2.2.2 Інтенсивна пластична деформація
Формування нано структури массівньтх металевих зразків може бути здійснено методом інтенсивної деформації. За рахунок великих деформацій, що досягаються крутінням при квазігідростатіческом високому тиску, рівноканальної кутової пресуванням і використанням інших способів, утворюється фрагментована і разоріентіровать структура.
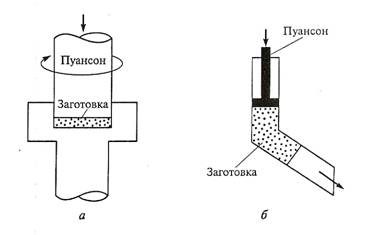
Малюнок 4 Схеми інтенсивної пластичної деформації:
а - кручення під високим тиском; б - рівноканальне кутовий пресування
При крученні під високим тиском ступінь деформації зазвичай регулюється числом оборотів. Так, для міді, піддамо тієї 2, 3 і 4 оборотам, середній розмір зерен склав (162 ± 19) нм, (149 ± 12) нм і (85 ± 8) нм відповідно. При проведенні деформування крутінням і рівноканальної кутової пресуванням розмір зерен наноматеріалів становить близько 100 нм. Гідність методу інтенсивної пластичної деформації полягає в можливості отримання беспорістих наноматеріалів, причому останні можуть бути досить значних розмірів, маючи на увазі можливості рівноканального кутового пресування.
2.2.3 Контрольована кристалізація з аморфного стану
Як відомо, багато хто з елементів, металевих сплавів і з'єднань (наприклад, Si, Se, сплави Fe, Ni, Al, Zr і ін.) Можуть перебувати в аморфному стані, тобто характеризуються тільки ближнім порядком при відсутності далекого порядку в розташуванні атомів.
Методи отримання аморфних матеріалів досить різноманітні і добре розроблені в різних варіантах: конденсація з газової фази, гарт з рідкого стану, іонна імплантація, високоенергетичне подрібнення і ін. Якщо аморфні матеріали піддавати контрольованому відпал рекристалізації, керуючи процесами зародження і зростання кристалітів, то можна отримати наноматеріали з кристаллитами невеликого розміру (близько 10-20 нм і менш) і практично безпористі.
Слід також мати на увазі, що в залежності від умов гарту з рідкого стану можна виділити три типи наноструктур [[13]]:
1) повна кристалізація безпосередньо в процесі загартування з розплаву і освіту одно- або багатофазної як звичайної полікристалічної структури, так і наноструктури;
2) кристалізація в процесі загартування з розплаву протікає не повністю і утворюється аморфно-кристалічна структура;
3) гарт з розплаву призводить до утворення аморфного стану, яке трансформується в наноструктуру тільки при подальшій термічній обробці.
Для переробки аморфних порошків, одержуваних, наприклад, газовим розпиленням рідких розплавів, використовують прийоми гарячої обробки тиском, як це було продемонстровано японськими дослідниками [[14]] на прикладі об'ємних заготовок високоміцного сплаву Al - Y - Ni - Co.
2.2.4 Технологія плівок і покриттів
Ці методи досить універсальні щодо складу наноматеріалів, які можуть бути виготовлені практично в безпористого стані в широкому діапазоні розмірів зерен, починаючи від 1-2 нм і більше. Єдине обмеження - це товщина плівок і покриттів - від декількох часток мікрона до сотень мікрон. Використовуються як фізичні методи осадження, так і хімічні методи, а так само електроосадження і деякі інші прийоми. Поділ методів осажаенія на фізичні і хімічні умовно, оскільки, наприклад, багато фізичних прийоми включають хімічні реакції, а хімічні методи стимулюються фізичними впливами.
