Технологія переробки нафти і газу. Частина 1
У технологічних схемах різних гідрогенізаційних процесів багато спільних рис. У них можна виділити наступні загальні елементи (рисунок 4.8). Сировина перед нагріванням в теплообмінному і пічному обладнанні змішується з водородсодержащим газом в трійнику змішання. Після виходу з печі газосирьевая суміш (ГСС) направляється в реакторний блок (мо-же складатися з одного або декількох реакторів), в якому здійснюють-ся всі хімічні перетворення. Залежно від глибини перетворення сировини може змінюватися сумарний тепловий ефект реакцій. Тому в неко-торих процесу х, зокрема при гідро крекінгу, потрібно проміжне охолодження продуктової суміші, що досягається подачею холодного ВСГ (квенча) або в реактор поличного типу, або в трубопровід, що з'єднує ре-актори.
Після виходу з реактора газопродуктовий потік (ДПП) охолоджується в теплообмінному обладнанні і потім піддається сепарації. При цьому можуть використовуватися дві технології: холодна або гаряча сепарації. Виокрем-ється в блоці сепарації ВСГ і вуглеводневий газ направляються на мо-нометаноламіновую (МЕА) очистку від сірководню, а рідкі углеводоров-ди - на ректифікацію.
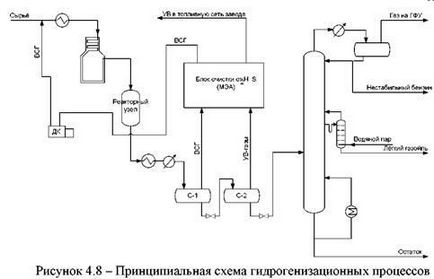
Принцип роботи блоків сепарації за схемою холодної та гарячої сепарації наведено на малюнку 4.9. За першим варіантом ДПП охолоджується в ті-плообменном і холодильному обладнанні орієнтовно до 40 ° С і при тиску на 0,2-0,5 МПа нижче, ніж на виході з останнього реактора, під-Вергал поділу на газоподібну і рідку фази в сепараторі високо -го тиску. Газоподібна фаза - ВСГ, повертається в процес, рідка фаза після скидання тиску надходить в сепаратор низького тиску, де з неї виділяються вуглеводневі гази, що направляються після очищення або в топ-зливи мережу заводу, або на газофракціювання. Тиск в сепараторі низького тиску зазвичай складає 0,8-1,2 МПа.
При гарячої сепарації ДПП після виходу з реактора охолоджується в теплообмінному обладнанні приблизно до 200-245 ° С і при високому тиску-ванні і температурі піддається поділу в гарячому сепараторі. Газооб-різна фаза - суміш ВСГ, газів С1-С4 і більш важких вуглеводнів, охла-ждается в повітряних і водяних холодильниках до 40 ° С і при високому давши-лення надходить в холодний сепаратор, де з неї конденсуються важкі вуглеводні. Несконденсировавшиеся газова фаза являє собою ВСГ. Він повертається в процес, а рідкі фази з гарячого і холодного Сепар-торів направляються на ректифікацію. На деяких заводах при гарячої сепарації продуктів гідрогенізаційних процесів використовують ще один гарячий сепаратор, в який надходить
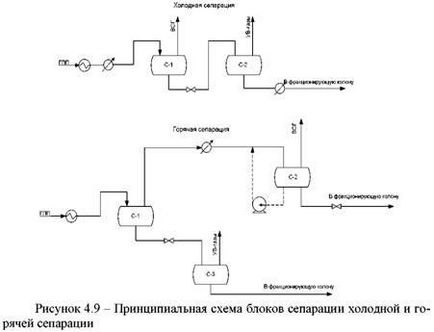
рідка фаза з гарячого сепаратора високого тиску (рисунок 4.9). У ньому за рахунок скидання тиску відбувається виділення легких вуглеводнів. Пре-майном гарячої сепарації ії в порівнянні з холодною є більш низькі енергетичні витрати на ведення процесу, за рахунок виключення ста-дии охолодження і подальшого нагрівання частини продуктового потоку перед його ректифікації. Недоліком же її вважається більш низька концентрація виділяється циркулюючого ВСГ. З цієї причини в процесах, в яких потрібна висока концентрація водню в ВСГ (гідрокрекінг, каталитич-ська гідродепарафінізація), використовується тільки холодна сепарація.
Реакторний блок складається зазвичай з 1-3 реакторів. При двох і більше реакторах в блоці вони можуть бути включені в схему послідовно або паралельно (рисунок 4.10).
