Оскільки цей матеріал призначений для любителів, є необхідність розповісти про деяких етапах виробництва порцеляни, які дуже добре знайомі професіоналам, але залишаються поза увагою всіх інших людей. Багато колекціонерів і продавці порцелянових виробів ніколи не були на виробництві та не мають необхідних знань.
Самі часто задаються дали мені можливість зрозуміти, що в цілому народ не має ніяких можливостей для отримання простих відповідей, які не потребують занурення в технологічні складнощі.
Найпоширеніший питання: Чому вироби з порцеляни порожнисті усередині?
Звичайно, питання відноситься до скульптури і посудним формам. Є плоскі вироби, які робляться методом формування або пресування і не мають всередині порожнин.
Є процеси, які краще показати, чим пояснювати. Для початку рекомендую подивитися невеликий фільм про виробництво порцеляни:
Рідка сметанообразная маса (фарфоровий шликер) заливається на певний час в гіпсову форму. Гіпс вбирає вологу, утворюючи черепок вироби. Як тільки товщина черепка стає достатньою, що залишився в формі шликер виливається через зливний отвір. Товщина стінок вироби, в залежності від його обсягу, може бути від 3 мм. до 8 мм.
Фарфор, в процесі виготовлення, має повітряну і вогневу усадку, тобто пропорційно зменшується в розмірі на 14-16% від вихідної моделі. (Фото).
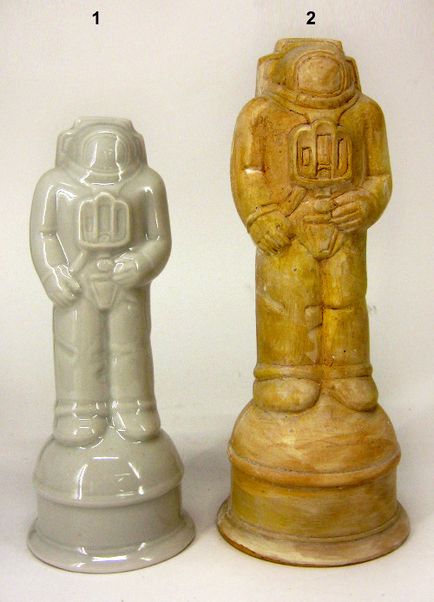
Температура политого випалу порцеляни 1350-1410 градусів. Відсоток усадки залежить від кінцевої температури. У камерних печах температура може бути різною в залежності від місця в печі. Відповідно, різною буде і усадка. Усадка залежить і від товщини стінок (черепка) вироби. Чим товщі стінки, тим більше усадка. Якщо виріб відлито з дуже товстими стінками і стінки мають нерівномірну товщину, то при политому випалюванні у нього може проявитися на поверхні деформація. Занадто тонке виріб ще більшою мірою деформується при политому випалюванні. Велика частина шлюбу порцелянових виробів проявляється після политого випалу: мушки, наколи глазурі, галявини (проступленіе матового черепка, в наслідок нерівномірного товщини глазурі), бульбашки, збірка глазурі і т.д. Слід сказати, що відсоток браку після политого випалу може доходити до 50% при нормі в 15%.
На великих виробництвах приготування шлікера контролюється технологами з ЦЗЛ. Щільність шлікера становить 1,72 гр на 1 кубічний см. Щільність вимірюється ареометром. Щільність глазурі 1,28 гр. Глазур розлучається у великій ємності для того, що б можна було вільно занурити виріб повністю. При висиханні можуть утворитися краплі і патьоки, які акуратно прибираються з вироби за допомогою повсті. Для того, що б приготувати виріб до ставки в випал, денце повністю зачищається від глазурі і замивається вологою губкою. У піч виріб ставиться на карборундові плити, покриті каоліном. Каолін охороняє виріб від прилипання до плити в процесі випалу.
Перший утельного випал проводиться при температурі до 900 градусів для закріплення черепка і подальшої поливання.
