Теоретично патентування є швидке охолодження дроту в аустенітному стані до заданої температури з подальшою витримкою протягом часу, що перевищує час ізотермічного розпаду при цій температурі з метою отримання структури сорбіту. На практиці кінцева швидкість охолодження дроту, перегрів вхідного ділянки ванни і тепловиділення в процесі фазового переходу у-у а-залізо призводять до того, що навіть при охолодженні в свинці, а тим більше - в селітрі аустенит перетворюється в сорбіт в певному температурному діапазоні, що залежить як від властивостей дроту, так і від охолоджуючого середовища (політермічні перетворення). Тому оптимальна температура охолоджуючої ванни виявляється різною для різних охолоджувальних середовищ і залежить не тільки від діаметра дроту і марки стали, але і від температури нагріву, часу аустенізації і навіть від плавки стали, бо в різних умовах стійкість аустеніту виходить кілька різною.
Знайдені в лабораторних установках з киплячим шаром режими швидкісного нагріву дроту різних діаметрів (від 0,8 до 12 мм) і марок сталей (У7-У12, 70С2ХА, 60С2), щоб забезпечити отримання необезуглероженной без окалини поверхні. Там же дані результати вельми грунтовних досліджень киплячого шару як охолоджуючої середовища при патентування. Спочатку на зразках в лабораторних установках Уральського політехнічного інституту, а потім на прохідній тринитковий ванні на Белорецком металургійному комбінаті (нагрів здійснювали в звичайної електричної печі) були відпрацьовані оптимальні режими охолодження дроту зазначених вище марок сталей і діаметрів. Найдокладніші порівняльні дослідження показали, що дріт, Патентірованний в киплячому шарі, що не відрізняється від патентованою в свинці і селітрі не тільки за своїми механічними властивостями (міцність, подовження, запас пластичності і т. Д.), Але і по ряду фізичних властивостей (електроопір, залишкова магнітна індукція, індукція насичення, коерцитивної сила). Оскільки коефіцієнт тепловіддачі від гарячої дроту до киплячого шару дещо менше, ніж до розплавленої селітри і набагато нижче, ніж до свинцю, для отримання тієї ж швидкості охолодження в ванні з киплячим шаром її температуру в порівнянні з температурою свинцевих і селітрових ванн слід вибирати тим нижче, чим більше діаметр дроту і менше стійкість переохолодженого аустеніту. Для вуглецевої дроту (сталь У8А) діаметром 6,3 мм, наприклад, найкращі властивості виходять при патентування в киплячому шарі (діаметр частинок корунду 60-100 мкм) температурою 35-40 ° С. При цьому, як показують термограмми охолодження, розпад аустеніту здійснюється при температурі дроту 500-600 ° с, т. е. приблизно в тому ж діапазоні, що і при охолодженні в селітрі з температурою 480 ° с (за прийнятою на заводах технології).
Іноді висловлюються побоювання, що патентування в шарі такої низької температури може призвести до збільшення кількості залишкового аустеніту. Спеціальні дослідження показали, що цього не відбувається: в результаті виділення тепла в процесі розпочатого при певній температурі фазового переходу температура дроту не тільки не зменшується, а навіть дещо підвищується, незважаючи на тепловіддачу до киплячого шару (якщо її діаметр не надто малий), тому практично весь аустеніт розпадається в досить вузькому діапазоні температур.
За інших рівних умов оптимальна температура охолоджуючої ванни знижується зі збільшенням діаметра псевдоожіжаемих частинок.
На підставі отриманих результатів в 1965 р був виконаний технічний проект 24-ниткового агрегату для патентування дроту з нагріванням і охолодженням її в киплячому шарі.
Згодом на базі цих розробок Гіпрометіз (Ленінград) спільно з нами виконав робочий проект агрегату, представлений на рис. 68. Він розрахований на патентування сталевого дроту діаметром 1,6-5,5 мм, що рухається безперервно в 24 нитки з кроком 28 мм зі швидкістю 10-36 м / хв (замість 6-20 м / хв на існуючій установці). Загальна довжина агрегату по осях складає 9,17 м (існуюча установка мала довжину 22 м).
Агрегат складається з печі для нагріву дроту (довжиною в світлі 3,4 м) і камери охолодження (довжиною 4,6 м і шириною 928 мм), розділених перегородкою. Температура киплячого шару в печі прийнята рівною 950 ° С, дріт на виході з печі нагрівається до цієї ж температури. Температура в камері охолодження прийнята рівною 60-450 ° С в залежності від діаметра дроту (при більшому перетині вона повинна бути нижчою). На виході з агрегату дріт охолоджена до 120-430 ° С.
