В обсяг ремонтних робіт входять наступні заходи.
При профілактичному огляді:
1) перевірка осьового розбігу ротора;
2) очищення і промивання картерів підшипників, зміна масла, промивання масляних трубопроводів;
3) ревізія Сальник-вої набивання і перевірка стану захисних гільз;
4) перевірка стану напівмуфт, промивка і зміна мастила.
При поточному ремонті:
1) повне розбирання з перевіркою зазорів в ущільненнях ротора в корпусі насоса, перевірка биття ротора;
2) ревізія і заміна деталей торцевих ущільнень.
При капітальному ремонті:
1) ревізія всіх складальних одиниць і деталей;
2) заміна робочих коліс, валів, ущільнюючих кілець корпусу, грундбукс, розпірних втулок.
Ремонт насосів проводиться за типовим технологічним процесом.
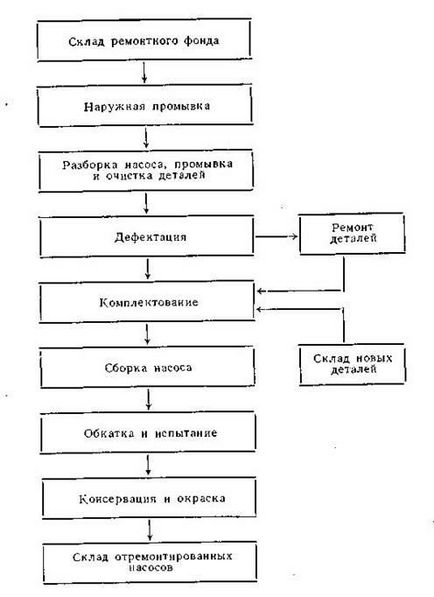
Малюнок - Схема типового технологічного процесу ремонту насосів
Перед відправленням в ремонт насос піддається зовнішньому огляду і контролю. Перевіряється зовнішнє стан насоса, його комплектність і проводяться такі виміри, що оформляються актом:
1) зміщення положення ротора в корпусі насоса в радіаль-ном напрямку;
2) осьової розбіг ротора;
3) розбіжність осей насоса і приводу в радіальному напрямку.
Насоси здаються в ремонт в зібраному вигляді, повністю повітком-плектованние деталями незалежно від ступеня їх зносу.
При відсутності базових деталей або при наявності наскрізних тріщин в стінках корпусу або днища насос списується.
Після зовнішньої промивання насос розбирається в такій послідовності:
1) випрессовиваются напівмуфти, виймається шпонка, попередньо відкріплюється і знімається шайба;
2) відкріплюється і знімається кронштейн;
3) відвертаються гайки, які кріплять насоса до кришки, знімається кришка разом з корпусом підшипника, ротором і дру-шими деталями;
4) знімається робоче колесо (для двоступеневих насосів після зняття діафрагми з прокладкою знімається друге робоче колесо);
5) знімаються кришка насоса, втулка сальника, ліхтар сальника, грундбукса і інші деталі торцевого уплот-вати;
6) виймається захисна гільза;
7) знімаються кришки підшипника з прокладками і втулками;
8) з корпусу підшипника виймається ротор, який потім розбирається.
Перед дефектації деталі очищаються від забруднення, промиваються, обезжирюються і висушуються. Деталі, покриті важкими масляні-простими відкладеннями (деталі проточної частини насоса), подвер-гаются промиванні в ванні з 8 - 10% розчином каустичної соди при 100 ° С протягом 30 - 40 хв. Деталі з досить сильною кор-розіей піддаються травленню згідно з інструкцією по їх хі-мічного очищення.
Промиті і очищені деталі поміщаються на 10 - 15 хв у водний розчин пасиватора для запобігання від корозії. Після пассивирования (розчин містить 20 г / л води каустіче-ської соди і 50 г / л води хромпика) деталі просушують при нормальній температурі. Термін зберігання деталей, оброблених пасиватором, становить 5 - 10 діб.
Дефектация деталей здійснюється на спеці-ном робочому місці, оснащеному картами дефектації та необхід-мим набором інструментів і вимірювальних інструментів.
Карти дефектації (дефектні відомості) є основним технічним документом, на підставі якого проводяться огляд, вимір, а при необхідності випробування деталей та со-напружень, сортуванню їх на три групи:
1) де-талі, придатні в сполученні з новими деталями;
2) деталі, що підлягають ремонту;
3) деталі, непридатні для подальшого викорис-тання.
Контроль підшипників кочення включає огляд, перевірку на шум і легкість обертання, вимір осьового і радіального зазорів, вимір розмірів кілець. Діаметри кілець вимірюються лише у випадку зсуву обойм на валу або корпусі, а також при наявності слідів корозії, опіків і появі чорноти.
