Щодня кожен з нас торкається своїми руками до десятків різних металевих деталей. Але ми рідко замислюємося, яким чином зробили цю залізяку. Тим більше, що в більшості випадків це фабричні вироби серійного виробництва. А чи часто Ви тримали в руках металевий аксесуар, зроблений спеціально на Ваше замовлення?
Наше виробництво спеціалізується на виготовленні індивідуальних декоративних решіток. Можливо вибрати матеріал виготовлення, конструкцію, вид обробки, візерунок, спосіб кріплення і інші опції. І звичайно розмір.
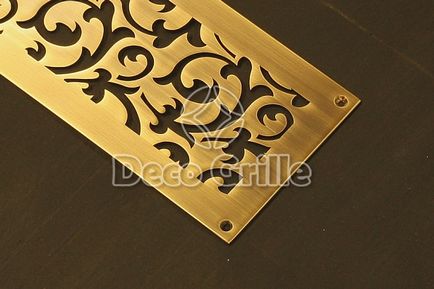
Всупереч поширеній стереотипу, що існує якийсь універсальний верстат, куди з одного боку закладаються металеві пластини, а з іншого - виїжджають готові декоративні решітки, все трохи складніше. Точніше сказати - цікавіше. Спробуємо без нудних подробиць розповісти про процес створення прорізного візерунка в металі.
У нашому арсеналі відразу чотири способи вирізання візерунка в металевому листі. Лазерне різання, координатна пробивання, фрезерна обробка і гідроабразивна різання. Всі ці способи реалізуються за допомогою комп'ютерного управління ріжучим механізмом - ЧПУ. Для того, щоб це спрацювало, обов'язковий електронний креслення вироби в цілому. Тобто просто картинки або якогось шаблону недостатньо. Дизайнер-кресляр виконує закінчений ескіз Вашої майбутньої решітки в двомірному просторі. Далі технолог визначає, яким чином буде вирізатися цей візерунок на цьому конкретному виробі. Для виготовлення виробу на кожному з цих комплексів оператор-програміст створює керуючу програму обробки. Там з урахуванням особливостей технології та існуючих інструментів він вказує, що конкретно повинен зробити верстат, щоб виконати поставлене контур.
Наприклад, для того, щоб лазерний верстат вирізав в металі невеликий трикутник або квадратик згідно креслення, в програмі задається розмір заготовки, її положення на столі верстата, матеріал і його товщина, режим різання (швидкість і ретельність). Також він вказує, де саме верстат повинен прошити метал. Адже лазерний промінь спочатку здійснює врізку, залишаючи некрасиву оплавлену дірку, а потім вже від неї, подібно до лобзику, ріже метал по заданому контуру. Так ось оператор задає, щоб лазерний промінь прошив метал всередині вирізуваного контуру, адже вирізаний трикутник піде в відхід. Крім іншого, такого, щоб на верстат поклали лист для вирізання лише однієї деталі, практично не буває - адже лазерний комплекс являє собою дуже дороге і складне обладнання, для роботи якого потрібна налагодити велика кількість допоміжних систем. Такі комплекси не можуть простоювати під час постійних переналадок. Кожна година простою виливається в збитки. Тому деталі комбінуються і укладаються на лист таким чином, щоб максимально ефективно провести обробку з мінімальним простоєм і відходом матеріалу. Для деяких наших замовників не секрет, що декоративні решітки ріжуться часом заодно з деталями для радіо-електронної апаратури або для авіаційної техніки. У підсумку з одного і того ж листа нержавійки або звичайної сталі виходять абсолютно різні деталі для різних механізмів з різних сфер нашого життя. Часом настільки специфічних, що ми навіть не знаємо про них, користуючись приладами, всередині яких працюють ці детальки.
Отже, розповімо детальніше про кожен вид обробки. Про лазерну різку Ви вже трохи знаєте. Працює це так. Над листом металу рухається керована серводвигунами лазерна «голова». Від джерела лазера (величезний ящик розміром з невелику кухню, стоїть поруч з верстатом) до фокусірущей оптики в цій «голові» промінь може проходити за спеціальними телескопічним каналах, відбиваючись від фокусирующих дзеркал, або по Світоволокно. В результаті лазерний промінь потрапляє на нашу заготовку. Розмір плями контакту променя і листи металу як правило не перевищує півміліметра. На цей маленький пяточёк подається енергія від півтора до п'яти кіловат, що призводить до розплавлення металу в цій точці. Для того, щоб процес був точним і керованим, а кромки різу - акуратними і гладкими, до зони різу під великим тиском подається допоміжний газ, який видуває розплавлений метал вниз, не даючи тут відбуватися ніяким іншим процесам, крім заданих програмою. Залежно від матеріалу і режиму різу це може бути повітря, азот, кисень, гелій і чорт знає що ще. Все, крім повітря, коштує чималих грошей і вимагає істотних накладних витрат на заправку і доставку балонів. А йде газ дуже швидко. Але не будемо про сумне.
