1.2 Катодне розпорошення
Катодного розпилення є одним з найбільш відомих способів нанесення покриттів. Ще в 1852 році було встановлено, що при проходженні електричного струму через розріджені гази відбувається руйнування катода і на стінках камери осідає покриття.
Схеми пристроїв для нанесення покриттів методом катодного розпилення представлені на малюнку 3.
У найпростішому варіанті (рисунок 7.18, а) пристрій складається з розпорошується катода 5, на який подають потенціал від 1 до 10 кВ, і анода з розташованими на його поверхні виробами 3. Між катодом і анодом розміщують, як правило, заслінку. На початковій стадії процесу виробляють відкачування вакуумної камери до максимально можливої ступеня розрядження (
10-1 ... 10-2 Па), потім здійснюють напуск в робочу камеру інертного газу (аргону). При цьому тиск в камері становить 1 ... 10 Па.
Малюнок 3 - Принципові схеми систем катодного розпилення: а) діодний; б) діодний зі зміщенням; в) тріодної; г) з автономним іонним джерелом: 1 - камера; 2 - подложкодержатель; 3 - деталі (підкладки); 4 - мішень; 5 - катод; 6 - екран; 7-джерело живлення (постійного струму або високочастотний); 8 - підведення робочого газу; 9 - відкачка; 10 - термокатодом; 11 - анод; 12 - іонний джерело
Наступною операцією є створення між анодом і катодом різниці потенціалів (0,5. 10 кВ). В результаті в робочій камері виникає газовий розряд. При впливі іонів на поверхню катода йде руйнування оксидних шарів, практично завжди присутніх на поверхні. Розпорошені атоми металу взаємодіють з активними газами (киснем, азотом), і в результаті осідають шари, забруднені неконтрольованими домішками. При цьому, однак, спостерігається зниження парціального тиску хімічно активних газів в камері, тому, як правило, завжди на початковій стадії осадження покриття проводиться на технологічну заслінку. По закінченню деякого часу заслінка відкривається, і йде осадження покриття на поверхню виробу. Розпорошені атоми при своєму русі до підкладки зазнають численні зіткнення. В результаті атоми розпилюється мішені втрачають свою енергію, що викликає, як правило, зниження адгезійної міцності осаждаемого покриття. З метою зменшення втрат енергії розпорошених атомів в процесі їх руху в газовій фазі відстань між анодом і катодом роблять мінімальним.
Процес розпилення може проводитися в хімічно активному середовищі, яка спеціально створюється в робочій камері. В цьому випадку процес називають реактивним катодних нанесенням покриття. Таким методом на поверхні підкладки формують шари з оксидів, нітридів, карбідів металу.
Таким чином, катодного розпилення характеризується наступними перевагами:
1) процес розпилення газової фази безінерційна, при припиненні подачі потенціалу на катод генерація газової фази також практично миттєво припиняється;
2) низький тепловий вплив на виріб (нагрівається тільки поверхня катода);
3) можливість розпилення тугоплавких металів;
4) можливість отримання покриттів різного хімічного складу (наприклад, методом реактивного катодного розпилення);
5) забезпечення високої рівномірності осадження покриттів;
6) зберігається стехіометричний склад покриттів при їх отриманні розпиленням мішені зі сплаву.
Основні недоліки катодного розпилення:
- низькі швидкості росту покриття (до 1нм / с);
- низькі енергія частинок, ступінь іонізації і, як наслідок цього, невисока адгезія покриттів;
- висока ступінь забруднення покриттів атомами газової фази;
- наявність в покритті високої щільності радіаційних дефектів, причиною появи яких є вплив на поверхню високоенергетичних електронів, негативно заряджених іонів.
З метою зниження ступеня забруднення покриттів, підвищення їх адгезії рекомендується підтримувати температуру підкладки в процесі осадження досить високою (400 ... 500 ° С). У ряді випадків для отримання якісних покриттів використовують бомбардування зростаючої плівки іонами інертного газу, що досягається шляхом подачі на підкладку негативного потенціалу або застосуванням додаткового іонного джерела.
При подачі на підкладку потенціалу зміщення одночасно з процесом осадження покриття відбувається розпорошення зростаючого покриття, яке, як правило, є неоднорідним і визначається структурою поверхневого електричного поля. Тому за певних умов може спостерігатися селективне розпилення і навіть повне видалення покриття в певних місцях. Іншою особливістю технології отримання покриттів катодних розпиленням є різке зниження швидкості напилення покриття при реактивному розпиленні в результаті утворення на мішені хімічної сполуки, що має низьку електричну провідність.
