Перевірка зубчастих коліс. При виборі методів перевірки зубчастих коліс виходять з дотримання основних технічних умов, що забезпечують нормальну роботу зубчастих зачеплень.
1. Постійність миттєвого передавального відношення.
2. Повного прилягання зубів, по довжині.
3. Наявності зазорів для компенсації деформацій і похибки-стей передачі, а також для розміщення мастила між зубами.
Залежно від розмірів колеса імогут піддаватися перевірці по різним елементам передачі. У великих коліс (діаметром до 5000 мм) проводять перевірку за такими елементами: ос-новному кроці, різниці окружних кроків. профілем, зміщення ис-перехідного контуру, напрямку зуба.
Всі прилади, що застосовуються для перевірки зубчастих коліс, де-лятся на стаціонарні та ручні або накладні. За своїм устрій * ству стаціонарні прилади вимагають установки на них вимірюваних коліс, тому область застосування цих приладів обмежується колесами невеликих розмірів. Для контролю великих коліс при-міняють прилади накладні або ручні. Однак накладні при-бори не пристосовані для вимірювання всіх перерахованих елементів, тому при перевірці доводиться вдаватися до непрямого контролю, т. Е. До контролю не самих елементів, а тих факторів, від яких залежить їх точність.
Відомо, наприклад, що точність профілю зуба залежить від точ-ності профілю і кроку (для черв'ячних фрез) зуборізного инстру-мента. Звичайно, інструмент є не єдиним фактором, що впливає на точність профілю зубів колеса. Сюди можна відне-сти також точність верстата і установки інструменту. Тому не-обходимо перевіряти комплексно всі фактори, які відображаються на точності того чи іншого елемента. Завдяки цьому, можна бу-дет забезпечити необхідну точність зубчастого колеса. Наведено-ве міркування справедливо і для інших перевірених елементів-тов.
Що ж стосується комплексної перевірки зубчастих коліс, виявив-ляющие сумарний вплив всіх похибок на роботу колеса в парі, то для великих коліс через відсутність приладів її вироб-дять на збірці. Контрольоване колесо монтують в вузлі і вводять в зачеплення з парної шестернею. При цьому виявляють загальний ре-зультат правільносіі обробки деталей, що впливають на отримання
Правильного зачеплення (розт-ки отворів під підшипники в корпусі, обробки підшипників, 'зубчастих коліс і т. П.). Перевір-ка ведеться по поверхні при-леганія зубів, для чого на зуби одного колеса наносять шар крас-ки, що покриває при зачеплю-ванні місця зіткнення зубів іншого колеса. Для кожного класу точності зубчастих коліс встановлена величина бічної поверхні зуба у відсотках, яка повинна бути покрита фарбою (повинна мати контакт). Перейдемо до методів перевірки окремих елементів зубчастого колеса.
Вимірювання отклоне-ня основного кроку. Ос-новним кроком називається рас-стояння між двома паралель-ними дотичними до двох суміжних однойменною профілів.
Точністю основного кроку визначається плавність передачі.- Вимірювання основного кроку ведеться крокоміром для основного кроку
Верхня межа вимірювання приладу (в модулях) 20.
Установку приладу на номінальний розмір основного. кроку. виробляють за допомогою настановної рамки 1, в яку застави-вают блок кінцевих мір і спеціальні боковики; розмір блоку підраховують за формулою
T0 - тк cos <х0.
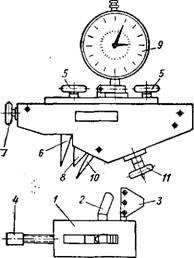
Фіг. 35. Крокомір для вимірювання основного кроку.
