У конструкціях передач підйомно-транспортних машин примі-ються циліндричні і конічні зубчасті колеса. Циліндри-етичні зубчасті колеса виконуються прямозубими, косозубимі і шевронними.
Конструктивні особливості коліс, їх діаметр і характер про-ництва в значній мірі визначають технологічні про-процеси механічної обробки коліс.
Зубчасті колеса ПТМ діаметром до 400 мм і короткі вал- шестерні виготовляють зазвичай з поковок і штамповок. Цилінд-дріческіе зубчасті колеса простої конфігурації в перетині можуть виготовлятися з прокату, однак при цьому неминучий великий відхід металу в стружку. Для виготовлення зубчастих коліс з прокату, поковок і штамповок використовуються стали марок 45, Ст40Х, 40ХН. Зубчасті колеса з діаметрами більше 400 мм изго-тавлівают відливанням з Ст35Л-І і 55Л-П з подальшою нормалінаціей. Технологічний процес механічної обробки зуб-чатих коліс включає токарної обробки заготовок, нарізування .шліцев або пазів шпон і нарізку зубів.
Токарська обробка передбачає обточування зовнішніх .поверхностей і розточування центрального отвору зубчастих коліс. При індивідуальному і дрібносерійному виробництві токар-ва обробка зазвичай виконується за два установа на токарних або карусельних верстатах. Як приклад на рис. 31 показана (Обробка заготовки великогабаритного зубчастого колеса на # 9632;
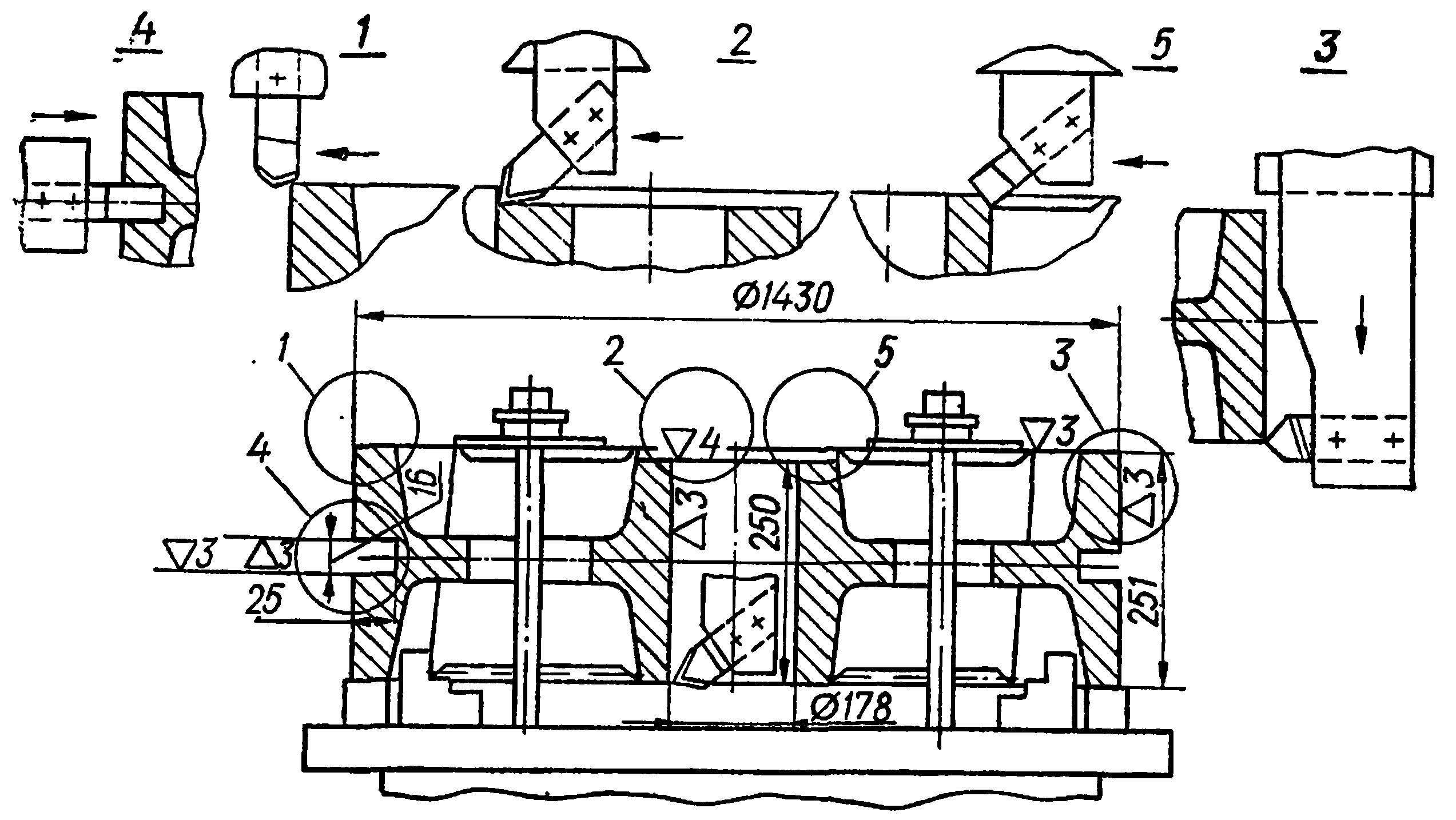