Так як швидкість осадження покриттів катодних розпиленням є низькою, вона використовується, в основному, для отримання тонких захисних і антифрикційних покриттів на прецизійних деталях машин і приладів (опори газових підшипників, приладові підшипники ковзання і кочення). Як матеріал покриття використовують дисульфід молібдену, золото, срібло, свинець, індій.
1.3 магнетронного розпилення
Магнетронного розпилення - різновид діодного катодного розпилення. Освіта парів розпилюючи речовину відбувається в результаті бомбардування мішені іонами робочого газу, які утворюються в плазмі аномального тліючого розряду. Найбільш проста схема магнетронного розпилення приведена на малюнку 4.
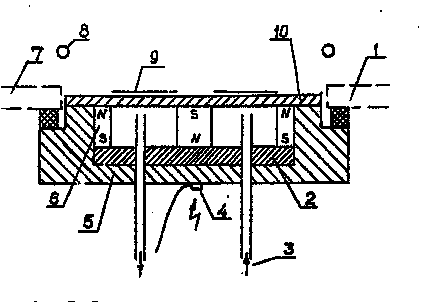
Малюнок 4 - Схема пленарному магнетронній системи: I - прокладки; 2 - підстава; 3 - водяний канал; 4, 5 - корпус: 6 - постійні магніти; 7 - вакуумна камера; 8 - анод; 9 - зона ерозії; 10 - катод - мішень
Безпосередньо під мішенню розміщені постійні магніти, які створюють практично паралельне поверхні катода магнітне поле. Між анодом і катодом запалюється аномальний газовий розряд. В результаті з катода вибиваються електрони, які захоплюються магнітним полем, і роблять в цьому полі під дією сили Лоренца спиралевидное рух. Електрони, захоплені магнітним полем, проводять додаткову іонізацію атомів інертного газу, що збільшує, таким чином, інтенсивність іонного бомбардування поверхні катода і, відповідно, викликає підвищення швидкості розпилення.
До основних взаємопов'язаним характеристиками, що визначає швидкість розпилення мішені, відносять напруга розряду, струм розряду, тиск робочого газу і індукцію магнітного поля поблизу поверхні катода. Як робочий газ в магнетронних розпилювальних системах зазвичай використовується аргон.
Магнетронниє системи крім високої швидкості розпилення мають ряд специфічних особливостей, основною з яких є відсутність бомбардування підкладки високоенергетичними вторинними електронами, які є основним джерелом радіаційних дефектів в покритті і нагріву підкладок. У магнетронній розпилювальної системі вторинні електрони захоплюються магнітної пасткою і не бомбардують підкладку, що забезпечує їй порівняно низьку температуру. Це дозволяє використовувати ці системи для нанесення покриттів на підкладки з матеріалів з відносно низькою термостійкістю (пластмаси, полімерів, паперу).
Слід зазначити, що магнетронні системи відносяться до низьковольтних систем розпилення, напруга живлення яких не перевищує 1000 В постійного струму. Робоча напруга, як правило, становить 300 ... 700 В; на мішень зазвичай подається окремий потенціал, а анод має нульовий потенціал. Магнетрон система може працювати в діапазоні тисків від 10-2 до 1 Па і вище. Найважливішими параметрами, багато в чому визначають характер розряду в ній, є геометрія електродів і величина магнітного поля, індукція якого біля поверхні мішені
Процес магнетронного нанесення покриттів характеризуються такими показниками:
-Швидкість розпилення - (4 ... 40) · 10-5 г / (см2 · с);
-Швидкість осадження покриттів - 50 ... 60 нм / с ;.
-питома випаровуваність - β≈3 · 10-6 г / Дж ;.
- енергія розпорошених частинок - 10 ... 20 еВ.
Переваги даного методу в порівнянні з іншими методами нанесення покриттів:
1) висока швидкість осадження;
2) практично повна відсутність перегріву поверхні деталі, при цьому електрони захоплюються магнітним полем і тому не викликають утворення радіаційних ефектів;
3) висока рівномірність покриттів;
4) низький ступінь забруднення плівок, т. К. Процес нанесення покриття протікає при досить низькому тиску р = 10-2 Па.
