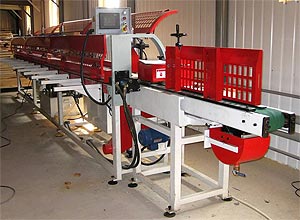
Складальні клеєні щити з масиву дуба, сосни, бука або ясена є на сьогоднішній день найбільш затребуваним вихідним матеріалом для виробництва меблів, виготовлення сходів і виконання декоративно-оздоблювальних робіт.
Найпоширеніша продукція з щита - це меблевий декор, сходи. спинки ліжок, фільончасті двері, стільниці. підлогові покриття та оздоблювальні інтер'єрні панелі. Останні часто використовуються при створенні інтер'єрів дорогих ресторанів, клубів і кабінетів.
Виготовляючи меблеві щити на замовлення. виробник зазвичай користується спеціальним обладнанням і лініями, орієнтованими на виконання різних технологічних операцій.
Якщо укласти весь техпроцес виробництва щита в одне речення, то вийде буквально наступне - з добре просушені пиломатеріалів виготовляються ламелі, які в свою чергу скріплюються один з одним по ширині і довжині, будучи згодом відформатовані за розміром.
Меблевий щит володіє не тільки бездоганними декоративними властивостями, але і здатний грати роль регулятора вологості в приміщенні. Він не токсичний, гігієнічний і довговічний. Якщо порівнювати меблевий щитової модуль з не менш популярною плитою ДСП, то він виявиться більш міцним, надійним і екологічно нешкідливим. Вологість стандартного вироби зазвичай становить 8%. Розміри щита варіюються і можуть досягати до 40 мм в товщину, 1,2 м в ширину і 4,5 м в довжину.
Технологічні етапи виготовлення кожного виробу включають безліч різноманітних операцій. Спочатку слід процес сушіння обрізної дошки. Даний етап дозволяє усунути напруги всередині пиломатеріалу і забезпечити досягнення певного значення вологості деревини. Для цих цілей застосовується сушильна камера конвективного типу, управління якою здійснюється автоматично. Після цього, заготовки калибруются, паралельно проходячи перевірку на наявність дефектів.
Далі за допомогою двостороннього рейсмуса (з встановленим на ньому блоком дискових пилок) заготівля розпускається на ламелі рівної ширини. Вищезазначений верстат забезпечує виконання одночасно чотирьох операцій в один прохід. Тобто формується база для подальшої обробки, заготівля простругівается з обох сторін, після чого проводиться розпуск исходника на ламелі.
Наступним етапом простує торцювання ламелей в розмір і вилучення дефектних ділянок. Лінія так званої оптимізації ламелей має до сотні програм розкрою. Наступного лінії проводиться торцеве зрощування ламелей в довжину, тобто на торцях заготовок вирізається зубчастий шип, який згодом покривається клейовим розчином і виконує функції додаткового кріплення. Після цього ламелі калібрують і набирають в щит, зрощуючи вже по ширині. Завершальним етапом слід обробка щита на форматно-розкроювальних обладнанні, його калібрування і шліфування.