Технологія виробництва комбікормів являє собою сукупність операцій, послідовне виконання яких дозволяє отримати з кормової сировини, значно відрізняється один від одного по комплексу фізико-механічних властивостей, поживності, хімічним складом відповідно до рецептури корм із заданими параметрами. При цьому кінцевий продукт у вигляді комбікорму враховує вид, стать, вік, стан і мета годівлі сільськогосподарських тварин.
Комбікорми готують при строгому дотриманні режиму роботи обладнання відповідно до зоотехническими вимогами нормативних документів, затверджених для державних підприємств Мінсільгосппродом або за його дорученням спеціальними лабораторіями та установами.
Структура комбікормового виробництва передбачає основні і допоміжні процеси. До основних процесів відносять процеси, безпосередньо пов'язані з перетворенням вихідної сировини в комбікорм. Допоміжні процеси безпосередньо з виробленням комбікормів не пов'язані. До них відносять: транспортування, приймання, розміщення і зберігання сировини; зберігання і відпуск готової продукції; переробку відходів основного виробництва і т. п.
Приготування комбікормів включає наступні операції: прийом, зважування та зберігання сировини; очистку сировини від сторонніх домішок; лущення вівса і ячменю; влаготерміческая обробка зерна, дроблення зерна та інших компонентів; сушку і подрібнення мінеральної сировини; підготовку суміші мікродобавок з наповнювачем; введення в комбікорми рідких добавок; дозування компонентів відповідно до рецептами; змішування компонентів; гранулювання або брикетування сумішей; облік і видача комбікормів.
Існує кілька принципів побудови технологічного процесу на комбікормовому заводі.
Послідовно-паралельна підготовка всіх компонентів і одноразове дозування. Компоненти до дозування готують окремо, в одних лініях послідовно, а в інших - паралельно. Розміщують їх в наддозаторний бункерах (рисунок 1). Цей спосіб іноді називають класичним, поширений він у багатьох країнах. Відрізняється великою кількістю наддозаторний бункерів, здатних вмістити запас компонентів на 8. 36 год роботи вузла основного дозування. Підготовчих ліній в цьому випадку від 10 до 12 і більше, комунікації - протяжні. Основний алгоритм роботи можна сформулювати так:
- необхідність постійного заповнення всіх наддозаторний бункерів вихідними компонентами на поточну вироблення згідно виконуваного рецептом;
- паралельна підготовка додаткових компонентів під наступну партію (рецепт) комбікормів, щоб звести до мінімуму втрати часу при переході з одного рецепта на інший.
До основним недоліком класичного принципу побудови технологічної схеми слід віднести великі витрати часу на підготовчі операції на початку зміни, якщо наддозаторний бункера були порожніми. Крім того, при проведенні змінних (декадних) зачисток дуже складно врахувати масу залишків сировини в бункерах. Тому зачистку виробничого корпусу проводять один раз на рік.
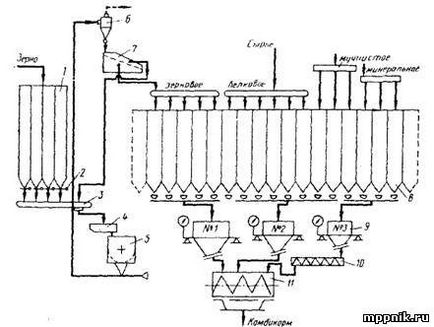
1 - силосний корпус зернової сировини; 2 - засувка; 3 - ланцюговий конвеєр; 4 - магнітний сепаратор; 5 - молоткова дробарка; 6 - циклон-разгрузітель; 7 - просівають машина; 8 - наддозаторний бункера; 9 - багатокомпонентний ваговий дозатор; 10 шнек; 1 + 1 - змішувач порційного дії.
Малюнок 1 - Класична технологічна схема:
Класичні схеми через численні паралельних технологічних ліній насичені основним, транспортним і допоміжним обладнанням, в тому числі аспіраційних, робота якого вимагає великих витрат енергії.
Формування попередніх сумішей зернового і білково мінеральної сировини з повторним дозуванням. Кожна з сумішей обробляється в своєму технологічному потоці. При використанні цього принципу можуть виникати такі варіанти:
створюється одна (дві) зі згаданих сумішей, що пов'язано з конкретними завданнями розвитку виробництва і черговістю проведення робіт з модернізації виробництва;
інші компоненти продовжують готувати на основі першого принципу;
сформовану суміш (суміші) направляють в наддозаторний бункера і далі на повторне дозування через лінію основного дозування - змішування (малюнок 2). В цьому випадку попередні суміші обробляють в потоці (подрібнюють, просівають, відбирають металомагнітні домішки). Місткість наддозаторний бункерів для попередніх сумішей повинна бути не менше 20. 30 т.
До недоліків схем з підготовкою попередніх сумішей та їх повторним дозуванням (якщо при роботі не використовують правила кратності і синхронізацію роботи ліній і інші методи технологічної підготовки виробництва) відносять виникнення неврахованих залишків попередніх сумішей, так званих хвостів. Все це ускладнює перехід на вироблення комбікорми з одного рецепта на інший, а також облік і звітність.
Формування попередніх сумішей зернового, білково-ми- ральним сировини без повторного дозування. Суміш (суміші) формують в суворій відповідності з фактичною місткістю основного змішувача, т. Е. Порційно (рисунок 3).
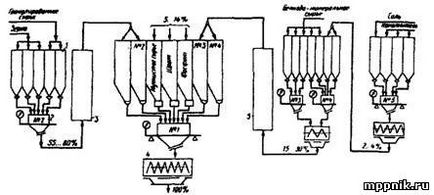
1 - наддозаторний бункер; 2 - багатокомпонентний ваговий дозатор; 3 - обробка попередньої суміші; 4 - порційний змішувач; 5 - обробка попередньої білково-мінеральної сировини.
