Ч уть більше століття знадобилося нержавіючої сталі, щоб підпорядкувати собі енергетичну і видобувну промисловість, машинобудування і медицину. Незважаючи на багатомільйонні вкладення і активну розробку органічних ланцюжків нового покоління, полімери у багатьох температурних режимах поступаються за механічними показниками високолегованих матеріалами. Нержавіюча сталь за допомогою додавання невеликого відсотка металевих домішок набуває хладо- або жаростійкі властивості, відмінні показники пластичності і здатність протистояти різним типам іржавіння. Здавалося б, незамінний у виробництві метал на практиці зварювання показує свій досить безглузда характер.
Гарячі і холодні тріщини
Спочатку проблема зварювання аустенітних сталей виникає на досить несподіваному місці: велика кількість легуючих компонентів і широкий спектр застосування готових виробів значно диференціює умови процесу зварювання. Це у великій мірі ускладнює контроль над якістю зварного з'єднання. Разом з тим, на зварних швах аустенітних сталей досить часто утворюються гарячі тріщини. Здебільшого це мікронадриви на межкристаллитного рівні, що визначаються лише ультразвуковим скануванням. Хоча іноді, можна зустріти і справжні видимі тріщини. Передбачити час появи структурних аномалій практично неможливо. Вони можуть виникнути і під час зварювання, і під час експлуатації в середовищі з підвищеною температурою.
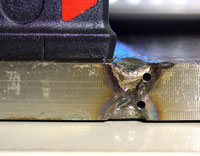
У першому наближенні можна сказати, що в основі гарячих тріщин лежить утворення грубозернистої структури. Термічний цикл зварювання створює багатошарові шви зі столбчатой структурою, коли кристали нижнього шару тривають вищерозташованими. Утворенню оной сприяє і напругу усадки, стабілізуючий кристалічні «колони». Але в результаті порушення дифузійних процесів на поверхні скупчуються активні елементи - кисень і вуглець - реагують з домішками основного матеріалу. Результатом зміни просторової концентрації елементів стають легкоплавкие і разом з тим тендітні евтектики (рідкі системи -розчину або розплави, що знаходяться при даному тиску в рівновазі з твердими фазами, число яких дорівнює числу компонентів системи). Високий рівень дисперсії сприяє зниженню пластичності і появи гарячих тріщин.
Говорячи про високодисперсних з'єднаннях, варто згадати інтерметалліді (з'єднання з двох або більше металів) з фіксованим співвідношенням компонентів. Що складаються з атомів кількох металів, міцні і хімічно інертні структури (ще один фактор порушення процесу дифузії) разом з карбідами підвищують крихкість околошовной зони.
Локалізація структурних аномалій в більшості випадків ліквідується додаткової десятихвилинної термічною обробкою при температурі 1100 ° С і наступним швидким охолодженням. В особливо складних випадках, коли столбчатая структура руйнується, але освіти интерметаллидов уникнути не вдається, додатково до аустенізації шва застосовується отжиг при 750-800 ° С. В результаті двохетапного термообробки вдається видалити карбідну і інтерметаллідним фазу.
Найчастіше освіту гарячих тріщин пов'язано з недостатністю захисного середовища. Як вже було сказано, високолеговані матеріали містять велику кількість присадок. Хром, алюміній та інші метали з точки зору фізичної хімії ближчі до кисню, ніж залізо, що зумовлює високий ступінь вигоряння, часом пробою захисного середовища. В особливо сумних випадках матеріал шва повністю втрачає карбідну і феритної фазу.
У разі незначного пропускання атмосферного кисню можливе використання укороченою дуги, а також фтористо-кальцієвих покриттів або флюсів, що базуються на хімічно активних фтористих підставах.
Але не варто впиватися додаткової Аустенізація шва. У століття економії електроенергії, настільки високоенергетичні процеси поступово повинні поступатися місцем інноваційним методам дугового зварювання. Відомо, що форма зварювальної ванни безпосередньо впливає на форму шва і відповідно на зростання кристалів аустеніту. Крім того, має сенс використовувати технології зі зниженим силовим фактором, адже усадочная деформація і жорстке кріплення виробів є відмінними каталізаторами утворення гарячих тріщин.