В результаті лазерна різка дійсно є напрочуд універсальну технологію. Але божевільна дорожнеча якісних верстатів привносить в цей процес купу складнощів у вигляді черги на різку від декількох годин до декількох днів. Адже верстат часом ріже великі довгі замовлення. І заради кількох решіток нікому не прийде в голову зупиняти виробництво і переналагоджувати верстат.
Лазер відмінно справляється зі звичайною сталлю і з нержавіючої сталлю. Гірше йдуть справи з алюмінієм. З латунню, міддю і бронзою - ще складніше. Середній лазерний верстат якісно ріже звичайну сталь товщиною до 10-15мм, нержавійку - до 8-10мм, алюміній - до 4-8мм, латунь і мідь - до 3-4мм. Чим складніше верстата дається різка матеріалу, тим сильніше матеріал прогрівається під час процесу, тим сильніше заготовку «поведе» - з плоского листа вона перетворюється в кривій. Для того, щоб цього не відбувалося на панелях зі складним орнаментом технологу і оператору доводиться часом здорово потанцювати з бубном навколо верстата. Або вибрати інший спосіб обробки.
Наступний за популярністю спосіб розкрою - координатна пробивання. Це дуже цікавий спосіб отримання деталей. У більшості випадків деталі для корпусів наших комп'ютерів, електрощитів, серверів, кольорів, будь-яких металевих боксів, шафок і інших виготовляються масово листових залізяк виробляються на верстаті координатної пробивки. Якщо говорити спрощено, то в цьому верстаті керований системою сервоприводів опрацьований лист металу рухається між двома інструментальними револьверними барабанами. Вгорі встановлено різнокаліберні штампувальні інструменти, внизу - їх матриці. Наприклад, треба нам пробити в листі отвір діаметром 10мм. У верхньому барабані варто інструмент, в якому робоча частина - надміцний циліндр діаметром 10мм. А в нижньому - надміцний металевий циліндр побільше з отвором 10мм посередині. У потрібному місці спрацьовує пробивальних механізм і верхній інструмент прошиває метал із зусиллям до 30 тонн за удар крізь нижню матрицю, подібно Діркопробивачі. У барабані встановлюється до 60 комплектів інструментів. Там кола, квадрати, овали, прямокутники, всякі заокруглення та інші спецінструменту, на кшталт наших, декоративних - всяких трикутничків, зірочок і хрестоцвітих. Виготовлення таких інструментів обходиться недешево, але за рахунок величезної швидкості пробивання і відсутності інших витратних матеріалів (нагадаю, в лазерного різання це дорогий допоміжний газ) такий спосіб перфорації виявляється дешевше лазера. У деяких режимах верстат встигає за хвилину провести до двох тисяч ударів. При цьому він ще встигає точно просувати лист металу відповідно до програми. Виглядає це досить забавно. Неначе хтось всередині верстата стріляє по листу з автомата, а той, Дрига в конвульсіях, отримує нові порції «поранень».
Пробивання дозволяє істотно знизити собівартість типових невеликих решіток з металу товщиною від одного до двох міліметрів. Технічно можлива пробивання і набагато більш товстого листа, але при цьому відбувається сильна деформація. Насправді вона відбувається і на двоечку (на професійному сленгу так ніжно називається лист товщиною 2 мм), але на відносно вузьких гратах, до 300мм це не помітно. Принаймні ми робимо багато, щоб було не помітно. У найгірших випадках лист вигинається «тазиком». Тобто утворюється опуклість, яку не прибрати ніякими вулицями або правилах. Лист, подібно кришечці від дитячого харчування «клацає» то в одну, то в іншу сторону, відмовляючись повертатися в плоске стан. Це відбувається тому, що кожна пробивання залишає навколо отриманого отвору острівець напруженості - під час штампування лист пручався, і це напруга так і залишилося. Коли ці острівці розташовані близько у великій кількості на невеликій площі, проявляється деформація. Загалом, почалася нудятіна і більше не будемо про сумне. Суть в тому, що при своїй дешевизні і швидкості, координатна пробивання не любить товстий метал, великі панелі з щільною перфорацією. А ще переналагодження займає досить великий час. Зате кромки отворів виходять як би трохи прилизаним всередину - то що треба для декоративних решіток. І покінчимо з цим.
