У статті розповідається про технологію виготовлення збройових мисливських стволів.
Частина 1. Технологія виготовлення стовбура
Ймовірно, багато хто погодиться. що головна частина рушниці - стовбури. Адже стріляють саме вони. Ефективність гарматних пострілів викликала у людини бажання зробити маленьку «ручну» гармату. Таку гармату в середині позаминулого століття знайшли в замку Таннеберг в Хессене (Німеччина). Вона була відлита в кінці XIV століття. Стріляти з неї з рук було, звичайно, важко і незручно і незабаром до неї пристосували арбалетного ложу. Виявилося, що по точності стрільби і купчастості нову зброю серйозно поступається хорошому цибулі, хоча по енергії, а значить і пробивний силі, значно його перевершує. Досить швидко з'ясувалося, що зі збільшенням довжини стовбура, постріли стають точнішими. З цього моменту і починається історія вогнепальної зброї.
Сьогодні у нашого «переломного» мисливської рушниці є три головні частини: стовбур (або стовбури, що утворюють стовбурний блок), колодка, ложа.
Стадії згортання трубки простого стовбура. Вгорі - пластина-заготовка для стовбура.
Стовбур надає напрямок польоту дробу або кулі. Чим правильніше і ретельніше він виготовлений, тим краще дробова осип і вище точність.
Колодка замикає казенний зріз стовбурів, служить сполучною елементом між стовбурами і ложею і є в зброю головним інерційним елементом, що поглинає силу віддачі. У колодці монтуються замикають, ударно-спускові і запобіжні механізми.
Ложа забезпечує зручність наведення зброї на ціль, природність прицілювання і пом'якшує дію сили віддачі за рахунок її часткового перетворення на обертальний момент.
Перш ніж розповісти про сьогоднішню технології виготовлення збройових стволів, хочеться познайомити читачів з частиною збройової історії, що стосується вдосконалення виготовлення цієї найважливішої частини зброї. Адже виготовити хороший стовбур - завдання досить важка навіть при сьогоднішньому рівні розвитку машинобудування. Однак наполегливість, старанність і винахідливість наших далеких предків знаходила різні варіанти вирішення цього завдання. Причому рівень якості кращих виробів XVIII століття сьогоднішнім фахівцям видається майже загадковим. Нам хочеться розповісти, яким шляхом майстра минулого створювали чудове зброю, показати деякі його зразки і разом подумати про велич їхнього духу з надією, що це зміцнить і наш власний.
У 1811 році Генріх Аншютц (з добре відомою збройової династії) видав книгу про збройовій фабриці в м Зуль. Він пише про чотирьох типах технологій отримання стовбурних трубок: звичайної, скрученої, навитої і стовбурах з «Дамаска».
Схема отримання скручених стовбурних трубок.
Звичайний (простий) ствол отримували зі смугової заготовки довжиною 32 дюйма (812,8 мм), шириною 4 дюйма (101,6 мм), товщиною 3/8 дюйма (9,525 мм). Після розігріву цю смугу ковальським способом загинали на оправці таким чином, що її поздовжні кромки прилягали один до одного встик, паралельно осі каналу ствола. Цей стик зварювався ковальським методом і ретельно проковувати. Є безсумнівні вказівки, що обидві довгі сторони прямокутної заготовки іноді зганялися «на вус» і зварювали НЕ встик, а внахлест. Після зварювання та охолодження стовбури проходили чотиригранної розгортку, обточували на токарному верстаті зовнішню поверхню, яку потім шліфували вручну на великому колі з м'якого пісковика діаметром 1,75 м. З казенної боку в стовбур вкручувалася гвинтова заглушка, яка іноді теж проварюють. Звичайно, «заглушалися» стовбури всіх дульнозарядних рушниць, незалежно від технології їх отримання.
Скручений стовбур. Зварений шов в звичайному стовбурі, що розташовувався паралельно осі стовбура, часто був місцем руйнування при стрільбі. Щоб уникнути цього, простий зварений стовбур починали повторно нагрівати в центральній частині і скручували уздовж осі по всій довжині так, щоб зварений шов мав форму гвинтової лінії. Цей прийом робив шов значно менше навантаженим при пострілі.
Навитої стовбур отримували шляхом поступового навівання сталевої штаби на оправлення у вигляді стрижня або труби. Гвинтоподібний зварений шов послідовно проковували ковальським молотом.
