Металургійні властивості агломерату
Високоякісний агломерат характеризується високою міцністю, високою відновлюваністю, високою температурою початку розм'якшення і коротким інтервалом розм'якшення.
Міцність агломерату визначається будовою його шматків і мінералогічним складом.
Шматок агломерату є Систему блоків, розділених великими порами. Структура схожа на виноградне гроно. Периферійна зона кожного блоку складається з кристалів магнетиту, між якими невелика кількість силікатної зв'язки і скла. Ближче до центру - проміжна зона з підвищеною кількістю зв'язки. У центрі розташовано одне або кілька силікатних озер, що складаються з Са-олівіну. Абсолютні розміри блоків збільшуються при укрупненні коксового дріб'язку, використовуваної для спікання.
При навантаженнях в першу чергу руйнуються зв'язку між блоками. Оптимальними є блоки 15-20мм, що утворюються навколо частинок коксика 1-3 мм.
Способи поліпшення якості.
1. Збільшення витрат твердого палива покращує міцність, але при цьому знижується продуктивність. Тому доцільно додатково підігрівати спікається шар газовими пальниками ..
2. Добавка доломітизованого вапняку. Магній при кристалізації входить в
грати Ca2SiO4 і запобігає полиморфное перетворення β = Ca2SiO4 → γ-Ca2SiO4. При спіканні криворізьких руд з витратою коксового дріб'язку (5-6%) введення в агломерат
3% MgO знижує вихід дрібниці (<5 мм) после барабанного испытания с 22—25 до 17—20 %. В настоящее время доломитизированный известняк добавляют в агломерационную шихту на большинстве аглофабрик мира.
3. Доцільно спекать два міцних агломерату різної основності, які потім змішуються. Це дозволяє не проводити неміцний агломерат основностью 1,3-1,5.
Восстановимость прямо пропорційна поверхні пір офлюсованного агломерату і залежить від основності. Максимум восстановимости відповідає основності 1,4-1,5.
Температура початку розм'якшення основностью 0,5-0,7 і 2-4 становить 1100-1150 і 1200-1250С.
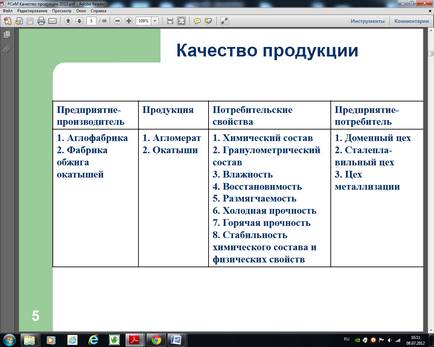
Крім текстури агломерату, на його міцність великий вплив робить і мінералогічний склад спека. Присутність в шматках агломерату залишків шихти, гематиту, магнетиту, кварцу, тюрінгіта значно послаблює шматок. Особливо шкідливо діють включення вапняку і вапна. Вапно гаситься водою з утворенням портландіта, що призводить до руйнування шматка агломерату. З цього випливає, що агломераційна шихта не повинна містити рудних частинок> 8 мм і частинок вапняку> 3 мм. Шкідливий вплив на міцність агломерату надає також присутність в його структурі крихкого скла, особливо Двухкальціевий силікату. Останній при охолодженні шматка агломерату (675 ° С) зазнає поліморфний перетворення β = Ca2SiO4 → Ca2SiO4, в ході якого обсяг цієї фази зростає на 11-12%. Це створює величезну внутрішню напругу в шматку агломерату, його міцність різко знижується.
Наведені вище дані відносяться до так званої холодної міцності агломерату, тобто до його опірності численним перевантажень, транспортуванні і т. д. Однак
агломерат руйнується ще й в самій доменної печі при нагріванні і відновленні ( «гаряча міцність»). Причини цього явища були розглянуті раніше. Стосовно до офлюсовані агломерату експериментально встановлено негативний вплив присутності гематиту і скла на його гарячу міцність. Гематит при нагріванні з відновленням змінює питомий об'єм, збільшуючи фон внутрішньої напруги в структурі, руйнується внаслідок анізотропії восстановимости. Скло зберігає крихкість аж до 600-700 ° С, коли стає пластичним і релаксує напруги. Таким чином, присутність скла шкідливо позначається не тільки на холодній, але і на гарячій міцності агломерату.
Ефективність використання офлюсованих матеріалів.
Ендотермічний ефект реакції розкладання вапняку, взаємодія виділяється двоокису вуглецю з вуглецем коксу і зниження відновного потенціалу газу в печі через розведення його двоокисом вуглецю погіршують показники доменної плавки і сильно впливають на витрату коксу.
При застосуванні офлюсованих матеріалів відбувається:
1. Виключення з доменної плавки ендотермічної реакції розкладання карбонатів, тобто СаСО3 = СаО + СО2 - Q або MgCO3 = MgO + CO2 - Q, що вимагають тепла, а отже, витрати коксу. Цей процес перенесений на аглоленту, де витрачається менше дефіцитне і більш дешеве паливо, ніж кокс.
2. Поліпшення відновної здатності газів в самій доменної печі внаслідок зменшення розведення їх двоокисом вуглецю, одержуваної від розкладання карбонатів.
3. Поліпшення восстановимости агломерату, так як вапно витісняє оксиди заліза з трудновосстановімих силікатів заліза.
4. Поліпшення процесу шлакоутворення, так як в офлюсовані агломерату оксиди щільно контактують один з одним.
5. Зменшення числа матеріалів, що завантажуються в доменну піч. В кінцевому підсумку, застосування офлюсованного агломерату призводить до скорочення витрат коксу на 6-15%.