У підшипниках кочення не допускаються:
1) тріщини або ви-крашіваніе металу на кільцях і тілах кочення, кольору побіжить-лости в будь-якому місці підшипника;
2) вибоїни і відбитки (лунки) на бігових доріжках кілець;
3) лущення металу, лускаті відшарування;
4) корозійні раковини, забоїни, ризики і вм'ятини на поверхні кочення, видимі неозброєним оком;
5) над-ломи, наскрізні тріщини на сепараторі, відсутність або ослаблений-ня заклепок сепаратора;
6) забоіни і вм'ятини на сепараторі, що перешкоджають плавному обертанню підшипника;
7) помітна на око і на дотик ступінчаста вироблення робочої поверхні кілець;
8) осьової зазор більше 0,08 мм і радіальний зазор більше 0,1 мм;
9) при перевірці на легкість обертання - різкий металеві-ний або деренчливий звук, а також помітне пригальмовування і заїдання.
Пружинні шайби не повинні мати тріщин або надривів. Колишні у вживанні пружинні шайби використовуються по-повторних, якщо вони не втратили пружності. При цьому нормальний розлучення шайби повинен бути рівний її товщині.
Більшість насосів хімічних виробництв перекачують корозійно-активні продукти. У зв'язку з цим стінки корпусу значно зношуються.
При огляді корпусу особливу увагу слід звертати на стан посадочних місць під діафрагму і грундбуксу, ущільнюючих кілець корпусу і порожнини роз'єму, знос внутрішньої порожнини, стан ущільнюючих поверхонь секцій, посадочних місць під поздовжні шпонки, центруючих штифтів, величини зазорів між ущільнювальними кільцями секцій і коліс.
Знос окремих місць внутрішньої порожнини корпусу повинен бути усунутий наплавленням металу за допомогою електрозварювання. Ризики, забоїни і вм'ятини на площинах роз'єму корпусу усуваються зачисткою шабером або заваркою. Значно зношені привалочних поверхні проточуються або фрезеруються. Можна також здійснювати розточення зношених місць і запрессовку втулок з наступною расточкой до номінальних розмірів.
При обертанні роторів в корпусі насоса можливий знос шийок і різьблення, викривлення або поломка вала. Викривлення валів відбувається в результаті виходу з ладу підшипників або ударів частин ротора об нерухомі деталі насоса.
Знос шийок валів може відбуватися через появу рисок, задирів, корозійних каверн і з інших причин з після-дме виходом з ладу підшипників кочення або ковзання.
Як правило, поломка вала спостерігається в місцях переходу вала з діаметра посадкового місця підзахисну гільзу на діаметр шийки вала. Поломка відбувається в результаті концентрації місцевих напружень.
Відновлення зношених шийок вала в залежності від сте-пені зносу здійснюється наступними способами:
до 0,3 мм - електролітичним хромуванням;
від 1,5 до 2,0 мм - електро-литическим залізненням;
від 2,0 до 3,0 мм - автоматичної вибродуговой наплавленням;
від 3,0 до 4,0 мм - ручного газового на-плавкою;
понад 4,0 мм - ручній наплавленням.
Порушена різьблення на валу відновлюється різцем. Якщо пошкодження значні, то ця ділянка вала проточується дощенту різьблення, а потім наплавляється, обробляється і на ньому нарізається нова різьблення.
Робочі колеса виходять з ладу внаслідок корозійного і ерозійного зносу, сильного осьового зсуву ротора в резуль-таті неправильної зборки насоса або руйнування радіально-наполегливих підшипників, попадання в насос сторонніх предметів.
При ремонті колеса відновлюються наплавленням пошкоджений-них місць з подальшою проточкою. Для деяких конструкцій можлива заміна пошкодженого диска. В цьому випадку несправності-ний диск зрізається, а замість нього за допомогою електрозаклепок приварюється новий диск.
Чавунні колеса замінюються новими або наплавляються мед-ним електродом з подальшою проточкою.
Торцеві ущільнення виходять з ладу через зношування пар тертя і корозії. Ремонт торцевого ущільнення полягає в заміні що вийшли з ладу деталей (пари тертя, пружини і ін.). Так само при ремонті прочищають систему охолодження ущільнення.
Після ремонту насос випробовують на випробувальному стенді. Випробування включає в себе:
1) короткочасний пуск;
2) прогрівання насоса;
3) випробування на робочому режимі.
Короткочасний пуск (до 3 хв) насоса здійснюється при закритій засувці на напірному трубопроводі. При цьому прове-ряют:
1) напрямок обертання ротора;
2) показання приладів;
3) мастило підшипників.
Насоси, призначені для перекачування гарячих продуктів, прогріваються. Щоб уникнути теплового удару при циркуляції рідини нагрівання повинен бути поступовим.
Випробування насоса на робочому режимі проводиться в послідовності:
1) пуск електродвигуна;
2) після досягнень-вання повної частоти обертання засувка відкривається на 1/3;
3) обкатка насоса на робочому режимі протягом 2 ч.
