ПРАКТИКА І ПЕРСПЕКТИВИ ЗАСТОСУВАННЯ ЗАХИСНИХ ПОКРИТТІВ НА КОРПУСНИХ ДЕТАЛЯХ І ВУЗЛАХ ПОГРУЖНИХ відцентрові насоси
Корпусні деталі і вузли заглибних відцентрових насосів постійно знаходяться під впливом виносу механічних домішок, руйнівною активності пластових рідин, високій обводнення, солеотложеній, підвищеної температури і освіти гальванопар. Все це веде до корозійного електрохімічного руйнування матеріалів (див. «Коррозионное руйнування УЕЦН»). Через триваючого погіршення умов видобутку нафти на родовищах проблеми корозії постійно загострюються, що вимагає вдосконалення способів підвищення антикорозійних властивостей і зносостійкості вузлів УЕЦН.
На сьогоднішній день компанії застосовують різні методи захисту від корозії: введення інгібіторів в пластову рідину, заміна матеріалів і вузлів на нові, нанесення захисних покриттів і просочень. Найбільш популярними і дієвими антикорозійними засобами залишаються металеві та протекторні покриття, а актуальним напрямком їх вдосконалення виступає оптимізація складу, структури і технології нанесення.
Сьогодні проблема корозійного руйнування корпусних деталей і вузлів заглибних відцентрових насосів вирішується різними методами.
По-перше, введенням в пластову рідину інгібіторів корозії, які сприяють пасивації поверхні основного металу вузлів УЕЦН, тобто утворення тонкої плівки оксидів, що перешкоджає руйнуванню основного матеріалу.
По-друге, заміною матеріалів вузлів і корпусних деталей УЕЦН на нові матеріали, що володіють більш високу корозійну стійкість.
По-третє, нанесенням корозійностійких металевих захисних покриттів методом високошвидкісного газопламенного напилення на основі заліза. Використання легуючих елементів в напилюються матеріалах збільшує зносостійкість і корозійну стійкість, дає можливість зменшити пористість, що підвищує міцнісні властивості матеріалів і мінімізує підплівкова корозію.
По-четверте, нанесенням металевих антикорозійного покриття методом електродугової металізації. При цьому виникає значна пористість, що вимагає додаткового захисту товстим шаром в'язкої просочення.
Нарешті, по-п'яте, застосуванням просочень, в тому числі включають фторосодержащіе ПАР, які забезпечують додаткову корозійний захист і захист тіньових зон.
Всі перераховані способи, що застосовуються для захисту від корозії вузлів УЕЦН, мають свої недоліки. Так, інгібітори корозії діють обмежений час. Заміна матеріалу вузлів і корпусних деталей ЕЦН на новий, наприклад, на нержавіючу сталь, досить дорогий захід, яке до того ж залишає невирішеною проблему корозії обсадної колони і колони НКТ. Просочуючих матеріали, які використовуються при захисті покриття, нанесеного електродугової металізацією, діють як теплозахист вузлів УЕЦН, викликаючи перегрів деталей, що несприятливо позначається на роботі всієї установки.
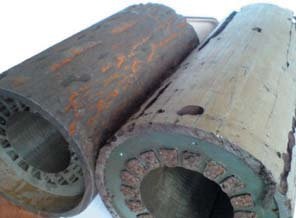
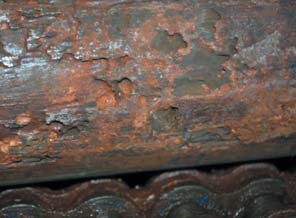
Схема електрохімічного процесу при механічному пошкодженні металевого покриття
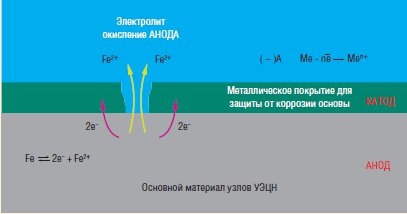
Захисні МЕТАЛЕВІ та протекторні ПОКРИТТЯ
Нанесені на зовнішні поверхні корпусних деталей і вузлів УЕЦН металеві покриття на основі заліза з додаванням легуючих елементів (хрому, нікелю, кремнію, молібдену, бору і вуглецю, які мають більш позитивний електродний потенціал, ніж потенціал основного металу корпусу УЕЦН) є хорошим захистом від корозії , але лише до тих пір, поки в покритті відсутні механічні пошкодження. Якщо при монтажі УЕЦН або СПО відбувається пошкодження, утворюється гальванічна пара: металеве покриття стає катодом по відношенню до корпусу, корпус ЕЦН - анодом. Починається процес електрохімічної корозії між покриттям і матеріалом корпусу, що призводить до подпленочной корозії захищається корпусу ЕЦН і до корозії обсадної труби.
