В даний час масштаби позапічної десульфурації чавуну і раніше зростають як при обробці товарного і передільного чавуну в доменних цехах, так і в ливарних цехах перед його заливкою в ливарні форми. Така тенденція характерна для заводів Західної Європи, США, Японії, Китаю та ін. Це обумовлено одразу декількома причинами, головними з яких є підвищення ефективності доменного виробництва, збільшення обсягів поставок високоякісного чавуну і виливків з нього, розширення обсягів виробництва якісних сталей і розливання їх на МБЛЗ.
Порівнюючи тенденції розвитку внедоменной десульфурації чавуну в 60-90 роки необхідно відзначити, що останнім часом основна частина капітальних вкладень спрямовується на розширення і вдосконалення способів позапічної обробки чавуну. При цьому найбільша увага приділяється раціональному вибору десульфуранти, створення промислової бази для їх виробництва і розробці методів їх ефективного запровадження в метал. З значного числа десульфуранти, які пройшли широкі промислові випробування (магній, магнийсодержащие реагенти, кальцинована сода, вапно, карбід кальцію, карбонат кальцію та ін.) Все більша перевага віддається гранульованому магнію і в ряді випадків промисловим сумішей на базі декількох десульфуранти. Крім того, досить поширеним реагентом в США і Західній Європі як і раніше залишається карбід кальцію. Разом з тим, певні обмеження в застосуванні карбіду кальцію обумовлені рядом технологічних факторів і міркуваннями техніки безпеки та екології.
Основні причини використання магнію замість карбіду кальцію полягають в наступному:
- зменшення витрат реагенту (гранульованого магнію з сольовий оболонкою необхідно в 8-12 разів менше, суміші магнію з вапном - в 3-4 рази менше, ніж карбіду кальцію);
- низькі питомі витрати на обробку чавуну через невеликої витрати магнію;
- зменшення капітальних витрат в результаті більшої безпеки магнієвого реагенту, що утворюється шлаку і виділяється з ковша диму;
- підвищення ступеня десульфурації при обробці чавуну з низькою температурою;
- можливість досягнення кінцевого вмісту сірки на рівні 0,003%;
- скорочення тривалості позапічної обробки приблизно в 2 рази;
- менший вияв негативного впливу на футеровку ковша;
- зменшення в 3-10 разів кількості утворюється шлаку.
Після обробки карбідом кальцію шлак містить непрореагіровавшій карбід, який при взаємодії з вологою утворює ацетилен. Тому при десульфурації чавуну карбідом кальцію застосовують спеціальне обладнання і спеціальні запобіжні заходи. При роботі на гранульованому магнії застосовують звичайні прийоми та обладнання для позапічної обробки чавуну.
Технологічні аспекти десульфурації чавуну магнієм багато в чому залежать від його фізичних властивостей, найважливішими з яких є температура плавлення, кипіння і пружність пара. Температура плавлення магнію становить 650 про С. Тиск пара p чистого магнію (мм рт.ст.) в залежності від температури Т визначається, наприклад, по Бауеру і Брунер з наступного рівняння:
Температура кипіння магнію, підрахована за допомогою рівняння (2.1), становить 1107 ° С при атмосферному тиску, 1200 о С при тиску в дві атмосфери і 1250 о С при тиску в три атмосфери. При оцінці ефективності магнію як модифікатора необхідно враховувати термодинамічні характеристики реакцій взаємодії його з компонентами розплаву, кінематичні умови протікання реакцій, умови евакуації продуктів реакції з розплаву і технологічні можливості введення в розплав модифікатора.
Термодинамічні передумови застосування магнію для рафінування розплаву визначаються його високою хімічною спорідненістю до сірки і кисню, які є шкідливими домішками в чавуні. Теплота утворення сульфіду магнію в два рази вище, ніж марганцю. Реакція взаємодії газоподібного магнію з розчиненою в розплаві сірої характеризується значною зміною вільної енергії. Хімічна спорідненість магнію до сірки швидко знижується з підвищенням температури і при 1600 о С наближається до спорідненості марганцю до сірки. Можна з високим ступенем впевненості вважати, що лімітуючим ланкою процесу при обмеженій глибині десульфурації чавуну є массоперенос сірки з обсягу металу до поверхні спливаючих в розплаві бульбашок пара магнію.
Магній має дуже високу хімічну спорідненість до кисню. Теплота освіти окису магнію досить висока:
Реакція взаємодії газоподібного магнію з киснем протікає з великим виділенням вільної енергії. У залізовуглецевих сплавах магній також активно взаємодіє з розчиненим киснем. Однак, розвиток реакції між магнієм і киснем залежить від наявності останнього в чавуні в розчиненому вигляді. Відомо, що промислові доменні чавуни мають низьку ступінь окислення, що дає підставу вважати втрати магнію від його реакції з киснем незначними.
