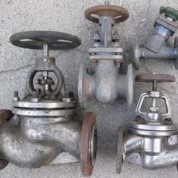
Діагностування стану засувок забезпечує виявлення акустично активних зон або зон концентрації механічних напруг корпусів засувок і оцінки в цих зонах як поверхневих порушень суцільності металу типу тріщин, так і внутрішніх несплошностей. При діагностуванні перевіряється герметичність як при експлуатації при робочих тисках діючого трубопроводу, так і при випробуваннях на герметичність на стендах відповідно до вимог НД.
Неруйнівний контроль (НК) корпусів засувок для магістральних трубопроводів є невід'ємною частиною робіт, які виконуються до і після капітального ремонту засувок.
Для проведення контролю корпусів засувок повинні бути забезпечені наступні умови:
- корпус повинен бути очищений від бруду, що відшаровується фарби і пухких продуктів корозії;
- ділянки корпусів, де повинні встановлюватися АЕ перетворювачі, а також підлягають УЗ, капілярному або магнітопорошковому контролю, повинні бути очищені від фарби і зачищені до металевого блиску;
- при контролі засувок на випробувальних стендах повинно бути забезпечено енергопостачання змінного струму напругою 220В;
- при контролі засувок з великими проходами повинні бути забезпечені підмостки або лісу для зручного розташування апаратури і дефектоскописта.
Підготовка засувки під контроль (очищення від бруду, що відшаровується фарби і пухких продуктів корозії) і видалення контактної мастила після АЕ і УЗ контролю, пенетрантов після капілярного контролю і магнітних суспензій після магнітопорошкового контролю в обов'язки дефектоскопистів не входять і виконуються спеціально виділеним персоналом. До керівництва та проведення робіт з контролю запірної арматури допускаються фахівці, атестовані по відповідним видам контролю відповідно до чинних Правил атестації фахівців неруйнівного контролю Ростехнагляду мають кваліфікацію не нижче II рівня.
При діагностуванні засувок використовують такі види контролю:
- контроль з використанням АЕ методу,
- капілярний (кольоровий) контроль;
- контроль напруженого стану металу корпусних деталей;
Візуальному контролю піддають засувки в разі забезпечення безпосереднього доступу до їх корпусам. Візуальний контроль зовнішньої поверхні корпусних деталей виробляють шляхом огляду неозброєним оком або за допомогою оптичних приладів зі збільшенням до 10. Внутрішня поверхня корпусу також повинна піддаватися візуальному контролю при забезпеченні доступу до неї. При візуальному контролі повинні бути виявлені неприпустимі дефекти поверхні основного металу і зварних з'єднань.
Контроль з використанням АЕ методу
АЕ контролю піддаються в обов'язковому порядку:
- нова засувка перед монтажем на трубопроводі;
- колишня в експлуатації і спрямована на капітальний ремонт;
арматура після капітального ремонту.
АЕ контроль проводять при стендових випробуваннях запірної арматури на міцність і щільність матеріалу корпусів. В процесі експлуатації засувки піддавати АЕ контролю можна тільки при забезпеченні безпосереднього доступу до корпусним деталям і можливості зміни тиску в трубопроводі відповідно до вимог технології АЕ контролю. У зв'язку зі складністю забезпечення на діючому трубопроводі необхідних умов для проведення АЕ контролю арматури при їх експлуатації рекомендується такий контроль проводити при гідроопрессовке окремих ділянок трубопроводу, наприклад, після капітального ремонту.
Герметичність затворів контролюють за допомогою АЕ течошукачів відповідно до інструкцій по експлуатації на них і оцінюється при цьому тільки якісно.
Капілярний (кольоровий) контроль
Капілярному контролю піддають ділянки поверхні корпусних деталей в зонах акустично активних джерел, виявлених при ЛЕ контролі, або в зонах концентрації механічних напруг, виявлених за допомогою магнітометричного індикатора напруги магнітного поля.
Ділянки поверхні, що піддаються кольоровому контролю, повинні бути ретельно очищені від бруду, фарби, пухких продуктів корозії і зачищені до металевого блиску.
Ультразвуковому контролю піддають ділянки тіла і зварних швів корпусних деталей з акустично активними джерелами, виявленими при АЕ контролі, або в зонах концентрації механічних напруг, виявлених за допомогою магнітометричного індикатора механічних напружень. При ультразвуковому контролі виявляють внутрішні дефекти (порушення цілісності металу) і дефекти, що розвиваються з внутрішньої поверхні корпусних деталей. Ультразвуковий контроль проводять з використанням прямих суміщених або прямих роздільно-сполучених перетворювачів з робочою частотою 2,5 МГц для виявлення внутрішніх дефектів тіла корпусних деталей і похилими суміщеними перетворювачами з робочою частотою 2,5 МГц і кутами введення по стали 65 ° для виявлення дефектів, що розвиваються з внутрішньої поверхні основного металу, а також при контролі зварних швів корпусних деталей.
Магнітопорошковий контроль допускається проводити замість кольорового при наявності відповідної апаратури і фахівців.
