Вибір раціональних режимів фрезерування
Вибрати раціональний режим фрезерування на даному верстаті означає, що для даних умов обробки (матеріал і марка заготовки, її профіль і розміри, припуск на обробку) треба вибрати оптимальний тип і розмір фрези, марку матеріалу і геометричні параметри ріжучої частини фрези, мастильно-охлаждаю- щую рідина і призначити оптимальні значення наступних параметрів режиму різання: В, t, sz. v, п, Ne, Тм.
З формули (32) випливає, що на об'ємну продуктивність фрезерування параметри В, t, sz і v надають однаковий вплив, так як кожен з них входить в формулу в першого ступеня. Це означає, що при збільшенні будь-якого з них, наприклад, в два рази (при інших незмінних параметрах) об'ємна продуктивність збільшиться також у два рази. Однак на стійкість інструменту зазначені параметри надають далеко не однаковий вплив (див. § 58). Тому з урахуванням стійкості інструменту вигідніше насамперед вибирати максимально допустимі значення тих параметрів, які в меншій мірі впливають на стійкість інструменту, т. Е. В такій послідовності: глибина різання, подача на зуб і швидкість різання. Тому і вибір цих параметрів режимів різання при фрезеруванні на даному верстаті слід починати в тій же послідовності, а саме:
1. Призначається глибина різання в залежності від припуску на обробку, вимог до шорсткості поверхні і потужності верстата. Припуск на обробку бажано зняти за один прохід з урахуванням потужності верстата. Зазвичай глибина різання при чорновому фрезеруванні не перевищує 4-5 мм. При чорновому фрезеруванні торцевими твердосплавними фрезами (головками) на потужних фрезерних верстатах вона може досягати 20-25 мм і більше. При чистовому фрезеруванні глибина різання не перевищує 1-2 мм.
2. Призначається максимально допустима за умовами обробки подача. При встановленні максимально допустимих подач слід застосовувати подачі на зуб, близькі до «ламає».
Остання формула виражає залежність подачі на зуб від глибини фрезерування і діаметра фрези. Величина максимальної товщини зрізу, т. Е. Значення постійного коефіцієнта I з в формулі (21), залежить від фізико-механічних властивостей оброблюваного матеріалу \ (для даного типу і конструкції фрези). Значення максимально допустимих подач ограни- j чиваются різними факторами:
а) при чорновій обробці - жорсткістю і вібростійкою інструменту (при достатній i точної жорсткості і вібростійкості верстата), 'жорсткістю оброблюваної заготовки і міцністю ріжучої частини інструменту, наприклад зуба фрези, недостатнім обсягом стружкових канавок, наприклад, для дискових фрез та ін. Так , подача на зуб при чорновому фрезеруванні стали циліндричними фрезами зі вставними ножами і великим зубом вибирається в межах 0,1-0,4 мм / зуб, а при обробці чавуну до 0,5 мм / зуб;
б) при чистової обробки - шорсткістю поверхні, точністю розміру, станом поверхневого шару і ін. При чистовому фрезеруванні стали і чавуну призначається порівняно мала подача на зуб фрези (0,05-0,12 мм / зуб).
3. Визначається швидкість різання; так як вона надає найбільший вплив на стійкість інструменту, то її вибирають виходячи з прийнятої для даного інструменту норми стійкості. Швидкість різання визначається за формулою (42) або за таблицями нормативів режимів різання в залежності від глибини і ширини фрезерування, подачі на зуб, діаметра фрези, числа зубів, умов охолодження та ін.
4. Визначається діюча потужність різання Ne при обраному режимі за таблицями нормативів або за формулою (39а) і зіставляється з потужністю верстата.
5. За встановленої швидкості різання (і, або i ^) визначається найближча ступінь частоти обертання шпинделя верстата з числа наявних на даному верстаті за формулою (2) або за графіком (рис. 174). З точки, відповідної прийнятої швидкості різання (наприклад, 42 м / хв), проводять горизонтальну лінію, а з точки з відміткою обраного діаметра фрези (наприклад, 110 мм) - вертикальну. За точці перетину вказаних ліній визначають найближчу щабель чисел оборотів шпинделя. Так, в прикладі, показаному на рис. 172, при фрезеруванні фрезою діаметром D = 110 мм зі швидкістю різання 42 м / хв частота обертання шпинделя буде дорівнює 125 об / хв.
Ріс.174 Номограмма частоти обертання фрези
6. Визначається хвилинна подача за формулою (4) або за графіком (рис. 175). Так, при фрезеруванні фрезою D = 110 мм, z = 10 при sz = = 0,2 мм / зуб і п = 125 об / хв хвилинна подача за графіком визначається наступним чином. З точки, відповідної подачі на зуб Sг = 0,2 мм / зуб, проводимо вертикальну лінію до перетину з похилою лінією, що відповідає числу зубів фрези г = 10. З отриманої точки проводимо горизонтальну лінію до перетину з похилою лінією, відповідної прийнятої частоті обертання шпинделя л = 125 об / хв. Далі з отриманої точки проводимо вертикальну лінію. Точка перетину цієї лінії з нижньої шкалою хвилинних подач, наявних на даному верстаті, визначає найближчу щабель хвилинних подач.
