У більшості сучасних машин зносу піддаються поверхні, що труться деталей, (наприклад, зуби шестерень редуктора, направляючі і повзуни, шийки колінчастих валів двигунів, внутрішня поверхня циліндрів двигунів внутрішнього згоряння і т. Д.), Тому що сполучаються поверхні, що труться деталей повинні бути більш стійкими, ніж вся деталь, до дії високих температур, тертю, корозії і т. д.
Існують різні способи поверхневого зміцнення деталей, підвищення їх корозійної стійкості і зниження тертя сполучених поверхонь, що труться. До них відносяться: поверхнева термічна обробка, легування поверхні деталі наплавленням сплавів, що відповідають необхідним вимогам, гальванічне нанесення на поверхню деталі антикорозійного покриття і т. Д. Одним із способів легування поверхні деталі або її елементів є Електроіскрове легування, яке супроводжується різними фізико-хімічними перетвореннями поверхневого зміцненого шару деталі. Воно дозволяє підвищити зносостійкість і твердість, жаростійкість, корозійну стійкість поверхонь деталей і знизити їх коефіцієнт тертя, а також провести ремонт і відновити розміри зламаним деталі, надавши її поверхневого шару нові властивості.
Сутність процесу електроіскрового легування полягає в перенесенні матеріалу ЕІ, що відповідає певним вимогам, на оброблювану поверхню деталі іскровим електричним розрядом. Цей спосіб забезпечує міцне зчеплення вводиться легуючого матеріалу з поверхнею деталі; він простий у виконанні.
При електроіскровому легировании діють закони і процеси, описані в гл. I, але в якості робочого середовища використовується повітря або безокисного газове середовище (аргон, гелій, водень). Розплавлені частинки анода, викинуті в міжелектродному простір, не виносяться робочим середовищем, а осідають на поверхні катода. Як і всякий новий технологічний процес, Електроіскрове легування має свої особливості, які ретельно вивчаються. Процес електроіскрового легування можна представити в наступному вигляді.
Якщо до електродів, один з яких легуємі деталь (катод), а інший - легуючий метал (анод), докласти імпульсна напруга і звести електроди до появи іскрового розряду, то між анодом і катодом потече імпульсний струм великої щільності. Внаслідок цього в точці іскрового розряду на поверхні електродів (переважно на аноді) метал розігрівається і частково випаровується. Краплі розплавленого металу з анода прямують до поверхні катода під дією електромагнітного поля. Після закінчення дії імпульсу струму рух не припиняється і краплі металу досягають поверхні катода. Досягнувши поверхні катода, розплавлені частинки анода впроваджуються в розплавлену лунку на поверхні катода і змішуються з металом катода, а частково осідають на кромці лунки і приварюються до неї. Якщо переміщати анод з якоїсь лінії, то отримаємо ряд лунок зі зміненим складом металу, т. Е. З новими сплавом і структурою. Щоб отримати порівняно гладку зміцнену поверхню, анод потрібно переміщати щодо катода за час паузи між імпульсами, яке за тривалістю одно. 0,01 с, не більше ніж на 1/4 діаметра лунки. В цьому випадку відбувається необхідне перемішування і взаємне проникнення розплавленого металу обох електродів один в одного і поліпшення якості обробленої поверхні.
Крім чисто механічного перемішування частинок розплавленого металу обох електродів під дією високих температур і тиску, що розвиваються в каналі розряду, в поверхневих шарах електродів відбуваються і дифузійні процеси. Процес легування протікає в газоподібному середовищі, тому розплавлені частинки на своєму шляху вступають у взаємодію з цим середовищем і утворюють зміцнюючої шар, що відрізняється своїми фізико-хімічними властивостями від властивостей легирующего і легованих металів.
Дуже цінним властивістю електроіскрового легування є те, що воно забезпечує дуже міцний зв'язок зміцненого шару з легованих металом. Проведені дослідження зміцнених деталей при знакозмінних навантаженнях і температурах показують, що зміцнений шар не відшаровується навіть в разі нанесення покриття КАРБІДНИЙ матеріалами (наприклад, карбідом вольфраму або металокерамічними сплавами). Це пояснюється тим, що між зміцненим шаром і легованих металом є дифузійна зв'язок. Під дифузією розуміється перемішування або проникнення однієї речовини в іншу за рахунок теплового руху молекул контактируемих речовин.
