Н а стадії проектування розробники стикаються з необхідністю візуальної оцінки зовнішнього вигляду виробів, правильності їх конфігурації, можливості збуту розроблюваних виробів та іншими питаннями. Відповіді на них вимагають наявності реальної моделі (прототипу) вироби, максимально наближеною до його комп'ютерної моделі.
Створення прототипу або прототипування є обов'язковим етапом процесу розробки будь-якого нового вироби. Моделі-прототипи допомагають оцінити зовнішній вигляд і ергономіку розроблюваного виробу, перевірити функціональність конструкції і внести необхідні зміни ще до запуску виробу у виробництво. Створення якісного прототипу, максимально схожого на майбутній виріб, - дуже непросте завдання. Доводиться вирішувати проблеми точного повторення геометричної форми і зовнішнього вигляду виробу, збирання вироби та пошуку матеріалів, максимально схожих на закладені в конструкторської документації. Традиційні способи виготовлення моделей трудомісткі, мають низьку точністю і поганий повторюваністю при відтворенні. Тому останнім часом все більшу популярність завойовують технології швидкого прототипування (Rapid Prototyping), яке іноді називають 3D печаткою (3DPrinting), тобто пошарового створення фізичного об'єкта, який відповідає математичної моделі вироби в форматі STL (Stereolithography Text Language), спочатку розробленого для процесу стереолітографії і в даний час є графічним стандартом представлення даних про моделі для систем швидкого прототипування. Використовуючи швидке прототипування. можна виготовляти корпуси деталей, пробні і тестові екземпляри, які дозволяють оцінити зовнішній вигляд, пропорції, ергономічність і сумісність майбутніх виробів до виготовлення дорогих ливарних форм або штампів, тобто, до запуску цих виробів у виробництво. Швидке прототипування значно дешевше і зручніше інших технологій (для установок швидкого прототипування або 3D принтерів, як і для звичних паперових 2D принтерів, характерні простота використання, легкість завантаження картриджів, можливість експлуатації в офісі, автономність, постановка завдань в чергу друку, друк з будь-якого комп'ютера локальної мережі). На відміну від традиційних методів виготовлення прототипів, швидке прототипування виробів не передбачає видалення матеріалу (фрезерування, свердління, сточування) або зміна його форми (штампування, кування, вигин, розкочування), а виконується за допомогою пошарового нарощування матеріалу, з якого складається модель, до освіти єдиного цілого - готового виробу. Особливість технології знімає всі обмеження на внутрішню структуру одержуваної моделі, в процесі створення якої всі внутрішні компоненти вироби, в тому числі і рухливі, виявляються розміщеними згідно із заданими координатами.
Технології швидкого прототипування відносяться до методів, заснованим на додаванні матеріалу (на відміну від класичної механообработки). Їх прийнято поділяти на кшталт витратних матеріалів на рідкі, порошкоподібні і листові твердотільні. Процеси з рідкими витратними матеріалами поділяються, в свою чергу, на процеси затвердіння за допомогою контакту з лазером, затвердіння електрозаряженних рідин або затвердіння попередньо розплавленого матеріалу. Процеси з порошкоподібними матеріалами здійснюють скріплення частинок під впливом лазера або вибіркового нанесення сполучних компонентів. Процеси з твердотільними листовими матеріалами можуть бути класифіковані за способом їх з'єднання: лазером або шаром сполучного матеріалу.
Швидке прототипування включає в себе кілька етапів, першим з яких є розробка математичної моделі вироби в форматі STL. Ця модель розбивається на тонкі поперечні шари за допомогою спеціальної програми, причому товщина кожного шару дорівнює роздільної здатності устаткування по координаті Z. Потім здійснюється пошарове синтез або пошарове "вирощування" моделі або готового виробу безпосередньо по електронних даних без використання технологічної оснастки. Перевагами цієї технології є швидкість, точність і зниження витрат на НДДКР. Швидке прототипування особливо привабливо для виготовлення дослідних, одиничних, ексклюзивних і унікальних зразків, оскільки не вимагає виготовлення спеціального оснащення і мінімізує ручну працю. Воно широко використовується в машинобудуванні, електронної та електротехнічної промисловості, поліграфії, медицині, ювелірній справі, архітектурному моделюванні і т.д. дозволяючи оцінити зовнішній вигляд виробу, провести різні випробування і перевірити виріб на наявність конструкторських помилок; крім того, швидке прототипування застосовується для виготовлення оснастки при необхідності виготовлення партії деталей.
