У дванадцятій статті циклу «Основи технології граничного сканування і тестопригодного проектування» пропонується огляд апаратних засобів системи onTAP фірми Flynn Systems, призначених для сполучення з JTAG-тестованими ПП і вузлами.
Запланований рівень якості і надійності продукції, що випускається є величиною розрахунковою і визначається максимально допустимої вартістю ремонтів, які передбачається провести в гарантійний період в залежності від вимог споживача, умов експлуатації продукції, що випускається і власне стратегії їх проведення.
кщо споживач при укладанні договору на поставку 10 тис. приладів вимагає, щоб гарантійний термін становив 10 років, при цьому географія використання поширюється на всю терріторіюУкаіни, а ремонт передбачається проводити силами підприємства-виготовлювача, то неважко підрахувати, що при рівні відмов в 1%, необхідно буде здійснити 100 виїздів для проведення гарантійних ремонтів.
Витрати на проведення гарантійних ремонтів плануються, як правило, на рівні 2-4% від відпускної ціни. Якщо прилад коштує 100 тис. Руб. то на проведення ремонтів всієї партії може бути запланована сума в 3 млн. руб. Це означає, що в середньому на одну відрядження може бути витрачено 30 тис. Руб. Якщо названі прилади будуть експлуатуватися переважно в Західному Сибіру і на Далекому Сході, то запланованих коштів буде явно недостатньо. Якщо прилади коштують 10 тис. Руб. а в партії - 100 тис. шт. ситуація різко погіршується, тому що плановані витрати на проведення гарантійних ремонтів зростуть в десятки разів і можуть перевищити запланований рівень прибутку. Підвищення відпускної ціни для компенсації цих витрат буде знижувати конкурентоспроможність продукції, що випускається і може стати перешкодою для укладення вигідного контракту. З урахуванням усього вищесказаного, стає зрозумілим найбільш часто зустрічається значення планованого рівня дефектності: 0,1% або 1000 ppm.
Використовуючи дані наведених прикладів, спробуємо розрахувати максимальні витрати на ремонт в процесі виробництва. Якщо в структурі ціни приладу (100 тис. Руб.) Прибуток становить 20%, то собівартість дорівнює 80 тис. Руб. У структурі собівартості компоненти, комплектуючі та матеріали становлять 70% (характерна величина при виробництві електронних приладів), а роботи - 30% (24 тис. Руб.). Припустимо, прилад має Одноплатний конструкцію від 1000 компонентів і 3000 паяних з'єднань. При використанні першокласного складального обладнання максимально досяжний рівень дефектності становить 100 ppm в середині великої партії. В цьому випадку в партії 10 тис. Шт. друкованих вузлів ми отримаємо:
3 000 · 10 000 · 100/1 000 000 = 3 000 потенційно дефектних паяних з'єднань.
Першокласні постачальники і виробники електронних компонентів гарантують рівень дефектності 10 ppm. Це означає, що в партії 10 тис. Шт. ми отримаємо:
1 000 · 10 000 · 10/1 000 000 = 100 потенційно дефектних компонентів, тобто 31% спаяних друкованих вузлів матимуть потенційні дефекти.
Час діагностики і локалізації дефекту на електронному модулі, що має 1 000 компонентів, складає в середньому не менше 4 год. При середній вартості нормогодини для висококваліфікованого фахівця 25 дол. США (з урахуванням накладних витрат), витрати на ремонт при випуску партії приладів без засобів автоматичної діагностики та локалізації дефектів складуть:
3 100 х 4 · 25 = 310 000 дол. США або близько 10 млн руб.
Середні мінімальні витрати на ремонт одного приладу складуть: 10 000 000/10 000 = 1 000 руб. Більш то-го, розрахунки справедливі, якщо все друковані вузли будуть оброблені в одній партії, тому що на початку і кінці партії рівень дефектності, як правило, в кілька разів вище (на початку партії необхідно усунути наслідки помилок операторів і використання невідповідних компонентів і комплектуючих, а в кінці - наслідки нестачі компонентів). Крім того, навіть самому кваліфікованому налагоджувальникові / регулювальника і самому сумлінному контролеру не під силу в повному обсязі перевірити свою продукцію на відповідність її конструкторської та нормативної документації. Як результат - додаткові витрати на ремонт приладів, які відмовили в процесі приймально-здавальних випробувань і у споживача в гарантійний період.
Наведені вище приклади наочно підтверджують відомий постулат: «вартість усунення дефекту тим нижче, чим ближче до місця його потенційного виникнення він виявлений», а це означає, що необхідно домагатися випуску якісної і надійної продукції на заводі-виробнику.
Питання друге: яка технологія забезпечує досягнення запланованих рівнів якості і надійності, і які витрати для цього потрібні? Отже, ми визначили мету: розробити і впровадити технологію, що забезпечує заплановані (розрахункові) рівні якості і надійності продукції, що випускається при мінімальних (оптимальних) витратах.
Розглянемо приклад: на технологічне-тії впроваджений типовий технологічний процес складання друкованих вузлів (див. Рис. 1).