Псевдозрідженим шар утворюється частинками корунду розміром 100 мкм. У печі передбачені завантажувальні люки та пристрої для вивантаження корунду. Висота щільного шару корунду прийнята рівною 470 мм над рівнем отворів ковпачків. Дріт в агрегаті рухається на висоті 270 мм над рівнем отворів ковпачків і підтримується від провисання поперечними перегородками.
Двоступенева спалювання природного газу, необхідне для створення безокисного атмосфери, здійснюється тільки в тій частині печі, де температура дроту перевищує 600 ° С і можливо її інтенсивне окислення - в так званій II зоні печі, що складається з трьох секцій ковпачків. Ковпачки розташовані у всіх зонах печі з кроком 100 X 90 мм. Вторинне повітря подається тут через ряд труб з отворами в горизонтальній площині, розташованих на висоті 470 мм над газорозподільної гратами з кроком 320-400 мм. У I (по ходу дроту) зоні печі, що складається з трьох секцій по ширині, газ спалюється за одноступеневою схемою. Тут дріт порівняно холодна і практично не відбувається інтенсивного окислення її продуктами повного згоряння газу при спалюванні його з а в = 1. Ця вхідна частина печі (довжиною 1 м) розширена для того, щоб можна було підвести більшу кількість тепла до дроту на малій довжині. Завдяки цьому вдається зменшити теплове навантаження решти печі, т. Е. Скоротити кількість що подається тут газо-повітряної суміші, і знизити швидкість псевдоожиження до значень, досить далеких від швидкості витання часток.
Для отримання термодинамічно рівноважних неокисляющих продуктів згоряння в зоні руху дроту (температура> 600 ° С) спалювання газу здійснюється з недоліком повітря (при а в = 0,4) в присутності каталізатора ГИАП-3, завантаженого в касети з подушкою з інертних куль там, запобігає його зауглерожіваніе. У I зоні печі довжиною 1 м каталізатор відсутній.
При патентування дроту великого перерізу з камери охолодження потрібно відводити тепло. З цією метою тут під рівень киплячого шару введені змійовики з циркулюючої по них холодною водою. Оскільки за даними наших лабораторних досліджень впорскування води безпосередньо в шари дає ще кращі ефект охолодження, були встановлені також форсунки для розбризкування води з метою перевірки працездатності випарного охолодження в промислових умовах. Крок між ковпачками в камері охолодження дорівнює 70-75 мм. Рівні киплячих шарів в обох камерах однакові. Для повернення частинок корунду, яких віднесло дротом з печі в камеру охолодження, в перегородці між цими камерами виконані похилі канали.
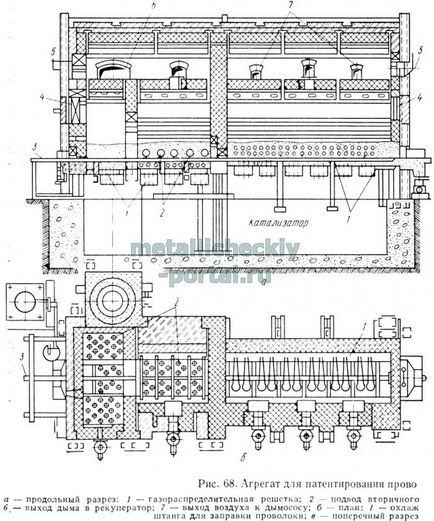
Підведення псевдоожіжающего агента в камерах здійснюється секціями рівномірно по ширині і довжині. Місця проходу дроту через зовнішні стіни агрегату ущільнені подачею стисненого повітря, що перешкоджає просочуванню частинок корунду назовні. За проектом кожну нитку дроту встановлюють на місце спеціальним штанговим заправних пристроєм, необхідним для протягання дроту від передньої стіни агрегату до задньої; потім нитка переміщується вбік по заправних щілинах і ставиться в певний гніздо. І піч, і камера охолодження виконані з двома склепіннями, простір між якими є газоходів.
Що йдуть з печі гази надходять в радіаційний рекуператор, що забезпечує підігрів повітря, що йде потім на вторинне дуття печі і псевдозрідження в камері охолодження, до 370-510 ° С. Охолоджені гази, що йдуть відсмоктуються димососом, в результаті чого всередині агрегату в просторі над киплячим шаром утворюється розрідження , що усуває можливість вибивання газів в атмосферу цеху.