Мал. 31 Токарська обробка заготовки зубчастого колеса на карусельних
переходи (1-5) і застосовується ріжучий інструмент. В процесі 'обробки колеса одночасно обточують або розточують не-, скільки поверхонь за рахунок включення бічних і верхніх ^ супортів. Так, наприклад, одночасно можуть виконуватися переходи 1 і 3; 2 і 4 і т. Д.
При среднесерийном виробництві токарної обробки зуб-чатих коліс діаметром 250-350 мм виробляють на токарно-кару-польових верстатах, а при великосерійному - на токарних багато-резцових автоматах (рис. 32). Заготівля колеса в цьому випадку встановлюється на оправлення, що має канавки до для виходу підрізних різців. З метою надання заготовки в момент її на- пресування на оправку служить шийка N.
Шпонкові пази коліс при дрібносерійному виробництві обра-бативают на довбальних верстатах, а при великосерійному - на протяжних.
Для нарізування зубів зубчастих коліс застосовуються метод деле-ня (копіювання) та методи обкатки. Нарізування зубів методами ділення виконується дисковими (рис. 33, а) і пальцьовими
(Рис. 33, б) модульними фрезами. З цією метою використовуються уні-версальная-фрезерні або спеціальні верстати.
До методів обкатки відносяться: нарізування черв'ячної модульної фрезою (рис. 33, в) і круглими або рейковими здолбяком.
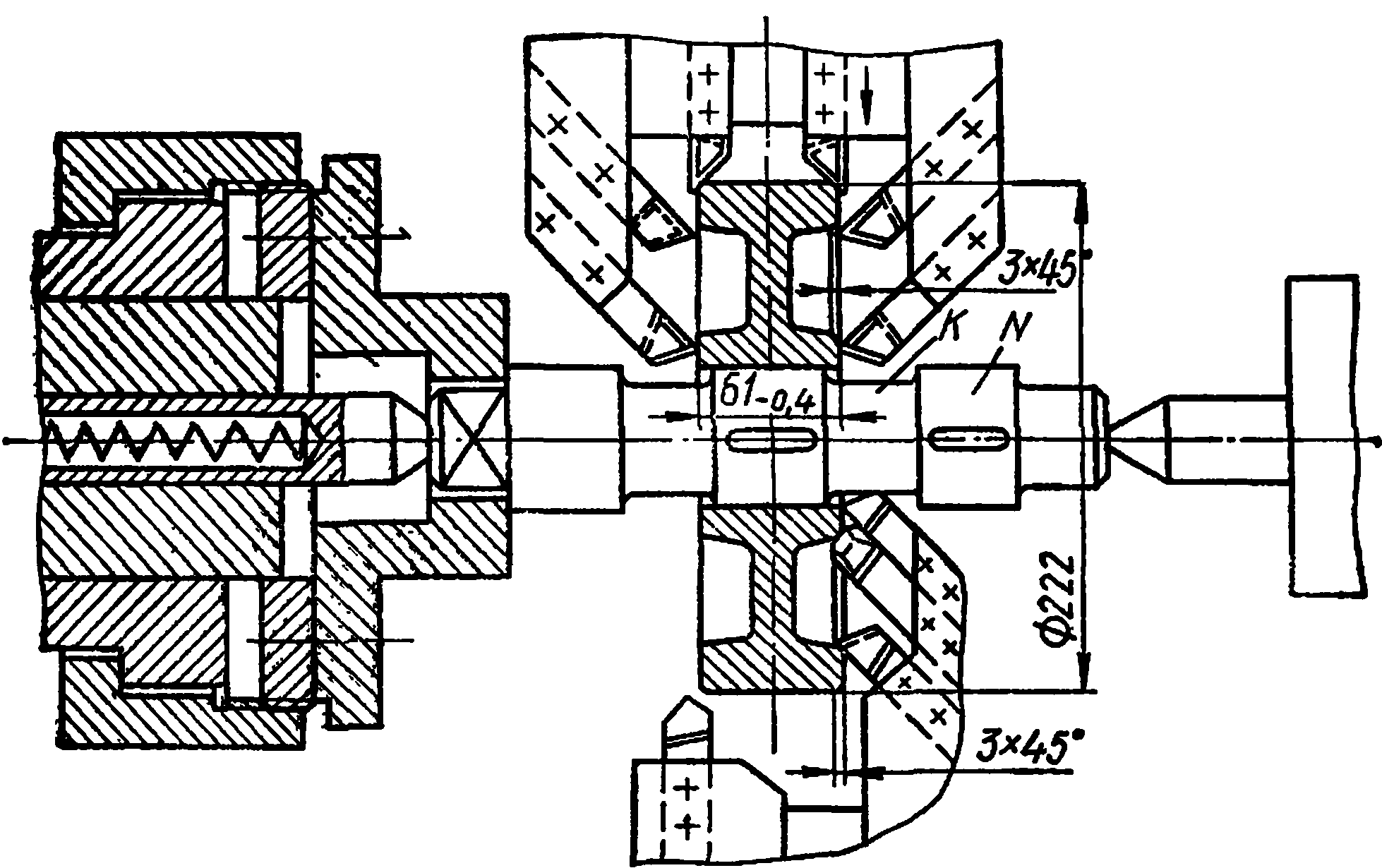
Мал. 32. Токарська обробка заготовки зубчастого колеса на Багаторізцеві автоматі
