- Головна
- інформація
- застосування матеріалів
- Інформація для виготовлення склопластику
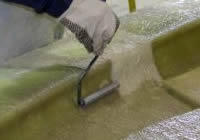
- склопластик
- смола
- матеріали зі скловолокна
- ровинг
- стекломата
- склотканина
- гелькоут (gelcoat)
- макет і матриця
- технології
Склопластик це матеріал, що складається з двох основних компонентів. Це матеріал зі скловолокна (скловолокно, склотканина, стекломата), який служить для армування (посилення) вироби, і смоли, що є сполучною.
Матеріали для виготовлення склопластику.
Смола є сполучною матеріалом і тому до вибору смоли треба підійти найбільш відповідально, особливо при відсутності досвіду виготовлення склопластикових виробів. Якщо при виборі склотканини або стекломата можна задовольнятися рекомендаціями фахівців, тому що цим вибором визначаються, в основному, механічні властивості готового виробу, то різна смола вимагає різних технологічних процесів.
Поліефірна смола, в основному, використовується для виготовлення цільних деталей
Хочемо також нагадати, що на властивості смол і на їх робочі параметри досить сильно впливають температурні характеристики приміщення, в якому проводяться роботи, і його проветриваемость. Часом для кращого застигання матрицю з виробом поміщають в спеціальну сушильну камеру. Це допомагає значно прискорити процес отримання готового виробу. Найміцніші вироби виготовляються в автоклавах під великим тиском і при високій температурі.
Сама смола досить тендітна, і саме стекломатеріал надає їй необхідну міцність і гнучкість
Матеріали зі скловолокна
Для виготовлення склопластиків використовується скловолокно, ровинг, стекломата, склотканина та інші стекломатеріали.
Найпоширеніші це ровинг, стекломата і склотканина.
Ровінг це скловолокно зібране в пучок і намотане на бобіну. Ровінг схожий на некрученого Склонитки. Укладання ровінгу проводиться спеціальним пістолетом, в який, під час роботи, подається ще смола і каталізатор.
Стекломата складається з хаотично розташованих волокон, а склотканина виглядає як звичайна тканина. Найбільше зміцнення дають склотканини. Скломати дають меншу міцність, але вони більш легкі в обробці і в порівнянні зі склотканиною краще повторюють форму матриці.
Стекломата може бути дуже тонким, а буває товстим, як ковдру. Скломати розрізняються по товщині і щільності, але поділяють їх за вагою одного квадратного метра матеріалу в грамах: 300, 450, 600. Чим тонше мат, тим більше складну поверхню він дозволяє вивести, з великою кількістю граней і різких переходів. Товстий мат (600 або 900) дозволяє набрати товщину вироби і домогтися необхідної міцності. При створенні товстих виробів робота проходить в кілька етапів. Викладається кілька листів для отримання першого шару і дається час на застигання. Потім додатково, уже на тверду поверхню, укладаються додаткові аркуші мату для надання необхідної товщини. Якщо спробувати укласти відразу всі верстви, то велика ймовірність, що готовий виріб пожолобиться, стягнеться.
склотканина
Склотканини бувають різної товщини. Склотканини також використовуються для додання жорсткості і обсягу готового виробу. Як і будь-яка тканина, склотканина неоднаково працює за різноспрямованого розтягуванні. Тому для надання необхідної жорсткості склотканина укладається під різними кутами. Скловолокно в склотканини грає важливу роль. Воно повинно добре просочуватися смолою і утримувати її між волокнами. На це властивість пропітиваемості в склотканини впливає наявність в ній і кількість парафіну. На відповідальні вироби бажано вибирати склотканини без парафіну. Парафін також можна випалювати перед застосуванням.
До слова про міцність. Як це не дивно прозвучить, але чим менше смоли в скловолокна (за умови його повної просочення і відсутності бульбашок), тим міцніше буде готовий виріб і тим менше виявиться і його вага.
Гелькоут (gelcoat)
Для додання кольору готової деталі. а також для захисту від зовнішніх впливів використовується особливий матеріал гелькоут (gelcoat - гелеве покриття). Можна сказати, що гелькоут це та-ж смола, але з додаванням барвника. Його можна підібрати за кольором або створити свій відтінок колеровочні складами. Крім того, шар гелькоута збільшує термін служби виробу, захищає від впливів навколишнього середовища і приховує структуру склопластику. Готовий виріб буде мати рівну (залежить від якості матриці) поверхню, потрібного кольору.
Гелькоут бувають внутрішніми і зовнішніми (topcoat).
