Кераміка є третім найбільш широко використовуваним промисловістю матеріалом після металів і полімерів. Вона є найбільш конкурентоспроможним в порівнянні з металами класом матеріалів для використання при високих температурах. Великі перспективи відкриває використання транспортних двигунів з деталями з кераміки, керамічних матеріалів для обробки різанням і оптичної кераміки для передачі інформації. Це дозволить знизити витрату дорогих і дефіцитних металів: титану і танталу в конденсаторах, вольфраму і кобальту в ріжучих інструментах, кобальту, хрому і нікелю в теплових двигунах.
Основними розробниками і виробниками керамічних матеріалів є США і Японія. У таблиці 14.1 наведено класифікацію основних видів кераміки.
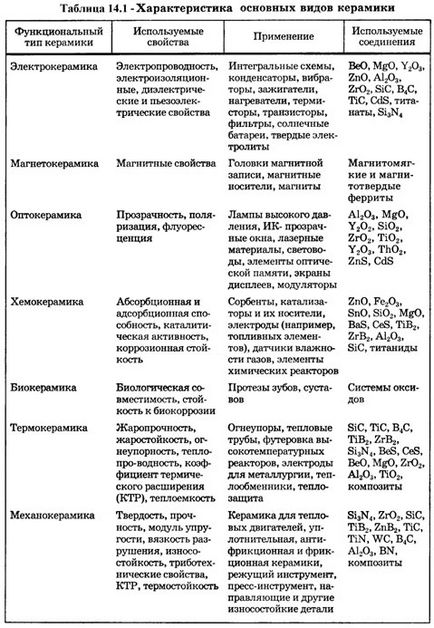
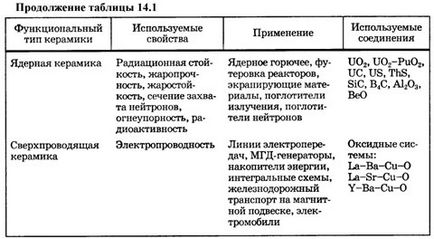
Керамічна технологія передбачає наступні основні етапи: отримання вихідних порошків, консолідацію порошків, т. Е. Виготовлення компактних матеріалів, їх обробку і контроль виробів.
При виробництві високоякісної кераміки з високою однорідністю структури використовують порошки вихідних матеріалів з розміром частинок до 1 мкм. Подрібнення здійснюється механічним шляхом за допомогою тіл, що мелють, а також шляхом розпилення матеріалу, що подрібнюється в рідкому стані, осадженням на холодних поверхнях з парогазової фази, віброкавітаціонним впливом на частинки, що знаходяться в рідині, за допомогою високотемпературного синтезу і іншими методами. Для надтонкого помелу (частки менше 1 мкм) найбільш перспективні вібраційні млини, або Аттритори.
Консолідація керамічних матеріалів складається з процесів формування і спікання. Розрізняють такі основні групи методів формування:
- Пресування під дією стискає тиску, при якому відбувається ущільнення порошку за рахунок зменшення пористості;
- Пластичне формування видавлюванням прутків і труб через мундштук (екструзія) формувальних мас з пластифікаторами, що збільшують їх плинність;
- Шлікерного лиття для виготовлення тонкостінних виробів будь-якої складної форми, в якому для формування використовують рідкі суспензії порошків.
При переході від пресування до пластичного формуванню і шлікерного лиття збільшуються можливості виготовлення виробів складної форми, проте ускладнюється процес сушіння виробів і видалення пластифікаторів з керамічного матеріалу. Тому для виготовлення виробів порівняно простої форми перевага віддається пресування, а більш складною - екструзії і шлікерного лиття.
При спіканні окремі частинки порошків перетворюються в моноліт і формуються остаточні властивості кераміки. Процес спікання супроводжується зменшенням пористості і усадкою.
Часто застосовуються поєднані методи консолідації, що поєднують формування з спіканням, а в деяких випадках - синтез утворюється з'єднання з одночасним формуванням і спіканням.
