Технологія термічної обробки металів
Загальні відомості. Пружини і амортизатори відчувають в роботі багаторазові знакозмінні навантаження і після зняття навантаження повинні повністю відновлювати свої первинні розміри. У зв'язку з такими умовами роботи метал, застосовуваний для виготовлення пружин і ресор, повинен володіти, крім необхідної міцності в умовах статичного, динамічного або циклічного навантажень, достатньо хорошої пластичності, високими межами пружності і витривалості і високої релаксационной стійкістю, а при роботі в агресивних середовищах (атмосфері пара, морській воді та ін.) повинен бути також і корозійно-ностойкім.
Не менш важливі для металу пружин і ресор також технологічні властивості - мала схильність до зростання зерна і обезуглероживанию в процесі термічної обробки, глибока прокаліваемость, низька критична швидкість загартування, мала чутливість до відпускної крихкості.
На якість пружин і ресор впливає стан поверхні прутків, дроту і смуг. Наявність зовнішніх дефектів (тріщин, заходів, полон, волосовин, раковин, задирок, втиснула окалини і ін.), А також обезуглероженного шару знижує пружні і циклічні властивості металу. Тому зовнішні дефекти на поверхні прутків і смуг повинні бути видалені зачисткою або шліфуванням, а глибина обезуглероженного шару не повинна перевищувати певної норми, встановленої ГОСТом на рессорно-пружинну сталь.
Для виготовлення пружин застосовують вуглецеві і леговані стали, а для приладів - сплави кольорових металів, головним чином берилієвих бронзу. Ресори виготовляють тільки з легованих сталей.
Замість патентування економічно більш вигідно застосовувати метод деформаційного зміцнення нормалізованої сталі. Даний метод, розроблений на Горьківському автомобільному заводі, полягає в наступному. Дріт, прутки, смуги з сталей 45, 65Г, 50ХГ піддають нормалізації, а потім холодною пластичної деформації волочінням або прокаткою зі ступенем деформації 40-60%. З отриманого напівфабрикату навивкой, штампуванням або вирубкою виготовляють пластинчасті і кручені пружини, ресорні листи, які піддають нагріванню при 280-300 ° С протягом 20-40 хв.
даного методу є також те, що забезпечуються розміри і форма пружних елементів, що особливо важливо для тонких пластинчастих пружин, сильно деформуються при загартуванню. Для усунення викривлення таких пружин необхідно застосовувати при відпустці спеціальні штампи.
Зміцнення загартуванням з наступним відпуском. Для виготовлення пружин, зміцнюючих термічною обробкою (загартуванням і відпусткою), застосовують вуглецеві (65, 75) і леговані (60С2А, 50ХФА, 60С2Н2А і ін.) Стали, для ресор - тільки леговані стали, для пружин, що працюють в агресивних середовищах, - нержавіючі стали 30X13, 40X13, 12Х18Н10Т і ін.
Вуглецеві сталі в зв'язку з їх малою прокаливаемостью застосовують для виготовлення пружин з дроту діаметром до 6 мм. Перевага кременистої сталі в порівнянні з вуглецевої - її підвищена прокаліваемость і більш високі міцність і пластичність. Недоліком цієї сталі є підвищена схильність до утворення поверхневих дефектів при гарячій обробці, обезуглероживанию і графітизації. В результаті обезуглероживания зовнішньої поверхні пружин або ресор різко знижується їх опірність тривалих навантажень. Тому нагрівання пружин і ресор необхідно проводити з запобіганням від зневуглецювання або (для усунення шкідливого впливу обезуглероженного шару) піддавати їх після термічної обробки обдувке дробом.
Широке застосування для виготовлення ресор автомашин і пружин рухомого складу залізничного транспорту мають крем'янисті стали 55С2 (А) і 60С2 (А). Сталь 60С2 (А) застосовують також для виготовлення пружин, що працюють при температурах до 250 ° С. Сталь 70СЗА має високі механічні властивості, але схильна до графітизації.
Марганцева сталь (65Г) в порівнянні з кременистої сталлю володіє деякими особливостями, до яких відносяться отримання менш шорсткою поверхні при гарячій обробці, велика прокаліваемость і менша схильність до зневуглецювання. Недоліками марганцевої стали є підвищена чутливість до перегріву, утворення гартівних тріщин, схильність до відпускної крихкості; застосовують цю сталь для пружин механізмів і машин.