7. Визначається машинний час.
Машинне час. Час, протягом якого відбувається процес зняття стружки без безпосередньої участі робітника, називається машинним часом (наприклад, на фрезерування площини заготовки з моменту включення механічної поздовжньої подачі до моменту її виключення).
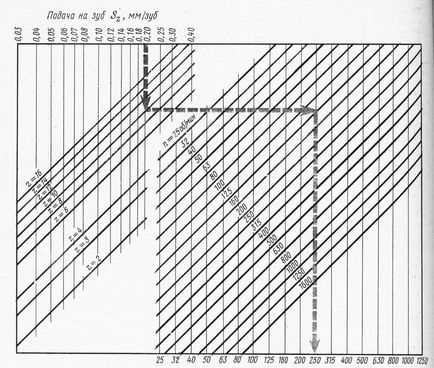
Мал. 1. Номограма хвилинної подачі
Підвищення продуктивності при обробці на металорізальних верстатах обмежується двома основними факторами: виробничими можливостями верстата і ріжучими властивостями інструменту. Якщо виробничі можливості верстата малі і не дозволяють повністю використовувати ріжучі властивості інструменту, то продуктивність такого верстата становитиме лише деяку частину від можливої продуктивності при максимальному використанні інструменту. У тому випадку, коли виробничі можливості верстата значно перевищують ріжучі властивості інструменту, на верстаті може бути досягнута максимально можлива при даному інструменті продуктивність, але при цьому не будуть повністю використані можливості верстата, т. Е. Потужність верстата, максимально допустимі сили різання і т. д. Оптимальними з точки зору продуктивності і економічності використання верстата і інструменту будуть такі випадки, коли виробничі потужності верстата і ріжучі властивості інструменту будуть совпадат ь або близькі один до одного.
Ця умова покладено в основу так званих виробничих характеристик верстатів, які були запропоновані і розроблені проф. А. І. Каширіним. Виробнича характеристика верстата являє собою графік залежностей можливостей верстата і інструменту. Виробничі характеристики дозволяють полегшити і спростити визначення оптимальних режимів різання при обробці на даному верстаті.
Ріжучі властивості того чи іншого інструменту характеризуються режимами різання, які допускаються в процесі обробки. Швидкість різання при заданих умовах обробки можна визначити за формулою (42, а). Практично ж її знаходять по таблиці режимів різання, які наведені в довідниках нормувальника або технолога. Однак слід зазначити, що нормативи по режимам різання як для фрезерування, так і для інших видів обробки розробляються, виходячи з ріжучих властивостей інструменту для різних випадків обробки (тип і розмір інструмента, вид і марка матеріалу ріжучої частини, опрацьований матеріал і ін.), і не пов'язані з верстатами, на яких буде проводитися обробка. Так як виробничі можливості різних верстатів різні, то практично здійсненний оптимальний режим обробки на різних верстатах буде різним для одних і тих же умов обробки. Виробничі можливості верстатів залежать перш за все від ефективної потужності верстата, частоти обертання, подач і ін.
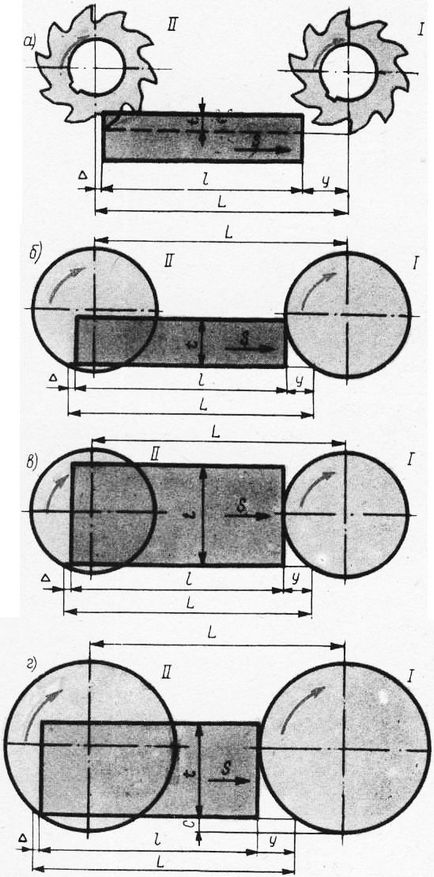
Мал. 2. Врізання і перебігаючи
Принцип побудови виробничих характеристик фрезерних верстатів (номограм) для роботи торцовими фрезами заснований на спільному графічному вирішенні двох рівнянь, які характеризують залежність швидкості різання vT за формулою (42) при -Bz '= const, з одного боку, і швидкості різання ід "допустимої потужністю верстата, - з іншого. Швидкість різання vN може бути визначена за формулою
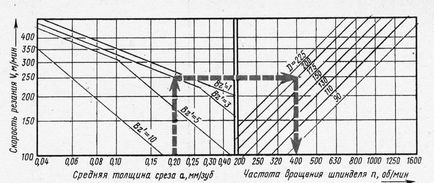
Мал. 3. Виробнича характеристика консольно-фрезерного верстата 6Р13