Внутрішній гелькоут наноситься першим шаром в матрицю. Після того як гелькоут затвердів, укладається скловолокно і смола. У цьому процесі криється один важливий момент. Якщо шар гелькута буде в одному місці занадто тонкий, то може статися таке: чи в цьому місці буде просвічувати структура скловолокна, або гелькоут може взагалі відійти і зморщитися. Тому вкрай важливо користуватися правильними матеріалами і слідувати технології. Для рівномірного нанесення гелькоута часто використовують не кисті, а фарбопульти. Так вдається значно скоротити кількість браку і зменшити витрату матеріалу. Але для розпилення гелькоут повинен бути більш рідким, ніж для ручного нанесення. В даний час у продажу є готові гелькоути для нанесення пензлем і для напилення.
Зовнішній гелькоут (topcoat) наноситься після того, як виріб вийняли з матриці. Тут він виконує роль фарби. Завдяки присутності в складі топкоут парафіну поверхню після затвердіння не залишається липкою, добре шліфується і полірується. Топкоут можна виготовити самим на базі гелькоута або смоли, додавши розчин парафіну в Стиролі.
Макет і матриця
Для виготовлення виробів з склопластику перше, що необхідно, - створити його макет. У деяких випадках макетом може бути вже існуючий виріб, яке Ви хочете розмножити. Наприклад: бампер автомобіля. Для ще не існуючих виробів макет може бути виготовлений різними способами: фанера, пластилін, пінопласт і т. Д. Від того, наскільки правильно зроблений макет, буде залежати якість майбутніх виробів. Більш того, якщо необхідно, щоб у деталі, яка буде потім створюватися, була ідеально рівна поверхня, над її якістю доведеться попрацювати вже на макеті. Чим більше гладким і рівним буде макет, тим менше роботи буде потрібно потім, при виготовленні і доведенні матриці.
Ще до створення макета необхідно зрозуміти, чи можна виготовити деталь цілком чи ні. Справа в тому, що при роботі з склопластиками і іншими подібними матеріалами необхідно, щоб готову деталь після застигання можна було витягти з матриці, нічого не пошкодивши при цьому. Можливо, деталь матиме таку форму, що її доведеться виготовляти з декількох частин, а потім скріплювати їх один з одним.
Матриця створюється за макетом. Це найвідповідальніший момент. Перш за все макет покривається тонким шаром воску. Цю процедуру можна порівняти з поліруванням автомобіля. Після того як макет підготовлений, на нього наноситься шар спеціального матричного гелькоута. Це покриття в подальшому дозволить вивести поверхню матриці практично до дзеркального блиску. Матричний гелькоут гущі, ніж звичайний, і лягає більш товстим шаром.
Після того як встане цей шар, починається укладання стекломатеріала. Спочатку більш тонкого (стекловуаль, ...). Він дозволить точно повторити всі вигини і контури макета. Далі бажано дати підсохнути першому шару. Потім вже можна викласти ще кілька шарів більш товстого матеріалу (мат, склотканина), але відразу набирати товщину не варто, інакше матрицю може повести (зігнути і покоробити). При створенні матриць на прості деталі можна спростити процедуру.
Якщо матриця буде рознімної, то при її виготовленні робляться спеціальні перегородки навколо макета, що розділяють його на сегменти. Виклавши основний, після його застигання перегородки виймаються і, обробивши кромки першого сегмента матриці, викладаються інші. Для правильного позиціонування сегментів один щодо одного в першому при формуванні робляться спеціальні ямки. Коли будуть формуватися наступні сегменти, ці ямки будуть заповнені смолою і скловолокном, і з'являться горбки. Ці пари і дозволять при майбутньому використанні правильно скріпити різні частини матриці воєдино. Для скріплення сегментів матриці в ребрах всіх окремих частин свердлити отвори під кріпильні болти.
Для того щоб матриця була міцною і добре тримала форму, після її виготовлення, перш ніж вийняти макет, до матриці пріформовивают ребра жорсткості. Залежно від її розмірів це може бути міцний сталевий каркас або невеликі фанерні або дерев'яні ребра.
Готова матриця, якщо макет був виготовлений акуратно, може і не вимагати додаткової обробки, але часто доводиться виводити поверхні, шліфувати і полірувати матрицю до блиску. Тільки тоді можна отримати ідеальну деталь. А до кузовним елементам взагалі потрібна особлива увага.
Потім починається довгий процес вощіння. Матрицю доводиться ретельно натирати воском кілька разів з перервами. Віск потрібно не просто намазувати, а розтирати до отримання тонкої, гладкою, невидимою плівки. Якщо цього не зробити, то поверхня готового виробу буде не гладкою, а шорсткою.
Після, а часом і замість вощіння іноді використовують спеціальні рідини, які, висихаючи, створюють плівкове покриття, що запобігає потраплянню смоли або гелькоута на матрицю, чого ніяк не можна допускати. Як можна і дряпати її поверхню. В іншому випадку смола може намертво прирости до матриці, і тоді процедуру шліфування, полірування і вощіння доведеться повторювати знову. Часом використовують спеціальні склади, обробивши якими матрицю можна знімати з неї до 100 виробів, але старий добрий віск завжди залишається самим зрозумілим і надійним засобом.