Деталі зі сталі 55ГС перетином до 25 мм мають наскрізну загартування, а тому її застосовують для виготовлення ресор товщиною до 10 мм, циліндричних пружин з діаметром прутка до 25 мм і буферних пружин; ця сталь малосклонна до обезуглероживанию і відпускної крихкості.
Хромомарганцевих сталь (50ХГ (А)) володіє глибокою прокаливаемостью, високою міцністю і щодо малої чутливістю до перегріву; її застосовують для виготовлення пружин і ресор великого перерізу; сталь добре гартується в маслі; недоліком цієї сталі є схильність до відпускної крихкості.
Невелика присадка до хромової сталі ванадію позитивно впливає на структуру і пластичність стали, а також зменшує її схильність до перегріву, внаслідок чого значно полегшується термічна обробка; тому хромованадіевой (50ХФА) і хромомарганцеванадіевая (50ХГФА) стали добре гартуються в маслі і малосклонни до зростання зерна. Застосовують ці стали для виготовлення пружин особливо відповідального призначення, а також ресор легкових автомобілів.
Стали 60С2ХФА, 65С2ВА і 60С2Н2А використовують для великих пружин відповідального призначення. Деталі з цих сталей малосклонни до зростання зерна і прогартовуються в перетинах до 50 мм. Особливо високими якостями володіє нікелькремністая сталь 60С2Н2А, легко Отжигают на структуру зернистого перліту, що має високу пластичність, що не подкалівающаяся при охолодженні на повітрі після гарячої прокатки.
Пружини з хромонікелевих сталей аустенітного класу (12Х18Н10Т і ін.), Зміцнюється холодною пластичною деформацією, після навивки піддають тільки відпустки при 450 500 ° С з витримкою протягом 20-30 хв.
Для підвищення корозійної стійкості та стабільності пружини з нержавіючих сталей після всіх операцій технологічного процесу піддають поліруванню (краще електролітичному) до повного освітлення поверхні. Необхідно враховувати, що при поліруванні діаметр дроту зменшується на 3-10%, що призводить до зниження силових характеристик пружин.
Циліндричні пружини нагрівають в горизонтальному положенні. Для попередження викривлення при нагріванні на поду печі розташовують швелерних балки, на які укладають пружини. Для гарту пружин стиснення застосовують пристосування, показане на рис. 157, що представляє собою сталевий стакан (внутрішній діаметр якого на 0,3-0,4 мм більше зовнішнього діаметра пружини, а висота на 10-12 мм більше висоти пружини) з отвором в дні, рівним середньому діаметру пружини. В пристосування поміщають пружину і завантажують його в піч. Після нагріву до заданої температури і витримки пристосування разом з пружиною виймають з печі і охолоджують в маслі (в горизонтальному положенні при безперервному погойдуванні). Загартовану пружину виштовхують з пристосування, натискаючи на неї з боку отвори в склянці.
Викривлення пружини, отримане при загартуванню (рис. 158, а), можна усунути при відпустці. Загартовану пружину надягають на оправлення і затискають клином (рис. 158, б). В такому стані здійснюють відпуск пружини. Після відпустки на оправці викривлення пружини, отримане при загартуванню, усувається (рис. 158, в).
Для отримання необхідної твердості і правильної форми тонкі пластинчасті пружини для усунення виниклого при загартуванню жолоблення піддаютьвідпустки в штампах на пресі з електропідігрівом. Прес має два штампи - нижній / і верхній 2 (рис. 159). Усередині штампів знаходяться сталеві диски 3 з пазами. Ніхромові нагрівальні елементи з жаростійкої ізоляцією розміщені в пазах дисків 3. Кінці 4 нагрівачів виведені з штампів до щита управління. Для теплостойкости штампи укладені в кожухи з азбестового теплоізоляцією 5. Нижній штамп 1 нерухомий. Верхній штамп 2 за допомогою пневмоциліндра б, керованого краном 7, може переміщатися в осьовому напрямку. Контроль температури здійснюється термопарою 8. Загартовані пружини поміщають на нижній штамп /, притискають верхнім штампом 2 і витримують протягом декількох хвилин при температурі відпустки.
