Технологія переробки нафти і газу. Частина 1
В даний час переважна більшість установок каталітичного крекінгу працює з використанням синтетичних микросферических цеолитсодержащих каталізаторів. Їх основними складовими частинами є носій і цеоліт.
Важливе значення в каталітичних системах відіграє носій активної речовини або як його ще називають - матриця. Матриця повинна забезпечувати збереження каталітичних властивостей цеоліту в умовах високих температур, охороняти його від впливу каталітичних отрут, створювати певну форму, гранулометричний склад і необхідну механічну міцність частинок каталізатора, забезпечувати доступність цеоліту компонента для молекул сировини.
У каталізаторах першого покоління матрицями служили синтетичні алюмосилікати, що містять невелику кількість кремнію, які отримували методом осадження алюмокремнегеля заданого складу з подальшою його термохимической обробкою водними розчинами з метою видалення оксиду натрію та формування пористої структури. У каталізаторах другого покоління в якості матриць найчастіше використовують спеціально синтезовані алюмосилікати, як правило, могокомпонентние, що містять 30-45% глинозему, який має мінімальну активність, але має комплексом властивостей, необхідних для забезпечення термічної стабільності каталізатора. Крім того, при синтезі матриці використовують стабілізатори, наприклад каолін, і сполучна - силікатні і алюмосилікатні золі або високогідратірованние гідрогелю.
Речовина матриці оточує кристали цеоліту, рівномірно розподіляючи їх і сприяючи інтенсивному протіканню массоі теплообмінних процесів. Воно суттєво впливає на термопаровую стабільність каталізатора. Матриця відповідальна за його механічну міцність, пористість і особливо за розподіл пор за розмірами.
Тверді каталізатори повинні володіти великою поверхнею. Чим більше площа контакту фаз, тим вище ймовірність протікання хімічних реакцій. У зв'язку з цим, практично всі тверді каталізатори являють собою високопористі речовини. Зазвичай загальна (сумарна внутрішня і зовнішня) поверхня каталізатора відноситься до одиниці його маси і називається питомою поверхнею. Залежно від типу пористого речовини і ступеня розвитку пористої структури його питома поверхня може змінюватися від 10 до 1500 м2 / г.
У каталізаторах повинні бути присутніми пори різного розміру. Найдрібніші - мікропори мають переважно діаметр 0,5-1,0 нм (10-9м). Найбільш часто вони утворюються в цеолітах і в їх обсязі в основному протікають хімічні перетворення. Діаметри більших - мезопор, багато більше розмірів адсорбованих молекул. Вони лежать в інтервалі від 1,5 до 200 нм. Мезопори є основними транспортними артеріями, за якими здійснюється підведення реагуючих молекул до активних центрів і відведення продуктів реакцій. Нарешті, найбільші - макропори, мають ефективні діаметри понад 200 нм і виконують роль великих транспортних проходів. Реакції в них практично не протікають, так як їх питома поверхня невелика (0,5-2,0 м2 / г). Необхідність наявності в каталізаторі всіх типів пір і їх певного розподілу за розмірами пов'язано з прискоренням протікання дифузійної стадії каталітичного процесу.
Матриця може бути неактивною, яка виконує функції підведення до цеоліту молекул сировини і відведення від нього продуктів крекінгу, або активної, на якій в цьому випадку здійснюється попередній крекінг великих молекул сировини. При залученні в сировині каталітичного крекінгу важких нафтових фракцій перевага віддається активним матрицями, до яких відносяться алюмосилікати і активний оксид алюмінію. Молекули оксидів алюмінію і кремнію, з'єднуючись між собою, утворюють частинки твердої фази з ефективним діаметром близько 3-20 нм. Зростаючись, вони формують гідрогель, в якому в проміжках між частинками твердої фази переважно сферичної форми знаходиться вода або водні розчини прореагировавших вихідних компонентів. При сушінні гідрогелю вода видаляється, а структурна сітка з пов'язаних між собою сферичний зберігається. В результаті виникнення міцних зв'язків між ними утворюється жорсткий кремнію алюмініевокіслородний каркас. Пори цього каркаса розглядаються як зазори між частинками. Матриця може бути мелкопористой (рис. 3.4, а), крупнопористой (рис. 3.4, б), а також містити весь набір пір. Її пористу структуру можна регулювати умовами осадження компонентів (температура, швидкість її зміни, рН середовища і т.д.). На хімічні та адсорбційні властивості матриці в значній мірі впливає наявність гідроксильних груп (ºSi-ОН або = Al-OH). Вони займають в основному вершини тетраедрів, що виходять на її внутрішню і зовнішню поверхню. Кількість цих груп можна регулювати температурою розжарювання каталізатора. Чим вище її значення, тим більша ймовірність протікання реакції дегідроксілірованія (2НО-® Н2О + Н +).