Нарізування методами обкатки проводиться на спеціальних зуборізних верстатах. Все методу нарізання зубів засновані на використанні-ванні евольвентного профілю зубів (рис. 33, г)
Технологічний про-процес обробки шестерень, які виконуються разом з ва-лом (валів-шестерень), со-стоїть з операцій обробки валів і зубів.
У процесі роботи у зуб-чатих коліс в наиболь-шей ступеня зношуються зуби. При недостатній міцності зубів на з-гинув відбувається, їх злам.
Протизносні свойст-ва робочих поверхонь зубів підвищуються за рахунок коригування зубчастого зачеплення, вибору мате-ріалу для виготовлення зубчастих коліс і їх тер-термічної обробки. У всіх випадках потрібно, щоб зуби мали велику міцність на вигин і високий опір зношування робочих поверх-ностей. Ці вимоги можуть бути найбільш повно задоволені,
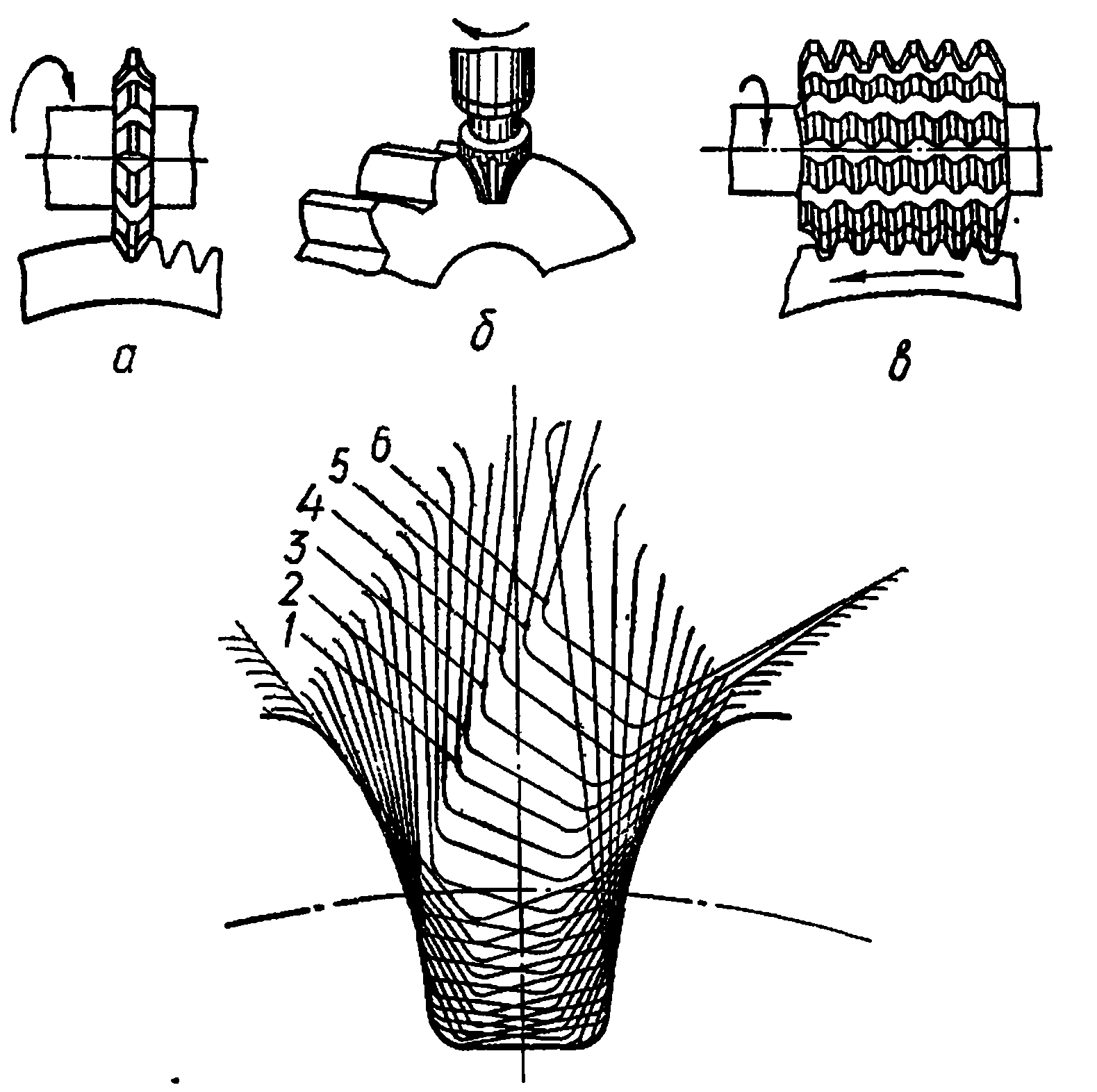
Мал. 33. Методи нарізання зубів зубчастих коліс фрезами:
а - дисковими; б - пальцьовими; в - черв'ячної модульної фрезою; г - профіль зуба
якщо метал по всьому основному перетину зубів буде мати високі показники міцності і в'язкості, а поверхневі шари металу робочих поверхонь зубів - високу твердість. Удов-летворіть одночасно ці два вимоги можна, застосовуючи методи хіміко-термічної обробки зубів або поверхневої їх гарту.