Процеси що проходять при випалюванні порцеляни докладно описані в спеціальній літературі. При випалюванні в електричних печах відбувається поступовий підйом температури, який відображається на контрольних приладах і при необхідності тестується за допомогою керамічних конусів, які мають задану температуру плавлення. Конус з певною температурною міткою оплавляется і стосується вершиною підстави при досягненні необхідної температури. Политій випал порцелянових виробів краще проводити в газових печах, в яких можна домогтися найбільшої білизни фарфору. У газовій печі відбувається ще зміна режимів за допомогою регулювання подачі повітря і газу. Можливий швидкісний випал порцелянових виробів, при якому добре просушені вироби можуть нагріватися зі швидкістю до 900 градусів за годину в різко окислювальному середовищі зі збільшенням подачі повітря. При швидкісному випалюванні початок відновного періоду відповідає температурі 1000 градусів, закінчення 1200 градусів (збільшення подачі газу). Подальший підйом температури йде при слабо відновної середовищі. Зазвичай для кожної газової печі складається оптимальний графік випалу з прописаними показниками тиску газу і повітря. Досвідчені випалювачі згодом визначають температуру в печі за кольором полум'я. Після досягнення потрібної температури робиться витримка протягом 15 хвилин для вирівнювання температури у всьому обсязі печі, після чого подачу газу припиняють. Потім піч за допомогою продувки повітрям охолоджують. Від 1350 до 900 градусів можливо швидке охолодження. Далі краще проводити природне охолодження, при якому піч менш руйнується.
Для тих Новомосковсктелей, які захочуть більш детально зупинитися на технології випалу, я даю цитату з довідника: «Політило випал можна розділити на ряд періодів, кожен з яких протікає при певному температурному режимі і газовому середовищі, що забезпечує поступове формування черепка з необхідними властивостями.
Перший період випалу порцеляни (20-950 ° С) характеризується різними фізико-хімічними реакціями, що залежать від попередньої підготовки виробів до политому випалу, а також від сушки виробів після глазурування. Попередня підготовка залежить від ступеня першого випалу і визначається наявністю в складі виробів газоподібних продуктів.
В першу чергу видаляється залишкова механічно пов'язана і гігроскопічна вода. Обидва види води випаровуються при температурі 110-130 ° С.
Після прогріву порцелянових виробів здійснюється більш інтенсивний підйом температури. У цьому інтервалі температур відбувається остаточна дегідратація глинистої речовини і повне видалення хімічно зв'язаної гідратної води, якщо цей процес не отримав завершення при першому випаленні. Найбільш активно пари гідратної води виділяються в інтервалі температур 500-600 ° С.
Оскільки при зазначених температурах фарфор володіє ще досить великою пористістю, бурхливе виділення вологи в цей період не приводить до розтріскування черепка виробів. Пічна газове середовище не впливає на видалення гідратної води.
Приблизно з температури 200 до 500 ° С вироби при випалюванні поглинають (адсорбують) сажистий вуглець з димових газів. Вище 700 ° С починається його поступове вигоряння, яке більш активно відбувається в окислювальному середовищі. Одночасно здійснюється сублімація органічних речовин, що містяться в глинистих матеріалах, яка також супроводжується науглероживанием черепка. Щоб зменшити коксування вироби в цьому інтервалі температур підтримують окислительную газове середовище (? = 2-4).
Чи не вигорілий при досягненні 1000 ° С вуглець, як і залишки не віддаленій вологи, на більш пізніх етапах випалу сприяють утворенню здуття у вигляді «прищів» в результаті закриття рідкої фазою, яка починає утворюватися при температурі 950 ° С, деякої частини капілярів в обпалюють черепку .
Чи не вигорілий до початку відновного періоду адсорбований черепком вуглець може викликати дефекти і в наступних періодах випалу порцеляни, особливо в початковий період охолодження, оскільки після періоду відновлення, коли співвідношення СО: СО2 стане менше 0,1, можливо його вигоряння з утворенням газових бульбашок, що обумовлюють виникнення на порцеляні наколів і кратеровідних заглиблень.
Органічні речовини так само, як і адсорбований вуглець, повинні бути повністю вилучені з черепка до початку відновного періоду в різко окислювальному газовому середовищі з надлишком вільного кисню (близько 4-6%), оскільки при температурі понад 1050 ° С випал вже ведеться в відновлювальної атмосфері .
Необхідність випалювання органічних речовин до температури 950 ° С обумовлена ще й тим, що при цій температурі фарфор має досить високу пористість (газопроницаемостью), що сприяє безперешкодному виходу газів, які утворюються при згорянні органічних речовин. Тривалість випалювання органічних речовин з порцеляни залежить від його товщини і вмісту кисню, а також від обсягу садки.
