Вперше термобарьерние покриття (TBC) були успішно випробувані в секції турбіни випробувального двигуна в середині 1970-их. До початку 1980-их вони почали працювати на соплових лопатках газотурбінних двигунів літаків, і сьогодні вони працюють на соплових і робочих лопатках. В удосконалених двигунах, в доступному для огляду майбутньому, як очікується, навантаження на ці покриття буде тільки збільшуватися.
Найпершими керамічними покриттями для аерокосмічної галузі були спечені емалі. Перше з цих покриттів було розроблено NASA і Національним Бюро стандартів (NBS). Спечена емаль використовувалася в авіаційних двигунах протягом 1960-их. Пізніше були розроблені покриття, що наносяться газополуменевим напиленням. З різних керамічних матеріалів, які були застосовані в якості теплового бар'єру необхідно виділити оксид алюмінію, оксид цирконію, стабілізований оксидом магнію і оксидом кальцію. Останній був найбільш підходящим і широко використовувався. Матеріал покриття зв'язку для цих покриттів, якщо він взагалі використовувався, був зазвичай ніхромом або молібденом. Втім, оксид алюмінію і оксид цирконію, стабілізований оксидом кальцію не мали належної довговічністю і не виявилися життєздатними матеріалами для вдосконалених ТВС. Поточна ера TBC почалася в середині 1970-их з розробки в NASA двошарового TBC, що складається з пористого нанесеного методом APS (air plasma spray, плазмового напилення в повітряній атмосфері) керамічного покриття з оксиду цирконію, стабілізованого оксидом ітрію (ZrO2-Y203), поверх нанесеного тим же методом металевого жаростійкого NiCrAIY сполучного покриття і з успішного випробування цього покриття на лопатках газової турбіни в експериментальному газотурбінному двигуні. Union Carbide був одним з перших розробників ТВС ZrO2-Y203 / MСrAIY (як M - Ni і / або Co). Перші покриття TBC на основі двоокису цирконію містили від 12 до 20% оксиду ітрію, який додавався, щоб повністю стабілізувати кубічну фазу. Пізніше, було доведено, що кращих робочих характеристик можна досягти, знижуючи рівень окису ітрію до 6 і 8%. Дослідження по TBC, в загальному, тепер підтримують уявлення, що ZrO2 / (6-8%) Y203 перевершує ZrO2 / (12-20%) Y203 для вдосконалених газових турбін, а ці TBC в свою чергу перевершують системи на основі оксиду цирконію, запропоновані раніше.
Системи термобарьерних покриттів широко використовуються в сучасних газотурбінних двигунах, щоб знизити температуру металевих поверхонь в секціях турбіни і камері згоряння. В авіаційних двигунах і енергетичних установках наземного базування широко застосовується практика нанесення термобарьерних покриттів, щоб задовольнити зростаючі вимоги збільшення ККД по паливу, зниження викиду NOx і зростання потужності і тяги. Компоненти турбіни, що піддаються впливу найбільш високих температур - камера згоряння, робочі лопатки ротора і соплової направляючий апарат турбіни високого тиску.
Система ТВС складається з чотирьох компонентів - кожен має помітно відрізняються фізичні, теплові, і механічні властивості, створюючи по суті комплексну структуру. Виріб з ТВС має витримати високу температуру, її циклічне зміна, і, як наслідок, напружений стан. Мінімальний термін служби не менше тисячі злетів і приземлень для комерційних реактивних двигунів і до 30 000 годин в промислових газотурбінних двигунах. Комбінація різних матеріалів і необхідних експлуатаційних умов робить TBC більш складними, ніж будь-яка інша система покриття. Чотири шару в сучасній системі TBC зроблені з різних матеріалів зі специфічними властивостями і функціями:
- основний сплав (безпосередньо матеріал вироби),
- сполучна покриття,
- термічно вирощений оксид (TGO),
- керамічне поверхневе покриття.
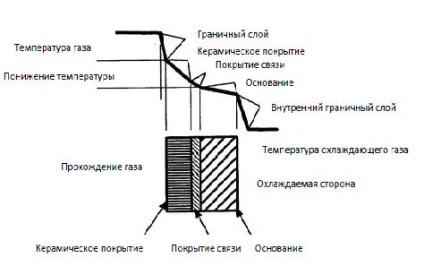
Схематичне уявлення темобарьерних покриття
Основний сплав - Суперсплав на основі нікелю або кобальту - матеріал, який охолоджується повітрям зсередини або через внутрішні порожнисті канали, таким чином, встановлюючи температурний градієнт поперек стінки вироби. Виріб з суперсплавів в монокристалічних або полікристалічних формах містить від 5 до 12 додаткових елементів, які додаються для підвищення питомих властивостей, таких як жаростійкість, пластичність, стійкість проти окислення, стійкість до гарячої корозії, а також для поліпшення ливарних властивостей.
Сполучна покриття - стійкий проти окислення металевий шар, з товщиною 75 - 150 мкм, він по суті диктує адгезію TBC. Покриття зв'язку зазвичай зроблено з NiCrAlY, або NiCoCrAlY, і нанесено плазмовим напиленням або електроннопроменевими методами фізичного осадження з парів (EB-PVD). Інший варіант покриття зв'язку зроблений з алюминидов Ni і Pt і наноситься гальванически з дифузійним алітуванням або хімічним осадженням з пари. Досить рідко сполучні покриття зв'язку можуть складатися з декількох шарів, що мають різний хімічний / фазовий склад.