Обробка кераміки і контроль є основними складовими в балансі вартості керамічних виробів. За деякими даними, вартість вихідних матеріалів і консолідації складає всього лише 11% (для металів 43%), в той час як на обробку доводиться 38% (для металів 43%), а на контроль 51% (для металів 14%). До основних методів обробки кераміки відносяться термообробка і розмірна обробка поверхні. Термообробка кераміки проводиться з метою кристалізації межзеренного стеклофази. При цьому на 20 - 30% підвищуються твердість і в'язкість руйнування матеріалу.
Більшість керамічних матеріалів з працею піддається механічній обробці. Тому основною умовою керамічної технології є отримання при консолідації практично готових виробів. Для доведення поверхонь керамічних виробів застосовують процес шліфування алмазними колами, електрохімічний, ультразвукову та лазерну обробку. Ефективне застосування захисних покриттів, що дозволяють залікувати дрібні поверхневі дефекти - нерівності, ризики і т. Д.
Для контролю керамічних деталей найчастіше використовують рентгенівську і ультразвукову дефектоскопію.
Міцність хімічних міжатомних зв'язків, завдяки якій керамічні матеріали мають високу твердість, хімічної і термічної стійкістю, одночасно обумовлює їх низьку здатність до пластичної деформації і схильність до крихкого руйнування. Більшість керамічних матеріалів має низьку в'язкість і пластичність і відповідно низьку тріщиностійкість. В'язкість руйнування кристалічної кераміки становить близько 1 - 2 МПа / м 1/2. в той час як для металів вона складає понад 40 МПа / м 1/2.
Можливі два підходи до підвищення в'язкості руйнування керамічних матеріалів. Один з них традиційний, пов'язаний з вдосконаленням способів подрібнення і очищення порошків, їх ущільнення і спікання. Другий підхід полягає в гальмуванні зростання тріщин під навантаженням. Існує кілька способів вирішення цієї проблеми. Один з них заснований на тому, що в деяких керамічних матеріалах, наприклад в діоксиді цирконію ZrO2. під тиском відбувається перебудова кристалічної структури. Вихідна тетрагональна структура ZrO2 переходить в моноклинную, що має на 3 - 5% більший обсяг. Зростаючи, зерна ZrO2 стискають тріщину, і вона втрачає здатність до поширення (рисунок 14.1, а). При цьому опір крихкому руйнуванню зростає до 15 МПа / м 1/2.
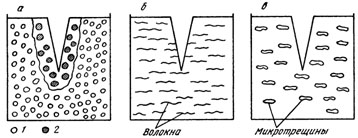
Малюнок 14.1 - Схема зміцнення конструкційної кераміки включеннями ZrO2 (а), волокнами (б) і дрібними тріщинами (в): 1 - Тетрагональна ZrO2; 2 - моноклінний ZrO2
Другий спосіб (рисунок 14.1, б) складається в створенні композиційного матеріалу шляхом введення в кераміку волокон з міцнішого керамічного матеріалу, наприклад карбіду кремнію SiC. Розвивається тріщина на своєму шляху зустрічає волокно і далі не поширюється. Опір руйнуванню склокераміки з волокнами SiC зростає до 18 - 20 МПа / м 1/2. істотно наближаючись до відповідних значень для металів.
Третій спосіб полягає в тому, що за допомогою спеціальних технологій весь керамічний матеріал пронизують микротрещинами (рисунок 14.1, в). При зустрічі основний тріщини з мікротріщин кут в вістрі тріщини зростає, відбувається затуплення тріщини і вона далі не поширюється.
Певний інтерес представляє фізико-хімічний спосіб підвищення надійності кераміки. Він реалізований для одного з найбільш перспективних керамічних матеріалів на основі нітриду кремнію Si3 N4. Спосіб заснований на утворенні певного стехіометричного складу твердих розчинів оксидів металів в нітриді кремнію, які отримали назву сіалонов. Прикладом високоміцної кераміки, що утворюється в цій системі, є сіалони складу Si3-х Alx N4-х oх. де х - число заміщених атомів кремнію та азоту в нітриду кремнію, що становить від 0 до 2,1. Важливою властивістю сіалоновой кераміки є стійкість до окислення при високих температурах, значно вища, ніж у нітриду кремнію.