Для виготовлення автомобільних ресор застосовують стали 60С2 (А), 50ХГ (А), 50ХФА, 50ХГФАідр. Ресорні листи нарізають в холодному стані, потім в них пробивають отвори, відтягують кінці і в гарячому стані загинають вушка. Термічну обробку ресорних листів, наприклад зі сталі 50ХГФА, проводять по наступному режиму. Листи завантажують в гартівну газову конвеєрну піч (температура I зони 600-700 ° С, II зони 800-850 ° С і III зони 850-880 ° С). витримку дають
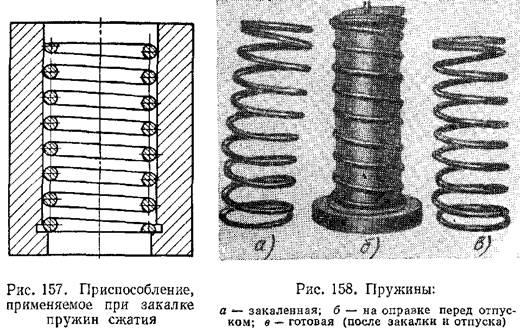
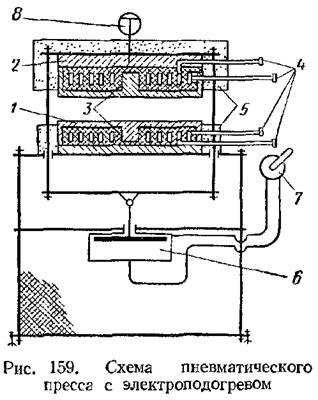
з розрахунку 1,2-1,5 хв на 1 мм перерізу. Після нагріву ресорні листи поміщають в гібоч-но-гартівну машину, в якій проводиться гнучка і гарт з охолодженням в циркулюючому олії (температура масла 40-60 ° С).
Після гарту ресорні листи піддають відпустці в газовій конвеєрної печі при 550-600 ° С з витримкою 40 45 хв. Ресорні листи укладають на конвеєр печі на ребро. Після відпустки ресорні листи надходять на конвеєр охолоджуючого бака. Швидке охолодження водою після відпустки перешкоджає виникненню відпускної крихкості, що не порушує потоку і покращує умови роботи в цеху. Після відпустки ресорні листи піддають дробеструйной обробці, що значно підвищує їх межа витривалості. Залишкові напруги стиснення зовнішніх шарів, викликані обдування дробом, зменшують напруження розтягання в зовнішніх волокнах, збільшуючи довговічність
В процесі термічної обробки контролюють: а) твердість після гарту (одного комплекту через кожні 2 ч роботи) (HRC 50-60); б) прилягання листів ресори в зборі (через кожні 2 ч роботи); в) твердість після відпустки (HRC 40-45).
Для перевірки результатів термічної обробки іноді ресори вибірково випробовують на витривалість.
Крім звичайної гарту ефективні індукційний нагрів пружин і ресор, ізотермічна гарт і особливо термомеханічна обробка.
Зміцнення загартуванням з наступним старінням. Матеріалом, зміцнює загартуванням і старінням, є берилієва бронза. Виготовлені з стрічки (штампуванням, витяжкою, гнучкою і т. П.), Прутків (обробкою на верстатах), дроту (шляхом навивки) деталі перед загартуванням знежирюють в бензині або ацетоні, промивають у холодній і киплячій воді і сушать теплим повітрям або в термостаті при температурі не вище 120 ° С. Підготовлені деталі поміщають в коробки, засипають деревним вугіллям, нагрівають в печі до 760-800 ° с з витримкою 8-15 хв, охолоджують у холодній воді і потім сушать.
Загартовані деталі піддають старінню (дисперсионному твердненню) при 260-400 ° С (в залежності від необхідних властивостей) з витримкою після нагрівання від 1 до 4 год і охолодженням на повітрі.
Щоб уникнути жолоблення старіння деталей проводять в спеціальних пристроях. Після термічної обробки деталі контролюють. Твердість залежно від умов роботи деталей НV 200-400.
Загартуванню піддають також заготовки з подальшим виготовленням з них деталей за наступним технологічним процесом: відрізка або вирубка заготовок; знежирення, промивання, сушіння; гарт; полірування заготовок (при необхідності); виготовлення деталей; знежирення, промивання і сушіння деталей, старіння; контроль.