У цьому періоді (при температурі 575 ° С) випалу відбувається реакція перетворення? -кварца в? -кварц, яка супроводжується збільшенням обсягу виробів, що, однак, не викликає появи дефектів. Пояснюється це наявністю великої кількості пір в нагрівається порцелянової масі. Крім того, при розширенні в поверхневих шарах вироби виникають стискаючі зусилля, яким матеріал добре чинить опір.
До температури 1000 ° С закінчується декарбонізація (термічний розклад) вуглекислих магнію MgCO3 і кальцію СаСО3, присутніх в порцеляновій масі. Карбонат магнію MgCO3 починає розкладатися при температурі 650 ° С, а карбонат кальцію СаСО3 - при 920 ° С.
При таких відносно низьких температурах матеріал має ще більшу газопроникність, що сприяє безперешкодному виходу утворюється при розкладанні карбонатів вуглекислого газу СО2.
Другий період випалу протікає при температурі від 950 до 1050 ° С в різко окислювальному середовищі. У цей період крім завершення реакції декарбонізації і перетворення? - в? -кварц відбувається інтенсивне вигоряння вуглецю в черепку, повне звільнення матеріалу від залишків гідратної води, а також окислювання сполук заліза.
Нагрівання виробів в другій період випалу носить майже ізотермічний характер, що сприяє вирівнюванню температурного поля в об'ємі садки виробів.
Третій період випалу - відновний. Відновлювальний період створюється збільшенням концентрації СО в продуктах горіння палива в температурному інтервалі 1050-1250 ° С. Оксид вуглецю СО відновлює оксид заліза Fe2O3 до оксиду FeO, а сульфати кальцію CaSO4 і натрію Na2SO4 - до сульфідів і сульфітів, що запобігає спучування черепка і сприяє створенню ефекту «відбілювання» порцеляни. Крім того, FeO сприяє утворенню склоподібної (рідкої) фази, розширює інтервал спікання. Склоподібна фаза, в свою чергу, сприяє інтенсивності протікання реакції муллітообразованія (муллит - основна складова кристалічної фази порцеляни).
Реакції відновлення оксиду заліза Fe2O3 до FeO здійснюється за такими схемами:
3Fe2O3 + СО = 2Fе3О4 + CO2
Fe3O4 + СО = 3FеО + CO2
O2 + 2СО = 2CO2
2FeO + SiO2 = 2FеО • SiO2
Підвищення температури в цей період випалу і концентрації СО прискорює реакції, але при занадто інтенсивному або занадто пізньому (по температурі) процесі відновлення швидкість утворення склоподібної фази може перевершити швидкість відновних реакцій, і гази, не знайшовши виходу з черепка, викличуть освіту в ньому здуття. Склоподібна фаза утворюється в основному в інтервалі температур 1150-1170 ° С, хоча в невеликій кількості вона утворюється вже при температурі 950-1000 ° С. У фарфоровій масі присутні і інші компоненти, що виділяють гази при нагріванні, тому ці гази повинні бути також вилучені до досягнення температури 1170 ° С, т. Е. До плавлення польового шпату, коли фарфор володіє ще достатньою газопроницаемостью.
Реакції відновлення сульфатів кальцію CaSO4 і натрію Na2SO4 протікають за такими схемами:
CaSO4 + CO = CaSO3 + CO2
CaSO3 + СО = СаО + SO2 + CO2
Na2SO4 + CO = Na2SO3 + CO2
Na2SO3 + CO = Na2O + SO2 + CO2
Якщо відновну середу в цей період замінити окислювальному, то розкладання сульфатів закінчиться при температурах, що перевищують точки плавлення польового шпату, що також призведе до утворення здуття. Відновне середовище значно знижує температуру газовиділення компонентів маси, що сприяє отриманню бездефектного (без здуття) черепка.
У продуктах горіння СО може міститися в кількості від 3 до 8% в залежності від типу печі. Збільшення вмісту СО небажано, так як при цьому в продуктах горіння утворюється сажа, яка осідає на виробах. При подальшому її вигорянні можуть виникнути дефекти на глазурі - наколи.
Тривалість відновного періоду визначається в основному товщиною і формою випалюються виробів.
