Отримання заготовок обробкою тиском.
У виробництві широко використовують поодинокі заготовки, отримані методом пластичного деформування металу. Основні різновиди цього методу - вільна кування, штампування на молотах і пресах, карбування (калібрування), висадка на горизонтально-кувальних машинах, вальцювання на кувальних вальцях, поперечно-гвинтова Прокатка, редукування на ротаційно-кувальних машинах, холодна висадка на автоматах і штампування видавлюванням .
Вільним куванням. здійснюваної на молотах і гідравлічних пресах без застосування штампів з підігрівом заготовки до температури пластичного деформування, отримують поковки масою від кількох кілограмів до сотень тонн в умовах одиничного і дрібносерійного виробництва. Отримані заготовки мають великі припуски і напуски для обробки різанням, точність їх низька (порядку 17-го квалітету), а дефекптий шар досить значний. Цей спосіб пластичного деформування - грубий, але універсальний і дешевий.
Гарячу об'ємну штампування з підкладним штампами використовують як додаткову операцію, яка підвищує точність і продуктивність вільного кування при виготовленні дрібних і середніх заготовок. Застосування підкладних штампів рентабельно при мінімальних партіях заготовок 50 - 200 шт.
Штампування можна виконувати на відкритих (облойной) і закритих (безоблойних) штампах на молотах і штампувальних пресах. Маса заготовки до 100 кг. Штампи можуть бути одноручьевимі і многоручьевого. На останніх можна отримати досить складні заготовки з великим перерозподілом обсягів металу. Приклад отримання заготовки зубчастого колеса в закритих і відкритих штампів показаний на рис. 6.2.
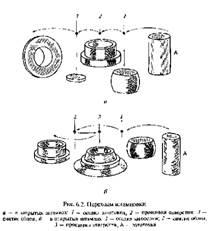
Гаряче штампування у відкритих штампах (рис. 6.2, о) на пресах більш продуктивна, ніж на молотах, оскільки на пресі заготівля штампується за один хол преса, а на молоті - за кілька ударів.
Штампуванням в закритих штампах (рис. 6.2, 6) виготовляють зазвичай заготовки, що мають форму тіл обертання або близьку до неї. При виготовленні складної заготовки її попередньо обжимають в спеціальному штампі, після чого штампують в закритому безоблойном штампі. Безоблойная штампування підвищує точність заготовки і знижує витрату металу, вимагає більш потужних пресів і точного розрахунку обсягу металу, потрібного для заготовки.
Карбування використовують для підвищення точності і якості заготовок, отриманих гарячим штампуванням, в цьому випадку обробляють тільки ті поверхні заготовки, до яких пред'являються підвищені вимоги (поверхні чорнових технологічних баз).
Розрізняють плоску і об'ємну карбування. У першому випадку виробляють обтиснення паралельних площин для отримання точних розмірів заготовки по висоті, в другому - виробляють обтиснення по всьому контуру заготовки Поверхні заготовки перед карбуванням очішают від окалини і задирок.
Процес карбування виконують або в холодному, або в підігрітому стані заготовки. Другий варіант використовують при карбуванні великих менш відповідальних поверхонь. Обладнання, що застосовується - кривошипно-карбовані і фрикційні преси або молоти. На перших карбують поверхні розміром до 200 см2.
Висадку на горячековочних машинах (ГКР) як високопродуктивний і ефективний спосіб пластичного деформування металу широко використовують в масовому виробництві для виготовлення заготовок, що мають форму тіл врашенія. Вихідним матеріалом служить прокат круглого перетину і труби діаметром 30 ... 250 мм і довжиною до 3 ... 3,5 м, маса заготовок в цьому випадку коливається в межах 0,1 ... 100 кг, Втрати металу становлять всього 1 ... 3% маси заготовки. При одному нагріванні вихідного матеріалу можна отримати кілька заготовок. Штамп на ГКР (рис. 6.3) складається з нерухомої 3 і рухомий 2 матриць і пуансона 1. Пруток нагрітим кінцем укладається в нерухому матрицю, рухлива матриця затискає пруток, утворюється порожнина штампа. При русі пуансона формується головка штампування. Стійкість штампів становить 10-20 тис. Заготовок. У деяких випадках обробку на ГКР ефективно поєднувати з іншими видами формоутворення заготовки, наприклад зі штампуванням в струмкових штампах або з поперечно-гвинтовим прокатом.
