Назва роботи: КОНТРОЛЬ ПАРАМЕТРІВ ПЛІВОК І ТЕХНОЛОГІЧНИХ РЕЖИМІВ ЇХ НАНЕСЕННЯ
Предметна область: Фізика
Опис: Найбільш важливий контроль в камері так як в залежності від його результатів регулюються режими процесу росту плівки що дозволяє усунути операції підгонки її параметрів після нанесення. Метод мікрозважування в основному використовується у виробництві гібридних ІМС полягає у визначенні приросту маси Δm підкладки після нанесення на неї плівки. При цьому середню товщину плівки визначають за формулою: де площа плівки на підкладці; питома маса нанесеної речовини. При вимірюванні товщини плівки зважуванням вважають що щільність.
Розмір файлу: 143.5 KB
Роботу скачали: 53 чол.
КОНТРОЛЬ ПАРАМЕТРІВ ПЛІВОК І ТЕХНОЛОГІЧНИХ РЕЖИМІВ ЇХ НАНЕСЕННЯ
Отримання високоякісних плівок з наперед заданими і відтворюваними параметрами зумовлює необхідність суворого контролю при їх нанесенні. Особливості контролю параметрів тонкоплівкових елементів визначаються малими товщинами наносяться плівок (від декількох десятків до сотень нанометрів). Параметри плівок контролюють безпосередньо в процесі їх нанесення в вакуумній робочій камері, і після нанесення, т. Е. Поза камерами. Найбільш важливим є контроль в камері, так як в залежності від його результатів регулюються режими процесу росту плівки, що дозволяє усунути операції підгонки її параметрів після нанесення.
Розглянемо основні способи вимірювання та контролю таких параметрів плівок, як товщина, електричний опір, адгезія і найважливішого технологічного режиму # 151; швидкості нанесення. Залежно від призначення плівок зазвичай визначають метод їх контролю і контролюють один або два параметри.
Вимірювання товщини плівок. Товщину плівок вимірюють такими найбільш поширеними методами, як мікрозважування і многолучевая интерферометрия.
Метод мікрозважування, в основному використовується у виробництві гібридних ІМС, полягає у визначенні приросту маси Δ m підкладки після нанесення на неї плівки. При цьому середню товщину плівки визначають за формулою:
де # 151; площа плівки на підкладці; # 151; питома маса нанесеної речовини.
Цей метод простий, але вимагає, щоб форма підкладки була простою, а її поверхня # 151; в хорошому стані. Крім того, на точність вимірювань впливає питома маса нанесеного матеріалу, яка може змінюватися в залежності від умов технологічних режимів (залишкового тиску, забруднень молекулами газу і ін.).
При вимірюванні товщини плівки зважуванням вважають, що щільність нанесеної речовини дорівнює щільності масивного. Під ефективною товщиною плівки розуміють товщину, яку вона мала б, якби утворить її речовина була рівномірно розподілена по поверхні з щільністю, рівною щільності масивного речовини.
Чутливість методу зважування становить 1 # 151; 10 мкм / м і залежить від чутливості ваг і площі плівки на підкладці
Метод багатопроменевої інтерферометрії. застосовуваний для виміру товщини непрозорих плівок, заснований на спостереженні в мікроскоп інтерференційних смуг, що виникають при розгляді в монохроматичному світлі двох поверхонь, розташованих під кутом один до одного.
Перед вимірюванням отримують на зразку так звану сходинку # 151; різку бічну кордон плівки на підкладці. Для цього маскують частину підкладки при осадженні плівки або хімічно видаляють частину обложеної плівки. У мікроскоп спостерігають зсув інтерференційних смуг (рис. 17). Чергуються світлі і темні інтерференційні смуги з кроком L на поверхні, як плівки, так і підкладки зміщуються відносно один одного у їх межі на значення l.

Мал. 17. Зрушення інтерференційних смуг
Вимірюючи за допомогою мікроінтерференціонного мікроскопа зсув будь-якої певної смуги, розраховують товщину плівки по формулі
де # 151; довжина хвилі монохроматичного світла, дорівнює 0,54 мкм; - крок між сусідніми інтерференційними смугами; l # 151; зміщення інтерференційної смуги.