Для регулювання основних процесів, автоматичної підтримки режиму роботи і контролю за режимом агрегат забезпечений необхідними приладами.
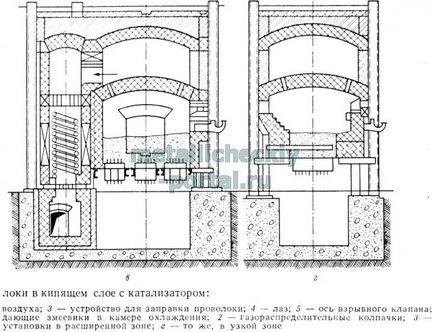
При монтажі агрегат обладнали відповідними намотувальним і розмотувальний пристрій, розрахованими на 20 ниток, 5 ч. Оскільки до моменту проведення випробувань ще не були замінені ковпачки в бічних секціях першої (розширеної) зони, ці секції були закладені цеглою, а дуття на них - відключено. В результаті зменшення теплової потужності випробування проводили при швидкості дроту 14,8 м / хв.
Опір решіток в першій і другій зонах становило відповідно 13,4 і 11,3 кН / м 2 при опорі киплячого шару -0,6 кН / м 2.
Результати випробувань наведені нижче. З них видно, що навіть при цих несприятливих по продуктивності умовах к. П. Д. Печі склав 23%, що перевищує к. П. Д. Звичайних патентіровочних печей, хоча ще й не досягає розрахункового (40%). Загальний енергетичний к. П. Д. З урахуванням споживання електроенергії повітродувкою і димососом (10 кВт на камеру нагріву) становить 22,1%.
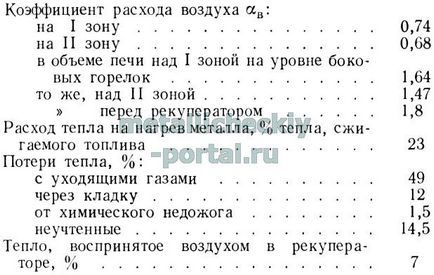
Великі втрати з газами, що, істотно перевищують розрахункові, пов'язані з великими присосами (під час випробувань був відкритий люк). Зменшення значення а в в обсязі печі до 1,1-1,15 дозволить збільшити к. П. Д. Печі до 26%.
Тепло гарячого повітря в к. П. Д. Не включене, оскільки його або використовували для псевдоожиження в камері охолодження, або виводили в атмосферу. При використанні цього тепла рекуператор дозволяє економити 7% палива. У всіх описуваних дослідах в піч і камеру охолодження завантажували корунд (частинки діаметром відповідно 200 і 100 мкм). Режими підбирали, як зазначено вище, при роботі на одній-трьох нитках.
З табл. 23 видно, що при всіх випробуваних режимах відпалу стали 1Х18Н1 ВІД наклеп знімається, межа міцності обпаленого дроту нижче 80 кгс / мм 2. що задовольняє вимогам, що пред'являються. Спеціальні випробування по ГОСТ 6032-58 показали, що у всіх випадках межкристаллитная корозія в отожженной дроті була відсутня.
Мікротвердість, заміряна на приладі ПМТЗ при навантаженні 0,1 кгс, зменшувалася зі збільшенням часу витримки в киплячому шарі, але при всіх витягах була вище, ніж при нагріванні в соляній печі протягом 40 хв через менший часу відпалу.
Випробування, проведені з метою оцінки запасу пластичності, показали, що дріт, відпалений в киплячому шарі при швидкостях 14,8 і 7,0 м / хв, так само як і дріт, відпалений в соляній ванні, витримала волочіння без руйнування до сумарного обтиску 96 , 4% (до 0,48 мм). Кілька меншим запасом пластичності характеризується дріт, відпалений при швидкості 28,8 м / хв. Вона протягнута до діаметра 0,51 мм (обтиснення 94,6%).
Мотки дроту, відпаленого в киплячому шарі, після звичайної підготовки поверхні до волочіння (була лише виключена операція розпушування окалини в розплаві каустичної соди), надходили в цех на волочіння по звичайному маршруту з послідовним зменшенням діаметра (мм): 2,50-2,05 -1,83-1,60-1,38- 1,20 зі швидкістю 120 м / хв. Волочіння проходило без особливих ускладнень.
У процесі первинної наладки було також здійснено патентування 13 ниток дроту зі сталі 60 діаметром 3,2 мм.