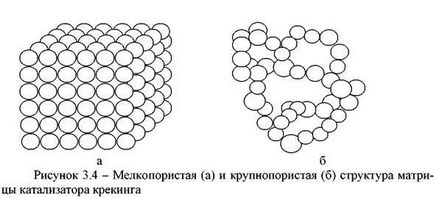
Шляхом включення в матрицю цеолітів і різних добавок - модифікаторів, можна впливати на різні процеси, що відбуваються при каталітичному крекінгу.
Цеоліт - алюмосилікати, що містять в своєму складі катіони лужних і лужноземельних металів (натрій, калій, кальцій, магній і т.д.). Вони відрізняються строго регулярною структурою пір, які в звичайних умовах заповнені молекулами води. Тому в процесі сушіння насичених водою цеолітів створюється видимість їх кипіння (цеоліти - киплячі камені, термін використовується американським вченим Кронштедом).
Загальна хімічна формула цеолітів:
його валентність, x, y, z - коефіцієнти.
Цеоліт бувають природними і синтетичними. Їх структурними елементами є кремніевоі алюмініевокіслородние тетраєдри (рис. 3.5), які з'єднані між собою в суцільний кристалічний каркас (рис. 3.6). З огляду на, що алюміній тривалентний, але має в кристалічній решітці чотири зв'язку, такий її фрагмент набуває частковий негативний заряд, компенсується катіоном, в якості якого найчастіше використовують натрій, калій, кальцій, барій, рідкоземельні метали і протон водню.
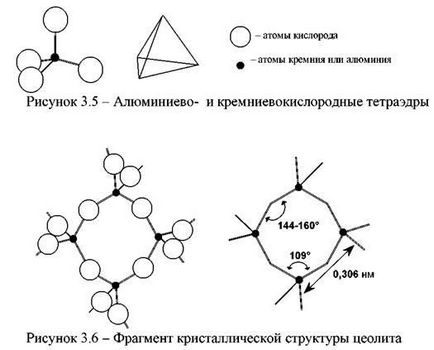
Тетраедри, з'єднуючись, утворюють кубооктаедр (так звані содалітовие осередки), з яких, в свою чергу, будуються елементарні осередки цеоліту, складові його кристалічний каркас.
Найбільш широке застосування в даний час знайшли синтетичні цеоліти типу A, X, Y і сверхвисококремнеземние (СВК) цеоліти. Вони відрізняються один від одного модулем (співвідношенням Si / Al), типом і кількістю катіонів, що припадають на елементарну комірку, а також її будовою і розміром пор. Найбільший інтерес для каталітичного крекінгу мають цеоліти типу Y і СВК.
Структура елементарної комірки цеолітів типу Y представлена на малюнку 3.7. Їх модуль зазвичай змінюється від 2,0 до 5,0. Кожна елементарна осередок має чотири входи в адсорбционную порожнину через двенадцатичленная кисневі кільця діаметром 0,8-0,9 нм. Ці цеоліти відрізняються підвищеною кислотостойкостью, термостійкість і каталітичної активністю в реакціях крекінгу, ізомеризації, алкілування і ін. Саме їх висока реакційна здатність визначила великий попит на них в нафтопереробці і нафтохімії, в тому числі в якості активного компонента в каталізаторах крекінгу.
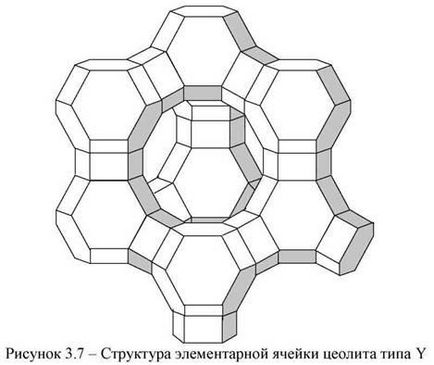
Цеоліт СВК знаходять останнім часом саме широке застосування в нафтохімії як високоефективні каталізатори процесів гідрокрекінгу, ізомеризації, алкілування і каталітичної депарафінізації нафтових фракцій. У США вони отримали фірмове позначення ZSM.
Модуль СВК цеолітів досягає величини 100-150 і вище. Як катіонів при їх синтезі використовують тетраалкілзамещенние аміни. Органічні радикали руйнуються при нагріванні до 400 ° С, а замість них залишаються протони, що і визначає високу реакційну здатність СВК цеолітів. Внаслідок низького вмісту алюмінію вони мають дуже високою кислотністю, термічної і термопаровой стабільністю. Значна реакційна здатність таких цеолітів і відповідний розмір пір дозволяють проводити з їх використанням селективний крекінг парафінових вуглеводнів. Тому при включенні цеоліту ZSM-5 в каталізатори крекінгу виходять бензини з максимальним октановим числом.
В даний час практично повсюдно відмовилися від використання в якості каталізаторів крекінгу природних і синтетичних алюмосилікатів, а також звичайних цеолітів типу Х і Y (з модулем до 4,0-4,5), так як вони мають відносно низьку термопаровой стабільністю і активністю. Для сучасних каталізаторів типовий модуль цеоліту типу Y вище 5,0. Такі цеоліти, звані ультрастабільнимі, отримують шляхом деалюмінірованія (видалення з кристалічної решітки атомів алюмінію) звичайних цеолітів типу Y з модулем 4,0-4,5 водяною парою або кислотами. При цьому модуль може бути доведений до 6,0 і навіть трохи вище.