Принципова схема всіх установок швидкого прототипування приблизно однакова: спеціальне математичне забезпечення установки розбиває модель на ряд плоских паралельних перетинів (рис. 1), віддалених один від одного на мале (0,05 - 0,4 мм) відстань, що визначається вимогами установки. При цьому кожне перетин виконано із зовнішнім і внутрішнім контурами різної складності. Потім тонкий шар матеріалу (ламінованого паперу, паперу, фотополімера, полімерного або металевого порошку, полімерної нитки, воску, спеціального силікатного піску і т. Д.) Наносять на робочий стіл (елеватор) установки, відтворюючи перші перетин вироби, після чого елеватор зміщується вниз на один крок, і наноситься наступний шар, і так далі. Так шар за шаром відтворюється повний набір перетинів математичної моделі, повторюючи форму необхідного вироби. При цьому на деякому шарі може виявитися, що окремі елементи "повисають" в повітрі, оскільки вони повинні кріпитися до верхніх шарів. Щоб уникнути такої проблеми, в 3D моделі будується система підтримок (підпірок) на кожен такий елемент. Послідовне з'єднання (нашарування) плоских об'єктів-перетинів призводить до синтезу вироби-прототипу.
Схема всіх установок для виготовлення прототипів приблизно однакова: спеціальне математичне забезпечення установки розбиває модель на ряд плоских паралельних перетинів (рис. 1), віддалених один від одного на мале (0,05 - 0,4 мм) відстань, що визначається вимогами установки. При цьому кожне перетин виконано із зовнішнім і внутрішнім контурами різної складності. Потім тонкий шар матеріалу (ламінованого паперу, паперу, фотополімера, полімерного або металевого порошку, полімерної нитки, воску, спеціального силікатного піску і т. Д.) Наносять на робочий стіл (елеватор) установки, відтворюючи перші перетин вироби, після чого елеватор зміщується вниз на один крок і наноситься наступний шар, і так далі. Послідовне з'єднання (нашарування) плоских об'єктів-перетинів призводить до синтезу вироби-прототипу.
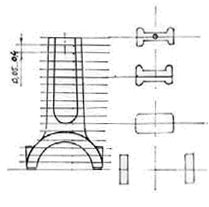
низькі температури переробки;
можливість паралельного виготовлення декількох деталей, якщо вони вписуються в робочу зону установки;
прототипи, розміри яких перевищують габарити робочої зони установки, можна виготовляти по частинах, а потім збирати в єдине ціле (наприклад, склеювати);
легкість експлуатації: після того, як модель виготовлена, потрібно тільки дістати її з установки, відокремити від пластикової основи і видалити матеріал підтримки. Ніяка спеціальна обробка моделей не потрібно;
прототипи зберігають форму, точність і інші якості протягом необмеженої кількості часу (в цій технології повністю відсутнє поняття усадки матеріалу).
Недоліки технології Fused Deposition Modeling (FDM).
наявність швів між шарами;
необхідність постійного руху головки екструдера для запобігання її засмічення застиглим матеріалом;
в певних випадках в процесі виготовлення моделі необхідно створювати підпори для підтримки звисаючих частин;
мала зсувна міцність отриманих моделей;
збільшення тривалості процесу для великих площ;
можливі коливання температури протягом циклу обробки, що призводять до розшарування моделі;
недостатньо гладка поверхня створюваної моделі;
деякий оплавлення попереднього шару при накладенні розплавленого матеріалу. Тому даний метод має обмеження на мінімальний розмір зазорів в створюваному виробі.