Слід пам'ятати, що при паралельному підключенні реакторів необ-ходимо забезпечити добре перемішування газосирьвой суміші перед її раз-розгалуженням на два потоки. Це дозволить запобігти нерівномірне рас-пределеніе щодо реакторів рідкої фази і прискорене закоксовиваніє катали-затору в одному з них.
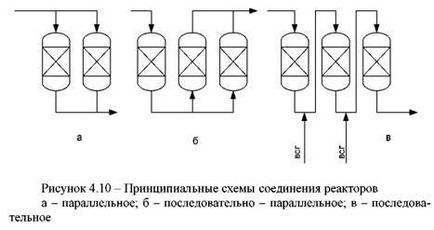
Опис технологічної схеми секції гідроочищення дизельного фракції (на прикладі схеми секції 300/1 установки ЛК-6У)
Сировина - широка дизельна фракція 180-360 ° С з резервуарів P-59,60 або Р-49,50 промпарків ЛК-Бу № 1,2, надходить на прийом підпірного насоса Н-310 (Н-310а) і подається в теплообмінник Т -306, де нагрівається теплом гидроочищенних фракції, виходить знизу колони К-301 до 120-160 ° С і надходить на прийом сировинних насосів H-301-303,303а. Ці насоси подають його в трійник змішання, куди надходить циркулює водородсодержа-щий газ (ВСГ) від компресора ЦК-301. Витрата сировини зазвичай становить 130 320 м3 / год. Є можливість прийому прямогонного дизельного палива по "жорсткої схемою" з секції 100 на прийом підпірного насоса Н-310 (310а). Як і сле змішання газосирьевая суміш (ГСС) з температурою до 120-160 ° С по-ступає в міжтрубний простір сировинних теплообмінників T-30I-303, де нагрівається до 280-300 ° С. Далі ГСС надходить в піч П-301 / 1,2, де на-Гревал до 340-400 ° С і надходить в реактор Р-301, де на каталізаторі при тиску на вході 5,0 МПа (хат) і температурі 330-390 ° С
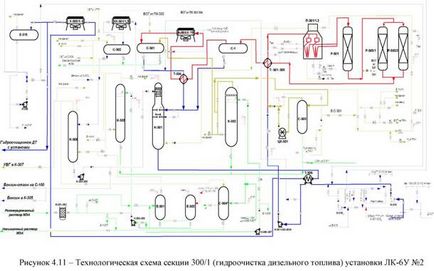
проходять реакції гідрування сіро і азотовмісних сполук (більшою мірою), реакції гідрування олефінів і поліциклічних сполук (частково). Процес гідроочищення в реакторі Р-301 протікає з виділенням тепла, тому для підтримки необхідної температури на вході в реактори Р-303/1 і Р-303/2 передбачена подача водородсодержа-ного газу від компресора ЦК-301 (квенч) в трубопровід на виході з реак-тора Р-301. Газопродуктовая суміш (ГПС) після реакторів Р-303 / 1,2 об'єд-вується і надходить в трубне простір теплообмінників Т-303-301, де охолоджується потоком ГСС і далі направляється в гарячий сепаратор С-1. Частина потоку ДПС після реакторів Р-303 / 1,2 надходить крім теплообмінників T-303-301 відразу в сепаратор C-1 для регулювання темпе-ратури гідрогенізату. У гарячому сепараторі С-1 потік ДПС розділяється на нестабільний гидрогенизат і парогазову фазу, частина якої надходить в трубне простір теплообмінника Т-304, де віддає тепло потоку Неста-бильного гідрогенізату з сепаратора C-301, потім охолоджується в повітр-ном холодильнику X- 301 до 20-55 ° С і входить в сепаратор C-301. Перед воз-задушливим холодильником в потік газопродуктовой суміші подається хімочі-щенная вода від насосів Н-31З, 314 для зв'язування і видалення аміаку, ко-торий утворює солі амонію, які призводять до корозії обладнання, з цир-кулір ВСГ.
У сепараторі C-301 відбувається поділ потоку газопродуктовой суміші на нестабільний гидрогенизат, воду і циркуляційний газ. Циркуля-ційний газ прямує в абсорбер К-302, де очищається від сірководню розчином МЕА. Очищений ВСГ з абсорбера К-302 через сепаратор С-303 надходить на прийом циркуляційного компресора ЦК-301, який подає його в трійник змішання. Для компенсації витраченого водню і підтримки необхідного парціального тиску водню циркуляційного-ний газ змішується зі свіжим ВСГ, що надходять від компресорів ПК-303, 304, в сепаратор С-301 або в лінію нагнітання компресора ЦК-301. Рідина (р-р МЕА) з сепаратора С-303 скидається періодичний-скі в сепаратор насиченого МЕА С-304а. Гарячий нестабільний гидрогенизат з сепаратора C-I і нагріте в теплообміннику Т-304 нестабільний гидрогенизат з сепаратора C-301 об'єднуються і з температурою 210-250 ° С надходять в стабілізаційну колону K-301.