Деякі зарубіжні фірми (зокрема Katalistiks) освоїли новий спосіб деалюмінірованія з одночасним збагаченням кристалічної решітки цеоліту кремнієм. Цю операцію здійснюють, використовуючи певні водні розчини з'єднань кремнію. При цьому модуль, наприклад, цеолітів типу Y може бути збільшений до 30 і вище. Такі цеоліти мають підвищеною кислотністю і надзвичайно термо- і паростойкость. Однак отримання цих специфічних цеолітів для каталізаторів крекінгу не завжди виправдовується з точки зору економіки.
Цеоліт мають ряд специфічних властивостей, використання яких дає можливість постійно вдосконалювати їх. До них відносяться іонообмінні властивості, термічна стабільність, кислотність і регулярний розмір пір, який зумовлює молекулярносітовое дію цеолітів.
Іонообмінні властивості. Внаслідок того, що алюмо-, кремнійкісло-родний каркас цеолітів має надлишковий негативний заряд, його компен-сіруют катіони. Вони слабо локалізовані і можуть обмінюватися на інші катіони різної природи і валентності, що дозволяє вводити в цеоліти каталитически активні елементи, а також змінювати розміри вхідних вікон в адсорбційні порожнини. Варіюючи природою катіонів і ступенем обміну, можна синтезувати набір каталізаторів і адсорбентів з найрізноманітнішими властивостями. У реакціях обміну можуть брати участь не тільки прості, але і складні катіони. Єдине обмеження, що відноситься до природи катіона, що вводиться іонним обміном, пов'язане зі збереженням стабільності цеоліту.
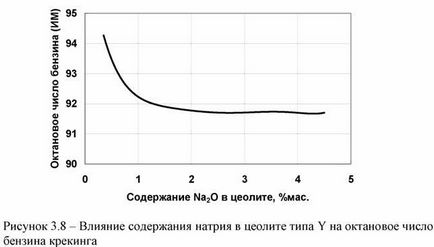
стабільність. При повільному нагріванні цеолітів в вакуумі або струмі інертного газу в інтервалі температур 100-250 ° С відбувається поступова десорбція молекул води, що призводить до втрати маси цеоліту. Подальше підвищення температури призводить до переміщення катіонів з адсорбційної порожнини всередину малих порожнин (всередину содалітовой осередки). Нагрівання цеолітів до 700-1000 ° С викликає розрив хімічних зв'язків, ущільнення структури і руйнування їх кристалічної решітки.
Структурна стабільність цеолітів типу Y підвищується після обміну іонів натрію на многовалентние іони (кальцій, магній, лантан і т.п.). Термічна стабільність водневих форм цеолітів, отриманих при обміні катіонів на протон або при розкладанні катіона амонію, на кілька сотень градусів нижче, ніж у вихідних цеолітів.
Кислотні центри. У цеолітах є два типи кислотних центрів, на яких протікають, зокрема, реакції крекінгу. До них відносяться бренстедовскіе (протонні) і льюїсовськие (апротонні) кислотні центри. Перші являють собою протони, пов'язані з каркасними атомами кисню. В якості других можуть виступати катіони або трехкоордінірованние атоми алюмінію, що знаходяться в місцях з дефіцитом кисню або в місцях розташування катіонів.
Високотемпературна дегідратація (понад 600оС) цеолітів типу. У призводить до видалення гідроксильних груп і появи льюїсовських кислотних центрів. Якщо температура прожарювання не перевищує 600оС, то в присутності молекул води кислотні центри Льюїса можуть перетворюватися в центри Бренстеда.
Молекулярносітовой ефект. Оскільки вхідні вікна пір і порожнин цеолітів за розмірами порівнянні з молекулами вуглеводневої сировини, цеоліти дозволяють виділяти певні типи молекул з їх сумішей різних форм, розмірів і складу. З точки зору каталізу цеолитсодержащие каталізатори є дуже селективними, якщо активні центри розташовані всередині їх порожнин і пор.
Молекулярносітовой ефект - здатність цеолітів пропускати в свої пори і адсорбувати молекули тільки певних розмірів і будови. Він в адсорбції найбільш часто використовується в процесах виділення налканов (процеси отримання рідких парафінів, ізомеризації і депапафінізаціі бензинових фракцій, виділення пара-ксилолу і т.д.). Молекулярносітовой ефект в каталізі знайшов значного поширення при освоєнні виробництва СВК цеолітів (ZSM-5), які є складовою частиною деяких каталізаторів крекінгу.
Модифікування каталізатора крекінгу - це процес введення в його склад додаткових речовин, що дозволяють поліпшити окремі властивості. Шляхом модифікування каталізаторів домагаються зниження вмісту оксидів сірки в газах регенерації, покращують умови випалу коксових відкладень, пасивують важкі метали, що відкладаються в процесі експлуатації каталізатора, і підвищують октанове число бензину.