Штампування холодним видавлюванням є пластичне деформування, при якому метал 3 тече в отвір матриці 2 або в зазор між пуансоном 1 і матрицею 2 (рис. 6.4), чим забезпечується отримання тонкостінних заготовок складної форми. Матеріалом заготовок служить алюміній, мідь, латунь, цинк, м'яка сталь марок 08, 10, 15, 20, 25.
Існує три різновиди холодного видавлювання: пряме, зворотне і комбіноване. При прямому видавлюванні метал втечеть в напрямку руху пуансона /, при зворотному видавлюванні метал під тиском пуансона 1 тече в напрямку, протилежному руху останнього, заповнюючи простір між-
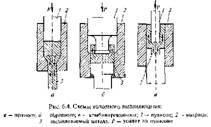
ду пуансоном і матрицею 2. Форма простору відповідає формі заготовки.
Процес штампування видавлюванням забезпечує точність 9- 11-го квалітетів, шорсткість поверхні заготовки Ra 80 ... 20 мкм і коефіцієнт використання металу - 0,9.-0,98.
Холодну висадку використовують для виготовлення деталей стрижневого типу з потовщеннями, виїмками і порожнистих деталей з гладкими і ступінчастими отворами (ковпачкові гайки, колісні шпильки, кульові пальці). Часто цим способом отримують деталі кріплення: болти, гайки, шурупи, заклепки і т.п. Матеріал для холодного висадження - сортовий прокат, гарячекатана калиброванная дріт, конструкційна малоуглеродистая сталь.
Основні операції холодного висадження схематично показані на рис. 6.5. Процес високопродуктивний, точність в межах
10- 12-го кваллітетов, шорсткість поверхні Яа 5 .1,25 мкм, рентабельний тільки при випуску виробів 10 - 50 тис. І більше.
Вальцовку на кувальних вальцях застосовують для попереднього і остаточного обтиску заготовок деталей, що виготовляються зі смуги або прутка (шатуни, вилки, гайкові ключі, важелі і т.п.).
Кувальні вальці мають два валика, на яких закріплюються половини секторного штампа / (рис. 6 6). Валики синхронно обертаються і при замиканні утворюють профіль заготовки 2, яка вводиться між половинами штампа і піддається обтисненню. Останнє супроводжується витяжкою, що веде до перерозподілу обсягів металу в 6 -8 разів.
З огляду на короткочасність процесу вальцювання (4 ... 5 с) відразу ж можна виконувати наступну штампування без додаткового підігріву. Таке поєднання підвищує продуктивність, знижує витрату металу на 10 ... 15% і забезпечує більш сприятливе розташування волокон матерівла.
Поперечно-гвинтову прокатку використовують в серійному і масовому виробництві для виготовлення заготовок з поверхнями тіл обертання. Схема процесу приведена на рис. 6.7. Форма заготовки утворюється в такий спосіб: нагріте в високочастотному індукторі до початкової температури конки пруток 3 подається в робочу зону, один кінець прутка затискається захопленням 4 механічної руки і починає переміщатися уздовж своєї осі зі швидкістю 10 ... \ 2 м / хв. Радіальні переміщення валків 2 (зближення їх осей і збільшення відстані між ними), завдяки яким утворюється форма заготовки, забезпечуються за допомогою трьох гідроциліндрів 7, які управляються щупом 6, що ковзає по змінному копиру 5.
Розглянутий спосіб забезпечує точність в межах 14 - 15-го квалітетів. шорсткість поверхні заготовки на 40 ... 10 мкм, економію металу 20 ... 30% і підвищення фізико-механічних властивостей внаслідок більш вигідного розташування волокон металу. Його ефективно використовують для попереднього формування заготовок під подальшу обробку на ГКР або в струмкових штампах. Таке поєднання підвищує якість заготовок і продуктивність обробки.