При пікових експлуатаційних умовах температура сполучного покриття в газотурбінних двигунах зазвичай перевищує 700 ° C, приводячи до окислення сполучного покриття і неминучого формування третього шару - термічно вирощеного оксиду (TGO; товщина 1-15 мкм) між сполучною покриттям і керамічним поверхневим покриттям. Наскрізна пористість, яка завжди існує в поверхневому керамічному покритті, дозволяє легке проникнення кисню з експлуатаційної середовища до сполучній покриттю зв'язку. Крім того, навіть якщо поверхневе покриття було повністю щільним, надзвичайно висока дифузійна здатність кисню в керамічному поверхневому покритті на базі ZrO2 робить його «кіслородопрозрачним». Хоча формування TGO неминуче, ідеальне покриття зв'язку проектується, щоб гарантувати, що TGO формується як? -Al2O3 і що його зростання є повільнішим, однорідним, і бездефектне. Такий TGO має дуже низьку іонну диффузионную здатність для кисню і створює чудовий дифузний бар'єр, сповільнюючи подальше окислення сполучного покриття.
Поверхневі покриття зв'язку (МCrAlY) в порівнянні з дифузійними покриттями (алюмініди Ni і Pt) дозволяють більшу незалежність від основного сплаву і гнучкість при проектуванні властивостей сполучного покриття. Композиція покриття може бути оптимізована відповідно до очікуваним механізмам зносу при експлуатації. Сполучні покриття MCrAlY містять зазвичай чотири або більше елемента. Хром дає цим покриттям чудову корозійну стійкість в комбінації з хорошим опором окисленню. Для нанесення сполучних покриттів зазвичай використовуються або плазмового напилення або надзвукові методи, наприклад, HVOF (high velocity oxygen fuel). Після нанесення покриття вакуумна термообробка активує диффузионное з'єднання для оптимальної адгезії.
Існують різні способи нанесення керамічних покриттів на металеві основи, два основні методи - APS і ЕВ-PVD. Ці два методи виробляють мікроструктури з певними характерними ознаками.
Завдані плазмою TBC мають наступні мікроструктурні характеристики: "лускату" морфологію (товщина 1-5 мкм, діаметр 200 - 400 мкм) з межами між лусочками і вертикальними тріщинами. Типове поверхневе покриття APS має товщину 300 мкм, але в деяких промислових газотурбінних двигунах може досягати 600 мкм. Орієнтація тріщин і нормалі пір до теплового потоку зменшує теплопровідність поверхневого покриття з 2.3 Вт / мK для повністю щільного матеріалу до 0.8-1.7 Вт / мK.
Як правило, поверхневі керамічні покриття нанесені ЕВ-PVD (середня товщина 125 мкм), мають такі особливості мікроструктури: тонкі області полікристалічного YSZ з равноосной зернами (від 0.5 до 1 мкм) біля поверхні розділу метал / кераміка; стовпчасті зерна YSZ (діаметр 2-10 мкм) вирощені з області равноосной зерна до поверхні покриття; пористість в межах стовпчастих зерен; і вертикальні канали, між столбчатимі зернами.
Універсальність і низька вартість виробництва роблять APS TBC комерційно привабливими. Однак, через швидке збільшення мікроструктурних дефектів паралельних до поверхні розділу і шорсткості поверхні розділу, APS TBC в цілому мають більш короткі термоціклічние терміни служби ніж ЕВ-PVD TBC. Це робить APS TBC відповідним тільки для менш вимогливих додатків в авіаційних двигунах, типу камер згоряння, сопла, паливних випарників, стабілізаторів полум'я форсажній камери, і статорних лопаток. APS TBC надзвичайно добре працюють в промислових газотурбінних двигунах, включаючи застосування на соплових і робочих лопатках, через знижених робочих температур, температурних градієнтів і меншої кількості теплових циклів.
Перспективи подальшого розвитку ТВС можна охарактеризувати основними напрямками - пошук і розробка нових матеріалів, удосконалення архітектури покриттів і вдосконалення методів нанесення.
Один з напрямків розвитку матеріалів легування ZrO2 різними рідкоземельними катіонами. Ці добавки призводять до формування кластерів легирующего речовини, які знижують питому теплопровідність приблизно на 20-40%. Для ZrO2 стабілізованого Y2O3-Gd2O3-Yb2O3, питома теплопровідність знижується з 2.3-2.6 Вт / м / K для стандартного YSZ до 1.6-1.9 Вт / м / K. Можливо отримати системи з піковою температурою експлуатації до 1650C.
Традиційні матеріали (YSZ) продовжать грати головну роль в задоволенні технічних вимог аерокосмічної промисловості для збільшення терміну служби і ККД, оскільки впровадження нових, альтернативних високотемпературних конструкційних матеріалів - кераміки, керамічних композитів, интерметаллидов і жароміцних металевих сплавів досі перебуває на стадії наукових досліджень.
Існує серйозна мотивація, щоб розробити керамічні поверхневі покриття зі зменшеною високотемпературної теплопровідністю. Зменшена теплопровідність допоможе збільшити термін служби TBC, зменшуючи температуру основного металу і сповільнюючи термічно активізовані процеси, відповідальні за руйнування покриття і / або покращуючи ККД, дозволяючи функціонувати при більш високих температурах. Хоча пошук відповідної нової кераміки TBC триває, успіх, в кінцевому рахунку, буде заснований на більш повній оцінці всіх сприятливих характеристик, які зробили YSZ таким успішним TBC до теперішнього часу, і включенням цих характеристик в кераміку з більш низькою питомою теплопровідністю і більш високою допустимою температурою експлуатації.