Установчі елементи пристосувань. Установку заготовок на плоску поверхню виробляють на основні опори (постійні, регульовані і самоустановлювальні), що визначають положення заготовки, і на допоміжні опори (регульовані і самоустановлювальні), що застосовуються для підвищення жорсткості і вібростійкості технологічної системи.
Основні постійні опори зі сферичною і насеченной головками використовують при установці невеликих заготовок з необробленими базами, а з плоскою головкою - для установки зазначених заготовок з обробленою базою. Для забезпечення високої точності установки розмір Н висоти головки виконують з досить жорстким допуском.
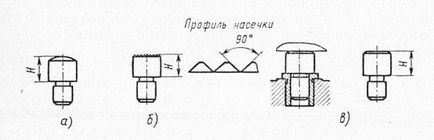
Мал. 1. Основні постійні опори зі сферичною (а), насеченной (б) і плоскої (в) головкою
З метою кращого видалення стружки опори з насеченной головкою встановлюють на вертикальні, а опори зі сферичною голівкою - на горизонтальні стінки пристосувань.
Замість опор з плоскими головками іноді застосовують плоскі пластини без пазів і з пазами. Пази полегшують видалення стружки при зсуві заготовки. Опорні пластини використовують при установці заготовок з обробленою базою.
Опори пристосувань повинні мати високу зносостійкість. Їх виготовляють зі сталі марки У7А (опори діаметром D до 12 мм), стчалі марки 20Х (опори більшого діаметру і пластини). Після термічної обробки твердість опор 56-61 HRQ. Опори з насеченной головкою виготовляють зі сталі 45 (твердість після термічної обробки 41,5-46,5 HRC3).
Регульовані опори застосовують при установці заготовок з необробленими базами або в якості допоміжних опор.
Самоустановлювальні опори широко використовують як основні і допоміжні при протягуванні отворів і виконанні інших операцій при обробці заготовок складної форми.
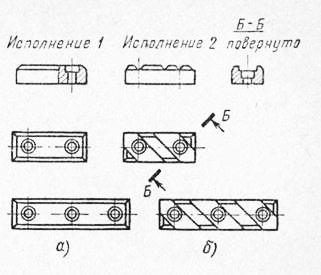
Мал. 1. Опорні пластини без пазів (а) і з пазами (б)
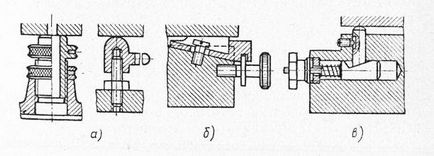
Мал. 2. Регульовані опори: а -вінтовие, б-клинові, в - клинові з плунжером
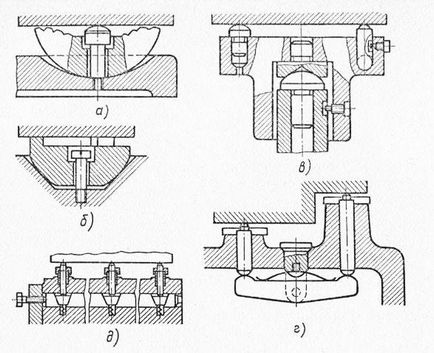
Мал. 3. Самоустановлювальні опори: а, б, в - кульові, г - для важеля плунжерні, д - плунжерні
Установку заготовок на отвір проводять з використанням оправок і циліндричних настановних пальців. При установці заготовки з зазором її базове отвір повинен бути оброблено по 7-му квалітету точності. При цьому зовнішня поверхня може бути зміщена щодо внутрішньої в межах зазору.
Велику точність установки (з відхиленням від співвісності 0,005-0,01 мм) забезпечують конічні оправлення і оправлення з запрессовивании заготовки.
Розтискні кулачкові оправлення застосовують при обробці заготовок з отвором, виконаним за 8-13-му квалітетами точності.
Найбільшу точність установки (0,002-0,005 мм) забезпечують оправлення з пружним елементом: цангою (отвір виконують по 8-13-му квалітетами точності); тонкостінної втулкою і Гідропласт (отвір виконують по 7-8-му квалі-тетам точності); гофрованої втулкою (отвір виконують по 7-8-му квалітетами точності).
