лиття полягає в виготовленні виливків заливанням розплавленого металу в багато разів використовувані металеві ливарні форми - кокілі з наступним затвердінням залитого металу, охолодженням виливки і витяганням її з порожнини форми (рис. 23).
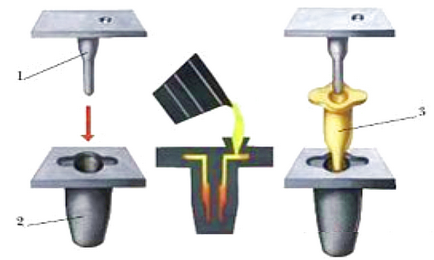
Рис.23. Лиття в металевий кокіль: 1 - стрижень; 2 - кокіль; 3 - виливок
Відмінні риси лиття в кокіль полягає в тому, що формування виливки відбувається в умовах інтенсивного теплового взаємодії з ливарної формою, т. Е. Залитий метал і затвердевающая виливок охолоджуються в кокіль з великою швидкістю, ніж в піщаній формі; кокіль практично не податливий і більш інтенсивно перешкоджає усадки виливки, що перешкоджає вилучення її з кокіль, а також може призводити до викривлення і тріщин у виливках; фізико-хімічну взаємодію виливки і кокиля мінімально, що сприяє підвищенню якості поверхневого шару виливка.
Кокілі - металеві форми - виготовляють литтям, механічною обробкою та іншими методами з сірого чавуну (СЧ 15, СЧ 20 і ін.), Стали (10Л, 15Л, 20Л і ін.) І інших матеріалів. Стрижні і різні вставки виконують з легованих сталей (30ХГС, 35ХГСА і ін.) Так як елементи кокиля працюють в умовах впливу високих температур і механічних навантажень.
Всі операції технологічного лиття в кокіль механізовані й автоматизовані. Кокільне лиття застосовують в масовому і серійному виробництвах для отримання виливків з чавуну, сталі і сплавів кольорових металів з товщиною стінок 3 ... 100 мм, масою від декількох грамів до декількох сотень кілограмів (рис.24).
При лиття в кокіль скорочується витрата формувальної і стрижневої сумішей. затвердіння виливків відбувається в умовах інтенсивного відводу тепла з залитого металу, що забезпечує більш високі щільність металу і механічні властивості, ніж у виливків, отриманих за допомогою піщаних форм. Виливки, виготовлені литтям у кокіль, відрізняються високою геометричною точністю розмірів і малою шорсткістю поверхні, що знижує припуски на механічну обробку вдвічі в порівнянні з литтям в піщані форми. Цей спосіб лиття високопроізводітелен.
Недоліки кокильного лиття - висока трудомісткість виготовлення кокілів, їх обмежена стійкість, труднощі виготовлення складних по конфігурації виливків.
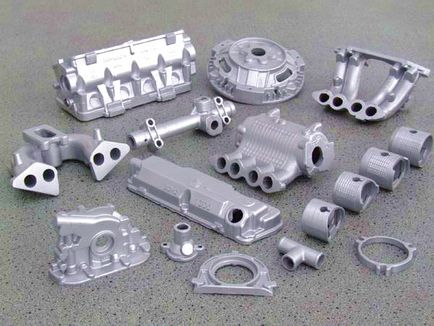
Мал. 24. Виливки, отримані литтям в кокіль
Відцентрове лиття. При відцентровому литті сплав заливають у які працюють форми; формування виливки здійснюється під дією відцентрових сил, що забезпечує високі щільність і механічні властивості виливки (рис. 25).
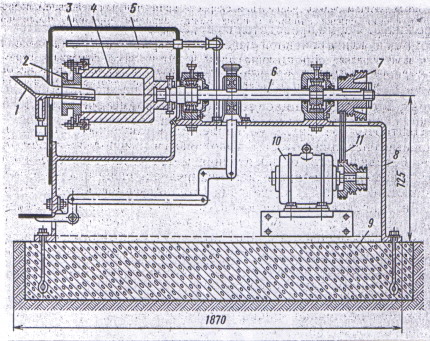
Рис.25. Шпиндельна машина для виготовлення виливків відцентровим литтям:
1 - жолоб; 2 - кришка; 3 - захисний кожух; 4 - форма; 5 - система охолодження; 6 - шпиндель; 7 - шків; 8 - станина; 9 - бетонну основу; 10 - електродвигун; 11 - кліноременниє передача
Відцентровим литтям виливки виготовляють в металевих, піщаних, оболонкових формах і формах для лиття по виплавлюваних моделях на відцентрових машинах з горизонтальною або вертикальною віссю обертання.
Металеві форми - виливниці виготовляють з чавуну і сталі. Товщина виливниці зазвичай в 1,5 ... 2 рази більше товщини виливки. В процесі лиття виливниці з зовні охолоджують водою або повітрям. На робочу поверхню виливниці наносять теплозахисні покриття для збільшення терміну їх служби. Перед початком роботи виливниці підігрівають до температури 200 о С.
Переваги відцентрового лиття - отримання внутрішніх порожнин трубних заготовок без застосування стрижнів; велика економія сплаву за рахунок відсутності літніковойсистеми; можливість отримання двошарових заготовок, що досягається почергової заливкою в форму різних сплавів (сталь і чавун, чавун і бронза і т.д.).
Лиття під тиском. Сутність лиття під тиском полягає у виготовленні виливків у металевих формах (прес-формах) заповненням розплавом під дією зовнішніх сил. Затвердіння виливки протікає під надлишковим тиском або при охолодженні водою. Після охолодження виливок витягають з прес-форми (рис. 26; рис. 27).