Малюнок 2 - Технологічна схема з формуванням попередніх сумішей
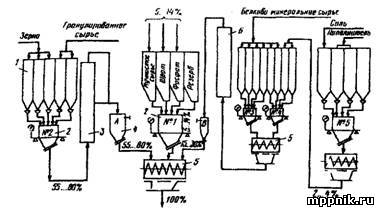
1 - наддозаторний бункер; 2 - багатокомпонентний ваговий дозатор; 3 - обробка попередньої суміші зернового і гранульованого сировини; 4 - бункер для попередньої суміші, що встановлюється паралельно головному вагового дозатора (А - для підготовленого зернового і гранульованого сировини; В - то ж, для білково-мінерального); 5 - порційний змішувач; 6 - обробка попередньої суміші білково-мінеральної сировини.
Рисунок 3 Технологічна схема з формуванням попередніх сумішей з одноразовим дозуванням і порціонної обробкою сумішей:
Обробку в технологічному потоці проводять також порціями, в зв'язку з чим неминуча робота молоткових дробарок в нестаціонарному режимі, з холостим ходом в кожному циклі.
Отриману порцію (або порції) попередніх сумішей минаючи повторне дозування через оперативний бункер малої місткості (2. 3 т) направляють безпосередньо в основний змішувач. При такій побудові технологічного процесу колишня основна лінія дозування спрощується, в ній залишається 2. 3 компонента (мучнистое сировину, шроти, можливо, кормові фосфати) і кілька бункерів, які виходять на один багатокомпонентний дозатор.
Переваги технологічних схем з явно вираженою порціонної роботою - в малій інерційності, швидкої реакції на керуючий вплив, відсутність неврахованих залишків сировини, в можливості переходу на вироблення комбікорми за іншим рецептом з мінімальними втратами часу.
До недоліків таких схем, побудованих за третім принципом, відносять періодичну роботу дробарок на холостому ходу в кожному циклі. Ця обставина підвищує ймовірність виникнення "хлопка" в дробарках, так як відповідно до теорії в кожному циклі двічі, при виході на режим і при сходженні з нього, утворюються вибухонебезпечні концентрації матеріалу, що подрібнюється продукту.
Для усунення цього недоліку можна працювати з неявно вираженими циклами (досвід Раменського комбінату хлібопродуктів), не допускаючи виходу дробарок на холостий хід. В цьому випадку навантаження головного електродвигуна знижується до 30% номінальної, схил компонентів слід за схилом з мінімально можливим інтервалом, а в разі порушення ритму датчики верхнього рівня, вмонтовані в бункера А і Б (див. Рисунок 2), заблокують роботу багатокомпонентних вагових дозаторів № 1 або № 3 і 4. Ситуація, коли в бункерах А і в виявиться по два схилу при добре налагодженому виробництві, може скластися тільки в разі аварійної зупинки однієї з дробарок.
Прямоточний метод. Всі компоненти дозують і обробляють в потоці аж до випуску порції готової продукції. Схема (малюнок 3) максимально прямоточні, розрахована на використання очищеного технологічної сировини. Будується вона зверху вниз, добре вписується в висотні будівлі, відрізняється мінімум підйомів і малими питомими енерговитратами на виробництво 1 т комбікорму. У схемі може бути реалізовано одно- та двоступенева подрібнення; змішувач-усреднітель може бути відсутнім, якщо конструкція молоткових дробарок дозволяє одночасно з подрібненням виконувати і змішування.
Гідність - це повне використання принципу прямоточности в будівлях великої висоти. До недоліків слід віднести необхідність застосування повністю підготовленого, очищеного сировини.
Загальна тенденція в розвитку технології виробництва комбікормів - рух від схем першого принципу до схем четвертого через різні варіанти другого і третього. Оцінним показником у виборі тієї чи іншої схеми слід вважати можливість створення надійного і простого управління технологічними процесами.
При виборі технологічної схеми підприємства потрібно враховувати основні зональні фактори: обсяги і асортимент місцевої сировини, потреба і рецептуру необхідних комбікормів; можливість завезення відсутнього сировини, його вартість і віддаленість виробництва; будівельні та фінансові можливості господарства; вартість будівництва і експлуатації підприємства.
На підприємствах, що працюють на готових БВД, одноразові витрати на 7. 10%, а поточні - на 15. 20% менше, ніж на підприємствах з повною технологічною схемою.
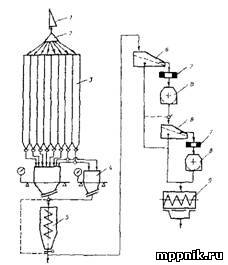
1 - нория; 2 - поворотний круг; 3 - силоси; 4 - багатокомпонентний ваговий дозатор; 5 - змішувач (усреднітель); 6 - просівають машина; 7 - магнітна колонка; 8 - молоткова дробарка; 9 - змішувач порційного дії.
Малюнок 4 Прямоточная технологічна схема
Підприємству в процесі експлуатації з метою вдосконалення технології надається право вносити окремі зміни в схему технологічного процесу при узгодженні з вищестоящою організацією.
Після внесення змін технологічна схема підприємства (цеху) повинна бути розглянута і затверджена вищестоящою організацією. Схема технологічного процесу повинна перезатверджуватися не рідше ніж через 3 роки. При цьому екземпляр технологічної схеми вивішується в цехах і на ділянках підприємства для вивчення і контролю за роботою окремих машин і устаткування.
Організація вироблення комбікормів, білково-вітамінних добавок і преміксів на підприємстві проводиться відповідно до встановленої документацією.