Блок поміщають між боковику 2 і 3 і затискають гвинтом 4. Попередньо прилад встановлюють при звільнених вин тах 5 шляхом переміщення рухомий губки з наконечником 6 гвинтом 7. Потім прилад налаштовують на рамці таким чином, щоб нерухомий вимірювальний наконечник 8 помістився між ро-ликами , і боковиком 3, жорстко з'єднаним з роликами, а під-1 Віжн вимірювальний наконечник 6 контактував з боковиком 2. за допомогою гвинта 7 індикатору 9 дають натяг на один
Оборот стрілки (натяг необхідний для отримання показань як позитивних, так і негативних). Після закріплення вин-тов 5 індикатор поворотом обідка остаточно встановлювали-ють на нуль. Налаштований прилад переносять на зубчасте колесо і встановлюють так, щоб вимірювальні наконечники 6 і 8 каса-лись однойменних профілів двох сусідніх зубів колеса, а упор 10, що встановлюється гвинтом 11 стосується своїм кінцем проти-воположного профілю третього зуба, забезпечував би щільне при-леганіе нерухомою губки до профілю зуба. Відхилення стрілки індикатора покаже відхилення основного кроку від номінального. Паралельність і прямолінійність вимірювальних поверхонь губок обумовлює їх торкання з зубами в точках, що лежать на загальній нормалі до профілів або на дотичній до основний окруж-ності колеса.
Вимірювання виробляють для трьох рівно віддалених один від одного по колу зубів колеса по лівим і правим сторонам (про-филя.
Вимірювання відхилень окружного кроку. Відхилення ня величини окружного кроку також позначаються на плавності зачеплення. Для визначення відхилень окружного кроку примі-няют крокомір (фіг. 36), що складається з корпусу 1, індикатора 2, опорних ніжок 3, рухомий вимірювальної губки 4 і поворотною вимірювальної губки 5. Відстань між губками встановлюють за допомогою рухомої губки за модульною шкалою, нанесеною на корпусі. Після цього рухливу губку закріплюють гвинтом 6.
Прилад встановлюють так, щоб губки стосувалися зуба прибл-зітельно по ділильної окружності. Опорні ніжки стикаючись-ються з колесом по окружності виступів; в такому положенні ніж-ки закріплюють гвинтами 7. Індикатор встановлюють на нуль. За-тим прилад переносять на наступну суміжну пару зубів і сни-мают показання індикатора, яке вказує на відхилення через міряють окружного кроку від попереднього, прийнятого за одиницю. Відхилення може бути як у бік плюса, так і в бік мі-нуса. Провівши вимір по всьому колесу, можна визначити похибки між окремими окружними кроками.
Крокомір застосовують для вимірювання коліс з модулем 3-15.
Перевірка профілю зуба. Як вже було сказано, про-верка профілів зубів у великих коліс проводиться непрямим шляхом: перевіркою інструменту, правильної його установкою, перевіркою точності верстата.
Для коліс 4-класу точності при перевірці профілю можна при-міняти шаблон, виготовлений за профілем або западині зуба. Од-нако в умовах одиничного виробництва це себе не опраздивает - так як виготовлення шаблону з теоретичним профілем викликаючи-ет певні труднощі.
Вимірювання величини зміщення вихідного кон-туру. Зміщенням вихідного контуру визначають зазор між зубами пари коліс зачеплення, необхідний для нормальних ус-ловий роботи. Для вимірювання зміщення вихідного контуру примі-няют тангенціальний Зубоміри і штангензубоміри.
Тангенціальний Зубоміри (фіг. 37) складається з корпусу 1 і двох вимірювальних губок 2, переміщаються від гвинта 3 з правого і лівого гвинтовою нарізкою. Вимірювальні губки розташовані сім-симетрично щодо осі індикатора 4 і мають вимірювальні

Поверхні, скошені під кутом зачеплення зубчастих коліс. Прилад на потрібний розмір встановлюють за допомогою спеці-них роликів. Комплект роликів для різних модулів докладаючи-ється до приладу. Ролик 5 ставлять на призмі 6 і губки Зубоміри сво-дять так, щоб середина вимірювальних поверхонь стикаючись-лась з роликом. Після цього губки затискають гвинтом 7, індикатор встановлюють на нуль і прилад переносять на виріб. Стрілка індикатора показує величину відхилення вихідного контуру від його номінального положення.
Тангенціальний Зубоміри придатний для вимірювання зубів з мо-дулем до 36 мм.