Контроль напруженого стану металу корпусних деталей
При неможливості проведення АЕ контролю засувки, але при забезпеченні безпосереднього доступу до їх корпусним деталям, при наявності відповідної апаратури і фахівців, допускається проведення контролю напруженого стану металу корпусних деталей за допомогою магнітометричного індикатора механічних напружень типу ІМНМ- 1 Ф. За допомогою індикатора знаходять лінії концентрації механічної напруги і коефіцієнти інтенсивності напружень вздовж цих ліній на поверхні, як основного металу, так і в районі зварних швів кор усних деталей арматури. Ділянки корпусних деталей в районі ліній концентрацій механічної напруги повинні бути обстежені з використанням кольорового або магнітопорошкового і ультразвукового методів контролю.
Радіографічному контролю в обов'язковому порядку піддають кільцеві зварні шви приварних патрубків, як на новій арматурі, так і на арматурі після капітального ремонту до монтажу на трубопроводі.
Оцінка результатів контролю
На основному металі корпусних деталей засувок неприпустимі тріщини, надриви, наплавлення, механічні пошкодження з гострими краями, раковини розміром в плані більш 4 мм і глибиною понад 15% товщини, несплошності округлої або удліненвой форми розміром більше 1,5 мм і глибиною більше З мм, корозійні пошкодження, виводять товщину деталі за мінусової допуск. Перехід від основного металу до наплавленого повинен бути плавним без підрізів і напливів, ширина і висота швів повинна бути рівномірною. Зварні шви приварювання патрубків для з'єднання з трубопроводом не повинні мати тріщин, прожогов, кратерів, грубої лускатий, підрізів глибиною більше 0,5 мм.
Контроль з використанням АЕ методу
При АЕ контролі реєструються акустично активні зони (джерела). Класифікацію джерел АЕ виконують з використанням наступних параметрів: число імпульсів, сумарний рахунок, активність, швидкість рахунки, амгiлітуда, енергія (або енергетичний параметр). У систему класифікації також входять параметри навантаження контрольованого об'єкта. Виявлені і ідентифіковані джерела поділяють на чотири класи:
- джерело 1 класу - пасивний джерело;
- джерело 2 класу - активне джерело;
- джерело З класу - критично активне джерело;
- джерело 4 класу - катастрофічно активний джерело.
Зони корпусних деталей із зафіксованими акустично активними джерелами 2, 3, 4 класів повинні бути обстежені з використанням кольорового, магнітопорошкового методів або магнітного індикатора тріщин на наявність поверхневих дефектів і за допомогою ультразвукового дефектоскопа на наявність внутрішніх дефектів.
Капілярний (кольоровий) контроль
При кольоровому контролі фіксації підлягають індикаторні сліди розміром більше 1 мм.
Не допускаються тріщини, а також дефекти, яким відповідають індикаторні сліди розміром:
- більше 10% товщини плюс 1 мм для стінок товщиною до 20 мм;
- більше З мм плюс 0,05 для стінок товщиною від 20 до 60 мм;
- більше 5 мм для стінок товщиною понад 60 мм.
При ультразвуковому контролі основного металу корпусних деталей фіксації підлягають несплошності з еквівалентної відбиває площею 10 мм2 для товщини до 50 мм і 15 мм 2 для товщини від 50 до 100 мм.
- з еквівалентної відбиває більше 20 мм 2 для товщини до 50 мм, і більше 30 мм 2 для товщини від 50 до 100 мм;
- непротяжних з еквівалентної відбиває від 10 до 20 мм 2 для товщини до 50 мм і від 15 до 30 мм 2 для товщини від 50 до 100 мм, якщо їх кількість більше 15 при мінімальній відстані між ними не менше 10 мм для товщини до 50 мм або не менше 15 мм для товщини від 50 до 100 мм, що проектуються на ділянку поверхні введення ультразвукових коливань розміром 200х300 мм.
Оцінка якості контрольованих ділянок корпусних деталей проводиться як при капілярному (кольоровому) контролі.
При магнітометричний контролі фіксуються лінії і зони найбільшої напруги деформованого стану (НДС) металу корпусних деталей засувок.
Лінії і зони ПДВ корпусних деталей повинні бути обстежені з використанням кольорового, магнітопорошкового методів або магнітного індикатора тріщин на наявність поверхневих дефектів і за допомогою ультразвукового дефектоскопа на наявність внутрішніх дефектів.
Корисні статті:
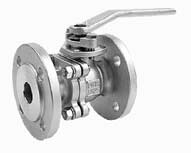
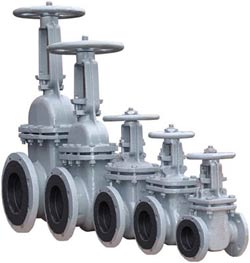
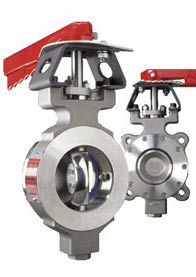
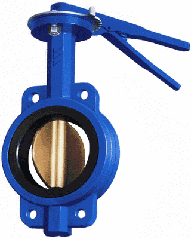