Як легирующего матеріалу використовуються різні карбідні і боридних з'єднання тугоплавких металів, які отримують, як правило, металокерамічним методом. Карбідні і боридних з'єднання мають малу хімічну активність, а тому при їх застосуванні не пред'являється високих вимог до робочого середовища. Вони утворюють хороше покриття, але з порівняно поганою якістю поверхні, і тому деталі, що працюють на тертя, необхідно шліфувати. Деталі, леговані карбидами і боридами, мають високу зносостійкість і твердістю.
Для легування рідше застосовуються: вольфрам, молібден, реній і хром. Якщо необхідно на деталь або елементи деталі нанести антифрикційний шар, який, знижуючи коефіцієнт тертя поверхонь, збільшує довговічність і надійність роботи деталей, то для легування застосовують: олово, свинець, вісмут, індій, графіт. Ці матеріали легко окислюються, а тому легування виробляють в нейтральних газах.
Корозійну стійкість деталі можна підвищити, зробивши її легування графітом, кремнієм, алюмінієм або ферохрому.
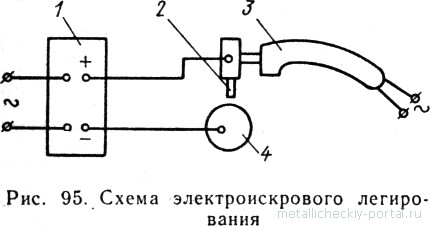
Устаткування для електроіскрового легування. На рис. 95 приведена схема установки для ручного електроіскрового легування; вона включає в себе: генератор імпульсів 1, електромагнітний вібратор 3, легуючий електрод 2 і легованих електрод 4.
Для стійкого здійснення процесу легування необхідно періодичне контактування з певною частотою легирующего електрода 2 з легованих електродом-деталлю 4. Таке контактування забезпечує електромагнітний вібратор 3 (є й інші конструкції вібраторів). Експериментально отримані найкращі результати в діапазоні частот контактування від 100 до 400 Гц. Збільшення частоти в цьому діапазоні дозволяє збільшити продуктивність процесу. Подальше підвищення частоти помітно погіршує якість поверхні.
Контактування легирующего електрода з легованих металом (деталлю) досягається тим, що легуючий електрод закріплюється на якорі електромагніта або на поворотній голівці (в останньому випадку на голівці закріплюється кілька електродів, але під різними кутами).
На рис. 96 приведена найпростіша конструкція робочого органу з електромагнітом. Легуючий електрод 1 закріплюється на електродотримачі 2, до якого проводом 5 підводиться імпульсна технологічне напруга від генератора. Джерелом коливання служить електромагніт 4. Для збудження коливання електродотримача на ньому встановлена трикутна феромагнітна вставка якоря 11, а сам Електродотримачі одним своїм кінцем вільно підвішений на осі 10. Тягове зусилля електромагніта регулюється гвинтом 3. Харчування до електромагніту підводиться проводом 6 від спеціального джерела живлення. Вся система підвішується за допомогою кронштейна 7 до рукоятки 9 і закривається кожухом 8.
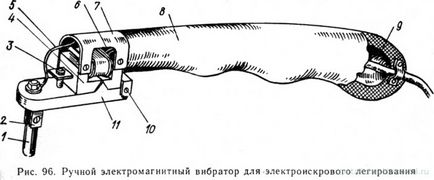
Принцип дії робочого органу з електромагнітом (зустрічаються й інші назви: збудник або вібратор) заснований на періодичному тяжінні феромагнітних тіл, поміщених в змінне магнітне поле. Під дією змінного струму, підведеного до електромагніту, до нього починає притягатися феромагнітна вставка якоря. При зменшенні напруги (синусоїда проходить через нульове значення) Електродотримачі під дією пружини повертається у вихідне положення. Електрод буде коливатися з подвоєною частотою мережі, т. Е. З частотою 100 Гц. Якщо необхідно отримати частоту більше, ніж 100 Гц, то застосовують спеціальні джерела живлення.