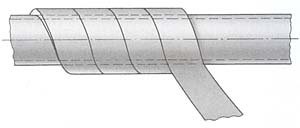
Принцип отримання навитих стовбурів.
Дамаску стовбури.
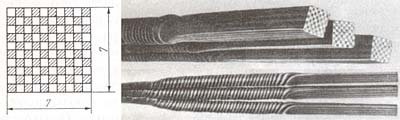
Стрімкий розвиток металургії в кінці XIX століття призвело до появи вуглецевих сталей з високими механічними властивостями. Перспективність їх використання для виготовлення стовбурів здавалася очевидною. Однак ще в першій чверті XX століття багато зброярі Європи продовжували робити стовбури по «дамаським технологій». Сьогодні необхідно розуміти, що такі стовбури, хоча і є пам'ятками фантастичного ретельності зброярів попередніх поколінь, але все ж поступаються за всіма найважливішими показниками сучасним легованим стовбуровим сталей. Нагадаємо нашим співвітчизникам, що сталь 50А і навіть 50РА, з якої і в Тулі, і в Іжевську роблять сьогодні стовбури, долегованим стовбуровим сталей не належать. І ще про дамаських стовбурах. Через сто і більше років після виготовлення досить імовірно, що ковальське зварювання елементів може значно зруйнуватися і міцність стовбурів може виявитися недостатньою для забезпечення безпеки стрільби. Будьте дуже обережні при бажанні постріляти зі старого рушниці з дамаської стволами.
Введення до складу вуглецевої сталі хрому, ванадію, нікелю, кремнію, марганцю та інших елементів привело до значного підвищення найважливіших властивостей стовбурних сталей - пружності, міцності при розтягуванні, поверхневої твердості, корозійної стійкості. Більш того, ці технології дозволяють отримувати стали з наперед заданими властивостями. Все це дозволило перейти до виготовлення однорідних заготовок для рушничних стовбурів. Цей процес почався ще в останній третині XIX століття і близько півстоліття співіснував з «дамаської» технологією.
Частина 2. Розвиток технології виготовлення рушничних стовбурів.
Новий етап починається з відмови від стовбурів, одержуваних з смуг, і переходу до стовбурів, канал яких утворювався глибоким свердлінням. Ця технологія незрівнянно більш продуктивна, але для її реалізації потрібно було вирішити ряд серйозних проблем, розповісти про які нам хочеться, щоб сучасні читачі могли уявити, якою ціною виходили рушниці, що володіють чудовим боєм. Нова технологія виготовлення стовбурних заготовок починається з кування, яка не тільки надає заготівлі стовбура зовнішню форму, близьку до готового стовбура, але і забезпечує поліпшення структури стали завдяки зменшенню її зернистості. Зазвичай для поковки відрізають шматок круглого прокату діаметром близько 50 мм. Довжина цієї заготовки залежить від майбутньої довжини стовбура. Шматка довжиною 320 мм вистачає, щоб з неї витягнути куванням заготовку довжиною 750 мм із середнім діаметром 30 мм. Звичайно, після кування діаметр заготовки в області патронника помітно більше, ніж у дульного зрізу. Тут слід зазначити, що при звичайній куванні близько 15% стали йде в окалину. Ковалі кажуть, що метал «чадіють».
Рихтування ствольної заготовки
Для зняття внутрішніх напружень в викував заготовках їх нагрівають до (приблизно) 850-860 градусів і витримують близько півгодини. Точні параметри нагріву залежать від марки ствольної стали і товщини заготовки. Завдання зняття внутрішніх напружень дуже важлива для всіх стадій виробництва стовбурів. Особливо важливо, щоб не було напруги в готової ствольної трубці, призначеної для освіти стовбурних блоків з двох або більше стовбурів.
Справа в тому, що пайка м'якими і особливо твердими припоями вимагає значних успіхів і асиметричного нагрівання стовбурів. Неоднорідне відбувається і охолодження спаяного блоку. Наявність внутрішньої напруги призводить до помітної деформації стволів після пайки. Більш того, високий розігрів внутрішньої поверхні стовбурів при стрільбі, особливо інтенсивної, може викликати необоротну деформацію стовбура, якщо в ньому залишалися напруги. Після нормалізації проводять загартування. Суть її полягає в отриманні оптимальних властивостей за рахунок формування тонкої структури металу.
Будь-яка сталь є складною в фазовому відношенні системою, що містить як мінімум дві кристалічні модифікації чистого заліза, карбід заліза, карбіди металів-домішок і тверді розчини деяких з цих компонентів один в одному. Температурна обробка змінює фазовий стан цієї складної системи і розміри окремих фаз, що дуже істотно впливає на експлуатаційні властивості.