В останні роки активно розробляються методи реактивного магнетронного напилення. При їх реалізації є ряд технологічних особливостей, які необхідно враховувати. При розпилюванні мішені частина реактивного газу зв'язується розпорошеним речовиною, а частина - безперервно оновлюється поверхнею мішені. Відбувається своєрідна відкачка реактивного газу. На цьому принципі, як відомо, засновані іонно-гетерні вакуумні насоси. Швидкість відкачки при розпилюванні залежить від площі осаждаемого покриття, швидкості росту покриття, площі мішені, швидкості видалення утворилася на мішені плівки і проявляється в різкому падінні тиску реактивного газу в камері з початком процесу розпилення.
При реактивному магнетронном напиленні швидкість росту покриття залежить від парціального тиску реактивного газу. При малих значеннях тиску реактивного газу з мішені розпорошується метал і хімічна реакція має місце на підкладці. При більш високому тиску на поверхні мішені утворюється плівка хімічної сполуки і швидкість розпилення різко падає, так як швидкість розпилення хімічних сполук (оксидів, нітридів, карбідів) значно нижче, ніж чистих металів. З метою зниження даного ефекту розроблено ряд пристроїв, в яких подача реактивного газу здійснюється безпосередньо до підкладки, а інертного - до розпилюється мішені (малюнок 5).
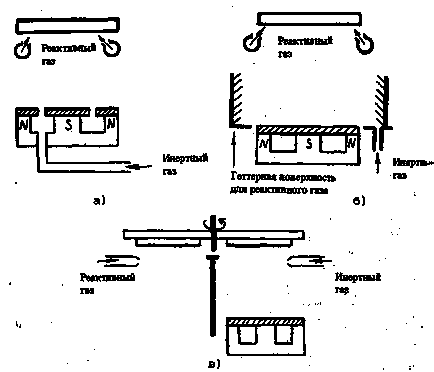
Малюнок 5 - Схеми пристроїв реактивного магнетронного розпилення шляхом поділу областей знаходження інертного і реактивного газів: а - за допомогою селективної подачі газів; б - із застосуванням гетерні поверхні; в - за допомогою перегородки і відносного руху підкладки
Розроблено також пристрої, в яких процеси іонного розпилення і термічного випаровування об'єднані в єдиний розпилювально-випарний процес. Це досягається, наприклад, при магнетронном розпиленні матеріалу, що знаходиться в рідкому агрегатному стані. У цьому випадку значно підвищується продуктивність процесу розпилення і коефіцієнт використання матеріалу мішені. Це пов'язано з тим, що процес іонного розпилення відбувається в поверхневому шарі металу товщиною 0,3. 0,8 нм, і на нього витрачається менше 3% енергії, що підводиться. Інша енергія переходить в основному в тепло, внаслідок чого доводиться інтенсивно охолоджувати мішень. У розроблених пристроях енергія, яка при розпилюванні з твердої фази втрачається у вигляді тепла, використовується на випаровування речовини.
Для здійснення цього процесу між плоским тигель, виготовленим з тугоплавкого немагнітного матеріалу, і водоохлаждаемой магнітною системою роблять невеликий (2-3 мм) зазор, що перешкоджає відведенню тепла від тигеля в процесі розпилення вміщеній в тиглі мішені (рисунок 6).
Малюнок 6 - Схема пристрою для розпилення матеріалів рідкої фази: 1 - тигель; 2 - розплавлена мішень; 3 анод; 4 - екран; 5 - магнітна система; 6 - подложкодержатель
Робочий об'єм відкачують, потім напускають аргон, і між тигель, який виконує роль мішені, і анодом прикладають напругу, поступово збільшуючи щільність струму на мішені до такої величини, при якій починається інтенсивне розплавлення знаходиться в тиглі матеріалу. При цьому плавиться спочатку зона, у якій локалізована плазма, потім - центральна частина мішені і, нарешті, крайова її область. При певній щільності струму на мішені починається інтенсивне випаровування матеріалу з розплаву. При досягненні високої пружності парів розпорошується матеріалу над катодом починається процес самораспиленія. В цьому випадку можна припинити напуск аргону, що істотно знижує забруднення плівки залишковими газами. Крім високої ефективності використання енергії, розпилювально-испарительная система дозволяє досягти високих швидкостей осадження.
З цілю підвищення адгезії покриттів до підкладки підводять, як правило, негативний потенціал зсуву
100 В, що дозволяє збільшити щільність і енергію іонів.