На машинах з горизонтальною камерою пресування порцію розплавленого металу заливають у камеру пресування (рис.26, а), який плунжером 5 під тиском 40 ... 100 МПа подається в порожнину прес-форми (рис.26, б), що складається з нерухомої 3 і рухомий 1 напівформи. Внутрішню порожнину в литві отримують стрижнем 2. Після затвердіння виливки прес-форма розкривається (рис.26, в), витягується стрижень 2 і виливок 7 виштовхувачами 6 видаляється з робочої порожнини прес-форми.
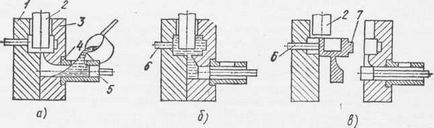
Мал. 26. Схема процесу виготовлення виливків на машинах з горизонтально холодної камерою пресування
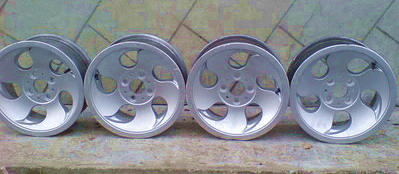
Мал. 27. Вироби, отримані методом лиття під тиском
На рис. 28, а показана одна з різновидів способів безперервного лиття і одержувані різної форми виливки.
Процес безперервного лиття здійснюється наступним чином. Розплавлений метал з металлопріёмніка 1 через графітову насадку 2 надходить в водоохолоджуваний кристаллизатор 3 і твердне у вигляді виливків 4, яка витягується спеціальним пристроєм 5. Довгі виливки розрізають на заготовки необхідний довжини. Цим способом отримують різні виливки (рис. 28, б) з паралельними утворюють з чавуну, мідних, алюмінієвих та інших сплавів. Виливки, отримані цим способом, не мають неметалічних включень, усадочних раковин і пористості завдяки створенню спрямованого затвердіння сплаву.
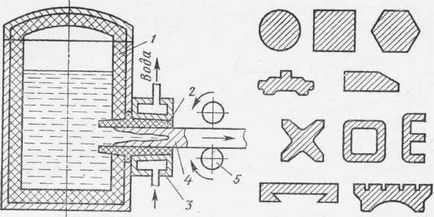
Мал. 28. Схема горизонтального безперервного лити (а) і зразки виливки (б)
Відмінні риси лиття під тиском:
- значний тиск на розплав (100 МПа і більше) забезпечує високу швидкість високу швидкість руху потоку розплаву в прес-формі (0,5 ... 120 м / с). Це дозволяє одержувати виливки з товщиною стінки менше 1 мм;
- висока швидкість впуску розплаву в порожнину прес-форми не дозволяє повітрю і продуктам розкладання мастильного матеріалу повністю піти з порожнини прес-форми. Для цього використовують вакуумирование порожнини прес-форми або продування камери пресування і порожнини прес-форми киснем до повного видалення повітря;
- висока інтенсивність теплового взаємодії між розплавом, виливки і прес-формою сприяє зміні структури в поверхневих шарах виливки, підвищенню її міцності і т.д .;
- для зменшення усадочною пористості використовується подпрессовка в кінцевий момент пресування, внаслідок чого підвищуються механічні властивості матеріалу виливків, і зростає їх герметичність;
- при лиття під тиском температуру заливки сплаву вибирають на 10 ... 20 о С вище температури ліквідусу, а прес-форму нагрівають до температури 120 ... 320 о С.
Лиття під тиском використовують в масовому і великосерійному виробництвах виливків з мінімальною товщиною стінок 0,8 мм, з високою точністю розмірів і малою шорсткістю поверхні завдяки точній обробці і ретельному полированию робочої порожнини прес-форми; без механічної обробки або з мінімальними припущеннями, що різко скорочує обсяг механічної обробки виливків; з високою продуктивністю процесу.
На рис. 29 показана схема промислової установки лиття під низьким тиском в металеву форму.
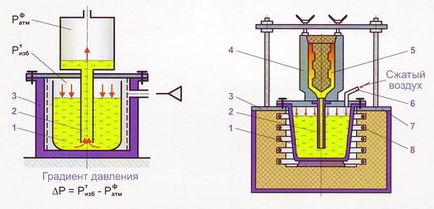
Мал. 29. Схема і установка для лиття під низьким тиском:
1 - тигель з розплавленим металом; 2 - металлопровода; 3 - камера тигля; 4 - металева форма; 5 - виливок; 6 - повітропровід; 7 - герметизуюча кришка; 8 - нагрівачі
Недоліки лиття під тиском - висока вартість прес-форм і обладнання; обмеженість габаритних розмірів і маси виливків; наявність повітряної пористості в масивних частинах виливків, знижує міцність деталей, і ін.
В даний час є ще ряд технологій отримання виливків:
- лиття під регульованим тиском (лиття під низьким тиском, лиття з протитиском, лиття вакуумним всмоктуванням і ін.);
- електрошлакове лиття. Цим способом отримують виливки відповідального призначення масою до 300 т: корпусу клапанів і засувок атомних і теплових електростанцій, колінчаті вали суднових дизелів, корпусу посудин високого тиску, ротори турбогенераторів та ін.
Вибір раціонального способу виготовлення виливків. Сучасні вимоги, що пред'являються до литим заготівлях деталей машин, характеризуються максимальним наближенням виливків за формою і розмірами до готових деталей, економією металу, застосуванням прогресивних методів лиття.
Вихідною інформацією для вибору способу виготовлення виливки є креслення деталі і технічні вимоги на неї; матеріал деталі; програма випуску; параметри, за якими здійснюється оптимізація способу отримання литої деталі, і т.д.