Вниз колони K-301 подається водородсодержащий газ зі щита сдува секції 300/1 або з установки PSA, який підігрівається в газоподогрева-тілі, встановленому в газоходах печі П-301 / 1,2. Подача ВСГ, що виконує функцію випаровується агента, призводить до зниження парціального тиску-ня парів нафтопродуктів в колоні і полегшує випаровування рідкого залишку. Щит сдува дозволяє також скидати ВСГ з реакторного блоку секції 300 / I в паливну мережу або на факел. Пари води, бензину і вуглеводневий газ виводяться зверху колони К-301 з температурою 150-200 ° С, проходять конденсатор-холодильник XK-301, де охолоджуються до температури не бо-леї 50 ° С і надходять в сепаратор С-302, в якому відбувається відділення газу від рідини і поділ бензину і води.
Бензин з сепаратора С-302 надходить в колону К-308 для очищення від сірководню очищеним вуглеводневим газом з абсорбера К-303, звідки він насосами Н-304,305 частково подається на зрошення колони К-301; ба-лансовое кількість бензину виводять з установки. Є перемичка з лінії гидроочищенних дизпалива в лінію зрошення колони K-301 для регулювання температури вгорі К-30I при аварії насосів Н-304,305. Бензин з сепаратора С-302 виводиться в цьому випадку в неконді-цію по байпасу колони К-308.
Надмірна бензин може виводитися:
в сировині колони К-305 секції 300/2 при роботі установки для виробництва реактивного палива;
через лінію некондиції на прийом сировинних насосів секції 100.
Вода з сепаратора С-302 періодично виводиться в лінію кислої води з установки. Вуглеводневий газ з сепаратора С-302 надходить в аб-сорбер К-303, куди подається газ з сепаратора С-309 секції 300/2 і углево-огрядний газ з УЛГК (установки легкого гідрокрекінгу), де вони очищають-ся від сірководню розчином МЕА . Розчин МЕА подається в абсорбер К-303 з ємності E-30I насосами Н-308, 309. При тиску
0,8-1,0 МПа в колекторі регенерованого МЕА, що надходить з установки сірки, насоси Н-308,309 можна не включати, а подавати його за рахунок тиску в колекторі. Частина вуглеводневого газу з абсорбера К-303 на-спрямовується в колону К-308. Можна скинути вуглеводні-родного газу з сепаратора С-302 крім абсорбера К-303 в паливну мережу або на факел. З колони К-308 газ також можна вивести на факел.
Стабільна гидроочищенних фракція йде знизу колони K-301, охолоджується послідовно в теплообміннику Т-306 (межтрубное про-странство), повітряному холодильнику Х-303 і надходить в ємність E-315, де відбувається її додаткова сепарація. При необхідності гідроочі-щенное паливо після повітряного холодильника Х-303 можна відразу вивести на ТСБ. Газ, виделяюшійся в ємності E-315, виводиться на факел, а дизель-ве паливо надходить на прийом насосів Н-340 (310а) і відкачується на ТСБ.
Розчин МЕА з ємності E-301 насосами Н-306,307 подається в абсорбер К-302 і абсорбер К-306, а насосами Н-308,309 в абсорбер К-303. У аб-сорбер К-307 розчин МЕА подається за рахунок тиску в колекторі регенера-рованного МЕА. Насоси Н-308, 309 використовуються також для відкачування раство-ра МЕА з ємностей E-30I, 302 в період підготовки до ремонту. Насичений МЕА з К-302,303,306,307 подається в сепаратор С-304а, де відбувається ви-ділення газу і відділення рідких вуглеводнів від МЕА. В сепаратор С-304а також виводиться розчин МЕА з сепараторів З-303,311. Розчин МЕА з сепаратора С-304а подається на установку регенерації МЕА. Нафтопродукт періодично дренируется вручну в ємність Д-207. Вуглеводневий газ з сепаратора С-304а надходить в колону К-307 на очистку від сірководню.
Всі параметри технологічного режиму установки виведені на щит в операторної і на монітор ПЕОМ секції 300/1.