Розглянутий температурний інтервал 1050-1250 ° С супроводжується інтенсивної усадкою маси. При цьому капіляри і пори в черепку поступово закриваються, а дифузія газів затухає. Найбільш інтенсивно усадка протікає в інтервалі температур 1000-1200 ° С. Найбільша усадка відповідає і найбільшому ущільнення черепка.
Четвертий період випалу (1250-1410 ° С) - спікання фарфору - протікає в умовах нейтрального середовища.
У цей період триває розкладання алюмосиликатов, що містяться в керамічної маси, на вільні оксиди з подальшим утворенням муллита (3А12О3 • 2SiO2) і вільного кварцу; завершується освіту склоподібної і кристалічної фаз; відбувається спікання фарфору, при якому він набуває основні фізико-механічні властивості, а також хімічну стійкість.
Цей період протікає від температури 1250 ° С до кінцевої температури випалу, величина якої в залежності від складу фарфорової маси може коливатися від 1280 (м'який фарфор) до 1410 ° С (твердий фарфор). Щоб отримати необхідну мікроструктуру, що характеризується закритою пористістю від 2 до 4%, оптимальну температуру випалу встановлюють на 20-50 ° С вище температури найбільшого ущільнення. Підвищення температури вище оптимальної викличе перевитрата порцеляни, при якому знижується білизна, збільшується пористість, зменшується міцність виробів.
Четвертий період випалу завершується витримкою при максимальній температурі протягом часу, необхідного для завершення реакцій спікання, а також більш рівномірного розподілу кристалічної фази в склоподібної. Тривалість витримки залежить від обсягу випалюються виробів. Надмірне збільшення витримки викликає перевитрата виробів. Відсутність же витримки при швидкому підйомі температури від 1250 ° С до максимальної створює недожог виробів.
П'ятий період випалу - різке охолодження. При охолодженні порцеляни велике значення має точка переходу склоподібної фази з розплавленого в тверде пружне стан і точка затвердіння глазурі.
Температурі переходу в твердий стан відповідає точка затвердіння глазурі на порцеляні. У глазypeй твердих порцелян ця точка знаходиться близько температури 700 ° С, у глазурі м'яких порцелян - 550 ° С. Для того щоб між черепком і глазур'ю не з'явились термічні напруги, рекомендується знижувати швидкість охолодження в цих інтервалах температур. В іншому випадку може виникнути розтріскування глазурного покриву. Надмірно уповільнене охолодження може привести до втрати блиску глазурі через її кристалізації.
На початковій стадії охолодження (1410-1000 ° С) на фарфорових виробах можуть виникнути два види дефектів: жовтизна на поверхні і матовість глазурі. Жовтизна виникає в результаті окислення заліза: 4FeO + O2 = 2Fe2O3. Оксид заліза Fe2O3 надає жовтий відтінок поверхні виробів. Хоча жовтий відтінок не погіршує інших властивостей фарфору, але при цьому псується зовнішній вигляд виробу. Жовтизна може бути усунена при повторному випалюванні, виконаному по нормальному режиму. Матовість глазурі виникає через її кристалізації.
При швидкому охолодженні від 1410 до 1000 ° С у повітряному (окисної) середовищі у зв'язку з великою інтенсивністю початковій стадії охолодження окислення FeO і кристалізація глазурі стають неможливими, внаслідок чого черепок зберігає білизну і блиск глазурі.
Шостий період випалу - охолодження. При подальшому охолодженні в інтервалі температур 1000-700 ° С рідка фаза остаточно твердне і фарфор переходить з в'язкого стану в крихкий. У цей період у виробі виникають термічні і механічні напруги. Термічні напруження, що виникли через різницю температур в період пружного стану, зникають після вирівнювання температури по товщині виробів, тому їх називають тимчасовими. Термічні напруги можуть привести до руйнування виробів при охолодженні. При застиганні рідкої фази в виробі виникають механічні напруги внаслідок нерівномірності усадки маси по її товщині. Такі напруги можуть також призвести до руйнування виробів як в процесі охолодження, так і у споживача. Тому механічні напруги називаються залишковими.
Тимчасові і залишкові напруги залежать від швидкості охолодження виробів в цей період. Допустима швидкість охолодження залежить від властивостей матеріалу, розмірів і форми виробів, а також від обсягу садки. Для зменшення напруг обох видів швидкість охолодження в цей період дещо знижується. Подальша швидкість зниження температури визначається термічною стійкістю виробів і вогнеприпасів. »