Кінетичні умови протікання реакцій взаємодії магнію з компонентами чавуну визначаються тим, що магній знаходиться в газоподібному стані. Газоподібний магній має надзвичайно розвинену контактну поверхню з металом, про-легшає умови підведення реагенту до реакційної поверхні. Велика кількість газу, що утворюється при введенні магнію, сприяє інтенсивному перемішуванню розплаву і, отже, покращує умови конвективного підведення розчинених в металі домішок до реакційної зоні.
Для технологічних процесів, пов'язаних з обробкою залізовуглецевих розплавів магнієм, важлива розчинність магнію в твердому і рідкому сплаві. Розчинність магнію в твердому залозі дуже низька, що пояснюється несприятливим об'ємним фактором магнію по відношенню до заліза. Атомний об'єм магнію більш ніж в два рази перевищує атомний об'єм заліза.
Для більш повного прояву властивостей магнію як Десульфуруючі, рафінуючі і модифікує реагенту велике значення має спосіб введення його в розплав. У промислових умовах використовується магній у вигляді злитків, гранул і порошку. Однак, у всіх випадках для ефективного використання десульфуранти характерним є прагнення забезпечити регульований введення магнію в струмені транспортує газу.
Найбільш дешевим, зручним (безпечним) в зберіганні і доступним в постачанні є зливковий магній, що випускається підприємствами кольорової металургії. Якщо занурювальний пристрій для введення магнію (випарник) виконати з порожнистої штангою і через неї під дзвін подати газ, то при зануренні випарника в ківш чавун не підніметься вище отворів в дзвоні. Це дозволяє розмістити у верхній частині випарника механічний дозатор і подавати магній в необхідній кількості через штангу в дзвін.
Злитки магнію (рис. 2.8, а), з'єднані в гірлянду, перед початком обробки надягають на гак і за допомогою приводного барабана, розміщеного в герметичному корпусі, втягують всередину штанги випарника так, щоб нижній край зливка знаходився приблизно на рівні отворів в дзвоні або кілька вище. Випарник занурюють в ківш з чавуном, подаючи в нього через патрубок газ (азот або повітря) з витратою, що забезпечує швидкість підйому тиску всередині корпусу і штанги, відповідну швидкості збільшення глибини занурення випарника в метал. Після досягнення випарником заданої глибини занурення витрата газу зменшують і починають повільно подавати злитки магнію до поверхні металу всередині дзвони випарника. У реальних пристроях швидкість випаровування магнію змінюють в діапазоні 0,05-0,20 кг / с, що для стандартних зливків магнію масою 8 кг і довжиною 0,48 м досягається при швидкості їх опускання 0,003-0,012 м / с. Величина разового заряду злитків визначається допустимим часом перебування випарника в розплавленому металі, прийнятої швидкістю введення магнію і зазвичай становить 3-4 злитка.
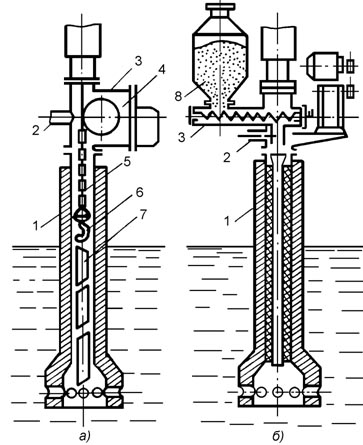
Малюнок 2.8 - Схема введення сліткового (а) і гранульованого (б) магнію: 1 - випарник; 2 - патрубок для підведення газу; 3 - корпус дозатора; 4 - барабан; 5 - ланцюг; 6 - гак; 7 - злитки магнію; 8 - бункер для гранульованого магнію.
Витрата газу, що подається у випарник в процесі обробки, вибирають з умови запобігання можливості проникнення парів магнію в штангу випарника і витіснення цих парів в чавун через отвори в дзвоні. При використанні азоту і повітря достатнім виявляється витрата, відповідно, 20-40 і 40-80 м 3 на годину.