Точність цього методу вимірювання товщини плівки становить 15 # 151; 30 нм.
Якщо плівка прозора, в місці "сходинки" на неї і підкладку осаджують додатково непрозору, добре відбиває світло металеву плівку (наприклад, алюмінію), товщина якої, щоб зменшити внесену похибку, повинна бути значно меншою товщини вимірюваної плівки.
Вимірювання електричного опору плівок. Електричний опір плівок вимірюють резистивним датчиком із зовнішнім вимірювальним приладом. В основному цей метод застосовують при контролі виготовлення резисторів гібридних ІМС, і він заснований на тому, що в міру потовщення плівки в процесі росту опір її зменшується. Це дозволяє безпосередньо при нанесенні контролювати опір плівки, а при досягненні номінальної її товщини припинити процес.
При вимірах (рис. 18) попередньо виготовляють спеціальну контрольну підкладку (свідок) 1 з ізоляційного матеріалу (скла, ситалла). на яку наносять плоскі контактні площадки 2 з срібла або іншого матеріалу високої провідності. Потім цю підкладку # 151; "Свідок" встановлюють в робочу камеру якомога ближче до робочої підкладці 3. Це необхідно для того, щоб обидві підкладки при нанесенні плівки перебували в однакових умовах. Резистивну плівку наносять на контрольну і робочу підкладки одночасно.
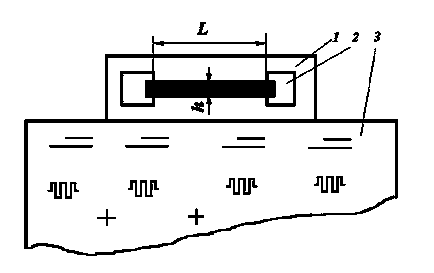
При монтажі резистивного датчика в робочу камеру з'єднують контакти "свідка" з вимірювальним мостом, в результаті чого опір "свідка" реєструється зовнішнім приладом. В процесі осадження резистивного матеріалу ріст плівки відбувається як на робочих підкладках, так і на контрольній, т. Е. Формується "резистор-свідок". У міру зростання опір плівки зменшується і відповідно зменшується опір "резистора-свідка". При досягненні номінального (заданого) опору наноситься плівки на "свідку" по ланцюгу зворотного зв'язку надходить сигнал, яким або вимикається харчування випарника, або закривається заслінка.
Оскільки вважають, що характеристики плівок на підкладці і "свідку" однакові, зовнішній вимірювальний прилад може бути відградуйованих одиницях опору (при постійній температурі підкладки).
Похибка вимірювання опору при контролі цим методом становить приблизно ± 10% і визначається нерівномірністю товщини плівки по поверхні (т. Е. Відмінністю опорів "свідка" і робочої підкладки). а також похибками вимірювань.
Зовнішній вимірювальний прилад можна також отградуировать в одиницях довжини. Товщину плівки в цьому випадку визначають за формулою
де ρ # 151; питомий опір плівки; R св # 151; опір плівки на "свідку" між контактами; L. і h # 151; довжина і ширина плівки на "свідку".
Чутливість методу складає 1 # 151; 5 нм, а гранична товщина вимірюваних плівок # 151; близько 1 мкм.
Під товщиною плівки при цьому розуміють товщину, яку мав би її шар, якби його питомий опір було одно питомому опору масивного металу. Внаслідок невизначеності значення питомого опору наносяться плівок точність вимірювань цим методом невелика.
Вимірювання адгезії плівок. Зчеплення (прилипання) поверхонь різнорідних тіл називають адгезію. Адгезія плівки до підкладки залежить від матеріалу плівки і швидкості її осадження, а також від чистоти поверхні і температури підкладки.