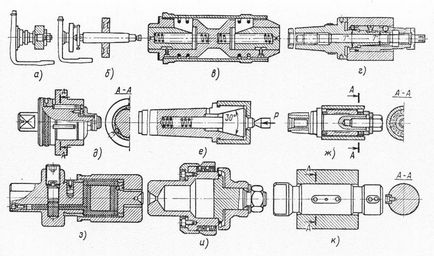
Мал. 4. Відправки: а - для установки заготовок з зазором, б-конічні, в - кулачкові, г - кулькові, д - роликові, е, ж - цангові, з - з тонкостінної втулкою і Гідропласт, і - з гофрованими втулками, до - з запрессованіем заготовки
При установці корпусних деталей і плит середніх розмірів за двома отворами забезпечується досить висока точність орієнтації. Отвори в заготовках повинні бути оброблені по 7-му квалітету точності. Один з настановних пальців виконують циліндричним, інший - зрізаним. В цьому випадку і при максимально можливій відстані між пальцями забезпечується найменша похибка кутового розташування заготовки.
Вали, циліндри, а також заготовки, розташовані на оправці, встановлюють в центрах.
Установку заготовок по зовнішній циліндричній поверхні здійснюють на призми, в патрони, у втулки. Призми для установки коротких заготовок стандартизовані. У пристроях використовують призми з кутом 2а = 60; 90 і 120 ° (найбільше застосування отримали призми з кутом 2а = 90 °).
Закріплення заготовок в патронах - універсальний, широко застосовуваний спосіб. Похибка установки при цьому визначається точністю виготовлення патрона, точністю виготовлення технологічних баз заготовки. При закріпленні нежорстких заготовок з силою, спрямованої по радіусу, можливий вигин заготівлі, для зменшення якого збільшують число кулачків в патроні.
Способи та елементи технологічного оснащення для установки їх на верстаті. Технологічне оснащення встановлюють на робочому вузлі верстата, що має спеціальне посадкове місце (комплект баз).
На верстатах токарної групи патрони і оправлення встановлюють безпосередньо на шпинделі з центруванням по посадковим елементам, розташованим на зовнішньої або внутрішньої (конусний отвір) поверхні шпинделя; з використанням перехідної планшайби з центруванням по планшайбе або по пальцю, встановленому в конусному отворі шпинделя.
На токарних верстатах пристосування також встановлюють на центрах (типу оправок), в конічний отвір задньої бабки, в резцедержатель.
На фрезерних, горизонтально-розточувальних, свердлильних та інших верстатах пристосування встановлюють на площину столу, що має Т-образні пази. Для орієнтації щодо поздовжньої подачі на корпусі пристосування передбачають дві призматичні прівертние шпонки, які входять в один з Т-образних пазів столу (як правило, в середній як більш точний). Внаслідок зносу і наступних ремонтів ширина пазів столу збільшується, тому в цілях запобігання можливих Проворотов пристосування при установці притискають до однієї сторони паза.
Для кріплення на столі в корпусі пристосування є спеціальні вушка під болти. При малих силах різання два вушка розміщують в тому ж Т-образному пазу, що і шпонки, при великих - чотири вушка розміщують симетрично в сусідніх пазах.
У ряді випадків з метою раціонального розміщення пристосувань на столі і збереження точності баз столу на останньому жорстко закріплюють накладні плити з сіткою пазів і отворів, які використовують для установки пристосувань.
Пристосування на столі верстата можуть встановлюватися без вивірки (при цьому виникає похибка установки пристосування) або з вивірянням положення по опорах. У технічних умовах на складальному кресленні пристосування і в технічній карті виготовлення деталі повинна бути вказана допустима похибка вивірки. Вивірку положення пристосувань широко застосовують на зубообрабативающих, шліфувальних, токарних, фрезерних та інших верстатах.
Всі ріжучі інструменти мають кріпильну частину, призначену для установки і кріплення різального інструменту на технологічному обладнанні або в пристосуванні.
У різців комплект баз складається з декількох площин або з циліндричною і плоскою (торцевої) поверхонь. У свердел, зенкерів, розгорток, фрез кріпильну частину виконують у вигляді циліндричного або конічного хвостовика або циліндричного або конічного отвору. Для передачі моменту у насадними інструменту передбачені шпонкові канавки в отворі або на торці.
Весь інструмент, який закріплюється на шпинделі верстатів з ЧПУ на фрезерних верстатах, забезпечений елементами для створення осьової сили кріплення.
При переточуванні ріжучого інструменту використовують, як правило, ті ж бази, що і при установці на верстаті або в пристосуванні. У той же час розгортки, зенкери, протягання при переточуванні встановлюють на центру, а кутову орієнтацію виконують по зубу інструменту.
При установці шліфувальних кругів на шпинделі верстата використовують отвір і плоскі торці; шліфувальні головки кріплять за циліндричний хвостовик.