Листове штампування - спосіб виготовлення плоских і порожнистих виробів з допомогою штампів з листів, смуг і стрічок з маловуглецевої сталі, міді, магнієвих та інших кольорових сплавів. При товщині листа до 15 мм обробка відбувається в холодному стані. При штампуванні складних за формою деталей з глибокими порожнинами вихідна заготовка повинна мати високу пластичність, дрібнозернистою структурою, рівномірної толшиной.
Лінійна штампування включає в себе послідовне або паралельне виконання наступних операцій: розділових (відрізки, вирубки, пробивки) і формозмінних (гнучкі, витяжки, формовки, обтиску, відбортовки). Схеми відрізки різними способами показані на рис. 6.8, прийоми листового штампування - на рис 6.9.
В автомобілебудуванні найбільш поширені вирубка;
(Рис. 6.9, а), витяжка (рис. 69, б, в) і комбінована штампов- I
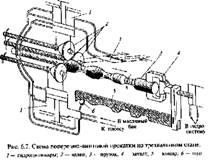
ка. Вирубкою по замкнутому контуру виготовляють деталі типу шайб, важелів, кришок, прокладок, витяжкою - просторові деталі облицювання автомобіля, ковпаки, диски коліс, бензобаки і т.д.
Переваги холодного листового штампування - мала маса деталі при забезпеченні необхідної міцності і жорсткості, можливість виготовлення деталей без застосування обробки різанням, значна економія металу, мала трудомісткість.
Заготовки із сталевого нормалізованого гарячекатаного прутка (ГОСТ 2590-73) застосовують для виготовлення гладких і східчастих валів з незначним перепадом в розмірах діаметрів ступенів. Заготовки із сталевого комбінованого прутка (ГОСТ 7417-86) 9-го квалітету точності використовують для виготовлення деталей, що не піддаються обробці по зовнішньому діаметру.
Для деталей кріплення і деталей фасонного профілю застосовують прокат по ГОСТ 2591-73 і ГОСТ 8560-83. Виготовлення заготовок із сталевого прокату різко скорочує витрату металу і обсяг механічної обробки.
Отримання заготовок методом порошкової металургії.
Даний метод використовують для виготовлення точних деталей без подальшої механічної обробки. Метод полягає в пресуванні сумішей металевих порошків в прес-формах під тиском з
пресуванні спікання виробляють при температурі нижче температури плавлення основного компонента. Пресування і спікання можуть здійснюватися одночасно шляхом пресування з нагріванням (гаряче пресування). Останнє використовують тільки для виготовлення деталей масою 10 кг і більше або тонких дисків і пластин, що мають схильність до викривлення при спіканні.
Порошок отримують дробленням попередньо переробленої стружки в кульових млинах і на бігунках (величина частинок порошку 0,04 ... 0,1 мм). Подрібнені порошки поділяються на фракції при просіюванні через металеві або шовкові сита. Змішання порошків проводиться в барабанах або кульових млинах, спікання - в газових або електричних печах при витримці від 15 хв до 24 год п залежно від розмірів виробів і спікливості матеріалу. Для підвищення точності деталей їх після спікання калібрують.
Заготовки із пластмас.
Застосування пластмас дозволяє отримувати заготовки складної форми і малої маси. Для навантажених детвлей застосовують армування заготовок металом. Механічна обробка деталей з пластмас або повністю виключається, або зводиться до мінімуму. Заміна чорних і кольорових металів пластмасами в умовах масового виробництва знижує собівартість для чорних металів в 1,5-3,5 рази, а для кольорових - в 5 - 10 разів.
У практиці використовують такі методи виготовлення заготовок з пластмас: пресування, литьевое пресування або лиття під тиском для дрібних деталей (маса 5 ... 10 кг); автоклавного лиття для деталей масою до 30 кг; контактна і вихровий формування для середніх і великих деталей; волочіння і екструзія для профілів без обмеження довжини.
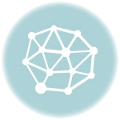
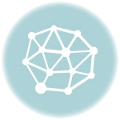
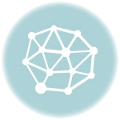
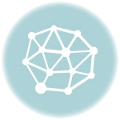