Періодичне контактування легирующего електрода з деталлю можна отримати за допомогою обертових багатоелектродних головок. Роз різні конструкції багатоелектродних головок для еластичних і жорстких легуючих електродів (в останньому випадку електрод закріплюється на корпусі за допомогою гнучкого пружного елемента).
Багатоелектродного обертається головка складається з багатоелектродного власника, токоподводящих щіток, еластичної муфти; для обертання багатоелектродного держателя застосовується електродвигун, але можна використовувати і пневматичні турбинки. Всі елементи монтуються в корпусі, виготовленому з пластику, який з'єднується з рукояткою. Весь робочий орган закривається захисним кожухом. Процес легування за допомогою багатоелектродного обертається головки дещо відмінний, ніж при роботі з вібруючим електродом. При тангенціальному зіткненні електрода з деталлю відбувається «розмазування» розплавленого легирующего металу по поверхні деталі, що сприяє зниженню шорсткості поверхні легування. Потрібно відзначити, що за допомогою багатоелектродного обертається головки легко можна механізувати процес легування. В даний час вже розроблені установки механізованого легування.
Генератори імпульсів для електроіскрового легування. Для процесу електроіскрового легування розроблені і виготовляються спеціальні напівпровідникові генератори уніполярних імпульсів, але на підприємствах ще застосовуються і інші типи генераторів (наприклад, релаксаційні генератори).
Дослідним заводом Інституту прикладної фізики АН МолдССР випускаються малими серіями установки для легування, основні технічні характеристики яких наведені в табл. 18.
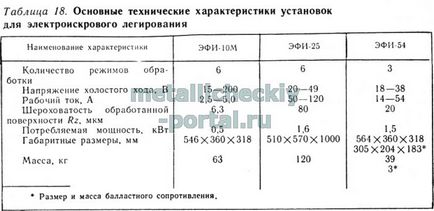
Установка настільного типу ЕФД-54 оснащена двома електромагнітними ручними вібраторами (великим і малим) і багатоелектродного обертається головкою ручного виконання. Установка призначена для нанесення благородних металів на поверхні деталей електричних апаратів з метою поліпшення їх комутаційних властивостей.
В установці ЕФД-25 є ручний електромагнітний вібратор; вона застосовується для легування великих деталей машин, а також для відновлення розмірів зношених деталей.
Установка ЕФД-10М виготовлена в настільному виконанні і оснащена ручним електромагнітним вібратором. Вона використовується для легування і відновлення розмірів зношених деталей машин.
Технологія електроіскрового легування. Технологічні характеристики процесу електроіскрового легування, як і при ЕЕО, в значній мірі залежать від обраних електричних режимів обробки, т. Е. Від величини енергії, що виділяється в міжелектродному проміжку, і від частоти проходження імпульсів. Інтенсивність процесу електроіскрового легування, т. Е. Кількість матеріалу, що переноситься на оброблювану поверхню в одиницю часу, залежить від поєднання якостей матеріалів електродів, а також легирующего і легованих матеріалів.
Великий вплив на процес легування надає температура нагріву електродів, тому грубі режими обробки з великою енергією в імпульсі застосовуються в тому випадку, коли маса деталі більше 0,5 кг.
За енергії, що підводиться імпульсів Електроіскрове легування умовно поділяється на чистове і грубе. Якщо необхідно отримати високу якість поверхні і наноситься шар невеликий, то обробку ведуть на чистовому режимі. Грубі режими з великою енергією в імпульсі застосовують, коли допустима значна шорсткість поверхні і легованих матеріал не схильний до утворення тріщин, а хімічна активність легирующего матеріалу невелика.
Вибір режиму легування для різних сполучень матеріалів проводиться досвідченим шляхом залежно від фізико-хімічних вимог, що пред'являються до обробленої поверхні, її шорсткості, пористості, а також товщини нанесеного шару. Стабільність процесу ручного легування в значній мірі залежить від досвіду оператора, так як встановлений режим може бути легко порушений неправильним вибором тиску легирующего електрода на деталь. Щоб забезпечити стабільність процесу легування, необхідно стежити за величиною робочого струму і підтримувати тиск легирующего електрода в заданих межах. Зі збільшенням енергії імпульсу (робочого струму) зростає товщина шару, що наноситься, збільшується глибина термічного впливу і погіршується якість легованої поверхні, з'являються прижоги, порушується і суцільність нанесеного покриття.