Загартування полягає в рівномірному розігріві деталі до температури, яка залежить від рецептури стали, з якої вона виготовлена. Заготовки із сталі Ск 65, яку в Німеччині часто використовують для стовбурів, нагрівають до 840 градусів. Після цього її опускають в масло, що має кімнатну температуру. Потім заготовку «відпускають», для чого її прогрівають в муфельній печі близько 4 годин при температурі 580-600 градусів. Такої складної термообробкою можна значно впливати на твердість, в'язкість, пружність і межа міцності при розтягуванні.
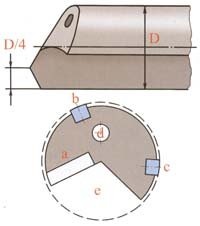
Збройне свердло:
а - ріжучий пластина,
b і з - напрямні,
d - канал для підведення охолоджуючої рідини,
е - порожнина для видалення стружки
Термічно оброблену заготовку ретельно рихтують. Це роблять, щоб під час свердління, яке відбувається при обертанні заготовки, вона не вібрувала. Рихтують заготовку в горизонтальному положенні при обертанні, коригуючи її форму притискними роликами. Після рихтування заготовку знову піддають нагріванню для зняття внутрішніх напружень, потім торцюють з обох сторін і знімають фаски.
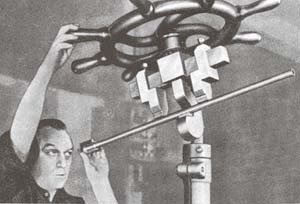
Рихтування стовбура за тіньовими кільцям за допомогою гвинтового преса
Після цього приступають до самого тонкому процесу у виготовленні стовбура - свердління. Глибоке свердління, особливо в довгій заготівлі з низькою поздовжньої стійкістю - особлива пісня. У збройовому справі для цього використовують спеціальні верстати, схожі на токарні. У них закріплена заготовка обертається, а спеціальне свердло рухається поступально. У цьому процесі дві головні проблеми: відведення свердла від осі заготовки і видалення стружки. Першу проблему можна вирішити за рахунок однорідності структури заготовки і відносно невисокою швидкості подачі свердла і швидкості різання, щоб виключити вібрацію заготовки. Зрозуміло, ці обмеження збільшують тривалість свердління. Проблема видалення стружки, яка іноді не тільки псує поверхню каналу, а й заклинює свердло, вирішується спеціальними прийомами. У XIX столітті застосовувалися «рушничні свердла», по конструкції вони були близькі до розгортки, тобто в їх основі була штанга, на всій робочій довжині якої був обраний циліндричний сектор з кутом близько 100 градусів. Конструкція свердла досить проста і добре зрозуміла з креслення. Через невеликий отвір в тілі свердла в зону різання подається охолоджуюча емульсія, яка по жолобку, паралельного осі свердла, забирає з собою утворюється стружку. Такі верстати давно стали багатошпиндельними і досить автоматизованими. Це дозволяє одному робітникові контролювати свердління на декількох верстатах. Цей процес все-таки не гарантував високу ступінь чистоти обробки поверхні каналу ствола. Стружка часто була основною причиною цього. Крім того, продуктивність свердління була невисока.
У 1937 році Бургсмюллер якісно змінив схему свердління. Він запропонував вертикальне розташування заготовок і направле¬ніе свердління від низу до верху для кращого видалення стружки. В якості основи свердла він застосував трубу, на робочій голівці якої були прикріплені три напрямні пластини і приварена одна ріжучий. Процес різання відбувається при охолодженні стисненим повітрям, який подається в зазор між поверхнею свердла і стінками утворюється отвори. Стружка ж зовсім не контактувала зі стінками отвору і разом з повітрям неслася вниз. Значно більший момент опору скручуванню, яким володіла «труба» в порівнянні з профільованої штангою, дозволяє, крім отримання хороших поверхонь, використовувати під час свердління більш високі швидкості різання і подачі.
У 1942 році Байснер удосконалив цей метод. Він повернув свердлильних верстатів горизонтальне положення, запропонував використовувати масло в якості охолоджуючої рідини і вдосконалив свердлильну головку. Масло подавалося під тиском в зазор між свердлом і утворюється циліндричною поверхнею і виносило стружку через центральний канал в спеціальний збірник. Поверхня виходила дуже гладкою в деякій мірі завдяки полированию напрямними. Проте, після свердління канал ствола обробляється розгорткою.