В даний час не існує доступних промислових методів високоточного вимірювання адгезії тонких плівок до підкладки. Тому виконують порівняльний контроль, при якому вимірюють зусилля відриву плівки від підкладки напаяти на її поверхню металевим циліндром. У центрі вільного торця циліндра закріплюють гнучкий тросик, пов'язаний через важіль з чашкою ваг. Щоб по зусиллю відриву Р визначити адгезію G a. необхідно точно знати площу контакту F k і виключити викликає нерівномірний розподіл зусилля по його площі перекіс циліндра. Розраховують адгезію за формулою
Зазвичай площа торця циліндра близько 1 мм 2. Для отримання надійних даних слід виміряти адгезію кілька разів, контролюючи, чи не відбулося відрив за місцем спаяний і не розчинилася чи плівка в припої.
Різновид цього методу # 151; контроль адгезії металевих плівок по відриву від підкладки за допомогою тонкої золотої або алюмінієвого дроту, що приєднується до плівки термокомпрессіі. При цьому площа контакту складає 50 # 151; 200 мкм 2. що дозволяє більш точно визначати адгезію локальних ділянок плівки.
Вимірювання швидкості нанесення плівок. Найбільш поширений контроль швидкості нанесення плівок методом кварцового датчика, який іноді називають резонансно-частотним. Як датчик при цьому методі використовують включений в контур генератора частоти кварцовий елемент.
Принцип дії кварцового датчика заснований на залежності частоти генерованих сигналів від зміни маси кварцового елемента при нанесенні на його поверхню плівки. Зі збільшенням маси кварцового елемента його резонансна частота падає. Для лінійної ділянки залежності частоти від маси нанесеної плівки справедливо наступне співвідношення:
де т 0 і f про # 151; маса і резонансна частота кварцового елемента до нанесення плівки; Δ m і Δ f # 151; зміна маси кварцового елемента і резонансної частоти після нанесення плівки.
Таким чином, за зміни швидкості (зсуву) резонансної частоти, зафіксованому вимірювальним приладом, визначають швидкість росту плівки.
Основною частиною кварцового датчика (рис. 19) є кварцовий елемент 5 круглої або квадратної форми, на обидві поверхні якого для подачі напруги наносять тонкі шари золота або срібла. Кварцовий елемент кріпиться на ізоляторі 4 і закривається кожухом 3. який вставляється в масивний мідний тримач 2. охолоджуваний по трубці 1 проточною водою. У кожусі і тримачі є наскрізний отвір 6 для пропускання потоку частинок матеріалу, що наноситься до кварцового елементу.
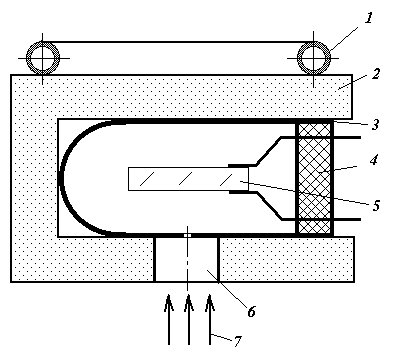
Необхідність ефективного охолодження утримувача пояснюється тим, що кристали кварцу дуже чутливі до змін температури. При нанесенні плівок джерела випромінюють значну кількість теплоти, що викликає підвищення температури кварцового елемента. Нестабільність температури кварцового елемента є основною причиною неконтрольованого зміни частоти. Для виключення похибок вимірювань через нестабільність температури датчика тримач охолоджують.
Цим методом можна також з урахуванням геометричних розмірів кварцового елемента і маси нанесеної плівки виміряти її товщину, використовуючи наступну формулу:
де F п # 151; площа кварцового кристала, покрита плівкою наноситься речовини; ρ п # 151; щільність наноситься плівки.
Точність вимірювання товщини тонких металевих і діелектричних плівок в інтервалі від 10 нм до 5 мкм становить ± 10%.
Випускаються серійно прилади дозволяють задавати необхідну товщину плівки, після нанесення якої подається сигнал, який зупиняє процес. Для виконання точних вимірювань прилади градуируют окремо для кожного матеріалу.
Максимально допустима сумарна товщина плівки, що наноситься на кварцовий датчик, визначається максимальним зсувом частоти і приблизно становить 20 мкм алюмінію. Максимальне значення вимірюваної товщини можна збільшити, перекриваючи періодично кварцовий елемент екраном.
Істотним недоліком методу є те, що крім градуювання по осаджувати матеріалу необхідна також періодична чистка кварцових елементів від обложеної плівки.