У Таблиця 2 наведені основні методи отримання наноструктурних плівок на основі тугоплавких сполук (карбідів, нітридів, боридів) [[15]]. Порушення дугового розряду в азотної або вуглецевмісної атмосфері - один з найбільш поширених варіантів технології іонного осадження; як джерело іонів металів використовують металеві катоди. Електродугове випаровування вельми продуктивно, але супроводжується утворенням металевого крапельної фази, звільнення від якої вимагає спеціальних конструктивних заходів. Цього недоліку позбавлений магнетронний варіант іонно-плазмового осадження, в якому мішень (катод) розпорошується за рахунок бомбардування іонами плазми газового розряду низького тиску, яка формується між катодом і анодом. Поперечний постійне магнітне поле локалізує плазму у розпилюється поверхні мішені і підвищує ефективність розпилення.
Таблиця 2 Основні методи отримання наноструктурвих плівок на основі тугоплавких сполук
Газоподібні і конденсовані прекурсори
Нітриди та бориди
На Малюнок 5 показана схема магнетронного розпилення з мішенню прямокутної форми, на поверхні якої в районі виходу і входу магнітних силових ліній виникає «доріжка розпилення». Напилювані підкладки (на схемі не показані) розташовані над мішенню і для досягнення рівномірності плівок за складом і структурі піддаються обертанню.
Магнетронного напилення дуже універсально, його можна застосовувати не тільки для металевих, але і для неметалічних мішеней (і, отже, для отримання відповідних плівок). При магнетронном напиленні температури підкладок невеликі (менше 100-200 ° С), що розширює можливості отримання наноструктурних плівок з невеликим розміром зерен і аморфних плівок. Однак швидкості напилення в кілька разів нижче, ніж в разі дугових методів.
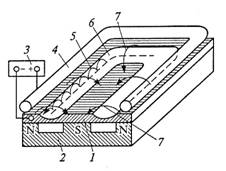
Малюнок 5 Схема установки магнетронного розпилення
1 - катод-мішень; 2 - постійний магніт; 3 - джерело живлення; 4 - анод; 5 - траєкторії руху електронів; 6 - зона (доріжка) розпилення; 7 - силові лінії напруженості магнітного поля
При іонно-променевої обробки вибивання атомів мішені відбувається за рахунок бомбардування її поверхні іонними пучками. На малюнку 6 приведена схема установки бінарного іонно-стимульованого осадження нітридних плівок. Металеві іони утворюються при бомбардуванні метталіческіе мішені іонами інерних газів або азоту з джерела 3, а джерело 2 використовується для бомбардування безпосередньо плівки (в разі іонів азоту плівки синтезованих нітридів можуть бути сверхстехіометрічнимі).
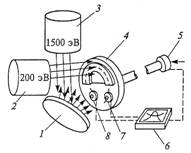
Малюнок 6 Схема установки бінарного іонно-стимульованого осадження нітридних плівок [15]:
1 - мішень (Ti, Zr, Hf); 2 - джерело іонів аргону, ксенону, неону або азоту для підкладки; 3 - джерело тих же іонів для мішені; 4 - підкладка; 5 - механізм обертання; 6 - фіксатор координат; 7 - лічильник щільності струму; 8 - лічильник швидкості осадження
Стосовно до деяких металів і сплавів (Ni, Cu, Ni-P, Ni-Mo, Ni-W та ін.) Для отримання наноматеріалів виявився досить ефективним метод імпульсного електроосадження, коли реалізується висока швидкість зародження кристалітів і за рахунок адсорбційно-десорбційних пригнічують процесів забезпечується їх низька швидкість росту.
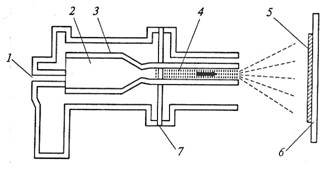
Малюнок 7 Схема установки газотермічного напилснія:
1 - введення газових сумішей; 2 - змішувач; 3 - система охолодження; 4 - плазмовий ствол; 5 - покриття; 6 - підкладка; 7 - введення порошку
Іонно-плазмова обробка поверхні, включаючи імплантацію, використовується стосовно до різних матеріалів (металів, сплавів, напівпровідників, полімерів та ін.) Для створення поверхневих сегрегації і Нанорельєф, що корисно для багатьох практичних застосувань.
Інформація про роботу «Особливості отримання нових матеріалів із застосуванням нанотехнологій»