§ 4.2 Монтаж відцентрового насоса
Перед монтажем насосів перевіряють і готують фундамент. Фундамент не повинен мати тріщин, пустот і оголеної арматури, що перевіряється зовнішнім осмо-тром. Після зовнішнього огляду перевіряються розміри фунда-мента, його висотні позначки, а також розташування щодо осей будівлі. Для цього фарбою або крейдою на фундамент нано-сятся середини міжцентровою відстаней колодязів під фунда-цементних болти.
При перевірці великого фундаменту по осях його натягуються струни, проводяться обміри фундаменту за допомогою схилів і рулетки, нівеліром або гідрорівнем перевіряються висотні позначки.
Після усунення виявлених дефектів фундамент прини-мається під монтаж. Підготовка до монтажу обладнання заклю-чає в розмітці і підготовці місць установки підкладок. Під-кладки встановлюються по обидві сторони кожного колодязя під фундаментні болти, а також під опорами насоса і двигуна відповідно до форми фундаментної плити. Місця установки підкладок вирівнюються зубилом; вони повинні бути горизон-тальне, розташовуватися на одній висоті з допуском до 5 мм і мати розміри на 10 - 20 мм більше розмірів підкладок. Най-більш поширені розміри підкладок 100 × 100, 200 × 150, 75 × 150 мм. Бажано, щоб кількість підкладок в одному пакеті не перевищувало трьох, а висота пакета становила 25 - 60 мм.
Після закінчення підготовчих робіт, пов'язаних з перевіркою і підготовкою фундаменту, проводиться ревізія (розбирання та збирання) насоса, установка насоса і приводу на фундамент, цін-трірованіе приводу з насосом.
Ревізія насоса полягає в зовнішньому огляді, розбирання та збирання, перевірки всіх деталей і вимірі всіх необхідних зазорів. При зовнішньому огляді перевіряється наявність всіх гайок, пробок, контрольних шпильок, відсутність пошкоджень корпусу насоса, корпусів підшипників, арматури і трубопроводів. Вручну перевіряється легкість обертання ротора.
При розбиранні насоса знімається кришка (для насосів з гори-зонтальним роз'ємом) і ряд деталей (кришки підшипників, сальники, верхні половини вкладишів). При необхідності розбирається ротор. Роз'єм корпусу ущільнюється прокладкою або мастикою з свинцевого білила та сурику, розведених бакеліто-вим лаком.
Перевірка деталей ротора полягає у визначенні биття втулок, робочих коліс, напівмуфти, вала. Биття перевіряється індикатором у власних опорах ротора або в центрах токар-ного верстата. Перевіряються також радіальні зазори в ущільненням-пах робочих коліс і осьові зазори між кільцями ущільнювачів і колесами насоса.
Перевірка підшипників полягає в контролі за фарбі прилягання вкладишів підшипників ковзання до розточеннях корпусів і до шийок вала. Один з підшипників насоса фікс-рілої положення ротора, т. Е. Є опорно-наполегливою, а другий підшипник для компенсації теплових розширень є тільки опорним. В опорному підшипнику при ревізії перевіряється зазор між жолобником вала і вкладишем підшипника (або між підшипником кочення і расточкой корпусу). При підвищенні температури рідини величина осьового зазору в опорному підшипнику також збільшується. Виміряний осьової зазор повинен відповідати зазору, вказаною в паспорті насоса.
При складанні насоса на роз'єм корпусу укладається нова прокладка з пароніту або електрокартону або роз'єм змазування-ється мастикою. Після установки кришки перевіряється легкість обертання ротора.
Насоси невеликої продуктивності поставляються смон-тірован на загальній фундаментній плиті під насос і електро-двигун. Для насосів, що поставляються без рами, при монтажі виготовляється зварна фундаментна рама, на якій до установки її на фундамент центрируется насос з електродвигуна-телем. Потім рама встановлюється на фундаменті на плоских або парних клинових підкладках, в колодязі фундаменту заводяться анкерні болти. Відстань між підкладками по пери-метру рами витримується в межах 300 - 500 мм в залежності від ваги насоса і двигуна. Підкладки розміщуються по обидві сто-ку фундаментних болтів. Установка по осях фундаменту осу-ється переміщенням насоса в потрібну сторону.
Далі перевіряється стан насоса в горизонтальній пло-скостити за рівнем. Для цього знімаються кришки і верхні вкла-дихай підшипників, а рівень укладається на шийки валу. Для насосів з підшипниками кочення рівень встановлюється на напівмуфті. Довгі ротори мають помітний прогин від соб-ного ваги, тому для великих насосів ухили на шийках валу повинні бути приблизно однаковими, і спрямовані в проти-воположние боку. Регулювання горизонтальності здійснюва-ляется підкладками.
Після закінчення вивірки підкладки прихоплюють електро-зварюванням один до одного і фундаментні рами разом з фундамент-ними болтами підливають бетонною сумішшю. Після затвердити-вання підливи проводяться підтяжка фундаментних болтів і контрольна перевірка центрування насоса і двигуна. При необхідності виправлення центрування виконується зраді-ням товщини підкладок під опорами електродвигуна. Після підливи фундаментної рами здійснюється приєднання всмоктувального і нагнітального патрубків.