У деяких інструментів в якості бази використовують їх робочу частину (наприклад, вигладжують частина у оправок для калібрування отворів, різьбова частина у гучних мітчиків із зігнутим хвостовиком).
Затискні пристрої. Пристрої призначені для досилання заготовок до настановних елементів пристосування, забезпечення надійного контакту заготовки з установочними елементами і попередження її зміщення і вібрацій в процесі обробки.
Необхідність закріплення заготовки відпадає, якщо сили, що виникають при обробці, не можуть змістити заготовку (наприклад, при цекованіі).
Затискач зазвичай складається з силового механізму і приводу. У той же час бувають пристрої, що складаються тільки з силового механізму (їх називають ручними затискними механізмами), і пристрої, що складаються тільки з приводу (їх називають пристроями прямої дії).
Силові механізми (гвинтові, клинові, ексцентрикові, важільні, шарнірно-важільні і т. Д.) Відрізняються простотою виготовлення, компактністю, здатністю змінювати величину і напрямок переданої сили. Гвинтові і клинові механізми мають здатність до самозагальмовування, що дуже важливо з точки зору техніки безпеки (особливо в комбінованих затискних пристроях з приводом при аварійному відключенні енергії).
Гвинтові затискні механізми застосовують для прямого закріплення заготовки натискним гвинтом.
Клинові затискні механізми, широко застосовуються в пристроях, мають кут клина 6-15 ° (що забезпечує значну силу і високу надійність затиску) і кут 45 °, якщо клин використовують для вимірювання напрямку сили.
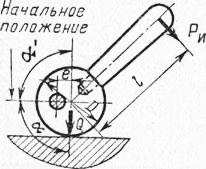
Мал. 5. Ексцентриковий механізм
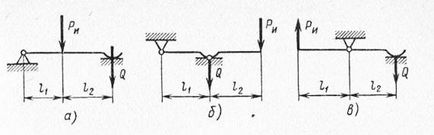
Мал. 6. Схеми важільних механізмів
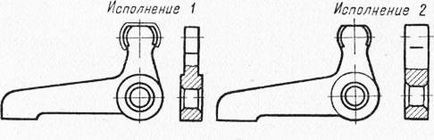
Мал. 7. Конструкція кутового важеля
Як приклад на рис. 7 показана конструкція кутового важеля. Застосування приводу (пневматичного, гідравлічного, пневмогидравлического, електричного, магнітного, електромагнітного, вакуумного) дозволяє підвищити швидкодію затискних пристроїв і збільшити силу закріплення. У ряді випадків кілька затискних пристроїв працюють від одного приводу.
Найбільш поширені пневматичні приводи. Поршневі пневмодвигатели (пневмоцилі-Ліндрен) забезпечують великий хід штока; термін їх служби зазвичай 10-15 тис. циклів. Діафраг-менниє пневмодвигатели виконують з діфрагми з прогумованої тканини; термін їх служби 0,5-1 млн. циклів; недоліки - малий хід штока і залежність сили від положення штока через змінного опору діафрагми. Сильфонний пневмопривід не має витоків, простий у виготовленні.
Пневмопривод простий по конструкції і надійний в експлуатації, проте він має великий розмір (так як стиснене повітря подається під низьким тиском 0,4 - 0,63 МПа) і створює шум при випуску відпрацьованого повітря.
Гідропривід має наступні переваги в порівнянні з пневматичним: використання робочої рідини під високим тиском (до 15 МПа) дозволяє зменшити розміри гідроциліндрів; один Гидропровод може обслуговувати групу верстатів; робоча рідина (масло) не викликає корозії елементів системи і одночасно служить мастилом; гідропривід працює плавно і безшумно. До недоліків гідроприводу відносяться висока початкова вартість, підвищені вимоги до експлуатації з метою попередження витоків масла.
Пневмогідравлічний привід до певної міри має переваги пневматичного і гідравлічного приводів. Стисле повітря подається в пневмоцилиндр, шток якого є поршнем гідроциліндра. Масло з циліндра по трубопроводу надходить в гідроциліндр пристосування. Зворотний хід циліндрів відбувається під дією пружин.