Для сталей з тимчасовим опором розтягування від 1500МПа і вище необхідно використовувати особливу методику. Високоміцні матеріали схильні до утворення послесварочних холодних тріщин, що виникають під дією власного зварювального напруги. У цьому випадку проводиться попередня аустенізація. підвищує пластичні показники стали. Після з'єднання заготовок необхідно провести додатковий нагрів до температури в 350-400 ° С.
Послесварочная межкристаллитная корозія
Аустенітні стали досить часто позиціонуються як стійкі до корозій різних видів. Межкристаллитная корозія, що протікає вздовж зерен, часто виникає не в самому зварювальному шві, а біля лінії з'єднання і навіть на значній відстані. В цілому фізичні аспекти розвитку корозії не відрізняються один від одного - різниця лише в причини виникнення.
Межкристаллитная корозія основного металу виникає при банальному перегріві деякого локального ділянки. Для матеріалу шва з фізико-хімічної точки зору все набагато складніше. Термічний цикл зварювання, як уже було сказано, порушує дифузійні процеси, в результаті чого на поверхню виділяються активний вуглець і легуючий хром. Вони утворюють одні з тих карбідів, що призводять до підвищеної крихкості шва. Очевидно, що паралельно з цим відбувається збіднення іншими легуючими компонентами (також в меншій мірі утворюються вуглецеві з'єднання з титаном і ніобієм), і матеріал стає більш вразливим до міжкристалітної корозії.
Очевидним рішенням зменшення схильності зварного шва і околошовной матеріалу до міжкристалітної корозії є аустенізація при 1050-1100 ° С
Непрямим рішенням проблеми є впровадження аустенитно-феритних матеріалів, більш стійких не тільки до міжкристалітної корозії, але несприятливого термічного циклу. Особлива структура - до 4% молібдену і 25% хрому - відрізняється меншими зернами і, відповідно, підвищеної протяжністю міжкристалічних кордонів. Збільшення площі виділення карбідів веде до зменшення їх дисперсності. Локальне збіднення хромом відбувається на незначну глибину. Крім того, аустенитно-ферритні матеріали володіють підвищеною швидкістю дифузійних процесів.
Зменшити схильність зварного шва і околошовной матеріалу до міжкристалітної корозії можна декількома способами. Очевидним рішенням є проведення вже відомої нам аустенізації при 1050-1100 ° С (можлива заміна на стабілізуючий відпал протягом 2-3 годин при температурі 850-900 ° С) Втім, завжди можна змиритися з випаданням карбідної фази, нейтралізуючи її наслідки за допомогою додаткового легування до освіти аустенитно-феритної структури. Мінусом такого підходу є не тільки перевитрата хрому та інших металів, а й зниження опірності загальної корозії, що розповсюджується по всій поверхні виробу. У цьому світлі деякі виробничники віддають перевагу в якості легуючого компонента використовувати титан, тантал або ванадій замість хрому. Разом з тим, більш дорогі метали виявляються також і більш вимогливими до захисної середовищі. Якщо не використовувати інертні гази або фторидні флюси замість кислих, близький до кисню титан вигорає на 70-90%.
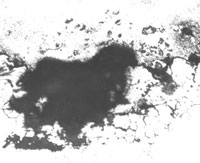
Додатково: необхідно налагоджувати автоматизовані процеси, що гарантують безперервність отримання шва стабільної електричною дугою, повторне порушення якої робить термічний цикл несприятливим.
Фізика на ділі
Звичайно, виключити з термічного циклу процеси, що призводять до утворення тріщин і міжкристалітної корозії неможливо. З іншого боку, завжди можна купірувати наслідки і повернути матеріалу втрачені властивості. Сьогодні тенденція винаходів говорить нам про важливість впровадження менш ресурсномістких методів аустенізації, видалення карбідних і інтерметаллідних фаз, повторного підвищення антикорозійних властивостей. Хоча, можливо вже завтра мова йтиме про повне виключення концентраційних змін і порушень процесів дифузії.
Олександр Гуща, спеціально для www.EquipNet.ru
Фотографії з сайтів know-house.ru, acsys.ru, schmolz-bickenbach.ru
>>> Хочете обговорити цю бізнес-ідею докладніше? Чекаємо вас на нашому Форумі