Штангензубоміри (фіг. 38) має дві взаємно-перпендикуляр-ні штанги зі шкалою 1 і нерухому губку 2, по штангах пере-розміщуються рамки 3 і 5 з ноніусом 4 і 7 з ціною поділки 0,02 мм. Шкала 1 служить для визначення відстані від виступу колеса, на якому заміряють товщину зуба. Це відстань визначається положенням лінійки 6. Розмір встановлюють за ноніусом 7, при-бор переносять на вимірюваний зуб і визначають його товщину з по-міццю ноніуса 4.
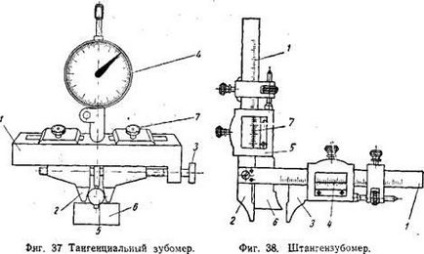
Штангензубоміри застосовується для коліс 4-го класу точності з
Модулем до 35 мм.
Перевірка правильності напрямку зуба. Пра-вильность напрямки зуба перевіряють по фарбі при комплексному контролі колеса, про що вже сказано раніше. При обробці косозубих коліс до початку нарізування зуба, як правило, перевіряють пра-ність настройки верстата. Для цього в супорті верстата встановлюють чертилку, верстат включають і на заготівлі наносять ризику, відпо-ствующую напрямку майбутнього зуба. Правильність фактичних-кого напряму зуба порівнюють з теоретичним напрямком зуба, викресленим на кальці, яку накладають на заготівлю. Перевірка ведеться і налаштуванням верстата, коли зуби обох коліс однієї пари нарізають на одному верстаті (при одній настройці його).
Вимірювання великих різьб. Заводи інструментальної примушує -. лінощів виготовляють калібри діаметром до 210 мм. У практиці виробництва прокатного обладнання зустрічаються різьблення значи-тельно великих розмірів. Перевірка таких резьб проводиться дво-ма способами. У деяких випадках заводи виготовляють калібри у вигляді контрольних болтів і контрольних гайок. за якими виро-лиє і перевіряється.
Різьба вважається виготовленої правильно, якщо контрольний болт або гайка нагвинчуються без особливих зусиль і не мають при цьому гри в осьовому або радіальному напрямку. /
Контрольний болт при виготовленні перевіряється по середньому діаметру, кроку і профілю, а гайка - на свинчивание з ним. Для великих різьблень (діаметром до 600 мм) обмежуються перевіркою витків різьби стержня (гвинта) в процесі обробки за шаблоном, а по гвинту нарізають різьбу в гайці. Правильність різьблення в гайці перевіряють загвинчування її на гвинт.
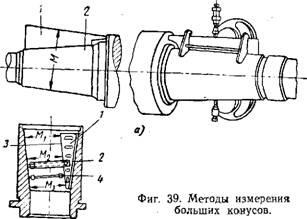
Перевірка конічних поверхонь. Вимірювання і контроль біль-ших конічних поверхонь ведеться звичайним методом - скобою, губки якої утворюють кут, рівний куту конуса.-
Недоліком скоби є низька жорсткість її і те, що важко забезпечити прилягання обох губок до вимірюваної поверх-ності. Ці недоліки усунуті в методі паралельних стороя (фіг. 39).
Зовнішній конус (фіг. 39, а) перевіряють за допомогою шаблону. Шаблон 1 прилягає до виробу 2, при цьому друга сторона Шаблій-на розташовується паралельно портівоположн-ой утворює ко-нуса. Провівши три виміри по довжині конуса за допомогою мікромет-рической або індикаторної скоби, можна визначити точність його обробки.
Перевірка внутрішніх конусів методом паралельних сторін (фіг. 39, б) проводиться шаблоном 1, який встановлюється радіально, радіусна вимірювальна поверхня його прилягає до котра утворює 2 конуса, а плоска поверхня 3 паралельна про-протилежний утворює конуса. Замір проводиться мікронут-Ромеро 4 в трьох місцях (розміри Мі М2, М3). Прямолінійність утворює конуса перевіряється лекальної лінійкою, на просвіт і під щуп.