Товщина нанесеного шару при електроіскровому покритті невелика і різна для різних сполучень легуємі і легуючого матеріалів і для різних режимів покриття. Вона коливається від одиниць мікрометрів на чистовому режимі до 1-2 мм - на грубому.
Рівномірність покриття залежить від рівномірності переміщення легирующего електрода по легуємі поверхні деталі і стабільності протікання процесу легування.
Під сплошностью (щільністю) шару розуміється відсутність в зміцненому шарі раковин і різних мікропорожнеч. Вона знижується при нерівномірному покритті, при наявності на поверхні окисних плівок і значної шорсткості зміцнюючих поверхні. Шорсткість легуємі поверхні повинна бути не більше Rz = 6,3 мкм. При чистовому легировании забезпечується висока суцільність покриття, а зі збільшенням енергії імпульсів вона зменшується і збільшується кількість раковин.
Поверхні після легування мають ту ж структуру, що і при ЕЕО. Шорсткість поверхні залежить від енергії імпульсів і ерозійної стійкості легуємі і легуючого матеріалу. Чим вище ерозійна стійкість матеріалів і менше енергія імпульсів, тим краще якість обробленої поверхні. Мінімальна шорсткість зміцненої поверхні знаходиться в межах Rz = 2,5-4 мкм.
Для електроіскрового легування, з метою надання елементам поверхні деталі або всієї поверхні деталі необхідних фізико-хімічних властивостей, застосовують різні композиції твердих сплавів, наприклад, ВК-2, ВК-3, Т15К6, Т30К4, диборид титану, карбіду хрому, титану і ніобію, сплави К.БХ і СНГМ; а також метали - вольфрам, хром, молібден, кадмій, берилій, срібло, золото та ін.
Вибір необхідного режиму легування виробляють при обробці зразків обраним легирующим матеріалом. Зразки зважуються до легування і через короткі проміжки часу (одна - три хвилини) в процесі легування виробляють повторні зважування з метою визначення приросту і товщини легирующего шару, а також необхідного часу легування. Якість легирующей поверхні і її суцільність контролюються візуально за допомогою лупи шестиразового збільшення.
Якщо легуванню підлягає партія деталей з однорідного сплаву, то рекомендується побудувати таблицю або графік питомих приростів легуючих шарів в залежності від часу легування для різних режимів і встановити оптимальний час обробки на кожному з режимів. Практично якість легування гарантується точним дотриманням електричного режиму легування і часом легування.
Раніше наводився перелік матеріалів, що застосовуються при легуванні. Однак практично доводиться мати справу з таким поєднанням легуємі і легуючого матеріалу, яке тільки за певних умов забезпечує необхідну якість покриття, -а дуже часто легуючий матеріал зовсім не осідає. Залежно від конкретних умов легування застосовують різні технологічні прийоми, що забезпечують необхідні кінцеві результати. Наприклад, при легуванні сталей вольфрамом відбувається часте приварювання анода і катода, в результаті чого поверхня виходить нерівною і горбистою. Усунути приварювання можна попередніми легированием вуглецем кожного квадратного сантиметра поверхні протягом 1 хв (для установки ЕФД-10М).
Доводиться наносити перехідний шар, коли обраний матеріал анода не осідають на легуємі металі. Наприклад, при легуванні алюмінієвих сплавів карбідом вольфраму спочатку наносять шар нікелю, а потім на шар нікелю - карбід вольфраму. При легуванні не рекомендується робити багаторазові проходи по одному і тому ж місцю, так як після досягнення певної товщини легирующего шару приріст зменшується і починається з'їм нанесеного шару. На різних режимах кількість максимальних проходів коливається в межах чотирьох - шести.
В процесі легування необхідно стежити за температурою нагріву анода і не допускати його перегріву.