Стосовно до гранульованому магнію принципова схема реалізації способу «магній-газ» представлена на рис.2.8, б. Процес десульфурации в цьому випадку регулюється більш гнучко, спрощується робота із зарядки пристрою магнієм, зменшується перетин штанги і, відповідно, скорочується витрата газу, що подається у випарник. Оптимальна швидкість введення магнію визначається в залежності від допустимого часу перебування випарника в розплавленому металі, величини «заряду» магнію і ступеня наповнення ковша. На практиці при обробці чавуну зливковий магнієм вона зазвичай становить 0,07 - 0,12 кг / с, гранульованим - 0,01 0,2 кг / с.
Розвитком способу десульфурації чавуну гранульованим магнієм є застосування гранул із спеціальним сольовим покриттям. Починаючи з 80-х років, гранульований магній застосовується на багатьох заводах Західної Європи і США. У країнах західної Європи були отримані магнієві гранули з негігроскопічним покриттям з евтектичною суміші 40-50% хлориду натрію і 50-60% хлориду калію. У США для десульфурації досить широко застосовують реагент «Pelamag», що представляє собою гранули, які містять 88-92% металевого магнію з сольовим покриттям із суміші хлоридів магнію, калію, кальцію і натрію. Використання реагенту «Pelamag» дозволило замінити на двох заводах фірми «Armco» раніше використовувану суміш магнію з вапном. Інтенсивність його введення в чавун становить 13 кг / хв при наповненні 200-тонних ковшів до 95%. Магній вводять в рідкий метал в струмені азоту через занурюється під кутом 15-25 о до вертикалі фурму, що має Т-подібний канал на виході. Ступінь засвоєння магнію в цьому випадку становить приблизно 50%, а тривалість продувки - 8 хв. Швидкість зниження температури чавуну в ході обробки дорівнює 1-2 ° С в хвилину.
Як приклад пошуку раціонального виду десульфуранти можна також привести завод фірми «Youngstown Steel» (США), де спочатку використовувався метод десульфурации магкоком (суміш магнію і коксу). Починаючи з 1977 р десульфурацию на цьому заводі виробляють гранульованим магнієм, покритим оболонкою з 54% хлористого натрію, 20% хлористого магнію і 13% хлористого калію.
У Франції з 1980 р застосовують магнієвий реагент, розроблений французькими фірмами USINOR і SOFREM і представляє собою суміш 80% сферичних гранул чистого магнію розміром 0,3-1,6 мм і 20% гранульованого основного шлаку, того ж гранулометричного складу. На думку розробників, шлак запобігає налипання магнію на зріз фурми і покращує плинність реагенту. Тривалість обробки становить 8-10 хв, а інтенсивність введення реагенту - 6-12 кг / хв.
Крім гранульованого магнію на ряді заводів використовується технологія вдування порошкоподібного магнію. У промислових масштабах вдування порошкоподібного магнію вперше реалізовано Інститутом чорної металургії НАН України (м.Дніпропетровськ) на комбінаті «Азовсталь» (м.Маріуполь). Магній вдувають в чавун через футерованную вогнетривким матеріалом фурму разом з наповнювачем - вапном або доломітом. Наповнювач екранує порошок магнію від теплового випромінювання рідкого металу і сприяє очищенню вихідного отвору фурми від налипають частинок магнію (заварювання фурми металом в цьому випадку не відбувається). Найкраще ставлення магнію і наполнительной суміші 1: 3. Принципова схема установки для десульфурації чавуну порошкоподібною магнієм приведена на рис.2.9.
Витрата повітря на транспортування суміші становить 70 - 120 м 3. витрата суміші - 50 - 80 кг / хв. Питома витрата магнію 0,7 - 0,95 кг / т забезпечує досить повне видалення сірки з чавуну. Надалі технологія була поширена на ряд заводів України.
Відомі також і інші варіанти промислового використання порошкового магнію в суміші з наповнювачами:
- суміш магнію і карбіду кальцію на заводі «Arbed Saarstahl» (ФРН);
- суміш з'єднань MgSi і MgAl2 O3.
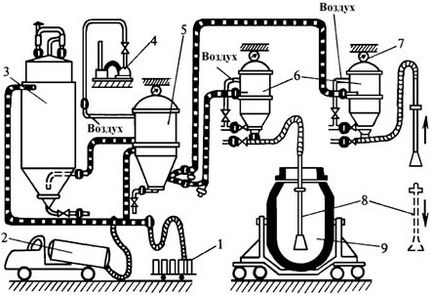
Малюнок 2.9 - Схема установки десульфурації чавуну порошкоподібною магнієм: 1 - ємності з магнієм; 2 - автоцистерна для подачі вапна; 3 - бункер для вапна; 4 - компресорна установка; 5 - змішувач; 6 - витратні бункера; 7 - динамометр; 8 - фурми; 9 - чавуновозних ківш.