В процесі електрохімічної корозії основний матеріал корпусу окислюється, розпадаючись на позитивно заряджені іони, в електроліт - пластову рідину і електрони (див. «Схема процесу електрохімічної корозії на корпусі УЕЦН при механічному пошкодженні металевого покриття»), анодкорпус розчиняється.
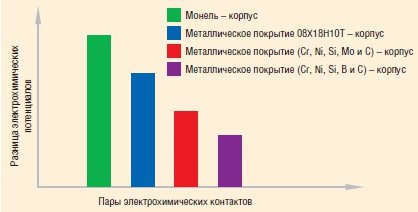
Надлишкові електрони перетікають до катодного ділянці - металевому покриттю.
Для вирішення проблеми подпленочной корозії корпусних деталей і вузлів УЕЦН зазвичай застосовується електрохімічний захист. Вона має на увазі нанесення протекторного (анодного) покриття (Al, Zn, Mg або їх сплавів) на металеве, має електродний потенціал більш негативний, ніж потенціал металевого покриття, основного матеріалу корпусу УЕЦН і обсадної труби (див. «Різниця електро-хімічних потенціалів між корпусом і застосовуваними захисними покриттями »). Однак в разі механічних пошкоджень при монтажі корпусів УЕЦН починається електрохімічна корозія між протекторним і металевим покриттям (див. «Схема процесу електрохімічної корозії на корпусі УЕЦН при механічному пошкодженні металевого і протекторного покриттів»).
Якщо покриття порушується, утворюється гальванічна пара між алюмінієвим або цинковим покриттям, яке стає анодом, і металевим покриттям або основним металом корпусу УЕЦН, який стає катодом по відношенню до протекторному покриттю. В даному процесі руйнується протекторное покриття, зберігаючи основний матеріал корпусних деталей і вузлів УЕЦН, на яких відбуваються відновні процеси. Їх корозія почнеться після того, як протекторное покриття повністю прокорродірует.
Протекторні покриття на основі сплавів цинку і алюмінію залишаються стійкими до морській воді протягом 10-60 років і мають ефект «самозарастанія» тріщин, подряпин. Для порівняння лакофарбові покриття (ЛКП) забезпечують стійкість в морській воді не більше трьох років, до того ж при їх застосуванні в морському середовищі в мікропорах розвиваються бактерії, що призводить до утворення виразкової корозії сталевого корпусу.
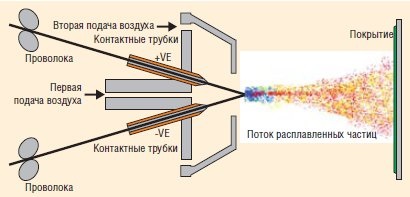
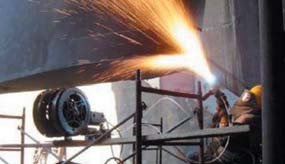
Схема процесу електрохімічної корозії на корпусі УЕЦН при механічному пошкодженні металевого і протекторного покриттів
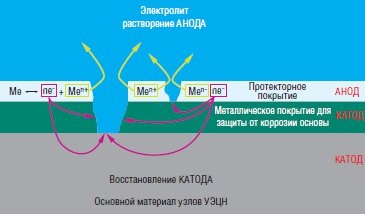
Схема високошвидкісного напилення
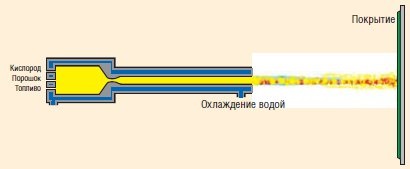
Сьогодні металеві та протекторні покриття залишаються ефективними методами в боротьбі з корозією, а одним з актуальних напрямків їх вдосконалення виступає оптимізація складу, структури і технології нанесення. Роботи в цьому напрямку ведуться декількома організаціями, зокрема «ТСЗП» спільно з ВНІІГАЗ і кафедрою електрохімії МДУ ім. Ломоносова. Ці роботи дозволять підбирати найбільш підходящий варіант покриття для кожного конкретного родовища з урахуванням особливостей його експлуатації.
електродугової металізації
Газотермічне напилення (ГТН) являє собою процес нагріву, диспергування і перенесення активованих частинок розпорошується матеріалу газовим потоком і формування на підкладці компактного шару. Для отримання цього покриття застосовуються високошвидкісний, плазмовий, Газополум'яний методи, метод газопламенной наплавлення і електродугове металлизация.