Перед тим як приступити до обробки зовнішньої поверхні стовбура його рихтують: перевіряють прямолінійність осі каналу і при необхідності виправляють її за допомогою гвинтового преса. Перевірку правильності каналу здійснюють за тіньовими кільцям, що кожен мисливець може зробити і сам. А ось процес редагування вимагає не тільки гарного зору, але і великого почуття металу, що приходить тільки з досвідом. Справа в тому, що стовбур має пружність. Тому якщо під навантаженням він випростався, то після її зняття частково повернеться в початковий стан. Досвідчений майстер відчуває, наскільки стовбур потрібно «перегнути», щоб після зняття навантаження він став бездоганно правильним.
Після формування каналу ствола встає чергова непросте завдання: токарно обробити ствол зовні. При цьому головна трудність, щоб центр зовнішньої поверхні точно збігся з центром каналу ствола. Якщо цього не зробити, то ствольна трубка вийде разностенность. Крім того, через велику величини відношення довжини стовбура до його діаметру при токарній обробці поверхні стовбура його необхідно фіксувати двома люнетами, для кожного з яких потрібно попередньо проточити шийки. Для коректного виконання цієї операції на середині довжини стовбура встановлюють спеціальну муфту, що дозволяє правильно утримувати ствол за його необроблену поверхню при проточці шийок для люнетів. Коли шийки проточені, муфту можна зняти і виконати зовнішнє обточування стовбура по копіру. Ці токарні обробки можуть привести до деякої деформації стовбура. Тому стовбур в черговий раз контролюють за тіньовими кільцям і при необхідності рихтують. Чистове обточування і шліфування проводиться після того, як окремо прошліфовивают шийки для люнетів. Заключна стадія виготовлення стовбурних трубок - тонке шліфування, зване в збройовій справі хонингованием.
Істотним прогресом у виготовленні рушничних стовбурів є їх кування на оправці. Звичайно, обладнання для цього процесу коштує недешево. Тому формування стовбурів куванням рентабельно тільки при великих обсягах виробництва. Однак економія коштів і часу виходить теж значна. При виготовленні стовбурів методом ротаційної гарячого кування використовують заготовки довжиною 260-280 мм і діаметром близько 35 мм. У ній свердлом Байснера роблять наскрізний отвір діаметром 20,5 мм. Заготівлю закріплюють на загартованої, ретельно відполірованою оправці, що має форму внутрішньої поверхні готового стовбура. Після електроіндукціонного прогріву заготовки до необхідної температури її подають в зону кування, де вона, обертаючись уздовж своєї осі, проходить під ударами хрестоподібно розташованих молотів. За півтори хвилини заготівля приймає зовнішню і внутрішню форму стовбура з патронником. Загартування після такої проковки не проводиться. Зовнішню форму стовбура доводять токарних обточування і шліфуванням. Канал стовбура начорно проходиться розгортку. Остаточну обробку каналу ствола, включаючи патронник і дульне звуження, проводять після збирання стовбурного блоку.
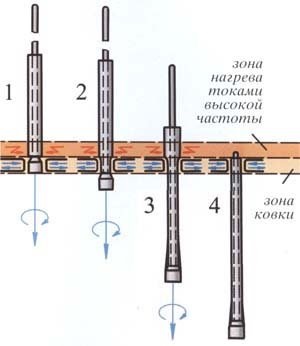
Схема ротаційного кування:
1 - розігрів струмами високої частоти,
2 - початок кування,
3 - процес кування,
4 - закінчення кування
Ще більш прогресивним методом виготовлення стовбурів є холодна кування на оправці. Одне з її переваг в тому, що вона економить близько 15% дорогою ствольної стали, що йде в окалину при гарячої куванні. Крім того, внутрішня поверхня стовбура виходить точною копією оправлення, так що можна отримувати повністю готові стовбури (з патронником, дульним звуженням і нарізами). Поверхня каналу ствола вимагає тільки полірування. До того ж структура холоднокованого стовбура забезпечує йому високі механічні властивості. Правда, холодне кування вимагає більш потужних молотів і більшої тривалості. Вона триває трохи більше трьох хвилин. Зовнішню форму доводять обточування і поліруванням. Перевірку правильності осі каналу проводять і після цієї технології і, якщо є необхідність, рихтують. Завершальною стадією виготовлення окремих стовбурних заготовок є відстріл і таврування.