З методів хіміко-термічної обробки зубів для зубч-тих коліс ПТМ найчастіше застосовують азотування цементацию. Азотування користуються для деталей, виготовлених з середньо-вуглецевих і легованих сталей. Після процесу азотіро-вання і подальшого гарту з відпусткою робочі поверхні 'зубів Тримаються 40-50 HRC при твердості внутрішніх шарів 190-230 НВ. Товщина азотированного (загартованого) шару зазвичай знаходиться в межах 2,5-4 мм.
Поверхневому загартуванню піддаються деталі з среднеугле-родістих і легованих сталей (Ст40, 40Х, 40ХН та ін.). Вона досягається нагріванням поверхневих шарів металу головним обра-зом струмами високої частоти (ТВЧ) або ацетилено-кисневим полум'ям і наступним охолодженням. При обох способах зам-ливаются тільки поверхневі шари металу, нагріті вище точки АСЗ на діаграмі «залізо - вуглець». Товщина загартованого шару 2,5-4 мм знаходиться в межах 40-50 HRC, але може бути знижена за рахунок відпустки.
У середньо- та крупномодульних зубчастих коліс поверхневому загартуванню піддається окремо кожен зуб. При цьому існує два методи загартування: тільки робочих поверхонь зубів або всіх бічних поверхонь, включаючи поверхні западини. При пер-вом способі в місцях переходу від загартованого металу до незак-ленному створюється концентрація напружень, що часто призводить до зламу зубів за цими перетинах. При загартуванню другим способом пе-реходная зона відсутня, що підвищує міцність зубів на вигин.