Електродугова металлизация (див. «Схема електродугової металізації») дає можливість отримати покриття на великих площах, так як ефективний ККД розпилювача досягає 70-90% - найвищий показник серед способів ГТН. За допомогою цього методу створюються покриття на основі Al, Zn, ZnAl, Cu, Fe. В даний час електродугова металізація використовується для захисту обладнання, виробленого на заводах «Борець», «Новомет», «Ойлпамп Сервіс», «Алнас» і ін.
Цинк-алюмініевогопокритія ZnAl (85/15)
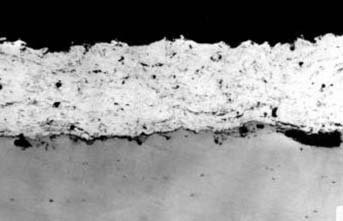
Алюмінієво-магнієвого покриття AlMg5
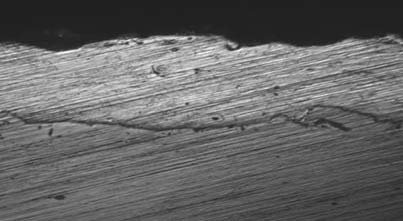
Електродугове метализаційні напилення з використанням нержавіючої сталі і монелю має міцність зчеплення 15-35 МПа, пористість - 5-10%, мікротвердість - 150-330 HV. Причому нержавіюча сталь частіше наноситься в Росії, тоді як на Заході більш популярні монельние покриття, які відрізняються порівняно більш високу пористість і тому потребують спеціальної просочення для запобігання подпленочной корозії.
Електродугове метализаційні напилення з використанням цинку, алюмінію і їх сплавів має міцність зчеплення 70-80 МПа, пористість - 10-20%, мікротвердість - 35-50 HV (див. «Електродугове метализаційні напилення»).
високошвидкісний напиленням
Високошвидкісне напилення має на увазі використання надзвукового потоку матеріалів, що дозволяє отримувати покриття з максимально можливими для газотермічних методів адгезійними і когезійний характеристиками (див. «Схема високошвидкісного напилення»). Частинки порошку мають розмір 30-50 мкм. Таке покриття можна розглядати як альтернативу гальванічним і вакуумним методам нанесення покриттів.
Високошвидкісне напилення застосовується для відновлення зношених, а також зміцнення нових металевих поверхонь, що вимагають високих зносостійкості і щільності. Треба відзначити, що дана технологія поки не дозволяє забезпечити захист внутрішньої поверхні НКТ, яка була б прийнятна для замовника з економічної точки зору.
Незважаючи на те, що з боку замовників відчувається інтерес до даної технології, дієвих способів знизити її вартість до прийнятних економічних характеристик не проглядається. Сьогодні високошвидкісне напилення застосовується для захисту деяких деталей літаків п'ятого покоління - з цією метою використовується складна високотехнологічна плазмова установка, що дозволяє наносити покриття на внутрішню поверхню труби діаметром 60 см і довжиною 1,5 м. Вартість покриття при цьому становить 250 євро за квадратний дециметр. Якщо обробити таким способом 2 км внутрішньої поверхні НКТ, то труба буде практично золотий.
Принципова схема нанесення газотермічних наноструктурованих покриттів
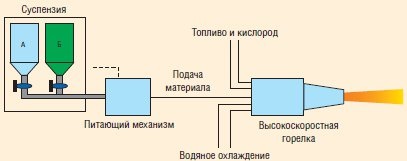
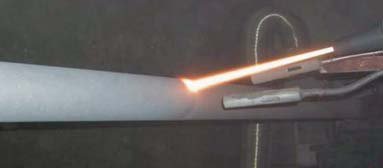
Завдані способом високошвидкісного напилення нержавіючі сплави на основі заліза мають мікротвердість 500-800 НV і міцність зчеплення 70-80 МПа. Сплави на основі нікелю мають пористість не більше 2%, мікротвердість - до 820 HV, міцність зчеплення - 70-80 МПа. Пористість твердих сплавів також знаходиться в межах 2% при мікротвердості 900-1200 НV і міцності зчеплення більше 80 МПа.
Таким чином, покриття, нанесені за допомогою високошвидкісного напилення, відрізняються більш високими якісними характеристиками в порівнянні з такими, нанесеними методом електродугової металізації (див. «Характеристика методів нанесення покриттів, що використовуються при захисті корпусів УЕЦН»). Особливо важлива низька пористість, оскільки в цьому випадку не потрібно додаткової просочення.
Вартість покриттів, нанесених за допомогою електродугової металізації, за рахунок більшої витрати матеріалу вище в порівнянні з такими, нанесеними за допомогою високошвидкісного напилення. При цьому обладнання, яке застосовується для високошвидкісного напилення, коштує в десятки разів дорожче обладнання для електродугової металізації.
Характеристика методів нанесення покриттів, що використовуються при захисті корпусів УЕЦН