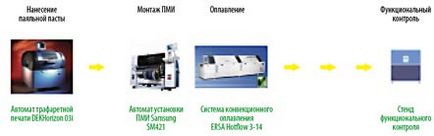
Мал. 1. Технологічний процес складання друкованих вузлів без систем контролю і інспекції
Після впровадження системи АОИ контролю якості монтажу і паяних з'єднань кількість дефектів виробів, пов'язаних зі зміщенням висновків компонентів стосовно контактних майданчиків на друкованій платі, значно скоротилося. Відповідно до запропонованого алгоритму (див. Рис. 2), прийняті перетворення з діагностики і локалізації названого типу дефектів можна вважати задовільними.
Таблиця 2. Критерії якості монтажу поверхнево-монтованих компонентів відповідно до вимог різних стандартів
Дефект - клас 1, 2. Бічний зсув (А) перевищує 50% ширини контактної поверхні (W) або 50% ширини контактної площадки (Р) (вибирається менше значення).
Дефект - клас 3.
Бічний зсув (А) перевищує 25% ширини контактної поверхні (W) або 25% ширини контактної площадки (Р) (вибирається менше значення).
Дефект - клас 1, 2. Бічний зсув (А) перевищує 50% ширини контактної поверхні (W) або 50% ширини контактної площадки (Р) (вибирається менше значення).
Дефект - клас 3.
Бічний зсув (А) перевищує 25% ширини контактної поверхні (W) або 25% ширини контактної площадки (Р) (вибирається менше значення).
п. 10.7 (рис. 50) Дефект «бічний зсув» (А) перевищує 10% ширини контактної поверхні (W).
Дефект - клас 1, 2. Максимальна бічний зсув (А) перевищує 50% ширини виведення (W) або 0,5 мм (вибирається менше значення).
Дефект - клас 1, 2. Максимальна бічний зсув (А) перевищує 50% ширини виведення (W) або 0,5 мм (вибирається менше значення).
Дефект «максимальне бічний зсув» (А) перевищує 25% ширини виведення (W).
Дефект - клас 3. Максимальна бічний зсув (А) перевищує 25% ширини виведення (W) або 0,5 мм (вибирається менше значення).
Дефект - клас 3. Максимальна бічний зсув (А) перевищує 25% ширини виведення (W) або 0,5 мм (вибирається менше значення).
Наступним за значимістю типом дефекту є: «встановлений невідповідний компонент» (рядок 3 в таблиці 2 і рис. 2). Найбільш ймовірними причинами установки невідповідного компонента можуть бути:
- помилка оператора при спорядженні живильника;
- дефектну деталь (шлюб виробника);
- пошкодження компонента в процесі виготовлення (технологічний дефект).
Найбільш ефективним засобом діагностики і локалізації дефектів даного типу є автоматичний внутрісхемний контроль. З огляду на високу щільність монтажу виробів і їх широку номенклатуру, як засіб для проведення автоматичного внутрисхемного електричного контролю була обрана система SPEA4060 (див. Рис. 4).
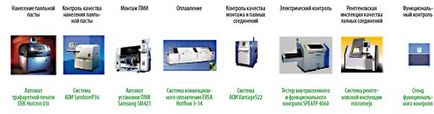
Мал. 4. Схема технологічного процесу складання друкованих вузлів при впровадженні сучасних автоматичних систем інспекції і контролю
Після впровадження системи автоматичного внутрисхемного контролю SPEA 4060 кількість дефектів виробів, пов'язаних з установкою невідповідного компонента значно скоротилося. Відповідно до запропонованого алгоритму (див. Рис. 2), прийняті перетворення з діагностики та локалізації дефектів названого типу можна вважати задовільними.
Наступний по значимості тип дефекту - «недостатній обсяг припою в паяних з'єднаннях» (рядок 4 в таблиці 1 і рис. 3). Найбільш ймовірними причинами незадовільного кількості припою можуть бути:
- некоректні розміри контактних майданчиків (помилка конструк-тора);
- некоректні розміри апертур (помилка конструктора);
- незадовільна якість трафарету (дефект виробника трафарету);
- незадовільна якість паяльної пасти (дефект постачальника і / або виробника);
- незадовільна якість підготовки паяльної пасти до роботи (технологічний дефект);
- некоректні параметри налаштування пристрою трафаретного друку (швидкість переміщення і / або зусилля притиску ракеля);
- викривлення друкованої плати.
Помилки конструкторів повинні бути виявлені на етапах приймання конструкторської документації, технологічної підготовки виробництва і виготовлення дослідних зразків - до постановки вироби в серійне виробництво. Якість трафарету, паяльної пасти і друкованих плат має контролюватися при вхідному контролі.
Якість нанесення паяльної пасти для різних областей застосування регламентується відповідними стандартами (див. Табл. 3).
Таблиця 3. Критерії приймання якості нанесення паяльної пасти відповідно до NASA-STD-8739
Паста повинна бути нанесена з точним суміщенням з контактними майданчиками, а також мати однорідну товщину. Без містків, бульбашок, корок і змазування.
NASA-STD-8739.2 [8.2], [8.6]
Освіта містків - індикатор некоректних параметрів процесу нанесення паяльної пасти.
NASA-STD-8739.2 [8.7.4.f], [12.6.1.a.1]