Процес створення матриці, описаний вище, є досить поширеним варіантом, використовуваним в більшості фірм, але існують і інші, більш складні технології.
Власне, далі можна приступати до виготовлення деталей. Шар гелькоута в принципі не обов'язковий, але, по-перше, він надає більш закінченого вигляду готового виробу, а будучи кольоровим, дозволяє заощадити на фарбуванні або взагалі від неї відмовитися, а по-друге, він захищає матрицю від скловолокна, яке насправді дуже навіть абразивно, т. е. дряпає.
технології
Технологій виробництва виробів зі скловолокна існує кілька. Варто відразу обмовитися, що ці методи використовуються і при роботі з іншими армирующими матеріалами, такими, як карбон, кевлар, інші ткані матеріали і їх поєднання.
Ручне (контактна) формування. Цей спосіб найпростіший і дешевий (якщо не брати до уваги витрат на кваліфіковану робочу силу). Просочення скловолокна здійснюється валиком або пензлем, які повинні бути стійкими до смол. Волокно або відразу укладається в форму, або вже після просочення. Обробка скловолокна креслення валиками сприяє кращому розподілу смоли між волокнами. Потім укаточнимі валиками проводять остаточну укочування склотканини, видавлюючи пухирці повітря і рівномірно розподіляючи смолу по всьому об'єму. Вкрай важливо не допустити, щоб під шаром склотканини залишалися бульбашки повітря. Якщо виріб застигне з таким шлюбом, це місце буде ослаблено аж до можливого наскрізного продавлювання. Такі брачком також можуть перешкодити подальшій обробці вироби, вимагати його відновлення або повної заміни. У будь-якому випадку будуть витрачені додаткові матеріали, праця, а також гроші.
Ручний метод може бути кілька механізований. Існують змішувачі, подають смолу з каталізатором через валик, і інші пристосування. Але укочувати все одно доводиться своїми руками.
Гідність ручного методу цілком очевидно: просто і дешево. Але будь-яка економія може мати і зворотний бік. Якість готових виробів дуже сильно залежить від кваліфікації робітників. І умови праці при такому підході досить шкідливі. Крім того, дуже складно домогтися великої продуктивності. Однак для невеликих фірм і малих обсягів роботи цей метод найкращий.
Метод напилення рубаного ровінгу. Цей підхід куди більш технологічний. У ньому використовується не скловолокно, а Склонитки, яка подається в подрібнювач спеціального пістолета, де робиться на короткі волокна. Потім пістолет «випльовує» їх разом з порцією смоли і каталізатора. В повітрі все змішується і наноситься на форму. Але після цієї процедури все одно масу необхідно прикатать, щоб видалити бульбашки. Далі затвердіння відбувається як завжди.
Такий спосіб виглядає дуже заманливо і просто. Здавалося б, стій і поливай зі шланга. Але є один суттєвий недолік, через який цей спосіб не настільки популярний, - занадто велика витрата смоли. Виріб виходить дуже важким, і, так як волокна не переплетені один з одним, механічні властивості такого склопластику дещо гірше. Крім того, до шкідливим парам смол подмешивается суспензія дрібних частинок скла від подрібнювача, дуже шкідливих для легенів людини.
Метод намотування. Цей специфічний метод призначений для виготовлення пустотілих круглих або овальних секційних компонентів, типу труб або резервуарів. Таким чином робляться вітрильні щогли, вудки, рами велосипеда, глушники автомобілів і т. Д. Скловолокна пропускаються через ванну зі смолою, потім через натяжні валики, службовці для натягу волокна і видалення надлишків смоли. Волокна намотуються на сердечник з необхідним перетином, кут намотування контролюється відношенням швидкості руху візка до швидкості обертання. Як намотування нитки на шпульку швейної машинки. В результаті виходять міцні і легкі вироби.
Метод препрегів. В даному випадку використовуються не окремі смола і тканину, а так звані препреги - попередньо просочена смолами склотканина. Скловолокно попередньо просочується предкаталізірованной смолою під високою температурою і великим тиском. При низьких температурах такі заготовки можуть зберігатися тижні і навіть місяці. При цьому смола в Препреги знаходиться в напівтвердий стан. При формуванні препреги укладаються в матрицю і закриваються вакуумним мішком. Після нагріву до 120 -1800 ° C смола переходить в текучий стан, і препреги під дією вакууму приймає потрібну форму. При подальшому підвищенні температури смола застигає.
Вся проблема цього методу в необхідності нагрівального обладнання, особливо автоклава. З цієї причини виготовляти великі деталі дуже складно. Але і плюси очевидні. Використання вакууму дозволяє значно знизити ймовірність появи повітряних бульбашок і істотно скоротити частку смоли в готовому виробі.
Існують і інші технології - пултрузії, RFI, RTM і ін. - практично на всі випадки життя. Вибір тієї чи іншої технології залежить від необхідних обсягів, складності виробу і кількості грошей.