Наступна за популярністю технологія - фрезерування. Для декоративних решіток з невеликими елементами візерунка (у нас таких більшість) підходять тільки інструменти малого діаметра. Інструменти - це фрези. Здорово схожі на свердла, тільки коштують від п'ятисот до трьох тисяч рублів за штуку. Основні використовувані фрези - діаметром від півтора до п'яти міліметрів. Такі маленькі інструменти дуже крихкі, тому ми можемо фрезерувати декоративні решітки тільки з м'яких матеріалів - алюміній, латунь, мідь. Пам'ятайте, як раз з ними у лазера бувають проблеми. Зате у фрезера - ніяких проблем. Точніше одна все ж є - процес займає в сто разів більше часу. Тому наші верстати працюють цілодобово. Часом один екран батареї або одна решітка в підлогу може фрезеруватися до трьох діб без перерви - і вдень і вночі. Весь наш фрезерний цех втиканий камерами і технолог вечорами і ночами контролює процес навіть з дому. Якщо щось пішло не так, він з дому зможе зупинити верстат. І нікуди не дінеться - одягнеться, сяде в машину і поїде посеред ночі усувати неполадки. А вранці ми збираємо латунну або алюмінієву стружку в мішки. Іноді здається, що скоро ми потонемо в цій стружці. Зате фрезерному верстаті не важлива товщина металу. Ось чому ми виготовляємо решітки в підлогу з алюмінію і латуні досить великої товщини - до десяти міліметрів і більше.
Фрезерний верстат являє собою стіл з дуже жорсткою станиною. На стіл кладеться і надійно кріпиться заготовка. А над столом на спеціальному порталі керований серводвигунами рухається шпиндель - спеціальний потужний електромотор, що охолоджується рідиною. Знизу у шпинделя цанговий патрон, куди затискається фреза. Все це господарство їздить вперед-назад, вправо-вліво і вгору-вниз. Для того, щоб вирізати елемент візерунка, наприклад все той же трикутник або квадратик, фреза за кілька шарів повністю зруйнує, тобто переведе в стружку матеріал, що знаходиться всередині контуру трикутнички. Причому часто для прискорення процесу ми спочатку швидко виймаємо основну масу матеріалу більшої фрезою, а потім добираємо дрібниця в куточках більш дрібної - це двоєчка або полуторка. Такі тонкі фрези дуже тендітні. Вони виготовлені з загартованих спецсталі, які важко затупити, але дуже легко зламати. Тому тонкі фрези працюють повільно. Ось чому ми і вигадуємо ці складні стратегії - спочатку дуже велика фреза, потім середня, потім в куточках дрібниця. Ах так, ще забув про одну цікавість. Щоб фреза довго не тупілась, а матеріал не грівся, в зону різання подається мастильно-охладающая рідина. Вона або ллється струменем, або напилюється під тиском з повітряного сопла. Ну в загальному ви зрозуміли, не нудно нам тут.
Ну що, втомилися? Залишилося трохи. Найрідше ми використовуємо гидроабразивную різання. Це дорого і довго. У нас навіть власного верстата такого немає - іноді звертаємося за допомогою до наших партнерів. У цьому верстаті цікавий спосіб різання - метал ріжеться водою. Причому не якась там фольга, а сталева плита товщиною до 10 сантиметрів і більше. Наші решітки не бувають такими товстими, це я просто для опису можливостей верстата. Ми найчастіше ріжемо на гідроабразіве товсту латунь, якщо малюнок дуже вже не зручна для фрезерування. Ну або якусь екзотику типу товстої міді або бронзи. Бувало, різали нержавійку, але я вже навіть не пам'ятаю, чому. А може і зовсім наснилося.
Так ось, уважний читач, який ще від всієї цієї писанини не заснули або не впав у кому, напевно задається питанням, вода ріже метал - що за фігня? Зовсім і не фігня, а справжнісінька правда. Спеціальні насоси високого тиску, які називаються мультиплікатори, нагнітають воду в фокусуючу форсунку, яка, як на фрезерному верстаті їздить на порталі навсібіч над заготівлею. Тонкий струмінь води під тиском до 6 тисяч атмосфер б'є в матеріал. Мабуть там відбуваються процеси, схожі на стирання морською водою круглих камінчиків, тільки в прискореному в мільйони разів режимі. Щоб ще прискорити процес, в воду подмешивается абразив - невеликий гранітний пісочок. Процес схожий на лазерну різку. Спочатку струмінь прошиває матеріал, утворюючи неакуратне отвір. Потім, вже рухаючись від нього, різання відбувається в десятки разів швидше, ніж прошивка. Як і у всіх перерахованих вище випадках, все відбувається за програмою. За процесом невсипно стежить оператор, постійно коригуючи параметри процесу: швидкість подачі, тиск, витрата абразиву і ще масу всяких кнопок тисне на своєму пульті. Від великої кількості цих кнопок на стійці ЧПК у будь-якої нормальної людини трапиться напад епілепсії. Тому нормальних людей в оператори не беруть. Але ми все одно їх любимо і пригощаємо цукром, коли у них закінчиться.
На цьому наша розповідь підійшов до кінця. Наостанок зауважимо, що вирізати візерунок на шматку металу - це лише частина роботи. І часто мала її частина. Далі буде зварювання, рихтування, шліфування і фінішна обробка. Якщо у Вас залишилися питання, пишіть і телефонуйте. А краще приїздіть. Багато побачите своїми очима. Із задоволенням проконсультуємо, покажемо, розповімо і дамо потримати.