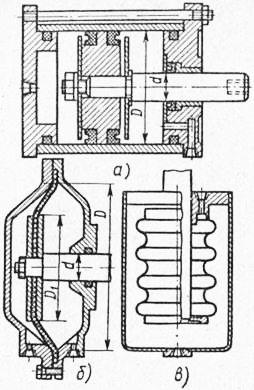
Мал. 8. Пневмодвигатели: а - поршневі, б - діафрагмові, в - сильфонні
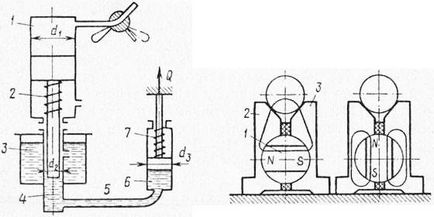
Мал. 9. Пневмогідравліче
Мал. 10. Магнітна призма ський привід
Закріплення заготовок за допомогою електроприводу перспективно і знаходить широке застосування в затискних пристроях автоматичних ліній. Стаціонарний електропривод (гайковерт) використовують для обертання гайки затискного механізму пристосування.
Широке застосування при закріпленні заготовок на плоскошліфувальних верстатах отримали електромагнітні та магнітні плити і пристосування. На рис. 10 показана схема магнітної призми для закріплення циліндричних заготовок. При горизонтальному положенні магніту магнітний силовий потік проходить через щоки призми, розділені немагнітним пластиною, і заготовку. Остання при цьому положенні магніту притиснута до призмі. При повороті магніту до вертикального положення магнітний потік замикається через щоки і заготівля звільняється.
Елементи пристосувань для направлення і установки ріжучого інструменту. Налагодження і підналагодження технологічної системи на розмір за допомогою пробних проходів і промірів займає багато часу і можлива не у всіх випадках обробки. За допомогою таких пристосувань, як шаблони і встановити, цей процес може бути прискорений. Особливо широко застосовують встановити для налагодження фрезерних пристосувань.
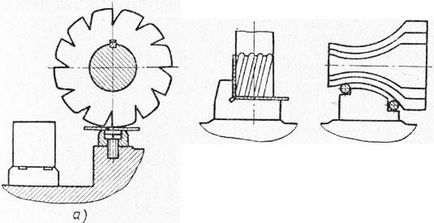
Мал. 11. Схема наладки технологічної системи для фрезерування заготовок за допомогою щупів і встановивши: а, г-висотного, б - кутового, в - фасонного
Обробку на гідрокопіровальний верстатах виробляють з використанням копірів. Їх застосовують також при обробці на фрезерних, токарних, стругальних, шліфувальних і інших верстатах. Копіри і ролики виготовляють зі сталі 20Х; їх цементують і гартують до твердості 56-61 HRC.
Кондукторні втулки призначені для орієнтації та напрямки осьових інструментів (свердел, зенкерів, розгорток і т. Д.). Застосовують постійні, змінні, швидкозмінні і спеціальні нерухомі втулки. Постійні втулки (без бурту - тип I; з бурти - тип II) використовують у разі, коли час користування пристроєм не перевищує часу, протягом, якого може настати знос втулки. У серійному і масовому виробництві застосовують змінні втулки. Швидкозамінні втулки застосовують при послідовній обробці (свердлом, зенкером, розгорткою) одного отвору з однієї установки заготовки. Спеціальні втулки дозволяють обробляти отвори в похилій площині, поглибленні або близько розташованих отвори.
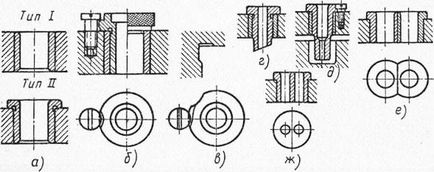
Мал. 12. Кондукторні втулки для обробки отворів осьовим інструментом
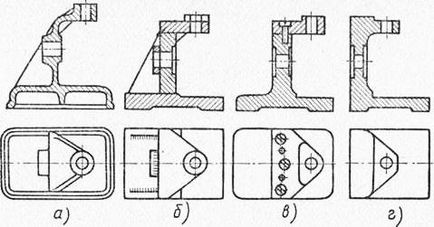
Мал. 13. Варіанти конструкції корпусу кондуктора при різних способах його виготовлення: а - литтям, б - зварюванням, в - складанням, г - з стандартної литої заготовки
Корпуси пристосувань. Всі елементи пристосування розміщують і закріплюють на його корпусі. Оскільки корпус пристосування сприймає всі зусилля, що діють на заготовку в процесі її закріплення і обробки, він повинен мати достатню міцність, твердість і вібростійкою. Ці якості забезпечуються вибором раціональної конструкції корпусу і в першу чергу введенням ребер жорсткості.
Різні варіанти конструкції корпусу кондуктора показані на рис. 13.
Литі корпуси і частини збірних корпусів зазвичай відрізняють з чавуну марок СЧ 12 і СЧ 15. Рідше застосовують сталеве лиття. Для виготовлення зварних корпусів використовують листову сталь.